Weathering steel (WS), also known as low‐alloy steel, are steels with a carbon content of less than 0.2 wt. % to which mainly Cu, Cr, Ni, P, Si and Mn are added as alloying elements to a total of no more than 3‐5 wt. % [1]. The chemical composition of these steel alloys is specially formulated to allow the early formation of a rust/iron oxide layer that will provide a weather protective coat to the underlying steel.
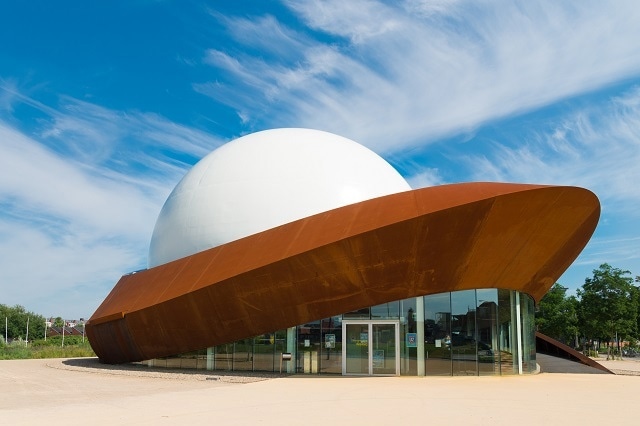
Image Credits: hans engbers/shutterstock.com
The corrosion rate of WS is so low that bridges built from weathering steel can easily achieve a 120 year design life with minimal maintenance [2a, 2b]. In reality weathering steel construction provides a host of additional benefits including lower overall lifecycle costs and improved safety because there is no need for a protective paint system and inspection cycles are reduced [2a]. No requirement for paint also means no volatile organic compounds are released into the atmosphere and more rapid construction. In general the costs of weathering steel bridges are 5% lower than conventional painted steel alternatives when taking from an initial material cost and maintenance point of view.Originally marketed in 1933 to eliminate the need for painting and other maintenance on ore wagons the alloy develops a rust-like appearance or patina, which is now especially sought after by some architects and adorns many well-known buildings and monuments e.g., The John Deere World Headquarters in Illinois and The Angel of the North monument in the UK. The patina on WS not only offers greater corrosion resistance than on mild steel, but is also responsible for its attractive appearance and self‐healing abilities [2].
Chemistry
The superior corrosion properties of WS are nominally based on the increased copper and nickel content of the alloy although other alloying elements (such as Cr, Mn and P) contribute as well. Copper is especially important for bonding the protective oxide layer to the metal and slowing down corrosion [1].
The steel is allowed to rust and because of its alloy composition rusts more slowly than conventional steel and the rust forms a protective coating slowing the rate of future corrosion. Research has shown [3] repeated wet/dry cycling is essential to form the optimum dense and adherent rust layer, with rainwater washing the steel surface well, accumulated moisture draining easily, and a fast drying action. Structures need to be free of crevices where water can collect, as corrosion in these areas would occur without the formation of a protective patina as a recent study of motorway bridges constructed from S355J2W steel in the Czech Republic showed [4].
The oxidation process can continue over a period of several years before steady-state ‘stabilisation’ of the surface occurs with a tightly bonded coating. This largely depends upon the prevailing atmospheric conditions. The contribution of phosphorus and sulphur in the formation of the patina layer is also important with low-solubility sulphates or phosphates developing between the base steel and the existing corrosion, provided the surface is exposed to cyclic wet and dry periods. ISO 9223 [5] indicates that “atmospheres with SO2 pollution allow a more protective rust layer to be formed”. Leygraf and Graedel [3] support this assertion but also believe that large amounts of non-metal oxides result in intense acidification of the aqueous layer and subsequent hindrance of patina formation. Phosphorus species have also been shown to form a protective passive film over the steel surface [6] that prevents the ingress of aggressive ions and moisture and thus supports the formation of a coherent dense patina layer. However phosphorus can have a detrimental effect on the alloy grain structure and consequent mechanical strength of the steel and so low level boron or carbon are added to restore the required grain boundaries [6].
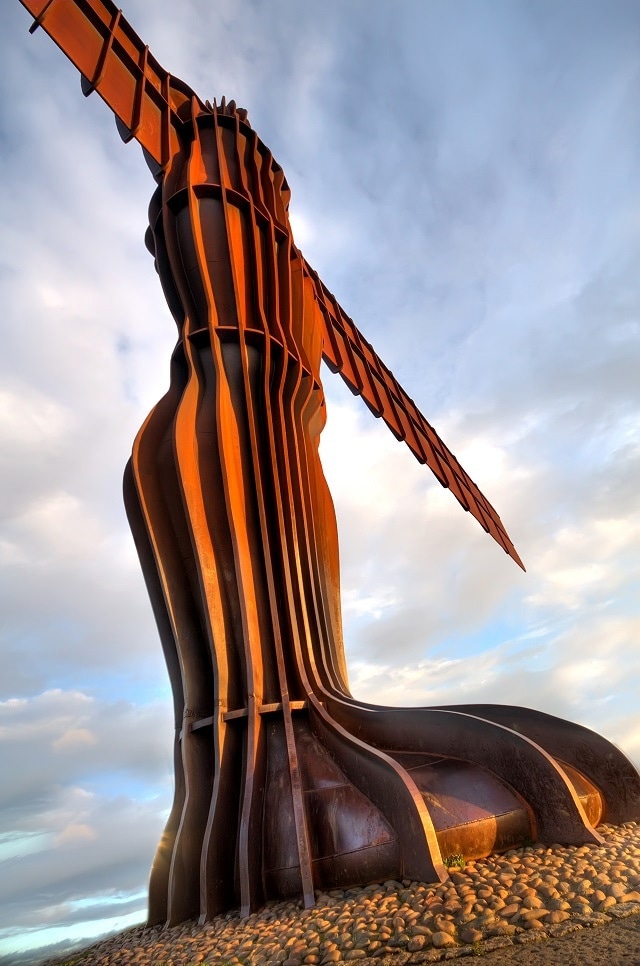
Image Credits: KevinTate/shutterstock.com
Cor-Ten®
One of the best known weather resistant steels is Cor-Ten. The brand name Cor-Ten reflects the two properties that differentiate it from carbon steel (CS), i.e., corrosion resistance (Cor) from its copper component and tensile strength, (Ten) for its superior mechanical properties. In fact Cor-Ten is claimed to provide a 30% improvement of mechanical properties and between 4-8 times more weather resistance than conventional CS [7].
Cor-Ten is available as Cor-Ten A and Cor-ten B. ASTM standard designation A 242 is Cor-Ten A (up to 12.7mm thick) and the newer ASTM grades are A 588 for Cor-Ten B (over 12.7mm thickness). Cor-Ten may be welded using gas shield, spot or submerged arc welding depending upon the thickness of the steel. Care must be taken to weld with a method that allows the rusting to occur in the same way as the bulk of the structure. In general Cor-Ten A and B are similar but Cor-Ten A alloys generally have a higher phosphorus content for additional corrosion resistance.
Grade |
C [%] |
Si [%] |
Mn [%] |
P [%] |
S [%] |
AI [%] |
Cu [%] |
Cr [%] |
Ni [%]
|
Corten A |
0.12 |
0.25/0.75 |
0.20/0.50 |
0.07/0.15 |
0.030 |
0.015/0.06 |
0.25/0.55 |
0.50/1.25 |
0.65 |
Grade |
Thickness (mm) Strip Products |
Plate Products |
Yield Strength RelN/mm²
Minimum |
Tensile Strength RmN/mm²
Minimum |
Elongation Aso%
Minimum |
Corten A |
2-12 |
6-12 |
345 |
485 |
20 |
Grade |
C [%] |
Si [%] |
Mn [%] |
P [%] |
S [%] |
AI [%] |
Cu [%] |
V [%] |
Cr [%] |
Ni [%] |
Corten B |
0.19 |
0.30/0.65 |
0.80/1.25 |
0.035 |
0.030 |
0.02/0.06 |
0.25/0.40 |
0.02/0.1 |
0.40/0.65 |
0.40 |
Grade |
Thickness (mm) Strip Products |
Plate Products |
Yield Strength Rel N/mm²
Minimum |
Tensile StrengthRm N/mm²
Minimum |
Elongation
A50 %
Minimum |
Corten B |
2 – 13 |
6 – 40 |
345 |
485 |
19 |
PATINAX®
PATINAX® is weathering steel produced according to the European standard EN 10025-5 and also as a special mill grade. The protective oxide rust coating produced during the weather resistance process is believed to be “virtually impermeable to oxygen” [8, 9]. PATINAX® is mainly used in its unpainted/coated form and because of its natural weathered rust colour, is typically used for bridges, landscaped structures, power line derricks, containers, mine cars, facades, tanks and steel sculptures. PATINAX® is available in several grades including: PATINAX® 355 (S355J2W) and the higher phosphorus content and more corrosion resistant PATINAX® 355P (S355J2WP) as well as the special mill grade thinner cold rolled sheet version PATINAX® 275PK, which contains the higher phosphorus alloy (S355J2WP).
Grade |
Max. plate thickness [mm] |
Grade acc. to EN 10025-5 |
Alloying elements |
Re, min [MPa] |
Rm [MPa] |
Amin [%] |
T27 [°C] |
PATINAX 355P |
12.5 |
S355J2WP+N |
Cr Cu P |
355 |
470-630 |
20 |
-20 |
PATINAX 355 |
50 |
S355J2W+N |
Cr Cu |
355 (t≤ 16mm) |
470-630 |
20 |
-20 |
Composition of PATINAX 355P
C |
Si |
Mn |
P |
S |
Cr |
Cu |
Ni |
≤0.12 |
0.25 - 0.75 |
0.20 - 0.50 |
0.07 - 0.15 |
≤ 0.030 |
0.50 - 1.25 |
0.25 - 0.55 |
≤ 0.65 |
Steel Grade |
Minimum yield point ReH MPa *) |
Tensile strength Rm MPa |
Minimum elongation A (Lo =5.65√So) % |
PANTINAX 355P |
355 |
470 -630 |
20 |
Steel Grade |
Minimum yield point ReH MPa *) |
Tensile strength Rm MPa |
Minimum elongation A % |
PATINAX 275PK |
275 |
410 |
25 |
Weathering fine grain structural steel
Heavy plates
|
Steel grade |
Material No. |
Material Specification
532
July 2014
|
TKSE-Short name |
EN-Short name |
PATINAX 355 |
S355J2W+N |
1.8965 |
PATINAX 355
C |
Si |
Mn |
P |
S |
Cr |
Cu |
V |
Ni |
≤ 0.16 |
0.30 - 0.50 |
0.80 - 1.25 |
≤ 0.030 |
≤ 0.030 |
0.40 - 0.65 |
0.25 - 0.40 |
0.02 - 0.10 |
≤ 0.40 |
Material thickness
mm
|
Minimum yield point ReH
MPa*)
|
Tensile strength Rm
MPa
|
Minimum elongation A
(Lo =5.65√So)
%
|
≤ 16 |
355 |
470 - 630 |
20 |
> 16 ≤ 50 |
345 |
European Standard Weathering Steels
European EN 10025 specifications weathering steels are very similar to Cor-Ten and PATINAX and there is equivalence for both corrosion resistance and mechanical properties [7].Cor-Ten A and PATINAX 355P are equivalent to EN 10025 S355 J0WP with similar phosphorus content (Cor-Ten A 0.20% vs.
S355 J0WP and PATINAX at 0.15%) for higher corrosion resistance. Corten B and PATINAX 355 on the other hand are the equivalents of European specification EN 10025 S355 J2W and EN 10025 S355 J2W+N respectively with similar tolerances of vanadium, copper, manganese, aluminium and chromium. However in the case of EN 10025 S355 J2W+N and PATINAX 355 to obtain a finer grain structure different combinations of nitrogen binding elements may be alloyed with the steel (e.g., ≥0.02% Aluminium, Nb 0.015-0.060%, V 0.02-0,12%, Ti 0.02-0.10% ) [7,8].
Thickness Range |
|
0.6mm |
0.8mm |
1mm |
1.2mm |
1.5mm |
1.7mm |
2mm |
2.5mm |
3mm |
Corten A |
x |
x |
x |
x |
x |
x |
x |
x |
x |
Corten B |
|
|
|
|
|
|
|
|
x |
S355JOWP |
|
|
|
|
|
|
x |
x |
x |
S355JOW |
|
|
|
|
|
|
|
x |
|
S355J2W+N |
|
|
|
|
|
|
|
x |
x |
S355J2WP+N |
|
|
|
|
|
|
|
|
|
PATINAX 355P |
|
|
|
|
|
|
|
|
x |
Thickness Range |
|
4mm |
5mm |
6mm |
7mm |
8mm |
9mm |
10mm |
12mm |
14mm |
Corten A |
x |
x |
x |
|
x |
x |
x |
x |
|
Corten B |
x |
x |
x |
|
x |
|
x |
x |
x |
S355JOWP |
x |
x |
x |
x |
x |
|
x |
x |
|
S355JOW |
|
x |
|
x |
|
|
|
|
|
S355J2W+N |
x |
x |
x |
x |
x |
|
x |
x |
|
S355J2WP+N |
|
|
|
|
|
|
|
x |
x |
PATINAX 355P |
x |
x |
x |
|
x |
|
x |
|
|
Thickness Range |
|
15mm |
16mm |
18mm |
20mm |
25mm |
30mm |
35mm |
40mm |
50mm |
60mm |
Corten A |
|
|
|
|
|
|
|
|
|
|
Corten B |
x |
x |
x |
x |
x |
x |
x |
x |
x |
x |
S355JOWP |
x |
|
|
|
|
|
|
|
|
|
S355JOW |
|
|
|
|
|
|
|
|
|
|
S355J2W+N |
x |
x |
x |
x |
x |
x |
x |
x |
x |
x |
S355J2WP+N |
x |
x |
x |
x |
x |
x |
|
|
|
|
PATINAX 355P |
x |
x |
x |
x |
x |
x |
x |
x |
x |
x |
Corten A |
Thickness Range |
Available Widths |
|
0.6mm to 12mm |
1000mm, 1250mm, 1500mm, 1800mm, 2000mm, 2500mm |
Corten B |
Thickness Range |
Available Widths |
|
3mm to 60mm |
1000mm, 1250mm, 1500mm, 2000mm, 2500mm, 3000mm |
S355JOWP |
Thickness Range |
Available Widths |
|
2mm to 15mm |
1000mm, 1140mm, 1250mm, 1310mm, 1400mm, 1500mm, 1800mm, 2000mm, 2500mm |
S355JOW |
Thickness Range |
Available Widths |
|
2.5mm to 7mm |
1400mm, 1500mm, 2000mm |
S355J2W+N |
Thickness Range |
Available Widths |
|
2.5mm to 60mm |
1000mm, 1100mm, 1250mm, 1500mm, 2000mm, 2500mm, 3000mm |
S355J2WP+N |
Thickness Range |
Available Widths |
|
12mm to 30mm |
1000mm, 1500mm, 2000mm |
PATINAX 355P |
Thickness Range |
Available Widths |
|
3mm to 60mm |
1000mm, 1250mm, 1500mm, 2000mm, 2500mm, 3000mm |
The above information is based on readily available from stock, where quantity is sufficient for mill production the availability of thicknesses and widths vary.
Conclusion
Weathering steel has been used for structural applications for over 50 years and has a good record for integrity and low maintenance. There are a number of equivalent products on the market such as Cor-Ten, PATINAX and European counterparts. All of these products are equally excellent in providing the required corrosion resistance and mechanical/tensile strength for a wide range of applications from buildings to bridges.
References
- T. Murata, Weathering steel, in: R.W. Revie (Ed.), Uhlig's Corrosion Handbook, J. Wiley & Sons, New York, 2000.
- Armstrong, Robert (14 April 2014). "Metal Building Materials and Corrosion". Absolute Steel. Retrieved 25 September 2014. [2a] http://www.steelconstruction.info/Weathering_steel ; http://resource.npl.co.uk/docs/science_technology/materials/life_management_of_materials/publications/online_guides/pdf/weathering_steel_bridges.pdf . Accessed 16th May 2016 [2b] B. McEleney, Building Blocks: A Primer on Weathering Steel, Structure Magazine, October 2005, p41-44
- C. Leygraf, T. Graedel, Atmospheric Corrosion, Electrochemical Society Series, J. Wiley & Sons, New York, USA, 2000.
- V. Křivýa, P., Konečnýb, Real Material Properties of Weathering Steels Used in Bridge Structures, Procedia Engineering, Volume 57, 2013, Pages 624–633.
- ISO 9223, Corrosion of metals and alloys. Classification of corrosivity of atmospheres, International Standard Organization, Geneve, 1991.
- B.K. Jena, N. Gupta, B. Singh, G. Sahoo, Mechanical properties of low alloy high phosphorus weathering steel, J. Min. Metall. Sect. B-Metall. 51 (1) B (2015) 81 – 87.
- http://xvator.com . Accessed 16th May 2016.
- https://www.nipponsteel.com/. Accessed 16th May 2016
- https://www.thyssenkrupp-steel.com . Accessed 16th May 2016.
- https://www.thyssenkrupp-steel.com . Accessed 16th May 2016.
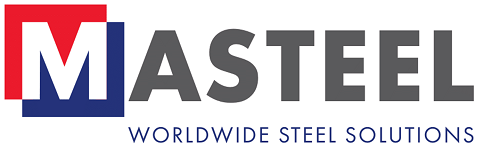
This information has been sourced, reviewed and adapted from materials provided by Masteel UK Ltd.
For more information on this source, please visit Masteel UK Ltd.