The goal of a laboratory test methodology is to establish an approach that will allow a user to acquire reliable, meaningful data. As materials and decoration techniques advance, routinely utilized test methodologies for measuring abrasion resistance of decorated plastics may prove insufficient. To guarantee product robustness, an understanding of how to simulate and quantify “real-world” damage is vital.
This article introduces a procedure for developing (or improving) test methodologies designed to measure the resistance of surface wear on decorated plastics. Emphasis is put on minimizing common sources of test procedure variance and sophisticated techniques of interpreting and quantifying the results. Taber Industries' Linear Abraser Model 5750 has been an ideal solution to address this need and has been incorporated into quality control and R&D efforts by numerous companies.
Introduction
Although identification of wear is often quite simple, understanding the process of wear is not as straightforward. Indeed, the process of wear is a complex phenomenon and any attempt to undertake an exact simulation in a laboratory environment typically poses great difficulties.
ASTM International defines wear as “damage to a solid surface (generally involving progressive loss of material), caused by the relative motion between that surface and a contacting substance or substances” [1]. In most cases, the motion is a repetitive action and material removal is a slow process.
Two typical categories of wear that transpire among plastics are wear abrasion and mar abrasion. Wear abrasion involves the removal of a section of the surface by some type of mechanical action (e.g. rubbing or sliding back and forth of an object). Mar abrasion is a permanent deformation of a surface, but the deformation does not cause the surface to break. Abrasion and wear should not be confused. While the terms are regularly utilized interchangeably, wear is defined as “the wearing away of any part of a material by rubbing against another surface” [2] whereas abrasion is the action that causes it.
Although laboratory wear tests can potentially generate substantial understanding of the various factors contributing to a material’s performance, most laboratory approaches fail to provide an exact simulation of the mechanics involved. This is because there are usually several influences that affect the rate of wear. It is essential that the limitations of testing are understood because accelerated wear testing may not always detect potential problems or predict field performance results.
Nevertheless, a controlled laboratory test permits an approximation of field conditions and enables the elimination of extraneous variables. This allows a product's life span to be condensed into a much shorter duration and enables the evaluation of materials in the same manner within a controlled setting. Furthermore, a laboratory test is considerably less costly than a field study.
Defining an Approach
Any attempt to simulate wear damage in a laboratory environment entails the determination of a complex array of interrelated properties. The goal of the test is to supply predictive performance under a specified set of criteria and compare with end-use performance. However, evaluating the conditions a product is subjected to during its life quickly exposes the difficult and multifaceted nature of establishing a test methodology.
A fundamental principal of developing new abrasion tests is to firstly utilize the most straightforward technique, stopping as soon as the required information becomes available. In many cases, the extra information that is acquired by examining further factors does not justify the added time and expense.
Due to concerns with reliability and product life, engineers may require accurate replication of the wear system. Contrastingly, a material developer looking to rank the wear resistance of materials might accept a convenient test that does not precisely simulate intended usage. In both cases, careful consideration must be made of the wear system and failure mode to generate useful data. The wear system comprises the test piece and contacting material(s) along with the relative movement that generates the wear. The failure mode is determined by how the system wears and which wear modes are entailed. [For further information on wear modes, see ASTM International, G40 Terminology].
Wear is a response stemming from the conditions to which the entire system is subjected. Resistance to abrasion is influenced by the nature of abradant, variable action of the abradant over the area of specimen being abraded, the pressure between the specimen and abradant, the tension of the specimen and the dimensional alterations in the specimen.
Although most standardized test methodologies delineate the variables which must be observed when performing tests, it must be acknowledged that the accurate identification of all of the influences that engender wear conditions is unlikely. The following influences must be carefully considered:
- contact geometry
- length of exposure
- interacting material surfaces
- normal force
- sliding speed
- environmental conditions
- material composition and hardness
NOTE: It is important not to become distracted when trying to isolate and reproduce the influence of each variable.
How can a determination of the conditions to which a product may be subjected be undertaken? The primary approach entails a consideration of existing understanding. If a field failure is being studied, an examination of the appearance of the surface wear from an actual application should be carried out. It is important to bear in mind that there may be more than one wear mode occurring simultaneously, while also recognizing that matching conditions in a laboratory are typically imperfect. The following parameters are usually related to sliding wear on plastic materials [3]:
- Intrinsic parameters associated with the materials in question, such as their surface condition, nature and finish. These comprise bulk characteristics (e.g. physical characteristics, chemical composition, mechanical properties, hardness) and surface characteristics (roughness, physico-chemical characteristics).
- External parameters associated with the sliding conditions, including sliding velocity, applied load, mode of contact, characteristics of the motion, ambient conditions (humidity, temperature), and any interstitial substances (lubricant, wear debris).
- Variables influenced by both the sliding conditions, especially surface temperature of the rubbing surfaces, and the nature of the materials in question.
Several industries have developed test procedures and endorse abrasion instruments that may be utilized to replicate the wear. However, “there are a lot of customer and industry specifications that really are not an indicator of meaningful product performance or durability” [4]. If a methodology does not exist or the industry standard is not followed, selecting a test that models the system in question is essential. If there is any hesitation regarding where to begin, contact with research industry associations should be the first step, as this will enable a determination of whether an accepted abrasion test procedure already exists. Additional sources of information comprise organizations committed to the development of test standards, such as ASTM International and ISO.
Producing Reliable Data
There are many instruments which can assess a material’s resistance to surface wear damage. However, since the findings for each instrument are based on that tester’s unique system, it is typically not possible to compare data between apparatus. Indeed, some materials may display differences in terms of the relative order of resistance to abrasion when tested by alternative methodologies.
The principle factors entailed in the simulation of a wear system comprise specimen preparation, test protocol, apparatus design, and measurement. Whether or not there is any correlation between a particular type of abrasion test and end-use performance is dependent not only on an equivalence of abrading mechanisms, but also on the extent to which that mechanism is maintained during the duration of the abrasion test. The following points introduce the important elements that require consideration:
Motion
The type of relative motion is regularly utilized to specify the wear that is produced. Due to its complexity, several different wear modes have been identified, comprising sliding, rolling, rubbing, and scuffing. Wear can transpire in combination or on different sections of the same component.
Apparatus
The test apparatus must embody a rugged design to yield repeatable and reproducible results. Variables such as speed, load, alignment, rigidity of apparatus construction and supply of abrasive demand sufficient control to guarantee wear conditions stability. The most regularly employed testers for decorated plastics entail a reciprocating movement, rotating abrasive disc / wheel or point contact.
Materials involved
The structure of the wear system encompasses the specimen and counter-body (typically an abradant of some variety). Fundamental characteristics such as hardness, toughness, elasticity, strength (comprising tensile, cohesive and shear strength) and, particularly in the case of wear resistance, thickness, can all affect wear resistance of the materials. It should be noted that a material might wear differently when exposed to divergent situations, or may be affected by the wear of the other contacting body.
Abradant (wear agent)
The mechanism of wear is dependent on the topographical nature of the counterface abradant. Common varieties of abrasives comprise engineered abrasives, textiles and sandpaper. While abrasive particles might not be the principle cause of actual wear, they are regularly employed to accelerate testing. Abrasive particles, irrespective of whether they are loose or embedded in a binder material, have a substantial influence on the rate of wear. In most instances, it is not desirable to re-use an abrasive, except if it can be refreshed.
- Shape – Particles that embody an angular or “blocky” shape can lead to up to ten times the wear rate in comparison to rounded particles.
- Size - The size of the particle is key, as larger particles effect proportionally more wear than smaller particles. Particles responsible for abrasion or erosion generally embody sizes between 1 µm and 500 µm.
- Type – Common abrasive particles comprise silicon carbide and aluminum oxide. With sandpaper, silicon carbide generates a thinner scratch pattern as a result of being a sharper grain than aluminum oxide, and will usually cut more rapidly.
- Friability – The ease with which the abradant breaks down and fragments under localized heat and pressure, generating new sharp edges.
Contact Geometry
This corresponds to the shape of the abrading head or abradant, and its contact with the specimen. Certain systems might need the specimen and abradant to “wear-in”, therefore generating a stable and uniform contact geometry. While point-contact can eliminate several alignment problems related to alternative contact geometries, stress levels can alter by the progression of wear, making further complex data analysis and comparison techniques necessary.
Contact pressure (applied load)
With an accelerated test, the load can surpass what is observed in the field. This variable typically relates to the amount of force involved in pushing the abrading material against the specimen throughout the rubbing action. It is important not to utilize a load that surpasses the ultimate strength of a material.
Sliding speed (sliding velocity)
This refers to the speed of the abradant as it travels across the specimen. Although acceleration in a test is advantageous, if the speed becomes too fast for the material (abradant), the accuracy of the test can be undermined via the introduction of different phenomena. Excessive speeds can lead to a typical thermal condition on the test specimen.
State of lubrication
Lubrication will influence a material's frictional properties. Generally related to metals, several plastics formulations also comprise a lubricant additive.
Specimen Preparation
Specimen preparation and the details of test control differ by the test and materials in question. For instance, homogeneity, hardness, surface roughness and geometry of the specimens should be supervised for reproducible test results. Comparable controls are also required for the counter-face and the wear-producing mediums. During the evaluation of multilayered systems, the substrate takes on a central role.
Environment
Several materials embody a sensitivity to alterations in temperature and humidity, and adjusting the test environment can impact on results.
Reducing Common Sources of Variation
As emphasized in the introduction, simulating wear in a laboratory environment is a complex process. There are various sources of variation that can impact on test findings. An awareness of these will assist in the development of a technique that can supply a means of generating repeatable and reproducible data.
If a new protocol is being developed, it is important to remember that test development depends on the developer's level of expertise. Sometimes, trial and error is necessary to identify a test procedure that yields valuable information. Broadly speaking, because wear involves at least two bodies and at least one material, and depends on a broad array of influences, an accurate simulation is neither practical nor possible, and accepting some differences is required.
Once an approach has been established, the procedure should be documented. Test methodologies lacking in critical procedural information can introduce issues relating to reproducibility, as much of the variation that transpires with abrasion tests is caused by operator error.
Depending on the instrument, any of the variables can introduce variation into the consequent test results. This is usually observed among companies that fail to observe an established test methodology or which utilize a procedure for which critical information is absent. The test set-up parameters must be reviewed to make certain that they are identical for all tests. For instance, the importance of sample positioning is often overlooked by operators. If the apparatus does not secure specimens in an identical position, a fixture or other device should be considered.
Debris adhering to the body that is producing the wear might cause changes to the rate of abrasion. If the abradant is not changed or refreshed, this may lead to a decrease in the abrasion rate. The age or condition of the abradant can be an additional factor, particularly if it has a shelf life or is detrimentally affected by environmental / storage conditions.
Moreover, the provisioning of adequate training for laboratory personnel should not be ignored. Variation might also be introduced if an operator does not understand the correct usage of the device and is using it improperly.
A considered wear test can still yield valuable data without precisely simulating the application. Before any attempt is made to replicate surface damage, it is necessary to determine the purpose of the test and the intended application of the data. Although this is often overlooked, taking the time to declare the goal(s) before undertaking any tests will help to maintain focus and diminish any distractions.
Most companies undertake testing only as a way of satisfying a customer or industry specification without which they could not sell their product. Others use testing as a way of better understanding their product / process. Irrespective of whether the decoration is for functional performance or cosmetic appeal, the principle reason for companies conducting surface damage testing on decorated plastics is to make sure that they are manufacturing a quality finish which will endure throughout the product’s life cycle. The objective is to ensure the product maintains a minimum performance over its estimated life and resists wearing out or deterioration in use.
This represents a challenge as customers can often use products in applications for which they were not initially designed or tested. A regular problem confronting today's industry derives from the chemical attacks on coatings caused by household cleaning agents and personal care products. As a result of the various formulations of sun screens, insect repellents and hand creams etc. that are commercially available, testing the effects of each is not feasible. Consequently, starting with a stated test objective will help any test to stay on track.
Advanced Techniques to Interpret and Quantify the Results
Abrasion resistance is typically determined utilizing one of three approaches: number of abrasion cycles needed to wear the coating through to the substrate material (wear cycles per mil); loss in weight for a specified number of abrasion cycles (mass loss); or a visual alteration in the appearance of the specimen (amount of coating removed in comparison to predetermined standards). Additional approaches that have been utilized comprise depth of wear, volume loss, haze measurement (for transparent materials), and strength testing.
Most of the recognized abrasion test approaches yield a comparative measurement of wear resistance, and the materials are ranked by the results. Among decorated plastics, interpretation of the findings is usually undertaken via a subjective evaluation of the condition or appearance of the specimen following a predetermined number of abrasion test cycles. For repeatable results, a standardized grading system (e.g. 1 – 5 visual scale), with which to quantify changes to appearance and rank performance, is recommended. Reference photographs alongside a corresponding verbal description are typically provided to indicate an evenly spaced ranking. A further common approach is to establish the number of cycles needed for a specified level of destruction (e.g. change in gloss, color, thickness, wear through) to be generated.
Following ongoing technological innovations, magnification of the test sample can be achieved in house at a reasonably moderate expense. With the electronic industry endeavoring to persist with attempts to miniaturize components, there are tools that can be utilized to magnify parts in every cost range. A 10x enlargement utilizing a reticle eyepiece or microscope can remain satisfactory if an application is decoration-based. However, a magnification of 200x or 300x is often required if an application is performance-based. In such instances, software can be used for performing analysis of surface damage or for producing a 3D surface mapping of the part.
Whichever evaluation methodology is selected, wear rate might not always be a linear function of time or number of contact cycles, as other factors such as the materials, type of wear, and the contact conditions, may also have an impact. Results should be extrapolated with great care.
Conclusions
The principle reason for companies conducting abrasion tests is to make sure that they are manufacturing a quality product that is consistent in quality and characteristics, free from defects, and which will endure throughout its life span.
By testing, a company can demonstrate a product's observation of industry standards, conduct product research and development, supervise quality assurance of the manufacturing process; develop new products; supply buyers with information; indicate criteria for warranties; etc. The employment of a worthwhile test program is an essential precondition for the validation of a product's quality and for any guarantees that the specified materials or surface finish will satisfy the consumer's expectations.
Nevertheless, no laboratory abrasion test can ensure success in real life; there are just too many parameters to be simulated in the laboratory. The impact of abrasion is typically only one of multiple factors that influence product durability, and the relationship can differ with divergent end uses. Sole reliance on abrasion results to forecast wear-life is thus not recommended, unless there is data demonstrating a specific relationship between laboratory abrasion tests and actual wear in the proposed end-use. Although it is sensible to determine a predictive wear model for design and component life estimation, no model is universally adequate. However, with genuine consideration, abrasion test results can yield worthwhile, dependable data.
Taber Industries has extensive experience with testing physical properties including resistance to abrasion (wear) and scratch & mar. For assistance in developing your test methodology, send a product sample to Taber. Taber's in-house test experts have can share our knowledge testing a diverse range of materials along with various assessment criteria.
References
- ASTM International, G40 Terminology Wear & Erosion
- Ibid.
- International Standard ISO 6601, Plastics – Friction and wear by sliding –identifation of test parameters
- A.F. Zielnik, Test of Time: Will Your Finish Last? Finishing Today, p. 28 (June 2007)
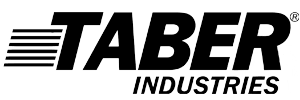
This information has been sourced, reviewed and adapted from materials provided by Taber Industries.
For more information on this source, please visit Taber Industries.