A team of researchers recently published a paper in the journal Additive Manufacturing that demonstrated the feasibility of using three-dimensional (3D) printed polymer-based optical fibers for sensing applications.
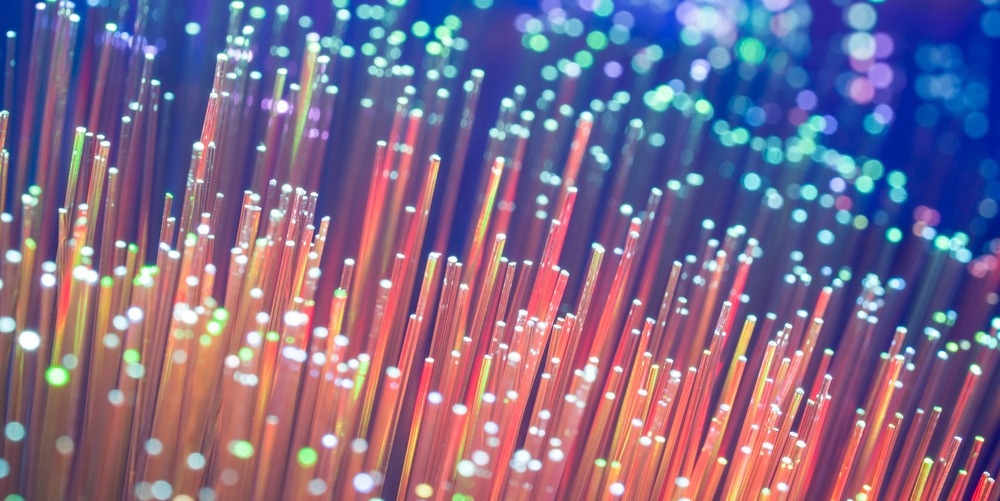
Study: 3D printed polymer composite optical fiber for sensing applications. Image Credit: asharkyu/Shutterstock.com
Background
Temperature sensors are used extensively in several applications, such as medical diagnostics, power generators, air conditioning, and the automotive sector to identify unexpected breakdowns or failures and maintain optimal working conditions.
Although electrical sensors are typically used for temperature sensing, they are less effective in harsh environments and cannot provide accurate readouts owing to magnetic and electrical disturbances.
Optical fiber sensors can operate in harsh environments as they are not impacted by electromagnetic interferences and possess remote sensing capabilities. Optical fibers are flexible, lightweight, and compact, making them suitable as sensors.
For instance, white light interferometers, glass-optical fiber temperature sensors, and Febry-Pérot interferometers have displayed high sensitivity. However, optical fibers have durability issues and are impacted by small mechanical disturbances.
Polymer fiber-based sensors can be used to overcome these issues as these sensors remain unaffected by any ambient disturbance owing to their excellent efficiency and robust strength. Although polymer-based fibers display low sensitivity, they are reusable and relatively accurate.
Polymer fiber-based sensors can be fabricated by molding or drawing. The additive manufacturing (AM)/3D printing process has fundamentally transformed the development of optical analytical and sensing devices by allowing the fabrication of customized optical devices or components of optical systems.
Open-source 3D printers allow the use of customized materials that meet the requirements of targeted applications. Different 3D printing techniques, such as digital light processing (DLP), stereolithographic apparatus (SLA), masked stereolithographic apparatus (MSLA), and fused filament fabrication (FFF) can be used for printing polymeric optical fibers.
Among these techniques, MSLA is more suitable as it is the fastest technique and has the highest resolution. Moreover, various materials can be customized easily in MSLA for complex functionalities, enabling the possibility of identifying different material compositions. Thus, MSLA can be effective for the fabrication of functionalized polymer composites.
Stimuli-responsive materials that display sensitivity to specific external triggers, such as magnetic/electric fields, light, ions, temperature, or pH, can be incorporated into the resin during or after the synthesis of resin to add sensing abilities or multi-functionalities into the 3D printed structures.
The Study
In this study, researchers fabricated thermochromic polymer optical fibers for temperature sensing applications using the open-source MSLA 3D printer. Reversible thermochromic micro-powders were incorporated into the 3D printable polyethylene glycol diacrylate (PEGDA)/polyhydroxyethyl methacrylate (pHEMA) photocurable resin to add thermal sensing functionality to the fabricated optical fibers.
The optical, mechanical, and physical properties of the fabricated 3D printed fibers were characterized, and quantitative optical analysis of the thermal sensing abilities of the fibers was performed in the 25-32 °C temperature range. Researchers also established a correlation between the light intensity and bending angle to demonstrate the strain sensing ability of the fabricated fibers.
pHEMA was selected due to its flexibility and good biocompatibility, while PEGDA, a flexible and long-chain polymer suitable for the fabrication of photopolymerizable polymer, was selected to assist in crosslinking HEMA. TPO can initiate the photopolymerization reaction in the presence of 385-420 nm ultraviolet (UV) light. The thermochromic pigments were non-toxic and sensitive to temperature.
A photocurable resin of PEGDA/HEMA was synthesized by mixing the photoinitiator trimethylbenzoyl diphenylphosphine oxide (TPO), PEGDA, and HEMA at room temperature for 3D printing of the PEGDA/HEMA copolymer-based optical fibers.
Subsequently, thermochromic powders of red, blue, and green colors were added to the as-prepared PEGDA/HEMA resin in stirring conditions. The final samples were designated based on the color of the thermochromic powder added to each sampleFiveve samples were printed for this study, including transparent PEGDA/HEMA without any powder, blue/red PEGDA/HEMA, red PEGDA/HEMA, green PEGDA/HEMA, blue PEGDA/HEMA.
An optical microscope, scanning electron microscope (SEM), UV-visible spectrophotometer, X-ray diffractometer, and a uniaxial tensile machine (UTM) were used for the characterization of the materials and fabricated samples. A custom-made optical setup was developed to investigate the thermal response of the fabricated polymer fibers.
Observations
Functionalized PEGDA/HEMA copolymer-based thermochromic optical fibers for strain and temperature sensing applications were fabricated successfully using the MSLA 3D printing method. The fabricated fibers were extremely flexible due to the flexible nature of the base polymeric materials utilized in their fabrication.
No morphological differences were observed among the colored powders used in the study. All pigments displayed characteristic dips in their transmission spectra based on their color, and such dips were also observed in both printed fibers containing these colors. The sample containing both red and blue pigment powders displayed a larger dip due to the combination of dips of both powders.
The thermochromic powders were crystalline, while all 3D printed samples were amorphous. No reaction occurred between the resin and thermochromic powders during the 3D printing processes and photocuring.
The strength of the polymer-based optical fibers was reduced after the addition of thermochromic powders. The transparent PEGDA/pHEMA sample demonstrated the highest strength and elastic modulus, while the red/blue PEGDA/pHEMA sample displayed the least strength and elastic modulus due to the highest concentration of thermochromic powders.
The micro-sized spherical thermochromic particles were well-distributed throughout the polymer matrix with extremely low agglomeration. Their shape and structures remained almost similar to the original powder even after dispersion. Moreover, the 3D printed layers fused effectively, and no pores were observed between the layers, which indicated the successful fabrication of the polymer-based thermochromic fibers.
Distinguishable colors were observed at 25 oC/room temperature in all samples. However, the samples became transparent at 32 oC and were indistinguishable. The effect was reversible as the colors again became visible when the samples were cooled to room temperature. The fibers displayed the thermosensitive property even after they were subjected to multiple cooling and heating cycles.
The reflectivity of the fibers increased with the rising temperature and became constant at 32 oC as their optical absorption reduced. Hence, the temperature and reflection intensity displayed a linear relationship.
The fibers remotely measured the changes in temperature of a liquid with high accuracy in the 25-32 oC temperature range, which indicated the feasibility of using these fibers for temperature measurements in biomedical environments. The red, green, and blue (RGB) values increased with the rising temperature in all samples, indicating the transparency of the samples due to thermochromic response.
The light intensity reduced significantly in all samples when the polymer fibers were subjected to bending conditions, with the highest reduction observed in green and blue optical fibers. Additionally, the light intensity decreased with the increasing bending angle. This effect can be used to sense bending or strain-related changes to predict structure deformations or failures.
Taken together, the findings of this study demonstrated that flexible, cost-effective, and reusable stimuli-responsive polymer-based optical fibers possess great potential in sensing applications. However, more development and testing are required to use them in real-world applications on a large scale.
More from AZoM: What is Glow Discharge Optical Emission Spectrometry
Source
Elsherif, M., Alam, F., Butt, H. et al. 3D printed polymer composite optical fiber for sensing applications. Additive Manufacturing 2022. https://www.sciencedirect.com/science/article/pii/S221486042200389X?via%3Dihub
Disclaimer: The views expressed here are those of the author expressed in their private capacity and do not necessarily represent the views of AZoM.com Limited T/A AZoNetwork the owner and operator of this website. This disclaimer forms part of the Terms and conditions of use of this website.