Potential load/strain scenarios and processes for materials and parts, before the actual deployment, can be determined with the help of simulation and computer modeling. Based on the results, simulation and computer modeling can be further improved, developed and customized to their environments and future applications. A highly precise calculation of mechanical properties can be achieved by combining simulated results with real experimental data. By using this resultant data, service times for newly designed materials can be predicted.
Measuring the Dynamic Response of Solar Panels with Scanning Vibrometers
For example, the mechanical vibrations on solar panels were investigated by researchers at the Fraunhofer Center for Silicon Photovoltaics (CSP) in Halle, Germany. Using this data, the researchers were able to make appropriate design improvements to obtain the best possible service time and stability.
In contrast to traditional contact transducer measurement techniques, the Scanning Vibrometer measurement of solar panel dynamic properties is a non-contact, non-destructive and remote method. Figure 1 shows the distance from the measurement head at the top of the tower to the panel at the bottom. This allows the determination of operational deflection shapes, resonance frequencies as well as material parameters like damping and stiffness without mass loading. Three of the panel’s measured resonance frequencies are illustrated in Figure 2.
.jpg)
Figure 1. Vibration measurement test setup for solar panel characterization using the Scanning Vibrometer.
.jpg)
Figure 2. Frequency spectrum averaged over all 316 measurement points.
As shown in Figures 3 and 4, the operational deflection shapes (ODS) for two of the resonance frequencies are compared to their respective simulation results. The shapes and frequencies substantiate the basic simulation model that has been employed. In order to optimize mechanical strength and thus increase the service time, variable parameters such as mounting/installation techniques and panel dimensions can now be reliably simulated, adjusted and measured to match the predicted application.
.jpg)
Figure 3. First ODS measured at 20.9 Hz (left) corresponding to the simulated mode at 18.7 Hz (right).
.jpg)
Figure 4. Third ODS measured at 63.8 Hz (left) corresponding to the simulated mode at 61.5 Hz (right).
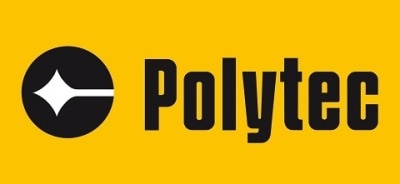
This information has been sourced, reviewed and adapted from materials provided by Polytec.
For more information on this source, please visit Polytec.