The Free-Flex® pivot bearings, manufactured by the Riverhawk Company, are high-technology frictionless limited rotation bearings. The bearing manufacturing process uses brazing and annealing steps that are performed in a batch atmosphere furnace. In order to create a non-oxidizing environment for the heat treatment and brazing processes, Riverhawk used to use a hydrogen atmosphere which was created using hydrogen stored in containers.
As its business expanded and the need arose for a more productive and safer means of creating the hydrogen atmosphere, the company looked for other options for hydrogen supply. After a careful and extensive requirement analysis, Riverhawk narrowed down on the Nel Hydrogen Proton Exchange Membrane (PEM) water electrolysis onsite hydrogen generation method. This article looks into the various considerations that enabled successful implementation of hydrogen generation for batch thermal processing applications.
Discussion
The Free-Flex® flexural pivot bearing from Riverhawk is a compact, easily installable and simply packaged limited rotation bearing that delivers predictable and reproducible performance. Some of the distinct capabilities of the bearing include:
- Precise positioning
- Lubrication-free frictionless operation
- Virtually infinite operational life
The Flex pivot bearings are especially suited for applications that require precise positioning and infinite life, but do not allow lubrication. The flex pivots manufactured by Riverhawk are available in various standard and custom configurations that vary in size, features, construction material, specific configuration and spring rate.
Initially, these bearings were developed for aerospace applications; however, they are now being used in a number of other applications such as medical, military, vacuum experiments and as clean room equipment.
Any application that requires lubricant-free, frictionless and long-life equipment can use these bearings. A few examples of such applications are missile guidance systems, scanning mirror assemblies for ground and satellite applications, vibration sensors and jet engine fuel control.
The pivot bearings were used in the Saturn V rocket engines that were used for the Skylab and Apollo missions, as well as on the Hubble telescope and the Voyager 1 satellite.
Construction of Free-Flex® Pivot
The Free-Flex is made up of flat springs that intersect at 90° and cylindrical counter-rotating sleeves for support. A number of specialized manufacturing steps such as brazing for assembling the internal parts, and annealing to acquire optimum metallurgical properties are part of the production process of these bearings. 410 and 420 stainless steel is used for making standard Free-Flex, while other materials like 455 stainless steel, maraging steel, titanium and Inconel 718 are used for making custom pivots. Figure 1 and 2 illustrate Free-Flex pivots.
.jpg)
Figure 1. Free-Flex® flexural pivot cutaway
.jpg)
Figure 2. Free-Flex® flexural pivot photo
Manufacturing of Free-Flex Pivots
Riverhawk use a batch atmosphere heat treat furnace and a braze-alloy to braze the springs to the body halves in the manufacturing of the flex pivot bearings. Simultaneous heat treatment for specific components used in the assembly is also executed in this furnace. Both brazing and heat treatment are carried out in a 100% hydrogen atmosphere, to prevent oxidation, followed for various metallurgy work.
After unloading a completed batch the furnace needs to be thoroughly flushed of hydrogen using an inert nitrogen flow. Before the start of a new batch and hydrogen is re-injected, enabling the batch-wise use of hydrogen. The hydrogen atmosphere enhances the fluxing of the braze alloy during heat treatment.
Until 2009 Riverhawk made use of hydrogen cylinders to provide hydrogen in the batch heat treat furnace. For every run of the furnace, several hydrogen cylinders were required, and as the production volume increased it was critical to control and manage the supply of hydrogen since an interruption in the hydrogen supply would result in the entire batch being rejected.
Post 2009, Riverhawk adopted a hydrogen supply method that would not interrupt production through on-site hydrogen generation or bulk storage of hydrogen. The PEM water electrolysis method from Nel Hydrogen for generating hydrogen was chosen since it meant the generation of hydrogen did not require an inventory; helping Riverhawk to save the costs involved in construction, permitting and compliance as in the case of bulk storage methods.
Comparison of Bulk Storage Approach and PEM Water Electrolysis On-site Hydrogen Generation
The delivered bulk storage hydrogen approach was not chosen for many reasons, which include:
- Capital costs involved in the storage infrastructure
- Requirements for allowing hydrogen storage
- Permit for Associated project schedule risk
- Ongoing compliance issues with stored hydrogen
- Price variations of delivered hydrogen resulting in complex cost accounting
Riverhawk and Nel Hydrogen personnel had to focus on arriving at a cost effective configuration of a HOGEN hydrogen generator and supporting infrastructure for supplying hydrogen. Calculations would have been easier if Riverhawk had employed a continuous furnace, such as a belt furnace, because the flow rate would have been uniform and continuous.
The batch furnace used by Riverhawk involved complex calculations because the flow rate of hydrogen varied with each step of the furnace cycle: a fast rate for when the furnace is filled, a slower rate for maintaining the atmosphere and finally no flow during the loading and removal of parts. Other factors that affected the precision of the furnace cycles that were used are the size of the Flex pivots in the batch, their specific metallurgy and the number of parts loaded. Generally, the Riverhawk cycle times varied from 6 to 12 hours per batch.
Hydrogen generation by the PEM water electrolysis on-site method provides the following unique capabilities:
- Zero hydrogen inventory
- High levels of hydrogen purity
- Load following
- Compact equipment
- Nearly instant on-off
- Substantial hydrogen pressure suitable for a variety of thermal processes
The on-site hydrogen generation was integrated with an in-house hydrogen surge storage in order to satisfy the requirements of the batch furnace. The choice of generation rate and the pressure and volume of the surge storage vessel are important to ensure high levels of flexibility and to minimize the stored hydrogen volume. The appropriate choice of surge system storage and specific hydrogen generator capacity as per the production requirements can help meet common customer expectations like a minimal volume of stored hydrogen, high expandability and low capital costs per system.
Riverhawk chose the optimum solution on the basis of low costs with maximum expandability to facilitate increased production.
After considering the flow rates, furnace cycles and available equipment models, personnel from Nel Hydrogen and Riverhawk had to choose from numerous PEM water electrolysers and surge storage configurations. The team narrowed down on the hydrogen generator model that was less expensive with a smaller capacity to arrive at an economical solution. This was integrated with a gaseous surge accumulator comprising of six hydrogen cylinders that are filled to 200 psig by the hydrogen generator, acting like a temporary buffer.
This combination of the generator and the surge storage enabled quick filling and provided atmospheric maintenance by incurring the lowest capital and operating costs. The period between furnace cycles does not require hydrogen, and at these times, the generator refills the hydrogen storage accumulator volume automatically. In each furnace cycle, the pressure of buffer volume varied from full-pressure at 218 psig to nearly empty at less than 50 psig. Table 1 shows the example calculations.
Table 1. Example of Hydrogen Surge Storage Calculations
On-Site Hydrogen Generator Combination with Low Pressure Surge Storage Vessel |
Vessel Volume |
High (fill) pressure |
Low (near-usage) pressure |
Total hydrogen volume stored |
Usable volume of hydrogen available |
49 liters (Gas cylinder) |
218 |
50 |
27 scf |
19 scf |
150 gallons |
218 |
30 |
311 scf |
250 scf |
1000 gallons |
218 |
60 |
2079 scf |
1400 scf |
1000 gallons |
435 |
60 |
4002 scf |
3323 scf |
On-Site Hydrogen Generation for Free-Flex Manufacturing
Following the success of the Flex Pivot on the market, Riverhawk incorporated the on-site hydrogen generator and surge storage hydrogen supply system to suit their requirements due to expansions in production. This expanded production meant additional daily furnace cycles.
As a result, Riverhawk conducted a thorough analysis on their hydrogen requirements to accommodate the additional cycles and concluded that it was sufficient to expand the surge storage in order to meet their demands. There was no need to expand the capacity of the hydrogen generator model that they had chosen, even though the capacity of this model could be doubled or even tripled within a few hours.
By using a total of 12 cylinders for surge storage, including the six cylinders added for expansion, Riverhawk was able to successfully increase the daily furnace cycles. Using 12 cylinders pressurized to 200 psig enabled Riverhawk to store a maximum hydrogen inventory of less than 324 scf, which is equal to 10% of the NFPA limit for indoor storage of 3000scf. As a result of this Riverhawk was able to manage its increased production requirements by maintaining the hydrogen inventory level much lower than the NFPA limit, avoiding permit and compliance issues. For future expansions, Riverhawk may continue expanding the surge storage until the maximum capacity of the hydrogen generator is exhausted. In case of expansions beyond this limit, the capacity of the hydrogen generator itself can be doubled or even tripled within a short span of a few hours. Figure 3 illustrates the system configuration that is being used currently.
.jpg)
Figure 3. PEM water electrolysis hydrogen generator with cylinder surge storage capacity
Conclusion
Based on a comprehensive understanding of the heat treatment and brazing processes by the engineering and manufacturing team at Riverhawk, a low inventory and hydrogen generation and surge storage system for furnace process atmosphere supply was implemented. These implementations helped in improving the manufacturing processes and managing increased production requirements of Riverhawk.
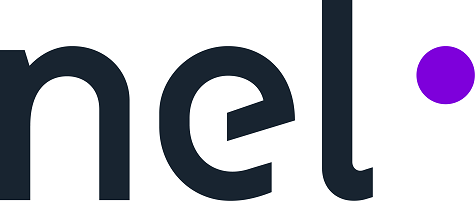
This information has been sourced, reviewed and adapted from materials provided by Nel Hydrogen.
For more information on this source, please visit Nel Hydrogen.