Induction heating technology is a more effective, cost-efficient solution for tube and pipe manufacturers. It is an ideal solution for operations including hot bending, brazing or coating, heat treating and weld stress relieving.
Induction systems are eco-friendly and capable of selectively heating only parts of a tubular product. They also offer ergonomic benefits and occupy less floor space when compared to conventional furnaces and ovens. Moreover, it provides a higher quality coating solution by heating the metal substrate under the coating and curing the coating from the inside out. This results in softer surface and enables solvent evaporation and any outgassing to take place. Removing coatings for recoating pipes and tubes is another typical application of induction heating. Ambrell offers fast and efficient induction heating solutions for all phases of the curing operation.
Pre- and Post-Weld Heating
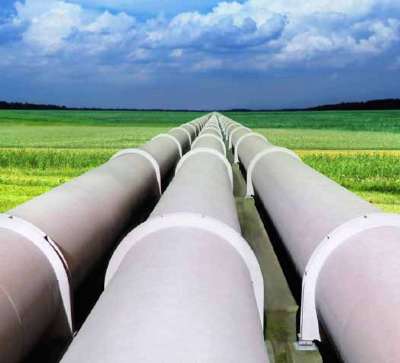
Since today’s oil and gas pipelines use more thin-wall steel alloy pipes, manufacturers and installers are showing interest towards Ambrell induction heating systems, which provide the required fast, accurate and homogeneous heating. For butt welding, the joint area is preheated by induction heating to 150-200 °C to prepare the surface for a uniform quality weld. After welding, the joint area then heated to 600-650°C to relief thermal stress.
Other advantages of induction heating include:
- No open flames or exposed heating elements
- Minimal damage to factory coating and eliminates deleterious surface residues
- Variable control over temperature/time parameters
- Large gas storage area is not required and energy costs are reduced.
Hot Pipe Bending
For bending larger, thicker walled pipes, induction heating is ideal as it offers the focused narrow band heating with higher quality bends with lower wall thinning and ovality when compared to other bending techniques. Induction hot pipe bending is also a suitable replacement for conventional fit-and-weld methods, helping companies to fulfill the stringent safety requirements of the chemical and energy industries.
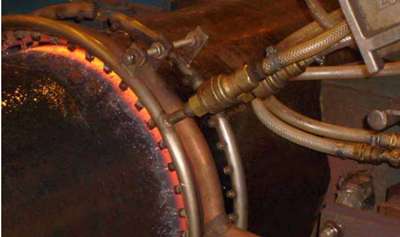
Ambrell offers induction heating systems with various frequency and power levels for hot pipe bending. For hot pipe bending, the pipe is surrounded by an induction heating coil at the bend point and heated. The heated pipe is then bent into the desired shape by applying pressure using a bending arm. Air and water quenches are utilized before and after heating to help bending only at the hot zone.
Drill Pipe Heat Treatment
Drill Pipe Manufacturing
Oil and mineral drill pipe manufacturers are using Ambrell induction heating systems to fulfill the prerequisites of API 5DP and GOST R 50278.
Advantages of induction heating over resistance or flame heating methods during the production processes in drill pipe heat treating and tool post welding onto the pipe ends are as follows:
- Productivity: Quicker heating allows for single-part processing
- Quality: Eliminates temperature differences that are common in flame heating
- Economical: It applies heat to the required area
- Consistency: Precise, rapid, uniform heating within the part
- Safe: Provides safer working environment as it eliminates exposed flame.
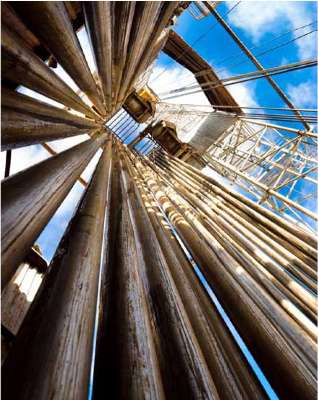
Upsetting or Forging Process for Wall Thickening
The pipe end is heated to 1100 °C for drill pipe end thickening prior to forging. Induction is utilized frequently for heating multiple pipes in a single channel coil, or sequentially in a multi-position coil that fabricates one pipe-end in 150 sec. These heating techniques not only provide the time needed for the heat to pass through the pipe wall but also in line with the 180-second floor-to-floor cycle time.
Tool Post Post-Welding Heat Treating
When the tool post is friction or arc welded onto the pipe end, the weld and surrounding pipe becomes brittle. To toughen the joint area, a three-step heat treating process is used.
Stress Relief: Stress around the weld area is relieved by heating a 100 mm wide band to 700°C.
Austenitization: For austenetising, a 25 mm wide band is heated to 900 °C. It is essential that the temperature through the pipe wall is uniform before quenching.
Through-Tempering: The weld joint is through-tempered by heating the surrounding 50 mm band to 675 °C for producing the correct drill pipe toughness.
Heat Treating Ends of Thin Walled Mineral Drill Pipe
The mineral drill pipes’ internal and external threaded ends are heat treated and surface hardened to get toughened tube-end and to reduce wear due to repeated connecting and disconnecting in the drilling process.
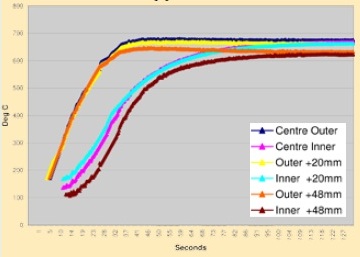
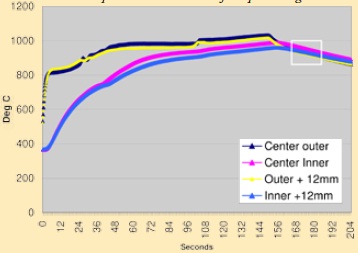
Brazing Diamond or Carbide Inserts onto Oil and Gas Well Drill Bits
Oil and Gas Well Drill Bits
Drill bit production involves individual brazing of multiple tool inserts (usually from 40 to 60) onto a single drill bit. These inserts may be tungsten carbide inserts (TCI) or a polycrystaline diamond compact (PDC). Induction heating is ideal for pre-heating the drill bit to 600°C to prepare the torch brazing of the diamond inserts.

The PDC or TCI inserts are the cutting portion of the drilling tool, so they will wear out with use. Induction heating is used in the reclaiming process to heat up the drill bit, which allows the inserts to be removed for rebuilding the drill bit. (These inserts image is courtesy of U.S. Synthetics, Orem, UT.)
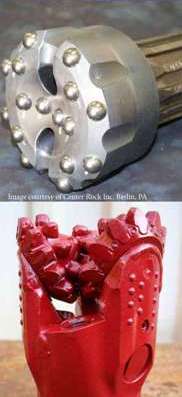
The brazing silver and copper eutectic alloy of the insert has a melting temperature of 790 °C, which is much lower than the melting temperature of copper or silver. This low melt temperature eliminates diamond bit overheating during brazing, resulting in a strong joint to the drill bit.
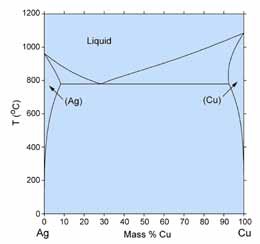
Summary
Ambrell offers EASYHEAT and EKOHEAT systems with various power and frequency levels. Hence, the company can help customers to achieve optimal productivity and cost efficiencies irrespective of their pipe or tube applications. The versatile systems are offered with multiple capacitor and tap transformer configurations. They reduce energy costs by providing efficient power conversion. The user-friendly systems provide repeatable heating through flexible frequency tuning. It is easier to integrate these systems into a customer’s existing process due to their small footprint.
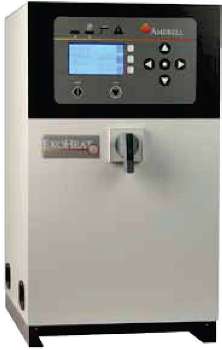
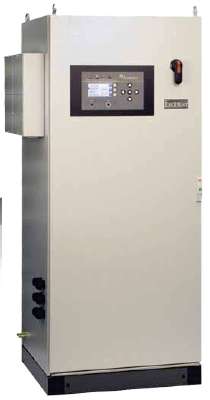
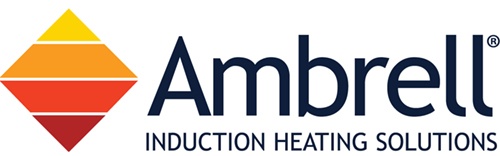
This information has been sourced, reviewed and adapted from materials provided by Ambrell Induction Heating Solutions.
For more information on this source, please visit Ambrell Induction Heating Solutions.