Do SilcoTek coatings have the ability to avoid fouling and coking in refinery applications? This article gives a detailed account of some quite impressive outcomes.
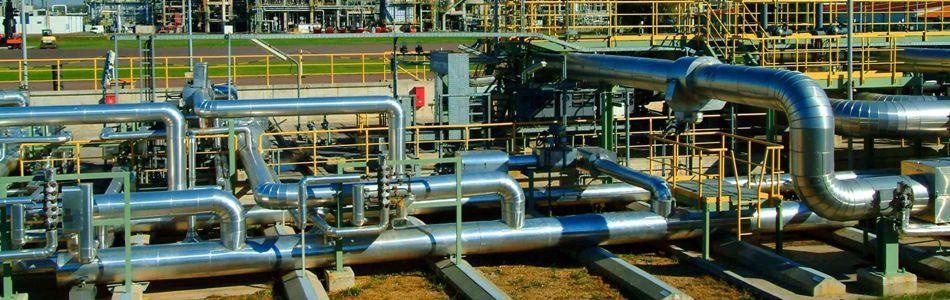
The following things can be learnt from this article:
- The impact of fouling on refineries
- Challenges faced with current fouling solutions
- The way inert anti-fouling coatings can prevent fouling or avoid coking
- Insights into CVD anti-fouling coating solutions and fouling prevention
Fouling could have drastic effects on the performance of processes and instrumentation in almost every industry. The impact of the accumulation of substances — such as the accumulation of carbon particulates in fuel systems or carbon fouling in a distillation process, can have a range of impacts.
Impact of fouling on refinery and fuel systems:
- Results in contamination
- Slows down production
- Promotes corrosion
- Reduces flow
- Increases emissions
- Raises drag/pressure
- Increases the requirement for maintenance
- Costs money

Tackling the adverse effects of deposits and accumulation of undesirable materials depend on the importance and application of the process. Yet, the cost could be high. Following are certain examples of the effect of the accumulation of materials on critical surfaces:
- Automotive: Fouling leads to more than 10% increase in fuel consumption
- Heat exchangers: About 50% of maintenance costs are related to the removal of deposits, which cost billions of dollars to the industry
- Refining: In 2002, 0.5 billion dollars were spent for finding a solution to coking issues
Potential Solutions to Fouling in Refinery Applications
There are many possible solutions to overcome this challenge, some of which are not realistic, some very expensive, and some resulting in added maintenance or redesign. A few examples are discussed below:
Solution |
Issue |
Additives |
Costly, difficult to manage. May not be realistic for some processes |
Steam cleaning |
Not entirely effective. Impacts productivity. Not realistic for some processes. |
Increase energy / power / fuel consumption (basically brute force idea) |
Expensive and does not solve the problem |
Control the incoming media that’s causing deposit build-up |
Rarely an option in industrial applications |
Material selection |
Several options, difficult to optimize performance & cost |
“Surface engineering” through advanced anti-fouling coatings |
Flexible and cost effective
Modify the existing part’s surface to make it behave how you need it to |
The Benefits of Coatings to Prevent Surface Interaction
Due to their ability to improve the performance of the surface and to prevent interaction of the base material with the interacting substance, inert coatings are considered to be an effective solution for various applications and industries. The outcome is a better surface without any modification of the part design or physical characteristic of the base material. However, various factors, such as those listed below, should be taken into account while selecting the right coating for the application:
- Is it mandatory to re-engineer to take tolerance changes into account? In most cases, tolerance change is not required. However, super high tolerance applications should be accounted for.
- Does the coating affect the environment in any way? The environmental impact of the amorphous silicon surface is relatively less during processing and even as a product.
- Does the anti-coking coating have the ability to endure corrosion, abrasion, temperature, and so on in the application? Although this is the norm in majority of the cases, to be sure, a user can approach a SilcoTek representative.
- Is the service life of the coating long enough? Although this is dependent on the application, the coating should provide excellent performance for several years. A SilcoTek representative can be approached for discussions on the application.
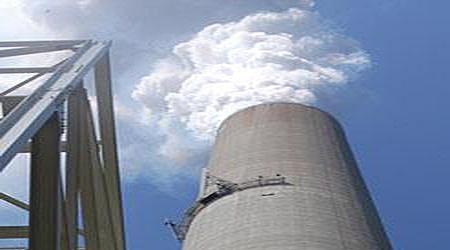
How SilcoTek Coatings Prevent Build-up
SilcoTek coatings are inert, high-temperature barrier coatings that inhibit chemical or catalytic interaction with the underlying surface. For instance, substrates that contain nickel catalytically form carbon deposits (coke) from petrochemical media, leading to accumulation on the surface. Coatings such as Dursan® or SilcoKlean® bond to the surface and alter the inertness and surface energy, thereby inhibiting adsorption of the substrate and chemical adhesion. The low energy surface of the coating prevents flow path chemicals from getting attached to the surface.
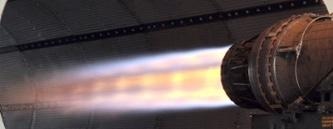
The applications are summarized in the following table.
SilcoTek® solutions and applications
Problem |
SilcoTek Coating Solution |
|
Carbon deposit, coke, formation from incomplete burning of fuel |
SilcoKlean barrier coating reduces catalytic coking and carbon deposit formation |
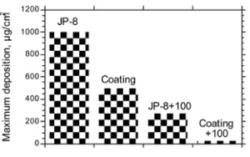 |
Bio-fouling in food applications. Spores from sour milk suspensions stick to testing equipment |
Dursan prevents sticking by up to 76% |
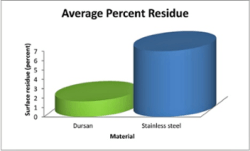 |
Protein binding in medical diagnostics |
Dursan prevents surface interaction and sticking |
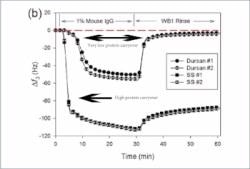 |
Carryover in GC & HPLC chromatography |
Dursan corrosion resistance prevents pitting & sticking to flow path surfaces |
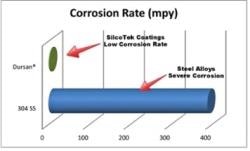 |
SilcoTek offers various solutions to overcome the challenges of deposits, sticking, carryover, and corrosion. More can be learnt about the coatings from the SilcoTek solutions page.
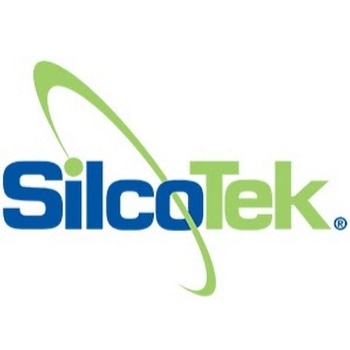
This information has been sourced, reviewed and adapted from materials provided by SilcoTek.
For more information on this source, please visit SilcoTek.