In cement sectors, including other industries, sample preparation is a vital step to guarantee that XRF analyzes are truly effective. To attain reliable and accurate XRF results that adhere to the official standard test methods for analysis of cement and raw materials, it is vital to delivering good quality samples to the spectrometer for measurement.
Crushing and Grinding the Sample
The first vital point is the sampling. The size and nature of material selected should be enough to represent the sample mass of interest. For fine-grained samples, this could be just 200-500 g, but for coarse-grained samples, it is not unusual to begin with 10–15 kg.
If the sample grain size is greater than 12 mm, the whole sample is initially crushed in a jaw crusher. During this step, it is vital that the time the material is in the crusher is decreased to a minimum in order to avoid excessive contamination or alteration of the sample. A jaw crusher, such as the BOYD Elite, is the perfect tool for that. Featuring bottom and top moving jaws, the crusher delivers the maximum amount of crushing, decreasing sample by 35 times its original size in only one pass. For practical reasons, it is also vital that the jaws can be readily cleaned.
This is followed by splitting the crushed sample as many times as needed in order to obtain a portion of approximately 250 g. Taking a representative split from a huge sample is not as simple as many people believe. Rolling on a mat, multiple grabs, or riffle splitting do not produce precise results. A classic study performed at Bradford University showed that a rotating sample divider (RSD) provided the best results. Table 1 presents the standard deviation obtained using different dividing techniques.
Table 1. |
Dividing methods samples % |
Standard deviation |
Cone and quartering |
6.810 |
Scoop sampling |
5.140 |
Riffle splitting |
1.010 |
Table sampling |
2.090 |
Rotating splitting |
0.125 |
Random variation |
0.076 |
Source of Contamination Through Grinding
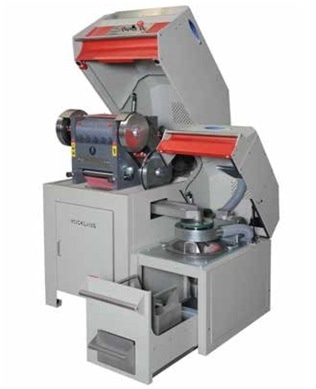
BOYD Elite RSD combo
There are two key sources of contamination during the crushing and pulverizing: (1) the previously pulverized sample (cross contamination); and (2) the grinding container.
- To reduce contamination from the earlier sample, the grinding head and the jaws are cleaned after each run - by employing a portion of the next sample to grind that is discarded after use. Alternatively, a run of pure silica can be employed, followed by a rapid cleaning to avoid contamination by SiO2.
- This source cannot be prevented, but the appropriate choice of grinding containers can decrease the contamination to elements that are irrelevant. For instance, a tungsten carbide head would not be used when W and Co are important to the analyst. Data can be provided on the contamination expected from the different grinding containers.
It is very important at this stage to treat all samples the same way in order to keep the systematic error to the same level. This makes the results more precise, reproducible, and comparable. Always use the same grinding container, grinding time, and amount of sample.
Method of Specimen Preparation
Two techniques are used for the preparation of the specimen: (1) confection of compressed powder tablets; or (2) preparation of beads or glass disks by fusion.
- For the pressed tablet technique, the sample must be ground as fine as possible (to below 75 µm), attempting to restrict the particle size distribution, in order to obtain a fine powder. This powder is then pressed with or without adjuvants in order to obtain a pressed tablet or briquet.
- The fusion technique comprises of the reaction at a high temperature between a molten borate flux and the specimen in order to develop a homogeneous molten glass. For XRF work, the molten glass is cooled without crystallizing to produce an amorphous homogeneous solid glass disk, with a polyborate glass structure.
A combination of the RSD and BOYD Elite, have been designed to work together for a one-step crushing and splitting process to minimize operator intervention and perfect division every time.
This portion of 250 g is then pulverized to a powder fine enough to pass through a 100 µm opening size sieve. Theoretically, the finer the better, but too much pulverizing can lead to serious contamination.
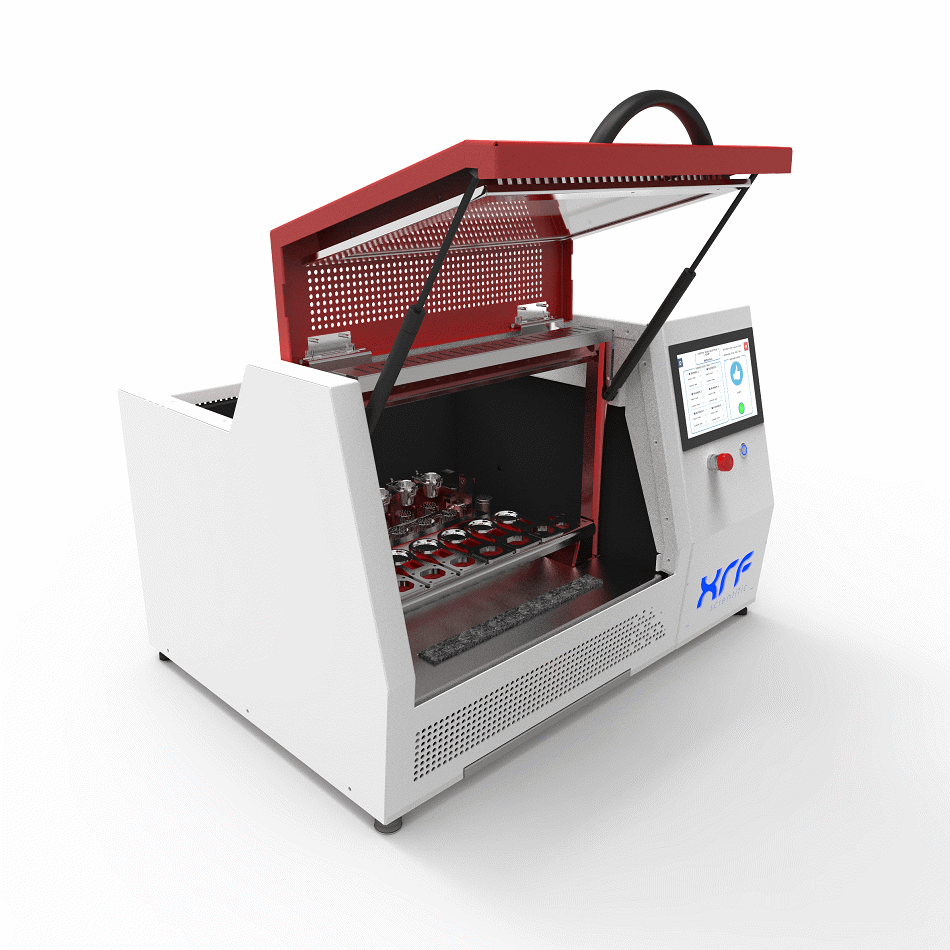
Phoenix 2
The Perfect Specimen
For the X-ray fluorescence (XRF) analysis, the best preparation method to get a completely homogenous and representative specimen is by the fusion technique. The flat glass disk obtained by fusing the powder samples offers more accurate analytical results compared to the pressed pellet. This method overcomes all the problems linked with the variation in mineral grains and others mineralogical effects.
In the cement industry, fusion is currently often used as the reference method and replaces the standard wet chemistry methods for major elements.
Using this preparation technique, it is possible to construct a robust calibration curve covering the complete range of concentrations for the elements of interest in the cement industry, including the raw materials.
Perfect Bead Repeatability
In order to develop repeatable fused glass disks, it is vital to have perfect control of the fusion conditions. Modern fusion machines are significantly more sophisticated, and the process of the preparation of the fused glass disk is carried out fully and automatically with a perfect control of the conditions and in a safe environment. Existing systems use gas or electrical heating and this is the case with Phoenix gas fusion machines, and the xrFuse electric fusion machines, developed by XRF Scientific.
Both machines allow the operators to load the crucibles containing the sample/flux mixture, start the program, and return after 12 min. in order to collect the glass disks, all conducted in a safe enclosed environment.
Comparison Between Gas and Electrical XRF Scientific Fusion Machines
There is a huge difference between a gas and an electric fusion machine, but the most vital thing is that they both reach the same performance level and meet the needs for the actual norms. A good way to examine this is using the “Rapid Test Method” as proposed in the ASTM C114-15 norm.
Table 2. |
|
Norm C114-15 |
xrFuse 2 |
Phoenix |
Precision |
Accuracy |
Precision |
Accuracy |
Precision |
Accuracy |
Na2O |
0.03 |
0.05 |
0.01 |
0.03 |
0.00 |
0.03 |
MgO |
0.16 |
0.20 |
0.01 |
0.17 |
0.01 |
0.15 |
Al2O3 |
0.20 |
0.20 |
0.13 |
0.12 |
0.13 |
0.12 |
SiO2 |
0.16 |
0.20 |
0.15 |
0.15 |
0.12 |
0.16 |
P2O5 |
0.03 |
0.03 |
0.00 |
0.01 |
0.00 |
0.01 |
SO3 |
0.10 |
0.10 |
0.05 |
0.06 |
0.01 |
0.05 |
K2O |
0.03 |
0.05 |
0.01 |
0.03 |
0.00 |
0.03 |
CaO |
0.20 |
0.30 |
0.18 |
0.24 |
0.12 |
0.19 |
TiO2 |
0.02 |
0.03 |
0.00 |
0.01 |
0.00 |
0.01 |
Cr2O3 |
/ |
/ |
0.00 |
0.01 |
0.00 |
0.01 |
Fe2O3 |
0.10 |
0.10 |
0.04 |
0.05 |
0.01 |
0.04 |
ZnO |
0.03 |
0.03 |
0.00 |
0.01 |
0.00 |
0.01 |
SrO |
/ |
/ |
0.00 |
0.00 |
0.00 |
0.00 |
Mn2O3 |
0.03 |
0.03 |
0.00 |
0.01 |
0.00 |
0.01 |
The ASTM C-114 norm covers the chemical analysis of hydraulic cement, explaining all the test methods employed for chemical composition analysis of cement. XRF is mentioned an example of “Rapid Test Methods.”
The technique has to be validated with acceptable certified reference materials (CRMs). The standards employed for this test are the Reference Materials 601B, containing 15 different standards from the Japan Cement Association.
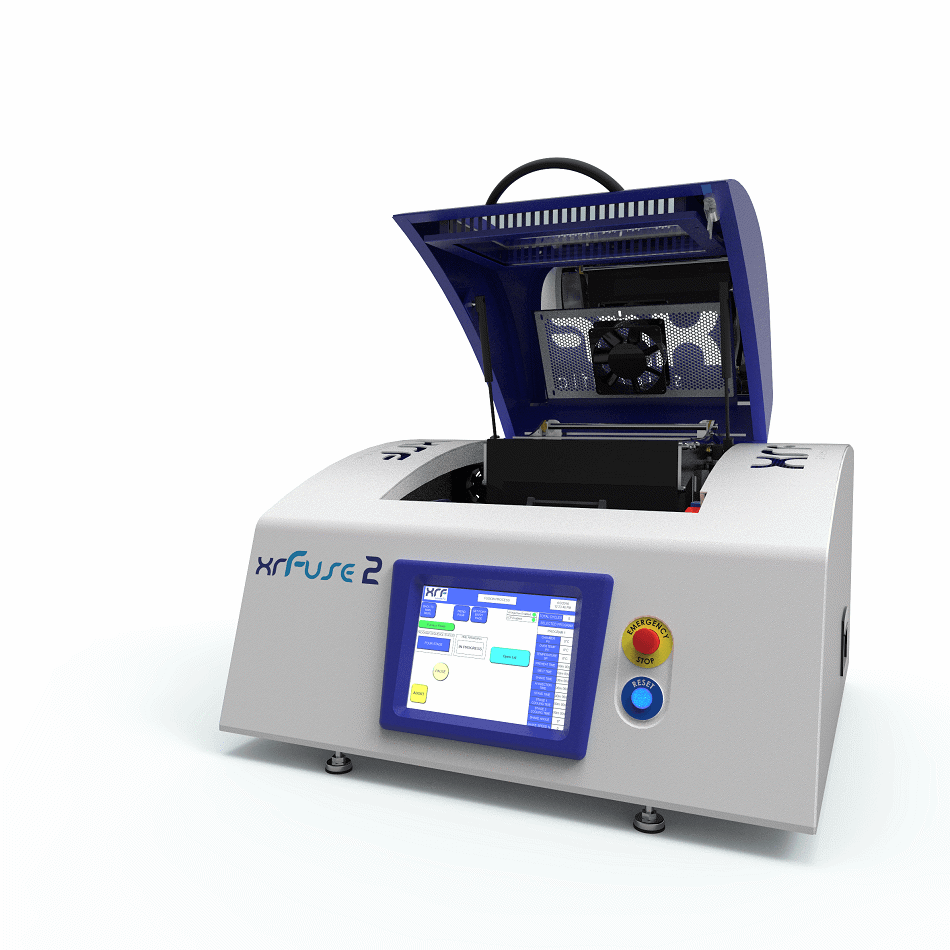
xrFuse 2
Experimental
For this study, all samples were calcined at 950 °C for two hours prior to the fusion. Two sets of glass disks were prepared on two different days employing both the Phoenix and the xrFuse fusion machines.
For all the preparations, 1.250 g of sample were mixed with 10.000 g of flux LT66:LM34 + 0.2LiBr (66% lithium tetraborate/34% lithium metaborate containing 0.2% lithium bromide as non-wetting agent) to develop beads of 40 mm. The fusion Program for the Phoenix comprises of 200 sec melting, 250 sec mixing (swirling) at 1100 °C. The fusion Program for the xrFuse includes 250 sec melting, 350 sec mixing (rocking) at 1100 °C.
The XRF analyzes were carried out on a Bruker WD-XRF S8 Tiger spectrometer. This device is provided with a Rh tube of 4.0 kW, multi-crystals, flow counter (Ar/CH4) and scintillation counter as detectors. The analytical conditions for the measurements were produced specifically for the raw mix, cement, and clinker analysis, and are available as a complete XRF calibration package from Bruker.
All reference materials were duplicate and analyzed as unknowns. Table 2 presents all the results and limits in terms of precision (difference between duplicates) and accuracy (difference of the average of duplicates and RM certificate value) for all the elements needed to be examined by XRF.
The results obtained confirmed that both the Phoenix 2 and xrFuse 2 fusion machines comply with the ASTM C-114 requirements and that the choice of either system will be based on other reasons.
Source of Error Through Fusion
There are three vital sources of analytical error due to the fusion: (1) incorrect fusion temperature; (2) insufficient homogenization; and (3) a deformed mold surface.
- Silicon dioxide (SiO2), calcium oxide (CaO), sodium oxide (Na2O), and sulfur trioxide (SO3) are the most affected by temperature. From experiments conducted, a 50 °C variation could cause a 0.5% change in result for CaO in cement.
- An insufficient homogenization leads to a change in the result for SiO2 and CaO.
- If the glass bead is not perfectly flat, this difference causes a change in the result. From experiments conducted, a 0.1 mm variation can cause up to 1% relative error in the result.
Conclusion
The repeatability and accuracy of XRF analysis is based on the sample preparation. Do not neglect this vital step and always check the method repeatability and create a control chart for the weekly control.
References and Further Reading
- ALLAN, T., and KHAN, A. A., “Critical Evaluation of Powder Sample Procedures”, The Chemical Engineer (May 1979) pp. 108-112
- WILLIS, J,. FEATHER, C., and TURNER, K., “Guidelines for XRF Analysis (James Willis Consultants-, 2014).
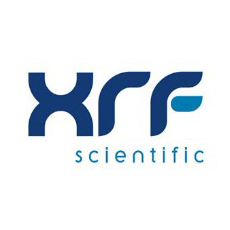
This information has been sourced, reviewed and adapted from materials provided by XRF Scientific.
For more information on this source, please visit XRF Scientific.