Sponsored by QATMJul 9 2019
Titanium and titanium alloys are the materials most frequently used for dental implantology and have become a gold standard for tooth replacement. A disadvantage of titanium, however, is its grayish color which is sometimes visible through the peri-implant mucosa. Moreover, research has shown that metals are able to induce a nonspecific immunomodulation and autoimmunity1.
New ceramic materials are likely to overcome these drawbacks2. However, ceramics are known to be sensitive to shear and tensile loading which may lead to early material failure. Consequently, high-strength zirconia ceramics have become the materials of choice for dental implants.
When defining the mechanical and prosthetic capacities of the implant body, the material and processing characteristics need to be considered. That means both the monoclinic and tetragonal phases of zirconium dioxide (ZrO2) should be taken into account. Compared to the monoclinic phase, ZrO2 can resist extreme loading forces in the tetragonal phase; moreover, its high biocompatibility makes it an ideal dental material. Beside these positive properties, its enormous stiffness leads to fracture at the load limit. These characteristics influence the design, mainly with respect to production, the application and the properties of one-piece and two-piece implant systems.
Two different approaches for producing implants exist in the market: one-piece (= screw-retained) and two-piece (= cemented) ZrO2 implants. The advantage of one-piece ZrO2 implants is the absence of a micro-gap. Two-piece implants made of ZrO2 show the risk of fractures or loosening at the connection between implant and abutment. The latest two-piece systems are designed in a way to avoid these risks altogether. Hence, there are no significant disadvantages in comparison to two-piece titanium implants.
Thanks to new techniques, like digital planning, together with the prosthetic diversity of two-piece ZrO2 systems, it is possible to combine the adequate prosthetic solution with the surgically reasonable position of the implant. Thus, faulty functionalities, including the presumed fracture risk, can be avoided in advance.
Materialographic Preparation of ZrO2 Samples
The zirconium dioxide used for dental implants needs to be examined for its suitability. The materialographic sample preparation of an ZrO2 implant to determine the porosity is described in the following paragraph. Porosity is a critical factor with major influence on the mechanical stability and tissue ingrowth properties.
Preparation Method
As the sample shows a natural porosity and fractures at a specific pressure limit it was mounted by using the castable material KEM 15 plus with a mixing ratio of 1.5:1 of powder and liquid. The final mount has a diameter of 40 mm.
Cold Mounting
Table 1. Mounting parameters
Mounting material |
Mixing ratio |
Curing time |
Mould |
KEM 15 plus |
1.5 : 1 (powder : liquid) |
12 min |
PTFE, Ø 40 mm |
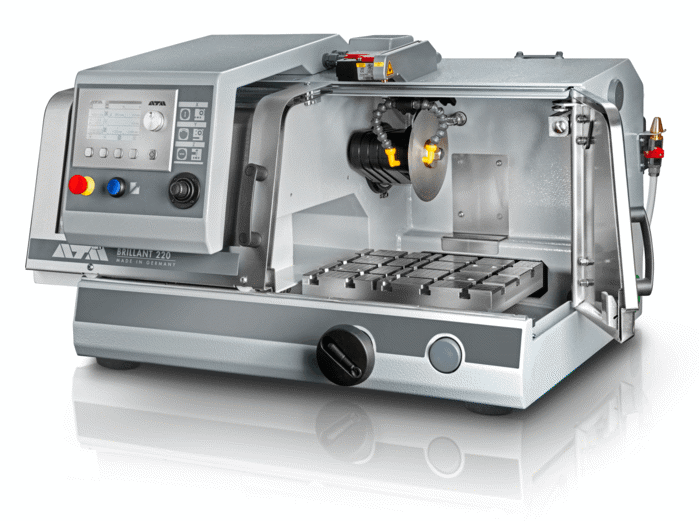
Figure 1. Cut-off machine Brillant 210 A
The mounted sample was clamped on a clamping vice 60 with a prism jaw and cut in a Brillant 210 A cut-off machine using an ATM diamond cut-off wheel for ceramics afterwards. The cutting parameters of the direct cut were 0.08 mm/s constant feed speed at 2500 rpm. The Brillant 210 A model is a compact, user-friendly precision wet abrasive cutting machine. It can be fitted with up to three automatic axes (X, Y, Z) and several cutting modes for maximum flexibility and ideal use of space.
Cutting
Table 2: Cutting parameters
Equipment |
Cut-off wheel |
Anti-corrosion coolant |
Clamping tool |
Brillant 210 A |
|
ATM CoolCut |
Clamping vice 60 with prism jaw |
Cutting method: |
direct cut |
|
|
|
Parameters: |
Feed speed 0.08 mm/s |
Pulse parameter none |
Rotational speed 2500 rpm |
Notes: At the beginning and at the end of the cut the feed speed should be reduced.
Grinding/Polishing
The grinding and polishing procedure was carried out in a Saphir 250 A1-ECO using consumables with abrasives of diamond and hard polishing cloths won metal sheet. The first step is planar grinding using a diamond grinding foil of 74 µm grain size with 30 N individual pressure followed by 6 minutes grinding at 45 N individual pressure on a Galaxy green grinding disc. The Saphir 250 A1-ECO grinder/polisher is a single-wheel grinding and polishing machine with working wheels in Ø 200/250 mm which is conveniently operated via a 4.3" touch screen.
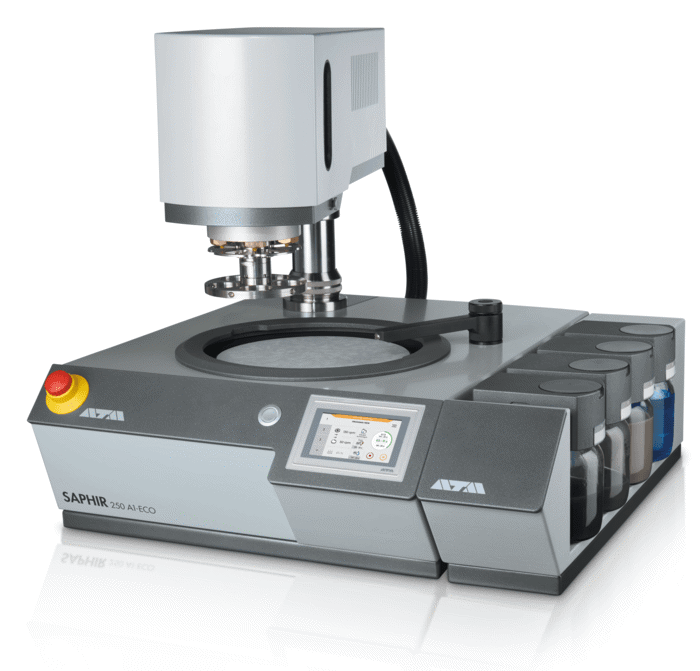
Figure 2. Grinding & Polishing Machine SAPHIR 250 A1-ECO
Table 3. Grinding and polishing parameters.
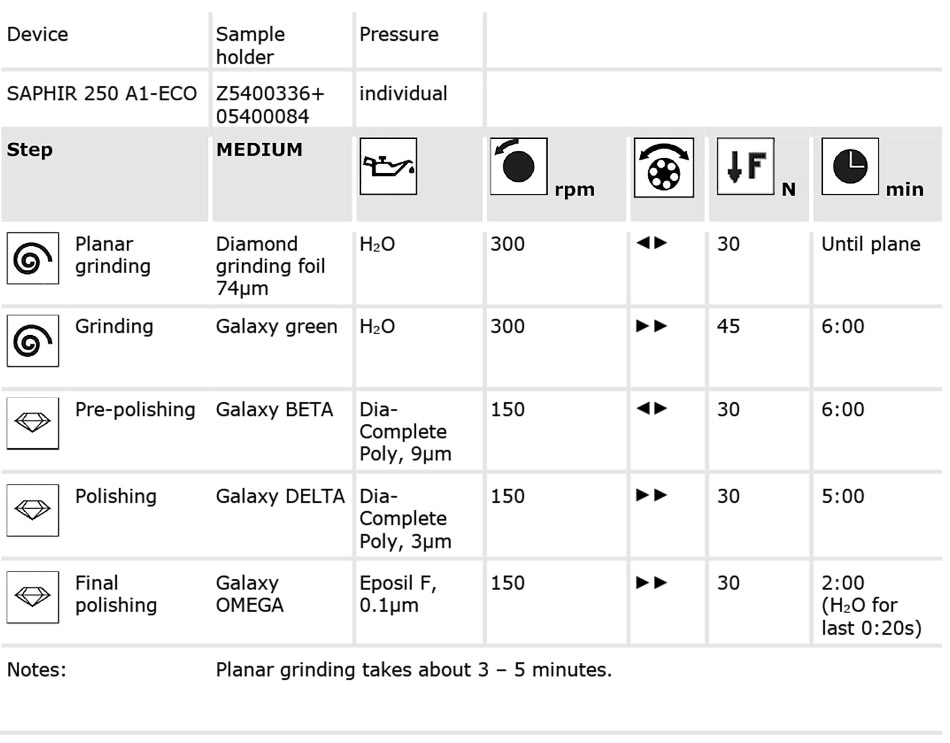
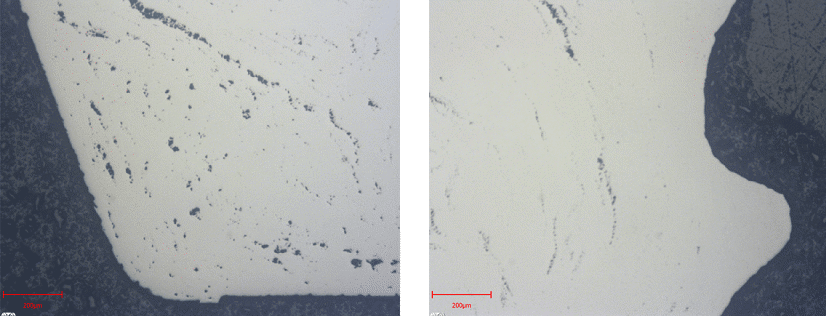
?Figure 3: Both bright field images have a magnification of 500x. The porosity of the sample varies depending on the manufacturing process. Left: the porosity is larger compared to the image on the right-hand side, which shows the screw thread part.
Video Galaxy Grinding Discs
The first polishing step was performed for 6 minutes with 30 N individual pressure on a Galaxy BETA polishing cloth and 9 µm Dia-Complete poly diamond suspension. After this pre-polishing step the sample was polished for 5 minutes on a Galaxy DELTA polishing cloth with 30 N individual pressure and 3 µm Dia-Complete poly diamond suspension. Final polishing was done with Eposil F for 2 minutes followed by rinsing with water for the last 20 s and 30 N individual pressure.
ATM provides a wide range of consumables for materialographic sample preparation. Especially for grinding/polishing/etching applications, the Solution Boxes offer an all-in-one solution containing all grinding and polishing media required for the preparation of a specific material.
Video Solution Boxes
References and Further Reading
- Stejskal J, Stejskal VD. The role of metals in autoimmunity and the link to neuroendocrinology. Neuroendocrinol Lett. 1999;20:351–364.
- Kohal RJ, Klaus G. A zirconia implant-crown system: a case report. Int J Periodontics Restorative Dent. 2004;24:147–153
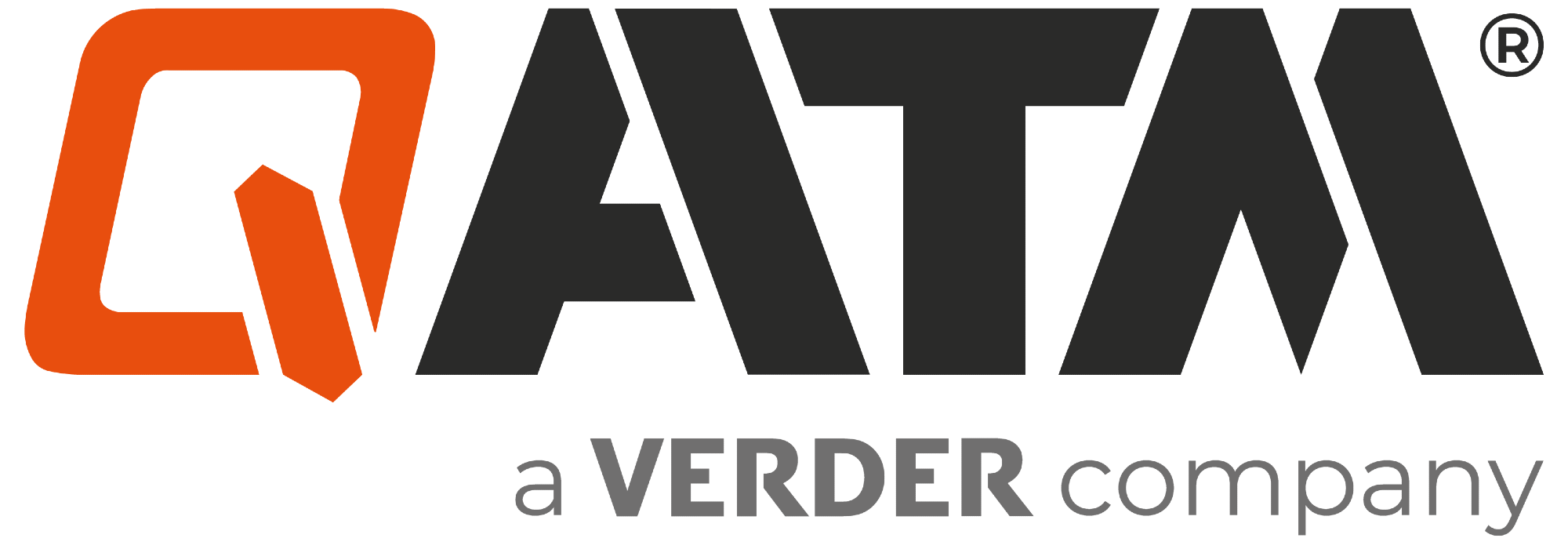
This information has been sourced, reviewed and adapted from materials provided by QATM GmbH.
For more information on this source, please visit QATM GmbH.