Interview conducted by Mychealla RiceJan 2 2018
Fouling can severely impact the performance of processes and instrumentation in just about every industry and is a costly surface problem.
In this interview, Dr David Smith, R&D Manager from Silcotek talks to AZoM about their range of anti fouling and coking solutions that can help many applications and industries.
Please tell us a bit about Silcotek and the work you do?
SilcoTek® is a company that provides coating services for customer-supplied parts. It is our mission to create game-changing coatings that will improve the performance of our customers’ parts beyond their expectations.
Our coatings are deposited via thermal CVD, are thin (< 2um), conformal, coat the entirety of a 3-dimensional part (including interiors, blind holes, and over long lengths of tubing), performed in bulk, and are cost effective.
They provide surfaces with exceptional chemical inertness, improved corrosion resistance, low stiction /controlled surface energies, and anti-fouling capabilities.
SilcoTek was became an independent company in 2009, but existed as a Performance Coatings division of Restek Corporation beginning in the late 1990’s.
What impact can fouling and coking have on industrial applications? Why is it an issue?
Fouling is the deposition of by-products or otherwise unwanted material on a surface. As a result, and depending on the environment, fouling can cause a variety of many problems, including:
- increased weight
- process contamination
- reduced flow
- increased drag
- inefficient thermal transfer
- surface corrosion
- increased maintenance
- false results/analyses
All of these issues add up to increased costs in operation efficiency and function.
Please tell us about Silcotek’s range of coating solutions for anti-coking and fouling?
There are different mechanisms for the source of fouling, depending on species of foulant and the surface that it binds to.
In one example, a hydrocarbon-based liquid is exposed to high temperature, causing it to thermally break down in to carbon deposits that precipitate out on to a surface. In a second example, a hydrocarbon-based liquid at high temperature is exposed to a nickel-containing surface which causes a catalytic breakdown of the hydrocarbon to form carbon deposits on the surface. With these two potential mechanisms, what can a coating do to prevent fouling issues?
A coating cannot prevent the formation of carbon deposits in example 1. If the hydrocarbon is unstable at high temperature, coke may form no matter what surface it comes in contact with. However, in this case, a low energy surface with a high hydrophobicity/oleophobicity may prevent adhesion of the coke to the surface.
The chemistry of the surface will then determine whether or not the foulant formed will stick to a surface or simply move along with flow and not accumulate. SilcoTek has several treatments, which through their unique surface chemistries may prevent accumulation of foulant on the treated surfaces.
SilcoKlean® is an amorphous silicon deposition with an alkyl surface functionalization that has been proven to prevent coke accumulation in high temperature fuel flow systems, fuel injectors, and internal combustion engine pistons and components. Several studies have been published highlighting the performance of SilcoKlean®.
Dursan® is a silicon, oxygen, carbon deposition with alkyl surface functionalization that has been shown to prevent biofouling (e.g. protein sticking) in medical analysis device applications.
Protect your Equipment from Corrosion - Dursan® from SilcoTek®
Protect your equipment from Corrosion with Dursan®
Scientists at SilcoTek Corporation and Abbott Laboratories have co-written a paper documenting this characteristic of Dursan. SilcoTek also has a low energy surface treatment currently in the beta-test phase that is very stable to thermal oxidation and maintains an extremely high level of hydrophobicity and oleophobicity.
In the case of SilcoKlean® and Dursan®, these two depositions provide an excellent barrier coating to prevent contact with substrate metals, such as nickel (example 2), that react catalytically with hydrocarbon materials to readily form coke deposits.
Since the substrate metal beneath the coating cannot react with the hydrocarbon, one coking mechanism can be eliminated. This significantly reduces the potential for coke formation.
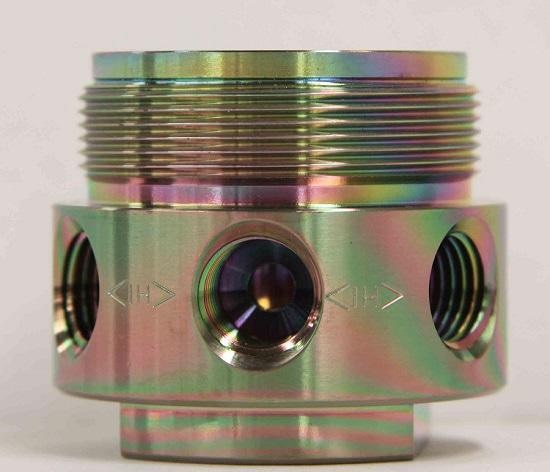
Dursan® from SilcoTek can prevent biofouling in medal analysis equipment
How can CVD coatings help improve fuel efficiency in aerospace and automotive applications?
When coke deposits form from inefficient hydrocarbon degradation, it can accumulate on many different surfaces within a variety of engine components. These include fuel injection systems, fuel exhaust systems, fuel flow lines, sensors, exhaust treatment systems such as EGR components and turbocharger components.
The efficient function of any fuel combustion system relies heavily on the design specifications which are optimized for flow, fuel mixing, heat transfer, sensor operation, etc. Any accumulation of foreign material on any of these systems will severely disrupt the function of that part, causing inefficiencies that can rob horsepower, thrust, flow, fuel consumption, sensitivities, and thermal transfer.
To prevent fouling in these applications with surface coatings and treatments is to maintain the efficiencies and performance of the original design.
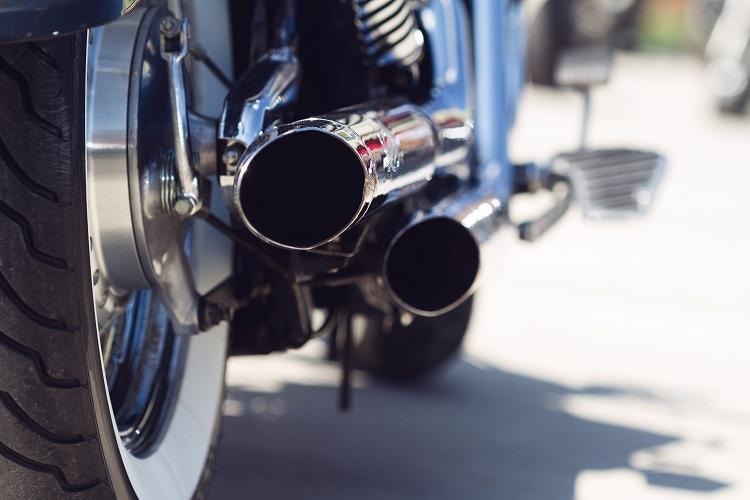
CVD coatings can help improve efficiency for fuel exhaust systems and prevent fouling and coke deposits from forming Image Credit: shutterstock.com/Macondo
Can SilcoTek coatings perform under extreme pressure and temperature? What applications will benefit from this?
SilcoTek coatings perform equally well under a wide range of pressures. For example, sampling cylinders’ pressure ratings are not altered despite having been coated. There are no examples that I can recall where high (and low) pressures alone affected the performance of a coating.
There are temperature limitations for SilcoTek treatments, but they are impressively stable to high temperatures in challenging environments. Dursan has an operating limit of 500°C in an inert atmosphere environment and 450°C in an oxidative environment.
SilcoKlean has a temperature limit of 450°C in an inert atmosphere environment and 400°C in an oxidative environment. The beta-test treatment with high hydrophobicity and oleophobicity has shown excellent stability up to 300°C in an oxidative environment.
There are many potential applications that would benefit from these characteristics. Fuel injection systems and fuel line systems are typically under high pressure and elevated temperature. Exhaust systems, sensors, and recycling/treatment components are also exposed to high temperature and pressure. Having a robust surface treatment capable of performance in these challenging conditions is critical.
How can anti fouling CVD coating ensure accurate results in medical diagnostics and pharmaceuticals?
Medical diagnostic equipment is continuously in contact with bodily fluids or biological molecules used as markers or reactants to perform diagnostic analyses. Many of these molecules exhibit the tendency to “stick”, often through their protein structures, to the surfaces of instrumentation components, sampling systems, fluid transfer systems, etc.
When this type of biofouling occurs on diagnostic equipment, the result can be inaccurate analyses due to sample loss and/or carry-over from one sample to another. This is a serious issue, as equipment in this application arena is used to diagnose disease and help determine the proper course of action on a patient.
Much of the medical diagnostic equipment is constructed with stainless steel components, and stainless steel is known to bind or react with many protein-based biomolecules.
Dursan on these stainless steel surfaces, however, has been shown to reduce or eliminate adhesion of biomolecules and therefore allow the diagnostic equipment to provide true and accurate analyses for highly important applications.
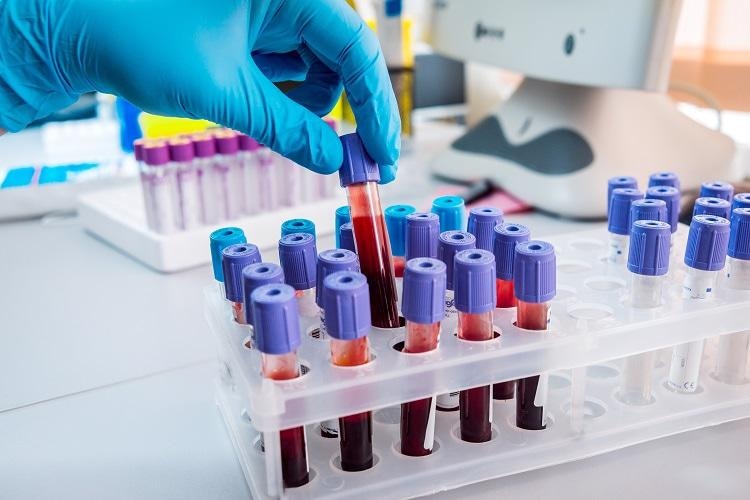
CVD coatings can prevent biofouling on many medical diagnostic and pharmaceutical equipment Image credit: shutterstock.com/Romaset
Additionally, medical diagnostic equipment may use solvents, acids, and bleach for rinsing and cleaning routines, which can be corrosive to the stainless steel component over time.
Dursan is an excellent anti-corrosive barrier that will extend maintenance cycles and increase instrument up-time.
Data in support of the performance of Dursan in diagnostic systems can be found in the following paper: “Protein-resistant properties of a chemical vapor deposited alkyl-functional carboxysilane coating characterized using quartz crystal microbalance” Vaidya, S.V.; Yuan, M.; Narvaez, A.R.; Daghfal, D.; Mattzela, J.; Smith, D. Appl. Surf. Sci. 2016, 364, 896-9.
Where can our readers go to find out more?
SilcoTek’s website contains many pages of technical data, blogs, white papers and references relative to anti-fouling solutions.
We also have an excellent technical service staff that would be happy to discuss your fouling issue and how SilcoTek may be able to help.
About David Smith
David Smith has a Ph.D. in chemistry and has focused on the field of silicon chemistry since 1988.
David is currently the R&D Manager at SilcoTek Corporation and has been on the SilcoTek R&D team since the company’s incorporation in 2009.
David was the founding member of the original Performance Coatings group at Restek Corporation in the late 1990’s, which eventually grew to form SilcoTek as an independent company. He is the author or co-author of several patents for many SilcoTek products and processes.
Disclaimer: The views expressed here are those of the interviewee and do not necessarily represent the views of AZoM.com Limited (T/A) AZoNetwork, the owner and operator of this website. This disclaimer forms part of the Terms and Conditions of use of this website.