Integrated with internal passive air isolators, high-resolution instruments may allow the option to add vibration cancelation motors and inertial sensors to transform passive air isolators into active air isolators. While this method is able to cancel the amplification of the air isolators, not much isolation is gained over the remaining frequency spectrum.
An alternative way is to support the whole instrument on a piezo-driven active vibration isolation platform, wherein the force actuators are in series with the springs supporting the payload, and where the transfer functions of both stages of isolation are additive. When compared to adding active controls to a passive system, this two-stage, passive-over-active approach offers a significantly better vibration isolation.
The need for nano-precision has become more and more important in many research and manufacturing fields such as laser/optical system applications, microelectronics fabrication, materials, life sciences and biological research. As a result, there is a growing need to develop improved vibration isolation technology to allow instrumentation operation under highly precise requirements.
Passive pneumatic vibration isolation, which was the basis for stabilizing the most critical micro-engineering instrumentation in industry and academia, has been shown to be less than sufficient in isolating very low-frequency vibration that negatively affects instrumentation working at atomic scale resolutions.
Many factors can cause vibration that influence high-resolution sub-micron instrumentation. Fans, elevators, pumps and the heating and ventilation system are some of the mechanical devices that produce vibration within the building itself. Defining the distance of the sensitive instrumentation from these vibration sources and the exact location of the equipment in the structure will determine how strongly the equipment is affected.
Outside the building, the equipment can be affected by vibration from various sources such as nearby construction, adjacent road traffic, aircraft, as well as wind and other weather conditions that can promote movement of the structure. These external and internal influences induce low frequency vibration in the range of 1.0 Hz to 50 Hz which is transmitted through the structure and disturbs precision instruments.
In pneumatic vibration isolation systems, this low-frequency vibration may not be sufficiently compensated for and is thus transmitted to the instrument’s sensitive part, affecting image quality, resolution and data integrity. At frequencies below 10 Hz, pneumatic isolators deliver only limited isolation vertically and even much less isolation horizontally. Such isolators can actually create vibration isolation issues in the area of their resonant frequency.
Also, all isolators amplify at their resonant frequency and begin to isolate above this frequency. Pneumatic isolators amplify vibration in the usual range of 1 to 4 Hz, and therefore sensitive instruments produced with internal air isolation are subject to vibration problems.
Further taxing pneumatic isolation functionality is the growing trend of locating highly sensitive instrumentation- electron microscopes, scanning tunneling microscopes, laser interferometers and optical profilers- in building locations where vibration levels are high such as upper floors.
With vibration-handicapped environments becoming more common for the placement of high-sensitive instrumentation, there is a need for better vibration isolation solutions than what is currently available with the instruments' internal pneumatic isolation systems, which are designed for less than severe vibration environments.
Converting an Internal Passive Air Isolator to an Active-Controlled Air Isolator
At locations with high levels of vibration where the internal pneumatic isolation of the instrument is not sufficient, instrument manufacturer is likely to design in an upgrade path – the option to convert the instrument's passive isolation system into an actively controlled system.
This option may appear to be attractive because of the space efficiencies of locating the actively controlled system within the instrument itself instead of requiring an instrument supporting, vibration-isolation platform. However, there is a slight improvement in vibration isolation performance when internal passive air isolators are converted to actively controlled air isolators.
In order to convert passive air isolators to active air isolators, cancelation motors and inertial sensors are installed. The sensors are then added to the payload which measure X, Y and Z vector vibration, which is fed to a controller. The controller, in turn, instructs an equal and opposite force to be exerted via actuators to cancel the payload motion. This active-feedback control system constantly monitors the payload that it is controlling, and based on the vibration data measured, alters its output.
This results in a parallel-type active isolation system, as the force actuators are in parallel with the springs supporting the payload. The resonant frequency of the air isolator will be suppressed between 1 and 4 Hz by the active vibration control of the passive air isolators.
While the performance of the air isolator in this frequency range is improved by active cancelation, not much additional isolation is gained over the remaining frequency spectrum between 1 and 50 Hz. The upgrade to this parallel type of active isolation will not provide much benefit, unless the need for improved vibration isolation is restricted to the 1 – 4 Hz range.
Usually, problematic floor vibration will be seen over the frequency range of 1 – 50 Hz. This means any enhancement to the passive isolators should perform over this range. Also, structural resonances in the instrument pose a problem for an active control system. As the active control sensors are located on the isolated payload, they find it difficult to distinguish between structural resonances of the instrument and vibration in the environment.
Hence, active control sensors should be “de-tuned” (low gain) to avoid creating feedback loop instability. However, this process restricts the sensors’ performance to a narrow frequency range.
Internal Passive Isolator Supported on a Piezo-Driven, Active-Isolation Platform
Supporting the whole instrument on a piezo-driven, active vibration isolation platform is an alternative and better solution to the rather ineffective parallel-type active vibration isolation method for instruments fitted with internal passive air isolators. In such an active vibration isolation platform, the force actuators are in sequence with the springs supporting the payload, and also the transfer functions of the two stages of isolation are additive.
This two-stage, passive-over-active approach offers better vibration isolation in comparison to integrating active controls to a passive system.
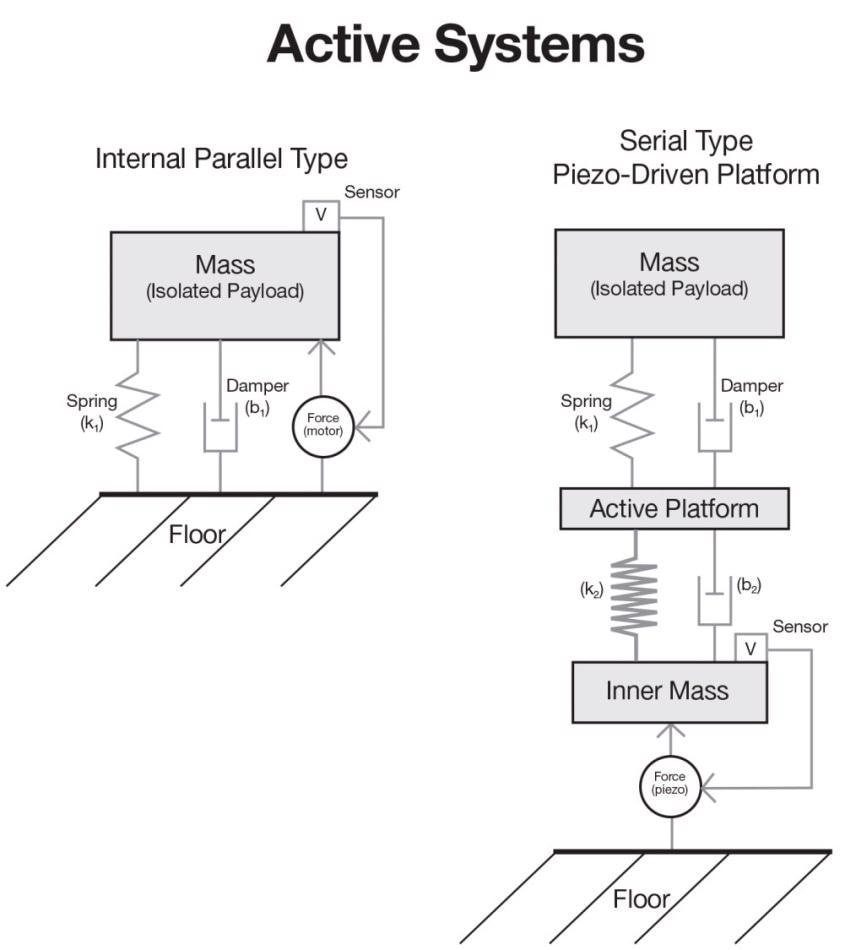
Figure 1. Internal parallel-type active system versus serial-type piezo-driven active platform.
The stacking approach, however, will offer 30 decibels more isolation at 10 Hz when compared to upgrading a 2 Hz air isolator to an actively-damped 2 Hz air isolator. While the serial approach can be stacked, parallel-type approaches are not stackable and involve technical risk.
Utilizing precision piezoelectric actuators and stiff passive springs, the serial configuration makes the entire stiffness of the system extremely high. Therefore, such an active “hard-mount” system is more than 100 times stiffer than the usual pneumatic system. One key benefit offered by a hard-mount is that softer systems, including parallel-active pneumatic systems or passive pneumatic, are stackable on the hard-mount platform without the coupling of the two systems. This is attributed to the broad separation of their resonant frequencies.
The serial-type control system does not sense payload motion, but only floor motion. Therefore, in a serial-type system, stability and vibration cancelation performance is unaffected by payload motion or resonances. Thus, the serial-type system is intrinsically stable.
Through the stiff elastomer mount, the sensor is decoupled from the payload and detects only floor vibration. Subsequently, the measured vibration is canceled through the piezoelectric actuators. As a result, the floor vibration measurement and the resultant feedback cancelation effort is not affected by the motion or resonances of the payload.
The piezoelectric transducers employed in serial passive-over-active isolation are perfect for achieving extremely low frequency performance due to their response and stiffness across a wide frequency range. This is the result of the high stiffness of the PZT (lead zirconate titanate) stacks, which contains layered structures of specialized PZT ceramic interleaved with electrodes.
When a voltage is applied, the length of the ceramic undergoes a major change. This allows the use of actuators for fast, high-force, real-time position control at the nanoscale level. Compared to traditional actuators, PZT materials deliver excellent precision performance, thanks to their solid-state nature.
Performance
Serial-type passive-over-active systems are capable of maintaining active vibration isolation between 0.6 and 150 Hz. Owing to the additive performance of the serial active – passive pneumatic combination, serial-type passive-over-active systems provide cancelation across a broad frequency range, considerably surpassing what active isolators or passive isolators can achieve separately.
In the 0.6 to 4 Hz range, performance with serial-type passive-over-active systems effectively removes the amplification induced by the passive system. It reduces vertical and horizontal vibration by more than 50% at 1 Hz and more than 90% at frequencies above 2 Hz.
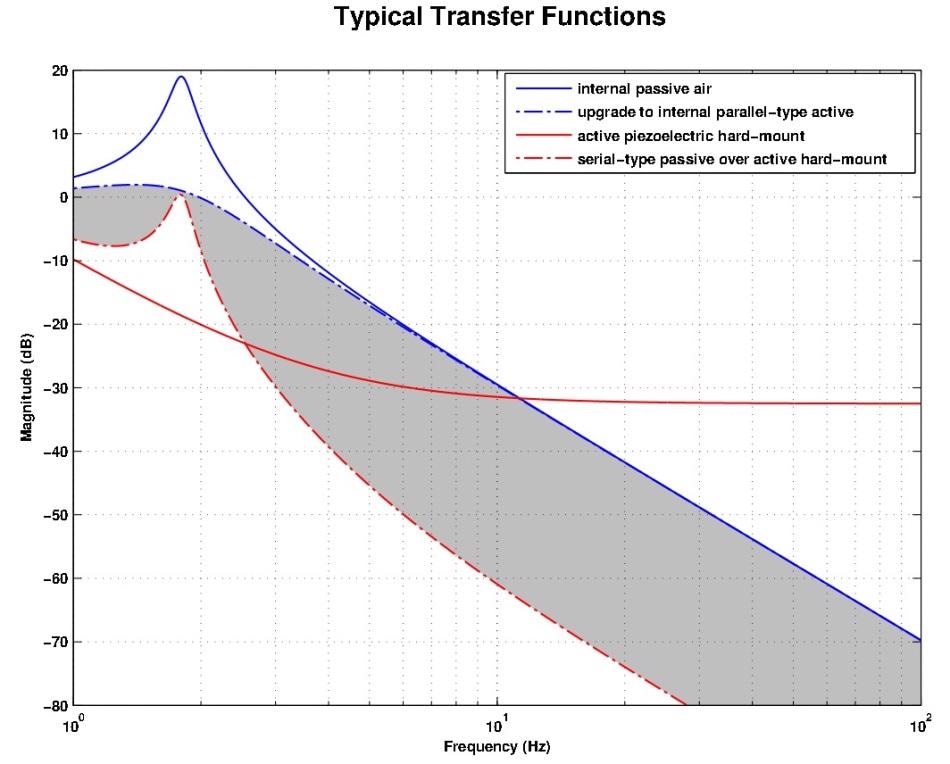
Figure 2. Typical transfer functions. The shaded area indicates the improved performance when installing an instrument with internal isolators on a piezo-driven active cancelation platform, compared to installing parallel-type, motor-driven air active cancelation in the payload and installing the instrument on the floor.
Floor vibration criteria in many precision instruments should be met to obtain their performance specifications. If a site fails to meet these requirements, either the instrument should be moved to another site or an appropriate vibration isolation solution should be applied. A highly effective vibration isolation solution is provided by serial-type passive-over-active systems across a wide frequency range, allowing instruments with internal passive air isolation to be deployed in environments that would otherwise be too noisy for effective operation.
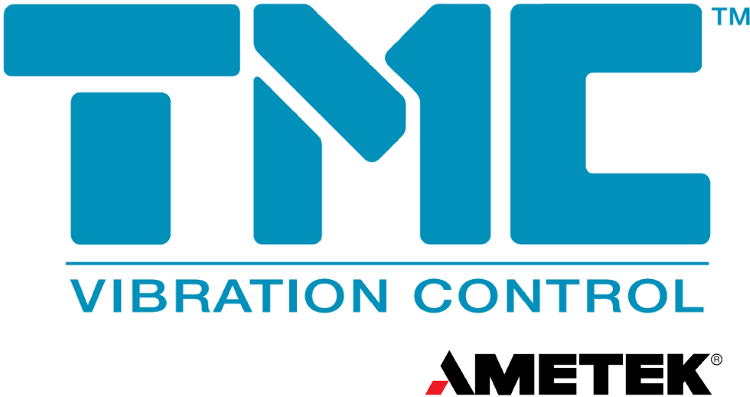
This information has been sourced, reviewed and adapted from materials provided by TMC.
For more information on this source, please visit TMC.