.png)
SilcoTek® can help reduce downtime during processing by preventing coking, build-up and fouling with their non-stick coatings. This article will explore how non-stick coatings can be used to increase fouling and coking resistance and save operators money by reducing system downtime.
Surface performance can be improved using SilcoTek’s newest surface treatment, Notak™, and their Dursan® coating of modified silicon dioxide.
This article will specifically look at:
- The tools required to coat a surface so it is non-wetting, thereby lowering maintenance needs
- How coating via CVD can make surfaces easier to clean and more robust
- How fuel delivery and injection systems can coated to decrease the amount of fouling and coking
- How coatings can be used to decrease surface energy and increase surface lubrication for injection molding
Issues relating to sticking, fouling and low lubricity can result in interrupted process flows, problems with fuel delivery and mold release.
Changing the Surface Properties of Metals, Ceramics and Glasses with Silicon Coatings
.png)
Before discussing the proven benefits of coatings, we will look at how coatings for fouling resistance can be bonded to a surface.
Coatings such as Notak™ and Dursan® can be applied to the surface of metals, ceramics and glasses using a novel CVD process, where the coating is introduced as a gas and then deposits on the surface to form a coating of micrometer thickness. This method even facilitates the coating of complicated microstructures such as sintered metal frits.
The deposited coating bonds into the surface and acts as a fouling and corrosion resistant barrier, whilst also improving the surfaces lubricity. The sputter death profile given below shows the silicon-steel diffusion zone and the barriers bond to the surface of the steel.
.jpg)
Following CVD processing the surface’s properties are enhanced to those of the coating – providing useful behavior such as resistance to fouling and corrosion and lubricity, whilst also impacting the surfaces hydrophobicity and energy.
Coatings Result in Improved Mold Release and Less Friction
The benefits of coating a surface are clearly shown by comparison. The table provided below shows the results of on-disc wear comparisons between a ‘naked’ stainless steel surface and a surface coated using Dursan, a carboxysilane coating.
The data shows that the Dursan-coated surface has a 35% smaller coefficient of friction and a wear rate of half the naked steel, meaning it is a far more wear resistant and efficient.
A low friction coefficient means that products being transferred will slide at lower energies and will be less likely to bind to the surface. This allows systems such as injection molds and slider valves can operate at lower energies.
.jpg)
Avoiding Problems with Fouling and Coking Resistance
Fouling, the accumulation of materials on a surface, is a problem that impacts most industries and it can be severely detrimental towards instrument and process performance. Fouling, whether it is carbon particulate fouling in a fuel system (coking) or carbon fouling during distillation, causes a wide range of problems, including:
- Increased drag and pressure, resulting in reduced flow
- Contamination of the system
- Can result in increased corrosion
- Results in emission increases
- Increases the need for maintenance – costing money
- Slows the rate of production – costing money
.png)
Solving the problems associated with a build-up of materials inside the system depends on what the material is however; it is almost always expensive and often also hazardous. Some examples of the effects that unwanted material build up can have are given below:
- For Heat Exchangers half of maintenance costs are the result of unwanted deposits, which costs billions of dollars to solve
- In the Refining Industry coking costs half a billion a year to rectify (2002)
- In the Automotive Industry fouling means automobiles use 10% more fuel than they should have to.
Ways to Prevent Fouling and Coking
There are several different methods available to prevent fouling and coking from occurring. Some are prohibitively expensive and others are not that realistic or require a level of redesign. These include:
- Steam cleaning the system – Results in more downtime and not completely effective. Only works for certain processes.
- Not using media that fouls – Not an option for most industrial systems.
- Additives – Effective but also expensive and potentially polluting. Depending on what media is being handled this is not always an option.
- Selecting appropriate system material –Difficult to balance performance, cost and structural stability.
- Brute force - Increasing the system energy to force the media through quickly. Very expensive and ignores the true problem.
- Surface engineering (coating) – Flexible (with lots of choice) and cost effective.
Anti-fouling coatings allow the surface of existing parts to be modified. Research conducted by SilcoTek has shown that using coatings (either with or without surfactant) results in less than half as much fouling, reducing the amount of particles that bind and making filters easier to clean.
Coking and fouling studies show SilcoTek® coatings and coatings combined with a surfactant reduce fouling by 50% or more. This reduces the particulate binding effect and makes the filter easier to clean.
.jpg)
Improving Corrosion Resistance
Corrosion immersion testing (following the ASTM G31 method) to compare uncoated stainless steel with a Dursan coated analogue shows that Dursan coating improves corrosion resistance by a factor of 10. This improves the durability and lifetime of processing lines and filters.
.jpg)
Decreasing the Surface Energy
Reducing the energy of a surface (characterized by a high water droplet contact angle) reduces the strength of particle binding to the surface, making cleaning of the system easier. For this reason surface energy management is a key method of reducing fouling.
The new Notak™ coating from SilcoTek provides the lowest surface energy and highest contact angle of any silicon-based surface available. When compared to naked stainless steel, a Notak coated surface results in a surface energy which is 70% lower.
The graph and diagrams below display the different contact angles for SilcoTek coatings.
SilcoNert® (far left) is a hydrophilic coating used to wet surfaces, and has a surface energy similar to uncoated stainless steel. When water interacts with SilcoNert it forms a flat drop on the surface (as shown in the diagram) which makes the surface wet and hard to clean.
Notak behaves entirely differently as it is hydrophobic and has a very low surface energy. The water drop hardly makes contact with the surface and instead sits on top as a bead. This makes the surface very easy to clean and unlikely to foul.
.jpg)
Do Surfaces with Low Friction and Surface Energy Really Prevent Fouling?
The theory states that a surface with a high lubricity (low friction) and low surface energy will prevent fouling resulting in better system performance.
The graph given below puts this into practice and compares the simulated differential pressure of an uncoated filter (two higher lines) and a Dursan coating (bottom line) under processing conditions. The Dursan coated filter experienced half of the differential pressure of the uncoated filter, resulting in a lifetime that was two times longer.
The evidence is there – SilcoTek’s coatings, such as Dursan, can be used to extend system lifetimes whilst reducing the back pressure and energy of a system.
.jpg)
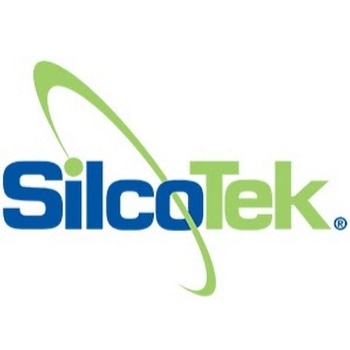
This information has been sourced, reviewed and adapted from materials provided by SilcoTek.
For more information on this source, please visit SilcoTek.