.jpg)
A chemical vapor deposition (CVD) coating is a material that is applied to a surface by chemical vapor deposition. This article will discuss how the coatings are made, coating benefits, and how to make the most out of a coating.
CVD coatings can be found throughout industry in many consumer products. They are known as being a durable as well as an environmentally friendly thin film surface. CVD products can be found in a range of applications from machine tools, analytical flow path components, wear components, instrumentation and many other areas demanding a high performance thin film. There are a lot of thin films available, so what is it about the chemical deposition process that makes a superior coating for high performance precision applications?
This article will discuss:
- Characteristics of a CVD process
- How CVD works
- Why SilcoTek coatings are so colorful
- Benefits and drawbacks of CVD
About CVD Coatings: What is Chemical Vapor Deposition?
Chemical vapor deposition is a process that involves the reaction of a volatile precursor which is injected into a chamber, typically under vacuum. This chamber is heated to a reaction temperature and this causes the precursor gas to react, or break down, into the desired coating and bond to the material surface.
Coating material builds on the surface over time and this creates a coating throughout the surface of the exposed part. For example, a trichlorosilane precursor can be used to bond silicon to a surface. Heating trichlorosilane in the coating chamber the decomposition and coating reaction may be as follows:
SiHCl3 à Si + Cl2 + HCl
The chlorine and hydrochloric acid gas will be vented from the chamber and scrubbed according to appropriate regulatory requirements whilst the silicon will bond to any exposed surfaces (both internal and external). The CVD coating system may look similar to the diagram below.
.jpg)
In this example, the desired coating material is a silicon oxide base coating with a functionalized (R) surface. The surface is indented to cap any remaining active sites on the coating surface, making it a superior non-reactive surface.
The materials used in CVD coating systems range from silicon compounds to carbon, to organofluorine or fluorocarbons, and nitrates like titanium nitride. Some of the materials, e.g. silicon, can be further enhanced by doping the surface with other materials in order to functionalize the surface for a specific performance goal (as demonstrated above).
Process control, surface preparation and material quality (both the precursor and the part material) play an important role in the coating quality. A typical CVD coating process is shown below.
.jpg)
Characteristics of a CVD Coating Process
- Typically applied under vacuum
- Applied at elevated temperature to facilitate reaction
- Process may limit the availability to mask specific target areas
- Contaminants must be removed from the part surface before coating application
- Film thickness is limited due to coating stress
- Process may limit the base materials that can be coated. i.e. temperature limitations or reactivity limitations
- Coating is bonded to the surface during the reaction which creates a superior adhesion when compared to a typical PVD (physical vapor deposition) or low temperature applied spray coatings
- Unlike most PVC processes, the CVD Process is not limited to line-of-site application. Coating gas will coat all areas of a part including threads, blind holes and interior surface
.jpg)
Coating Benefits
- Can coat precision surfaces and intricate surfaces including seal areas and internal surfaces
- Remains bonded in high stress environments and when the surface flexes due to high adhesion characteristics
- Can be applied to a wide variety of base materials including ceramics, glass, metals and metal alloy
- Precursor gas can be optimized for wear resistance, high lubricity, corrosion resistance, fouling resistance, high purity or chemical inertness
- Can withstand exposure to low and high temperature and extreme temperature variation
Coating Drawbacks
- Difficult to mask surface. Usually an all or nothing coating
- Typically applied at higher temperatures (depending on the precursor)
- Parts must be broken down into individual components and is not an “on site” process
- Size limited to reaction chamber capacity
.jpg)
The CVD Coating Process and How it Makes Color
Customers often note the multi-color rainbow appearance of the coatings. What makes the coated part so colorful and why does the color vary by part or by lot?
SilcoTek bond silicon to metals, glass, or ceramics and this process enables the building of a silicon layer on a surface on Angstrom (0.1 nanometer) at a time. A very thin layer of silicon is so clear that it can be seen through. As the silicon thickness increases, e.g. on a stainless steel surface, the light which travels through the silicon is bent.
.jpg)
Then the light reflects off the stainless steel surface and is bent again. This bending of the light causes some wavelengths of light to cancel out each other but some wavelengths are reinforced. The reinforced wavelengths hit the cones in the eye and are seen as color whilst the canceled (or interference) wavelengths cannot be seen. A few nanometer change in silicon thickness can have a bit impact on the colors seen.
A good analogy is that of oil on water. After a rain storm a colorful rainbow oil slick can be found flowing on surface oil. Oil is not normally colorful, it is either honey colored or black (as it gets older). The black becomes a colorful rainbow because of refraction. Light reflects off the surface of the oil and also travels through the thin oil and is reflected back from the water surface below the oil.
Depending on the thickness of the oil, light rays are either reinforced or interfered with by the oil refraction. As the rays of light reach the eye, the destructive interference wavelengths cancel each other out. The oil thickness variation dictates which colors are seen and which color wavelengths are canceled out. This analogy demonstrates that a slight variation in thickness can have a big impact on the color that is seen.
Small variations in thickness can also make a big difference in the color of the silicon coating. The differences in the colors observed on SilcoTek treated parts indicate different layer thickness. A blue color indicates a 300 to 450 Angstrom layer while a rainbow color corresponds to a coating of at least 1200 Angstroms (120 nanometers).
.jpg)
Depositions used in the SilcoGuard® and Silcolloy® processes are up to 1 mm (1000 nm) and have a rainbow to silver/metallic gray appearance. The images below show colors created by Silcolloy®, an 800 nm** coating (right) and SilcoNert®, a 500 nm** coating (left). A few nanometers change in thickness will result in a dramatic change in the color of the part.
.png)
SilcoTek coatings are colorful because they are thin. They are thin because the coatings are highly durable which means that they do not need to be thick. This is because the amorphous silicon coating, when thin, does not significantly impact part tolerance.
SilcoTek is an industrial coating company and focused on the ultimate performance of the coating, not the appearance. Making parts with uniform color would impact on the coating thickness and could result in a coating that is less robust.
*Image credit: Pinterest
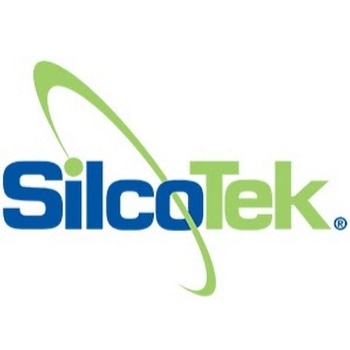
This information has been sourced, reviewed and adapted from materials provided by SilcoTek.
For more information on this source, please visit SilcoTek.