Historically, force measurement and materials testing were separate, distinct disciplines that had their own specific applications and place within a range of applications.
.jpg)
Generally, force measurement involved obtaining a product, material or part’s peak load measurement to either validate or verify that it was able to exceed or withstand a specific load. Force measurement was considered to be an innocuous test that was performed on the production floor or in a laboratory.
On the other hand, materials testing is commonly known as the science of ascertaining a product’s physical characteristics. Materials testing is generally undertaken by scientists and skilled engineers using complex software analysis.
Materials testing often involved a thorough evaluation of a material, for example, determining its modulus of elasticity, breaking load, or yielding characteristic by undertaking precise measurements according to recognized industry standards.
Now, the accuracy, precision, and functionality that was previously only possible with more complex, expensive testing systems is now achievable with a range of force measurement systems. This evolution in capabilities is being driven by demand from manufacturers to employ more direct testing on the production floor itself, alongside the need to be able to validate incoming products from suppliers around the world. Material tester functionality which had previously been reserved for research and development applications is now being employed directly on the production floor.
Thorough testing ensures that products that do not conform to specification can be addressed immediately, with the products and their related processes being measured, analyzed and adjusted quicker. Thorough testing also helps ensure improved production efficiency, improved yields and improved delivery performance as well as reduced nonconforming products, reduced manufacturing costs, and a considerable reduction in wasted or scrapped materials.
Testing on the Shop Floor
As the technology evolved, the production environment became an in situ testing laboratory, and the skilled staff who had previously been responsible for assembling and working with the materials, parts or products as part of their everyday role were now also able to perform real-time quality testing. Working in this way, the knowledge and experience of the production worker is vital to the product’s ultimate quality.
Force measurement systems in operation today are much more advanced, efficient, capable and accurate than ever before.
In fact, force testing has become a core part of the manufacturing process, with the forces required to insert or extract a component, make or break an electrical contact or even verify that a component can withstand an applied load following a number of cycles all being typical measurements that are undertaken directly on the production floor.
All these measurements combine to help confirm that a product is performing as well as possible, helping to determine its safety factor, life cycle and warranty period. Additionally, these measurements can pinpoint and identify non-conforming products within manufacturing processes, allowing these processes to be made more effective while helping to eliminate waste and scrap materials.
A modern force measurement system can measure peak loads, as well as being used to ascertain average loads, break loads based on differing sample break characteristics and even provide statistical analysis such as standard deviation, mean, and percent variation.
The ability to provide real-time pass/fail analysis based on predefined tolerances is commonplace, while measurement accuracy of better than 0.1% is usually the case. The current generation of force gauges can sample measurements at rates of up to 5,000 hertz before saving these results in the device’s internal memory.
Once results and data are obtained, these can be exported to computers before third-party quality control software is used to generated comprehensive product and process quality reports. These reports then form the basis of material or process improvements which directly affect the overall product quality.
Additionally, detailed production data from real-time measurements can be passed to research and development or quality functions, enabling correlations to be made between laboratory results in a more controlled environment.
A central factor in the efficiency of any integrated testing and measurement system is ensuring that performance and operation is simple to use and easy to understand. It is also important to ensure that the system is both practical and affordable.
Good quality force testers will include inbuilt menus which can assist the operator in selecting the appropriate measurement and method for the application at hand, while today’s truly global manufacturing environment means that contemporary force systems will offer multilingual capabilities for all menus, prompts and measured results.
A good quality, intuitive menu system can assist the operator in choosing the most appropriate measurement and method of measurement for their particular application.
Computer-Integrated Testing
The late 1960s and early 1970s saw digital computers find their way into the production environment, with computer-integrated manufacturing becoming popular in the 1980s as a way of automating industrial processes while ensuring manufacturing consistency.
Programmable logic controllers (PLCs) were adopted by the automotive industry first of all, having been developed from digital computers. These were used to improve the manufacturing process whilst reducing costs from the changing of manufacturing methods in hundreds of relays, drum sequencers, cam timers and dedicated closed-loop controllers. The application software used on these initial computers was complex and hard to use.
Automated testing has evolved considerably from programmable controllers where a computer and software performed a specific test on a material, product or component. These automated testing systems were used to precisely control speed ensuring repeatability, thus allowing results to be measured against each other.
The computer came with complex software packages which let the operator test a range of points, collecting large amounts of data at high sampling rates before providing comprehensive reports which could improve product and process quality.
While previously reserved for research and development applications, the functionality of materials testers is now available directly on the product floor.
Today's Functionality
Contemporary force testing systems are able to incorporate principles that were first developed for the programmable logic controller with a range of materials testing functions. These systems let the operator create multi-stage, albeit, logic-testing steps with no need to use a separate computer or third-party software package.
The operator can create test recipes based on individual testing methods or according to industry testing procedures and standards. The creation of tests is intuitive, so there is no need for the user to have specific computer programming knowledge.
Contemporary systems use precise motion and speed control algorithms with complex proportional integral derivative controls. These combine with high-resolution optical encoders to allow more advanced systems to test at varying speeds and to extremely precise load or distance limits, all the while collecting data points at up to 1,000 samples per second.
These systems can automatically correct for frame and load cell deflection, as well as being able to accurately measure sample heights. They can also accommodate complex spring testing, top load testing and texture analysis on food products.
Results from tests can include color-coded, tabular readouts that can highlight different tolerance limits. Results can also be shown graphically for fast comparison or analysis.
It is possible to save data for later use, and this can be archived or exported to other computer systems for collection and analysis of data; using serial data communications or even USB flash memory sticks. Like-testing systems can be ‘cloned’ within seconds when the system is configured using flash memory.
The graphical display of a force tester can illustrate the load result against time and deflection.
System configurations can be sent to different manufacturing sites via e-mail and uploaded to other systems in mere seconds, allowing consistency in testing across sites worldwide.
There will always be a need for thermal chambers, extensometers, computers and complex analysis software within materials testing applications. These systems are optimized for material evaluation and analysis, so form a core part of all research and development work.
However, advanced technologies that were previously only seen in materials testers have considerably expanded the capabilities of traditional force testing instrumentation, especially as they become more and more integrated with manufacturing processes.
Force measurement will continue to evolve, propelled forwards by the need for more sophisticated and ultimately more cost-effective testing solutions on the factory floor. Modern force measurement systems allow a combination of features, simplicity and functionality and this should be explored thoroughly before purchase.
Additionally, a system’s total cost of ownership should be thoroughly and carefully considered when selecting a testing solution for manufacturing requirements.
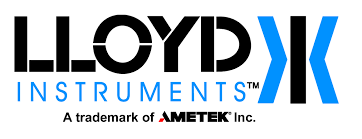
This information has been sourced, reviewed and adapted from materials provided by Lloyd Instruments Ltd.
For more information on this source, please visit Lloyd Instruments Ltd.