Additive Manufacturing, also called rapid prototyping or 3D printing, has attracted the attention of industries and people all over the globe due to its promising and limitless potential.
SEM for Detecting Surface Defects
AM operators are currently using SEM as a characterization tool for finished products. SEM offers high spatial resolution so the surface quality of the parts that are made using AM processes can be carefully inspected. Using SEM can help to show possible (micro)structural surface defects which can compromise the durability and mechanical properties of the finished products.
For some materials, like titanium alloys, it has proven to be particularly difficult to produce dense components with the matching properties to the components produced with conventional manufacturing processes. This is why SEM has proven to be an extremely useful characterization technique for finished products.
SEM on Alternative Additive Manufacturing Powder
SEM can also be beneficial in the characterization of the raw material that is used in AM processes, it does not just help in the examination of the finished product. Additive manufacturing is predominantly a powder-based technique; such processes include sintering of a large variety of powders.
A wide variety of materials, mainly metals and alloys, ceramics, composites, and plastics are utilized to construct components using a CAD-operated process.
Focussing on the metal powders which are used, it can also be concluded that numerous metals are presently being employed in additive manufacturing processes. Stainless steel, iron, nickel, cobalt, aluminum, titanium, and copper-based alloys are used, but the list is continuously getting bigger.
Those who utilize AM procedures are interested in various characteristics of the metal powders:
- Size (in the range of 1 to few hundreds of um) is a very important particle property to ensure uniform distribution, which will impact the product’s characteristics and its possible application.
- Shape (spherical particles are preferred) to enable efficient packing, flow and coating ability.
- Porosity, which influences the chemical composition and mechanical strength of the finished material.
Usually, careful inspection of the aforementioned properties of the powder is required and high homogeneity of their allocation is required.
Particle Characterization and SEM
SEMs are being used to characterize and image the surface of the products manufactured by AM processes. In addition, specialized software can be used for the characterization of the powder material, such as the ParticleMetric software that has been developed by Phenom-World.
ParticleMetric can automatically identify the particles that exist on a SEM sample and accurately distinguish them. This is by calculating a number of essential physical properties, such as aspect ratio, shape, size, circularity etc. It is crucial that these characterization processes can be undertaken automatically due to the vast quantity of particles that must be checked and analyzed.
Using SEM allows for the chemical characterization of the powder material by operating energy-dispersive X-ray spectroscopy (EDX), which most modern SEMs are equippedwith. Using an EDX detector in the SEM tool for AM processes means operators can precisely identify and quantify the elements that exist in their sample.
.jpg)
Figure 1. Screenshot of the ParticleMetric software. On the left, the detected particles in the SEM are shown. On the right, the results of the process are displayed; the detected particles, their properties and generated graphs with the particles’ properties.
It is evident that characterization requirements of products and materials used for AM processes can be fully covered by an SEM; with SEM imaging to assess the finished product’s surface, the EDX technique to detect and quantify the elements that they are composed of and specialized particle-analysis software to evaluate the physical properties of the powder material.
Download the Brochure for More Information
Additive Manufacturing and SEM
The quality control of the finished product—and detecting possible surface defects—is crucial in additive manufacturing. However, as an additive manufacturer you want it to improve your AM processes in a time-efficient way.
The same challenges were faced by Additive Industries, the world’s first equipment manufacturer dedicated to industrial metal additive manufacturing systems. They solved this problem and improved their quality control with scanning electron microscopy.
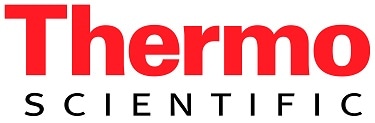
This information has been sourced, reviewed and adapted from materials provided by Phenom-World BV.
For more information on this source, please visit Phenom-World BV.