In order to properly comprehend the benefits of utilizing Bluehill’s Traceability module in the wider materials testing industry, it is prudent to first explore the reasons why the Food and Drug Administration (FDA) requires every medical device and pharmaceutical company trading in the United States to comply with 21 CFR Part 11.

Image Credit: Instron - USA
This is just one of a large number of regulations that traceability is able to address.
First introduced in 1996, Part 11 offers a series of guidelines for companies looking to implement digital signatures and electronic records in place of paper-based audit trails.
Transitioning from paper-based to digital recording may seem an intimidating process change for a laboratory, but the long-term security and cost benefits have led large portions of the biomedical industry to make this beneficial change.
Adjusting to the digital age is just one of a number of reasons that Part 11 compliance is beneficial to a lab. Ultimately, the primary value realized through this rigorous regulation is the confidence that product quality is consistently maintained.
Cost of Failure
There are huge cost of failure implications for a ‘bad batch’ of medical equipment. This is not only deeply problematic for the company but also for the end consumer whose life will likely be adversely affected by the failed product.
Products such as stents, sutures and syringes are relied upon by individuals and healthcare professionals, and these should perform as expected. The FDA’s role lies in protecting the public’s wellbeing through the provision of rules and guidance, which much be adhered to by any business selling products into the industry.
When a medical product fails during use, an investigation takes place in order to ascertain cause and liability. Should a company’s product be found to be liable for damages, the company will be required to pay a heavy toll via a combination of litigation, recalls and reputational damage.
The industry’s cost of failure is high, meaning that biomedical companies are financially motivated to abide by regulations and properly invest in process improvements designed to guarantee product quality.
Costly failures are not unique to the biomedical industry – these occur in any instance of a product or service prompting an undesirable experience by its user. This cost is sometimes modest; for example, a kitchen refuse bag prematurely tearing while under load.
In this common example, in all likelihood, the customer will simply take extra care when taking out their trash, but if premature tearing continues despite these reasonable precautions, the customer may submit a complaint, request a refund, or purchase a different brand in the future.
As long as this remains an isolated occurrence, however, the manufacturer’s profits are unlikely to be adversely affected in any notable way.
Should the underlying cause of the failure be more systemic, however, large numbers of customers may be impacted, prompting the manufacturer to take more costly corrective action.
While the relative cost of failure in this example is low and legal action can be mitigated via a simple replacement or refund, not every product failure is this harmless.
When the Cost of Failure is Too High to Ignore
Serious product failures have the potential to result in injury or even death to the user. For example, parachute manufacturers work within a safety-critical industry, with a skydiver’s life highly dependent on each individual component functioning according to its design.
Increased focus on product safety has led to rates of fatal accidents falling drastically in recent years, with the National Safety Council reporting that an individual is more likely to die from being struck by lightning than from skydiving.
However unlikely, a component failure due to manufacturer error; for example, the paracord snapping under stress that leads to a fatality occurring, will incur costly litigation and cause the manufacturer’s brand image to be irreparably damaged.
In these examples, the cost of failure is extremely high for everyone involved, and numerous companies have gone out of business following failures of this scale.
The severity of a product’s cost of failure will depend on the nature of the product itself. The product’s intended use will also affect this, as will any potential risks arising during its intended use.
Two non-biomedical manufacturing industries are also widely recognized as having to manage a high cost of failure: automotive and aerospace.
Safety-Critical Industries: Automotive and Aerospace
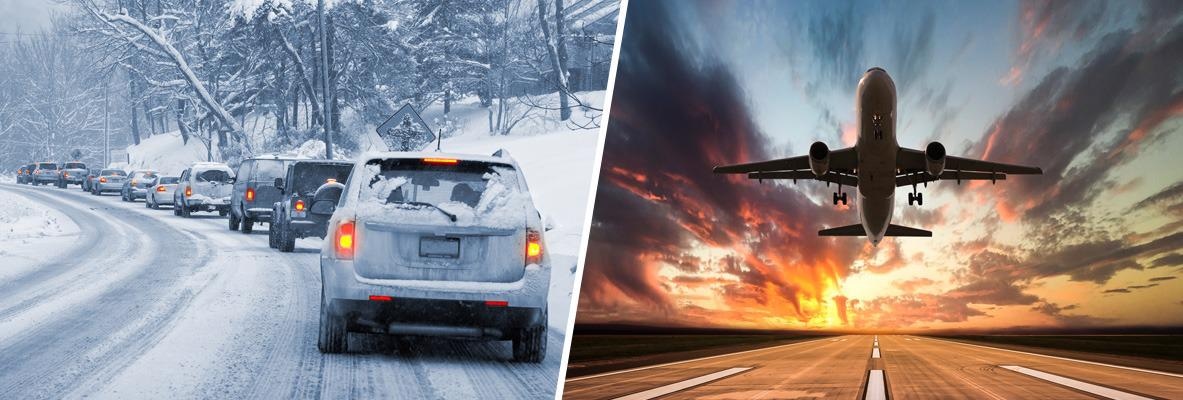
Image Credit: Instron - USA
The automotive industry sells cars, and buyers of these cars expect a high level of safety. If seatbelts malfunction or airbags are not deployed during a serious accident, the manufacturer will face intense scrutiny.
Similarly, billions of people take flights every year, with the aerospace industry flying these individuals at 30000 feet and being required to land all passengers safely. The financial livelihoods of aerospace companies depend on an extremely high rate of uneventful flights.
Suppliers producing materials and components for either of these safety-conscious industries are required to address this high cost of failure via appropriate business strategies.
The primary strategy for mitigating the risk of failure is investing in staff, materials, equipment and processes that result in improvements to overall product quality.
For many industries with a high cost of failure, quality is mandated by regulatory bodies – this is not optional. Much like the biomedical industry, the aerospace and automotive industries are both stringently regulated in order to ensure that the end customer consistently receives a reliable product.
The Role of Audits
Manufacturers undergo routine audits to ensure that regulations are being met. These audits are conducted not only by external government agencies but by the company’s own quality organization as well. Audits are key in verifying that the current manufacturing process will result in a sufficiently high quality product.
Audits also provide reassurance that if a ‘bad batch’ does reach the consumer, the manufacturer has the information required to rapidly identify the underlying issue, confirming the scope of the problem and perform appropriate corrective actions.
An audit of processes involving material testing equipment should also include proper control of product testing methods and associated results, and this is the area in which Bluehill’s Traceability module can provide tangible benefits to a wide range of processes and industries.
The Traceability module is integrated with Bluehill’s standard security modes, allowing a lab to track and review the who, what, when and why for any action undertaken on the test system in question.
The Traceability module’s potential can be understood by its capacity to provide context to each of the following questions:
“Who?” is the user performing the action in question.
“What?” is the action being performed. This could include creating, modifying, or reviewing Bluehill files such as samples, methods and report templates, or a range of system level actions; for example:
- Ex. 1 – generate a PDF test report for review
- Ex. 2 – delete a specimen from a sample
- Ex. 3 – modify a test method’s crosshead rate
- Ex. 4 – modify a test method’s yield stress calculation
- Ex. 5 – modify a user’s permissions
“When?” is the date and timestamp of the action being performed. This is recorded in local time with appropriate time zone information.
“Why?” is the reason the action was performed. This is entered by the user as a free text comment.
It should be noted, however, that all of these examples assume the user has appropriate security permissions to perform the action in question.
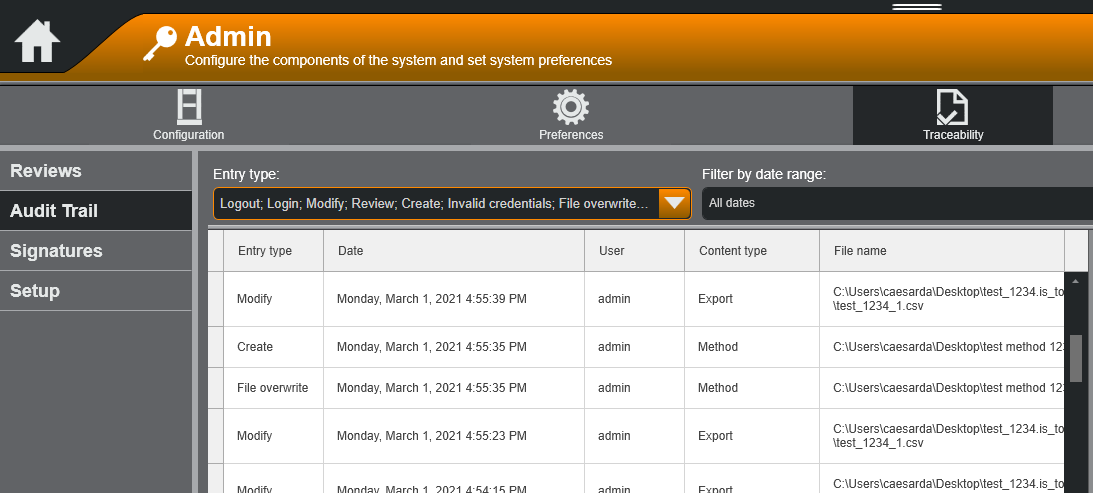
Image Credit: Instron - USA
Why These Questions Matter
System actions do not always create downstream quality issues, but all of the examples provided here could potentially compromise the integrity of Instron data, devaluing results used to characterize material properties or information on a component under test.
For example, if a user modifies a test method’s yield stress calculation incorrectly, this change could result in the yield stress result being artificially high for any subsequent tests. This could lead to a flawed batch passing product tolerance checks, and this issue is then not detected until a failure is reported in the field.
Because it is unaware of the underlying cause and scope of the issue, the company would need to begin an investigation, tracing the batch back to its production and ensuring that appropriate quality assurance tests are performed prior to shipment.
Ultimately, the test method used for the bad batch will need to be thoroughly assessed by someone confident with the test method, allowing the incorrect calculation to be identified.
The time between the calculation being changed and the issue being detected could be a week, a month, or even a year. Many bad batches could pass inspection during this period, meaning that the cost and scope of failure caused by a basic mistake can grow rapidly.
Insights Gained Through Traceability
The scenario would take place very differently if the Traceability module was configured on the Instron test system.
With traceability, the lab could ensure that any revisions to methods require electronic approval by one or two additional users, ensuring this takes place prior to an operator being able to test any specimens.
Should the reviewer reject the incorrect yield stress modification in the first instance, this issue could be avoided altogether.
Should the reviewer mistakenly approve the change, the company would not know until the issue was detected in the field. Traceability can assist the company’s investigation of the underlying cause in this situation, however.
Rather than manually probing for errors in the test method from memory, the lab can systematically identify any amendments to the method by searching the automated audit trail or examining the revision history of the method file, both of which are easily accessible within Bluehill Universal.
The example outlined here illustrates just one case where the Traceability module has the potential to not only improve a lab’s data integrity and, therefore, confidence in product quality, but it can also reduce the risk of an extremely costly product failure.
Considering all the materials and devices that human beings routinely trust with their health and safety reveals risk around almost every corner. Consumers trust their cars to transport them safely and expect planes to fly without issue.
Individuals expect these products to be safe in the same way that they trust medical supplies to be safe, despite the FDA not regulating the aerospace or automotive industries.
Part 11 compliance is not the only reason that companies should turn their attention to data integrity. Bluehill’s Traceability module offers incredible value in any industry or sector where a high risk of failure products are developed and manufactured.
The Traceability module has been designed to minimize any chance of costly accidents happening, therefore helping protect both the end-user and the manufacturer from the effects of potentially catastrophic failure.
Acknowledgments
Produced from materials originally authored by Daniel Caesar from Instron.

This information has been sourced, reviewed and adapted from materials provided by Instron - USA.
For more information on this source, please visit Instron - USA