Today, it is not advisable to leave the good/bad decision to the wind, and not just because it very rarely blows in laboratories and factories. Distinguishing from the good and the bad reliably and quickly has become more important than ever.
In both the consumer and capital goods industries, the economic success of any product is determined to a large extent by how well the production process, cost, and quality are optimized. Quality assurance in manufacturing relies on fast, robust, and automated test methods.
Structural defects can be detected through the analysis of the dynamic properties of components, assemblies or the final product. Features such as changes in amplitudes, mode shapes, and natural frequencies are characteristic quality markers. Therefore, a quick and automatic good/bad selection can be done on the product or component level with a suitable measurement, evaluation, and classification of these parameters.
Compared to conventional sensors such as microphones or accelerometers, laser vibrometers are particularly suitable for many applications in the final inspection of production as they provide significant advantages. In addition to their large bandwidth and wide dynamic range, vibrometers’ ability to target with pinpoint precision and the non-contact measurement principle are crucial.
Non-contact means that the acquired data is not affected by the measurement method. As there is no physical contact with the sample, integration becomes easier. The technique is not susceptible to ambient noise etc., as the vibrometer captures the vibrations directly on the sample surface. Easy calibration, lower repair expenses, and fast change-over ensure further reduction in operational costs.
Household Appliances and Medical Technology
Laser vibrometers can identify electrically driven medical devices, household appliances, or their components that generate unnecessary vibrations and noise during production, for removal from the line. Vacuum cleaners, washing machines, electric toothbrushes, motors for medical devices, or dental instruments are some examples.
The proper function of advanced medical products including membrane inhalation systems can be confirmed by vibrometers with 100% testing.
The Loccioni Group has worked in close cooperation with the biggest washing machine manufacturers of the world for 40 years, and is a developer of automatic quality control systems for in-process applications and laboratories. The company’s MUSA test station (Measurement Unit in Sound-proof Area) is a fully automated turnkey installation for vibration and noise testing on washing machines - a test that was conventionally conducted in the laboratory.
.jpg)
Figure 1. Testing of washing machines (Loccioni)
Experience shows that reliable results cannot be obtained by conducting spot checks at random on selected systems. High-quality standard can be guaranteed only by conducting 100% testing on the finished products. Vibration tests are a good technique to differentiate good products from faulty ones.
Therefore, vibration analysis is recommended for quality control of household appliances. Laser vibrometry has become an established non-contact method of choice for in-line testing. Laser vibrometer can enable reliable detection of defects such as loose or faulty components or machine tub unbalance.
Automobile Industry and Mechanical Engineering
Laser vibrometers are already used extensively for manufacturing inspection in these areas. They are used to perform failure and noise analysis on components with moving parts including gear drives, injection valves, A/C systems, combustion engines, steering systems, adjusters and miniature drives, and also for material testing, e.g. on light bulbs or camshafts.
Roller bearings are high-precision components that are manufactured on a large scale. SKF is the world market leader, continuously expanding its lead in manufacturing and quality technology. 100% of manufactured roller bearings are inspected by SKF noise.
Highly efficient test systems are essential to achieve goal cycle times of a few seconds. Therefore, SKF Group’s measurement technology center (QTC – Quality Technology Center) decided in the year 2010 to opt for optical measurement technology using IVS sensors from Polytec.
The signal quality, non-contact principle, and low operational costs which are a result of simple calibration, lower repair expenses, and quick sample changeover, are some of the advantages for SKF.
.jpg)
Figure 2. Testing of roller bearings (SKF)
Information and Microsystems Technology
Vibrometers are used as highly sensitive detectors of unwanted deviations in the dynamic behavior of read-write heads and other fine structures in the production of hard drives. Component testing of bubble-jet printers or DVD players is another application.
The dynamic and static properties of microactuators, microsensors, and other MEMS components can be tested during manufacture on the wafer level using the MSA MicroSystem Analyzer or other microscope-based vibrometers.
In many MEMS, material parameters and critical geometric, which cannot be directly measured using non-destructive methods, can be determined from the results of a vibration measurement. Other examples include the determination of membrane thickness of MEMS pressure sensors or the spring thickness of MEMS Fabry-Perot interferometers utilized as tunable IR filters.
The procedure can be fully automated: the structure to be examined is excited in broadband mode on an automatic probe station using a special probe card with a transparent electrode made of indium tin oxide (ITO) and an electrostatic stray field on the wafer. A laser vibrometer is used to measure the mechanic vibrations stimulated in this manner. The measured data and known excitation signal are used to determine the frequency response function and selected resonance frequencies precisely.
.jpg)
Figure 3. Automated testing of Fabry-Perot MEMS sensors (FHG ENAS)
A MEMS model comprised of polynomials is adapted to the resonance frequencies through parameter adaptation. The desired geometry and material parameters are precisely calculated in this manner. Before starting the measurements, the polynomials can be extracted from the parametric FE simulations.
The calculations that are necessary during the series tests for parameter adjustment can be performed with great efficiency. The measurement for all devices on the wafer is completely automated. This approach is highly suitable for 100% inspection during MEMS fabrication.
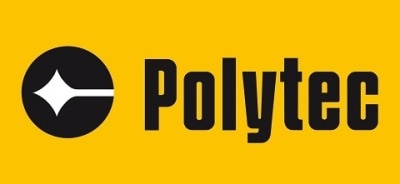
This information has been sourced, reviewed and adapted from materials provided by Polytec Ltd.
For more information on this source, please visit Polytec Ltd.