Experience the newest advancements in high-temperature rotational viscometers, the VIS 413, from TA Instruments.
Scientists who need to get melt viscosity data at the greatest temperatures from the widest variety of materials can use the VIS 413 viscometer. Viscosity measurements are now possible with greater precision because of developments in core measuring technology for torque measurement and rotational speed control.
With the viscometer sensor that uses TA Instruments’ exclusive technology, users can measure with greater accuracy over a larger viscosity range. The new robust, user-friendly, and secure reaction atmosphere control system increases the high-temperature viscometer’s range of applications for tests involving air-sensitive materials. This enables the user to simulate harsh environmental conditions like reactive, inert, and vacuum atmospheres.
The new viscometer furnace leverages TA Instruments’ extensive experience in the development and manufacturing of high-temperature furnaces. Consequently, the VIS 413 provides the best temperature uniformity and stability throughout the widest temperature range. Melt viscosity can be precisely measured in the broadest temperature range, thanks to the furnace’s exceptional quality and unique performance.
By significantly minimizing the furnace and sensor's cool-down time, the advanced water cooling system offers superior viscosity measurement stability and safe operation. Reduced idle time increases the instrument’s productivity and enhances the research output.
Sample loading is made easy and safe by the spring-loaded sample crucible holders at the viscometer sensor. Its well-proven design and compact instrument footprint enables the installation and use of the instrument in a glovebox for consistently managing samples that are sensitive to moisture or oxygen.
Specifications
Technical Specifications
Source: TA Instruments
|
VIS 413 |
VIS 413HT |
Viscosity Range |
101 – 108 dPa s |
Sample Temperature Range |
up to 1550 °C |
up to 1750 °C |
Atmosphere |
Air, Vacuum, Inert, Reactive |
Rotor Diameters |
12 mm / 16 mm |
Sample Volume |
26 ml |
Rotor and Sample Crucible Materials |
PtRh, Al2O3, other on request |
Rotational Speed |
0.001 – 300 min-1 |
Compliant Standards |
ISO 7884-2, ASTM C965, ASTM C1276 |
Dimensions W x D |
555 mm x 600 mm |
Technology
Furnace and Atmosphere Control
High-Temperature Furnace
TA Instruments' latest high-temperature furnace technology is included with the VIS 413 viscometer. With two water-cooled furnace setups, sample industry-leading temperatures as high as 1750 °C are available. When comparing competing instruments on the market, the VIS 413’s productivity is doubled because of its integrated water cooling system, which also allows for unmatched short cooldown times.
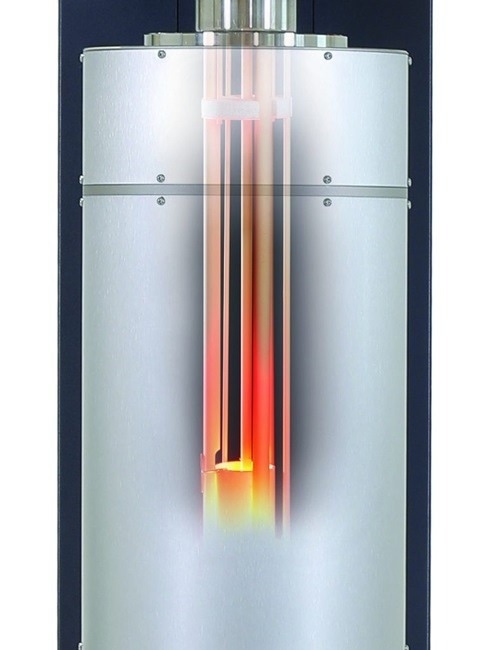
Image Credit: TA Instruments
The advanced high-temperature furnaces, which are supported by decades of design and manufacturing experience, guarantee exceptional thermal stability, temperature homogeneity, and a long lifespan.
The enhanced vacuum-tight construction of the apparatus facilitates the total removal of oxygen from the viscometer before and after an experiment. Viscosity measurements can be conducted in reactive (for example, H2/N2, CO/CO2) or inert (for example, N2, Ar) atmospheres.
These unique characteristics enable the analysis of oxygen-sensitive sample materials, such as coal ash, metals, or salts, as well as the measurement of viscosity in actual environmental circumstances. Reliable ventilation of the reaction atmosphere is enabled by the instrument's specialized gas flow channels and vacuum-tight furnace design, all through a single connection.
This guarantees the greatest safety standards for gas atmosphere experiments that may be hazardous. The new VIS 413 is a flexible, precise, and safe high-temperature viscometer for analyzing any sample material in air or a controlled environment.
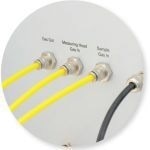
Image Credit: TA Instruments
Atmosphere Control
Reactive gas supply modules can be added to the VIS 413 to provide software-controlled sample evacuation and inert or reactive environment control in the furnace.
The reactive gas module offers certain operational advantages for measuring viscometry in difficult-to-measure samples:
- Compared to simple purging, complete system evacuation improves environment purity faster
- Emulate the actual process environment or consistently regulate the measurement conditions
- To avoid contamination when handling volatile materials, purge the viscometer sensor
- Measure atmospheric reductions such as CO/CO2 and H2/N2 to produce completely oxygen-free environments
- A controlled ventilation channel ensures laboratory safety
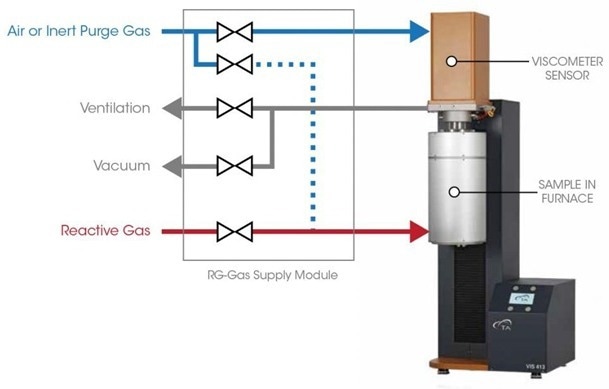
Proprietary furnace technology provides the widest temperature range and exclusive vacuum and reactive atmosphere capability. Image Credit: TA Instruments
Sample Crucible, Rotor, Holders
Sample loading is made simple and safe using VIS 413 viscometers. Ceramic fittings with spring loads secure the sample crucible in place. It is simple and convenient to load samples, even the viscometer is housed in a glove box or fume hood. Ceramic and platinum alloy sample crucibles and rotors are offered.
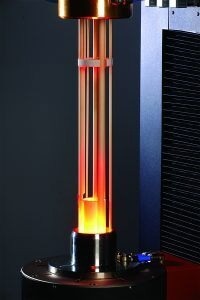
Image Credit: TA Instruments
The ability to swap out measuring systems allows for the selection of the appropriate material for each sample material and client need. The materials used in the measuring system are listed in the table below.
The sample crucible’s practical geometry and the universal rotor coupling enable the provision of bespoke rotors and sample crucibles made of various materials to satisfy the needs of specific customers.
The VIS 413’s thoughtfully designed accessories and design allow for trouble-free, flexible configuration and viscosity measurements of any sample material in air or regulated atmospheres.
Source: TA Instruments
|
Pt-Alloy |
Ceramics |
Type of use |
Re-usable
Typically cleaned by heat and acid treatment |
Disposable
No cleaning required |
Usually applied for |
Glass, Enamel, Casting Powder |
Ash, Slag, Magma, Metals |
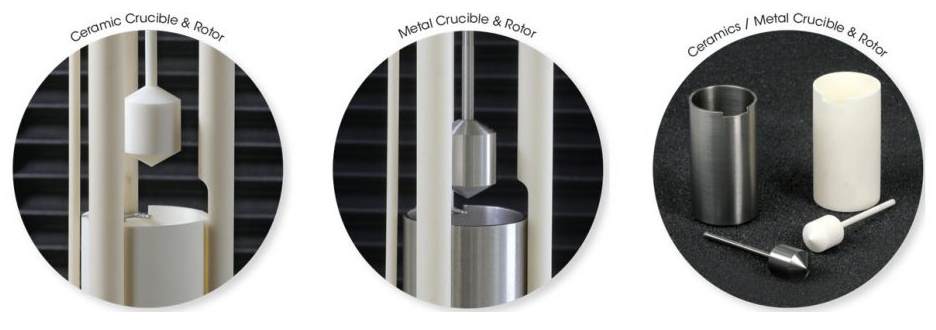
Ease of sample handling through field-proven design with the right choice of measuring systems for each sample material. Image Credit: TA Instruments
Viscometer
At the center of the VIS 413 viscometer sensor is a patented wear-free and frictionless EC motor. Rotational speed control and measurement with the highest accuracy is achieved when used in conjunction with the digital optical encoder. Sealed high-precision ball bearings enable the rotor to be aligned optimally with the least amount of repeatable friction.
Compared to air bearing, the primary benefit is the capacity to function in a vacuum. For high-temperature viscosity measurements in regulated environments, this is a huge advancement.
The EC motor, the optical encoder, and the ball bearings are all protected by the purge gas flow provided by the gas dosing accessory.
This function makes it possible to detect the viscosity of volatile sample materials, which could contaminate the viscometer sensor. The most accurate high-temperature viscosity data is provided by the patented EC motor-based torque sensor, even on difficult sample materials in the largest temperature range and application-relevant controlled atmospheres.
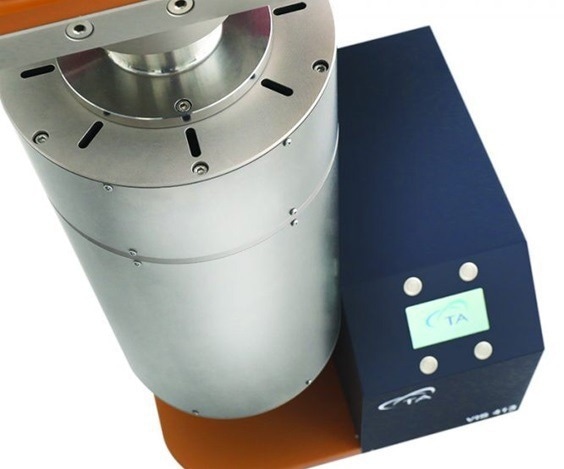
Robust proprietary rheometer provides vacuum capability for higher temperature viscosity measurements on challenging samples. Image Credit: TA Instruments
Applications
Viscosity of Melts at High Temperature
High-temperature melt processing is the foundation for the industrial production of numerous goods, such as metals and glassware, as well as the steady operation of industrial incinerators by the continual removal of slag.
Apart from temperature, the chemical makeup of materials and external factors like the atmosphere also have a substantial impact on their melt viscosity. The viscosity of the molds used in industrial processing is a crucial factor that impacts the economy, environment, and product quality of the operations.
Glass
Glass Industry
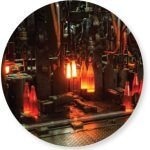
Image Credit: TA Instruments
The industrial production of glass goods, including frits, glass fibers, and float glass, includes the processing of molten glass.
Glass Viscosity
The temperature ranges at which a glass can be worked depends on its viscosity. Determining the proper melting and heat treatment regimes during the production and processing of glass requires the measurement of the temperature-viscosity relationship.
Viscosity, for instance, has a direct impact on a melt's homogeneity and air bubble removal. It allows glass producers to forecast and simulate the glass’s behavior during the forming or glass fiber creation process.
Temperature and glass viscosity are negatively correlated. Viscosity lowers with heat, allowing the glass to flow more easily. Viscosity and temperature have a clear correlation that is related to a glass's chemical makeup. Techniques for measuring and modeling this connection for a variety of glass compositions and temperatures are required by manufacturers.
Most glasses have viscosities that are commonly tested in the 700 °C to 1600 °C range. The viscosity measurements of three glasses with a VIS 413 at high temperatures are plotted vs temperature in the diagram below.
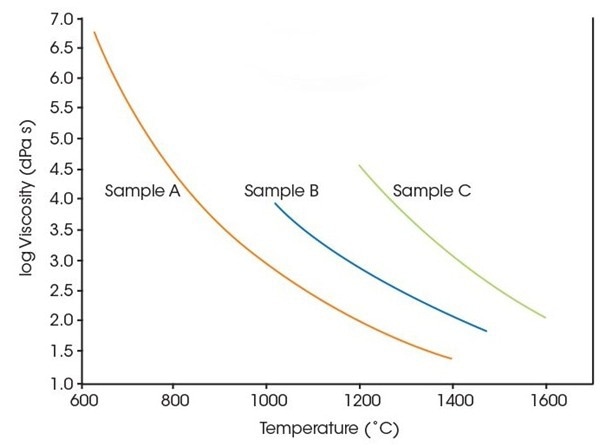
Image Credit: TA Instruments
Learn more about the high-temperature analyzers for glass that TA Instruments offers here:
- Glass materials’ softening points and thermal expansion are measured using high-temperature dilatometers
- Use a heating microscope to study the surface tension and flow characteristics of glassy melts at high temperatures
- Thermal conductivity and temperature diffusivity at high temperatures can be measured using laser flash analyzers
Metals
Metal Industry
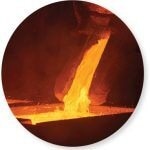
Image Credit: TA Instruments
Both traditional and additive manufacturing procedures include handling molten metal. Casting powder additives are necessary to produce metal products of superior quality.
Metals
Molten metal flows happen in soldering and welding applications, additive manufacturing, and conventional and continuous casting operations. The molten metal’s viscosity is the fundamental quality needed to comprehend, forecast, and enhance these fluxes. In general, molten metals react strongly with oxygen.
Even at the greatest temperatures, measurements in reducing atmospheres, such as forming gas (H2/N2 mixture), are made possible by the VIS 413’s unique vacuum and reactive gas capacity, which prevents metal oxidation.
Casting Powder
Continuous casting procedures require the use of casting powders. The primary purpose of the glassy casting powders is to lubricate the copper mold that is cooled by water and the solidifying metal. Continuous additions of casting powder are made to the top of the mold, covering the liquid steel's free surface.
The powder layer in contact with the liquid steel melts. It then infiltrates into the space between the steel shell and copper mold, providing lubrication. The viscosity of the melted casting powder influences the lubrication. To achieve the least amount of friction, the values must be changed. As a result, the viscosity values of casting powder at temperatures between 1200 °C and 1400 °C are thought to be significant for industrial applications.
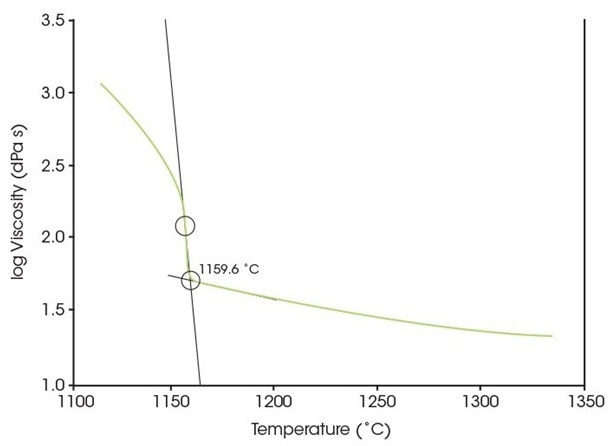
Image Credit: TA Instruments
Here is additional information about TA Instruments’ supplementary high-temperature metal analyzers:
- Quenching dilatometers for studying metal phase transitions during fast deformation and cooling
- Thermal conductivity and temperature diffusivity at high temperatures can be measured using laser flash analyzers
Energy Industry
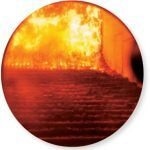
Image Credit: TA Instruments
Energy Industry
The dependability, safety, and efficiency of energy conversion processes depend heavily on the viscosity of melts at high temperatures. In conventional coal-fired power plants and gasifiers, to transform solid fuels into syngas, slag and ash must run down the boiler wall. Melted metals and salts are being studied for cooling and heat transfer in upcoming novel power generation processes.
Coal Ash / Slag
Ash and slag must be taken out of the boiler in coal-fired power plants, coal gasification plants, and waste incinerator plants. Slag needs to be continuously eliminated from the process as feedstock is being provided. Letting the molten slag flow into a quenching bath that it can withdraw from is the most effective approach to accomplish this.
The slag must have a low enough viscosity to allow it to pass through the boiler lining without leaving behind deposits. Fluxing agents can be used to change the viscosity of the slag. The slag viscosity of the utilized feedstock needs to be assessed under boiler operating circumstances to dose fluxing chemicals properly.
Measurements of the viscosity of slag must be done in an atmosphere identical to that of the boiler. As recommended for the measurement of coal slag viscosity, the VIS 413 is capable of conducting measurements in regulated CO/CO2 mixed atmospheres.
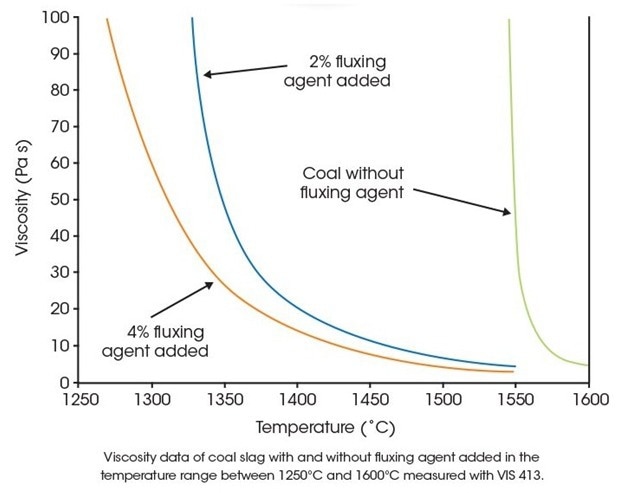
Image Credit: TA Instruments
Salt and Metals as Heat Transfer Mediums
For solar and/or nuclear energy applications, molten salts and low melting temperature metals are material groups with enormous promise as thermal energy storage and heat transport mediums. In addition to other thermophysical characteristics, a successful application requires a viscosity that is low enough throughout the whole temperature range of 100 °C to 700 °C.
Viscosity measurements on metals and salts frequently need to be conducted in inert atmospheres that are dry and oxygen-free. The VIS 413’s special vacuum and environment control features enable viscosity tests on samples that are oxygen- or humidity-sensitive.
Learn more about the high-temperature energy analyzers from TA Instruments that are compatible here:
- Thermal analyzer that measures heat flows and reaction kinetics simultaneously
- High-pressure TGA for monitoring gasification and combustion processes in high-pressure, controlled environments
- Utilizing a heating microscope to examine the fusion of slag and ash at elevated temperatures
Geological Materials
Magma
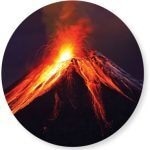
Image Credit: TA Instruments
The primary physical characteristic that controls the formation, movement, and eruption of magma is viscosity. Natural silicate magmas can have viscosities ranging from over 15 orders of magnitude. These differences are mainly caused by changes in temperature, the makeup of the melt, and the amounts of suspended particles and/or exsolved fluid phases.
Improved geological process modeling is based on experimental studies of magma. Partial crystallization occurs when mixed aluminosilicate liquids cool, changing the makeup of the remaining liquid. This may result in intricate variations in magma viscosity that can only be determined through measurement.
The viscosity of basaltic andesite magma is plotted against temperature in the diagram below.
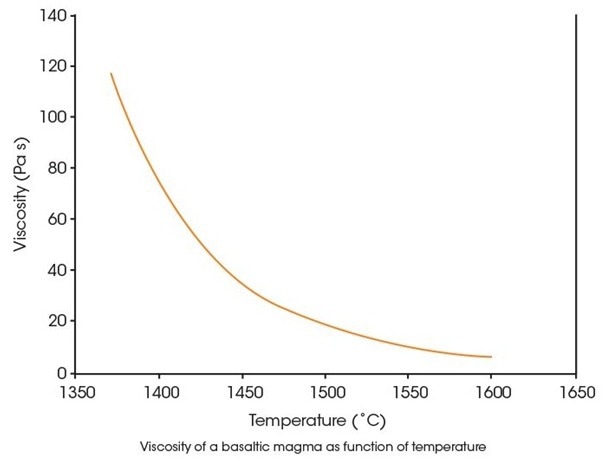
Image Credit: TA Instruments
Learn more about TA Instruments’ complementing high-temperature analyzers for geological research here:
- A thermal analyzer that measures both outgassing kinetics and heat flows at the same time
- High pressure TGA for assessing outgassing and solubility in controlled environments