An interview with Alan Jaenecke, VP of Marketing at Taber Industries.
What are the most common issues with Taber test methods and results?
Occasionally, customers tell us that their Taber abrasion wheels are 'too aggressive.' Since their test results varied between tests, customers have concluded that the abrasive wheels must be the source of the variation.
Often, the customer has been running these tests for a long time and feels confident in their approach, so trying to identify the source of variation can be a challenge when the customer insists that they performed the test correctly.
In a recent instance, an innocent comment uncovered the true source of the problem. The technician conducting the test had recently been trained by the lab manager, who had over 15 years of experience performing the test.
Due to the simplicity of the Taber Abraser test, training consisted of the technician receiving a general overview of how to operate the instrument and then watching the lab manager perform the test.
The trainer had performed the Taber test for years, so training was simple and did not involve any review of the test method or a documented procedure. This resulted in some key details being omitted. As the lab technician had never seen the lab manager reference the test document, they had no idea what information they were missing.
Laboratory tests have the potential to provide considerable insight into the factors that contribute to a material's performance, but in order to generate repeatable and reproducible test results, the method that you follow must establish the necessary requirements and parameters or risk unintended variation.
Unfortunately, lab technicians often do not know how to handle requirements that their lab is not able to accommodate. As a result, they often consider these requirements optional and choose to ignore them. This is often due to a lack of understanding or a failure to acknowledge their decision's potential to introduce variation in test results.
What factors should be considered when preparing specimens for Taber tests?
Issues around specimen preparation are highly dependent on the material under evaluation, but most of these can be avoided simply by following standard industry practices. However, if a user has not read through the test method, some simple requirements may be missed.
The field of application is varied for the Taber Abrasion Test, and this includes solid materials, metals, plastics, coated surfaces (for example, paint, lacquer, electroplated), textiles (ranging from sheer silks to heavy upholstery), leather, rubber, linoleum and others.
This range of applications makes it difficult to offer one solution for all materials, but most test methods provide adequate directions on how to properly prepare the specimen.
For instance, the critical aspects of specimen preparation when conducting Taber tests on organic coatings (as per ASTM D4060) include ensuring a uniform coating is applied to a rigid panel with both surfaces substantially plane and parallel, and for the panel to be cured under agreed humidity and temperature conditions.
If the coating is not of a uniform thickness, the substrate may be worn through and exposed sooner in any area that has a thinner application of the coating - resulting in a failure within fewer cycles than if the coating had consistent thickness.
Applying the coating to a rigid panel, steel, for example, helps avoid cracking or delamination issues that may present themselves if the substrate is a flexible or compressible material.
If the specimen's surfaces are not plane and parallel, the abrasive wheels will not contact fully with the specimen's surface, resulting in uneven wear with heavier wear found on the inside (or outside) of the wear path.
For maximum performance, it is advisable to wait until the coating is completely cured. However, many manufacturer’s need data much quicker and are not able to wait for the recommended 3 or 4 weeks (or more).
In these cases, it is essential that stakeholders agree on how long the coating should cure before being tested and under what environmental conditions.
Another example of how specimen preparation can influence test results is taken from ASTM D3389, which provides guidance on evaluating the abrasion resistance of coated fabrics.
For this Taber test, the specimen should be free of holes, blisters, or other imperfections. Imperfections in the wear path may cause rapid wear, resulting in a premature failure.
If the specimen is thin, the vacuum system may lift the specimen during testing if a hold-down ring is not utilized – resulting in undesired contact between the vacuum pick-up nozzle and test specimen and possible damage.
To prevent this, ASTM D3389 suggests that the operator adheres the specimen to a suitable substrate such as a mounting card.
One factor that is often overlooked is the surface roughness of a homogeneous test specimen. For specimens that have a rough surface, it may be advisable to run a preliminary break-in period before measuring weight loss. Specimens that have a rough surface typically have less contact area between the abrasive wheels until the asperities are worn.
Including a break-in period allows for the rough surface to be worn smooth, ensuring full contact between the abrasive wheels and specimen surface.
If determining the abrasion resistance of a rough surface is the objective, the test should be monitored, and data should be recorded at different intervals so that results can be differentiated as the asperities wear down.
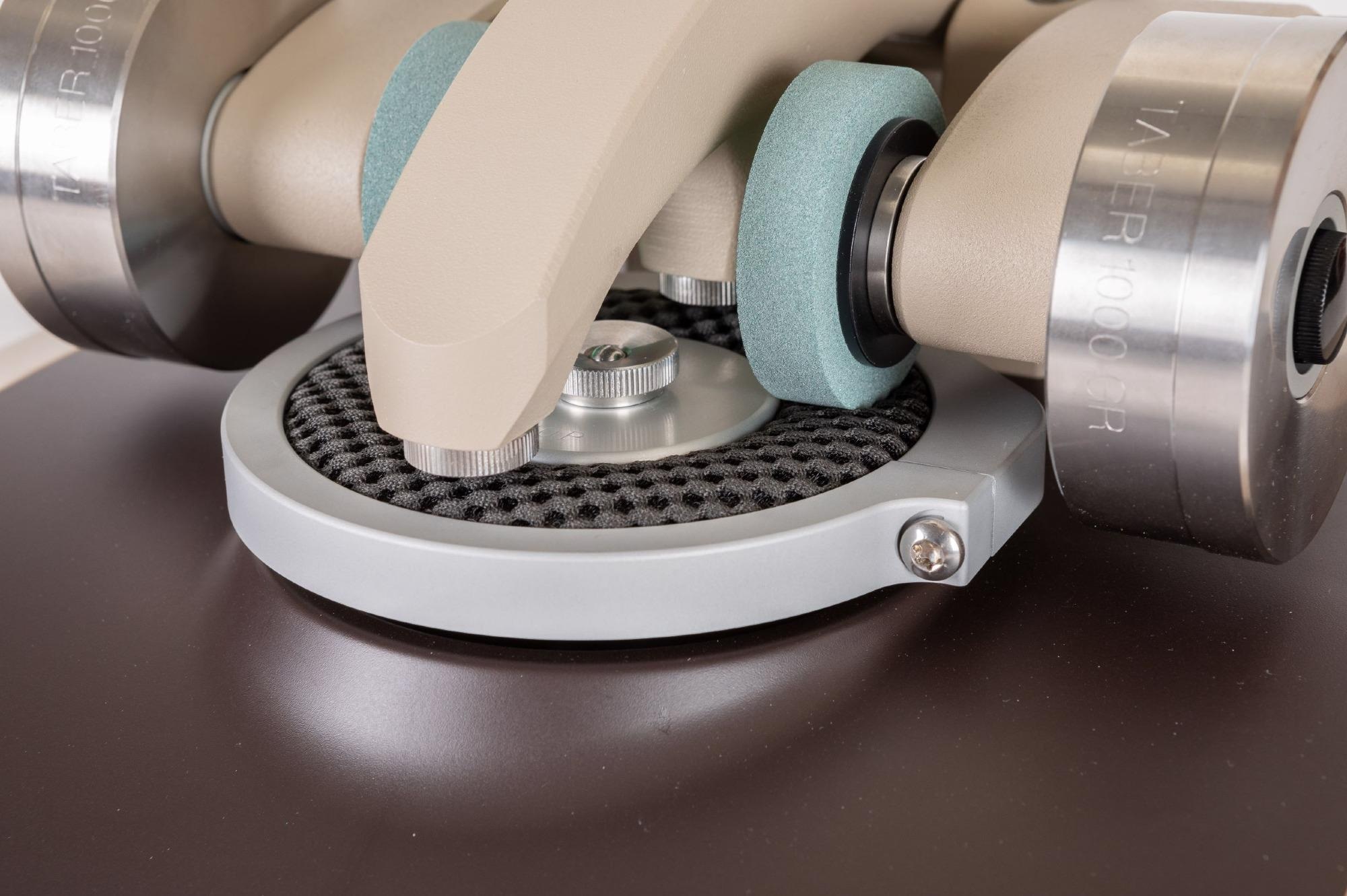
Image Credit: Taber Industries
How important is it to consider environmental conditions when looking to ensure reliable Taber test results?
Environmental factors are very important. Wear is a response to conditions to which the whole system is exposed, and it is important to recognize that resistance to abrasion can be affected by test conditions, including environmental factors.
Since many materials are sensitive to changes in temperature and humidity, tests that are performed under different environmental conditions (especially humidity) may introduce variations in the results.
Robust test procedures take this into account by requiring the test specimen to be conditioned prior to testing and stipulating that the test be performed in a temperature- and humidity-controlled environment.
Unfortunately, specimen conditioning or testing in a controlled environment is generally overlooked by companies that do not have a dedicated test lab (or are not able to control temperature and humidity).
While it may be desirable to test under different environmental conditions, the lab performing the test should make certain that they are doing so under the same criteria to ensure that the test results are comparable.
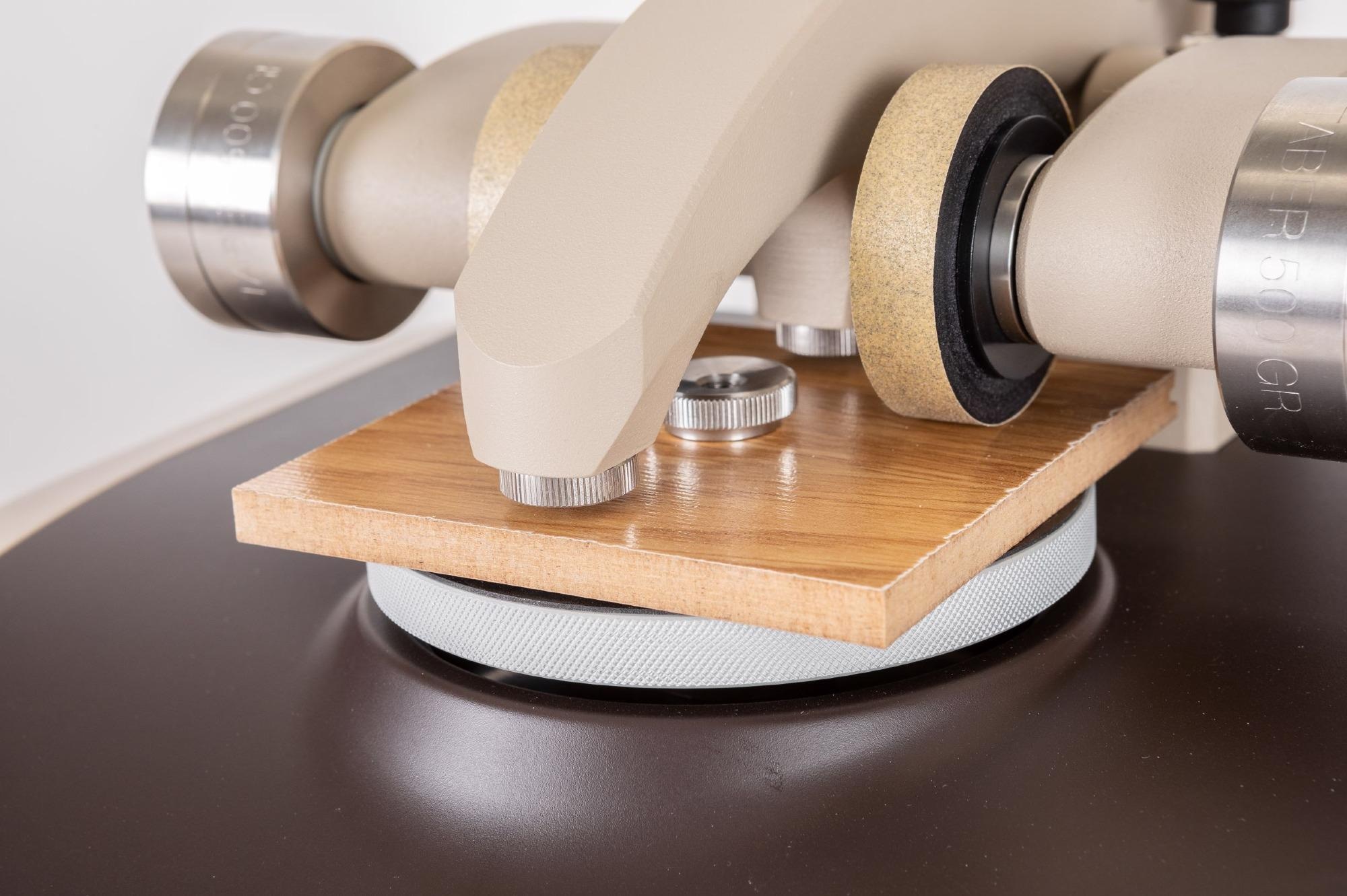
Image Credit: Taber Industries
Should the abradant be standardized?
Yes. Conducting a Taber test is relatively straightforward, but there is so much more involved than simply just selecting the abrasive wheel, load and number of cycles.
One of the most common issues involves resurfacing the abrasive wheels. When testing certain materials, the abrasive wheels may become clogged as particles worn off the specimen adhere to the working surface of the wheels. This changes the abrasive characteristics of the wheel and often impacts test results.
To reduce this variation, the working surface of abrading wheels should be cleaned and refreshed prior to use and if necessary, at regularly defined intervals during the test.
If an operator is not aware of this key requirement, they may start a new test using abrasive wheels with wear debris from a previous test present. This will produce results that show less mass loss or a higher number of abrasion cycles until failure occurs.
To ensure that the abrading function of the wheels is maintained at a constant level, ASTM D4060 requires the abrading wheels to be prepared prior to each test and after every 500 cycles, unless otherwise agreed.
What is the best way to remove this wear debris during the test?
The Taber Abraser includes a vacuum suction system to remove debris and abrasive particles from the specimen's surface during testing.
The vacuum system should start operating when testing commences, and it is essential that the vacuum nozzle gap be set properly. Most test methods specify the gap between the specimen's surface and vacuum nozzle, with 3 ± 1 mm being the most common. A vacuum setting of 100% is standard, but the operator is still expected to monitor the test to ensure the vacuum removes any wear debris.
For certain materials, abrasion tests utilizing the Taber Abraser may be subject to variation due to changes in the abrasive characteristics of the wheel during testing.
Depending on the material being tested, it is possible for wear debris to adhere to the surface of the abrasive wheel instead of being removed by the vacuum system. When this occurs, the abrasive wheels should be resurfaced at more frequent intervals to maintain their rate of abrasiveness.
To determine if more frequent resurfacing is needed for a coating being tested to ASTM D4060, the operator may plot the total mass loss every 50 cycles. If a significant negative change in slope is observed prior to 500 cycles, the point at which the slope changes will determine the resurfacing frequency.
What are the most common and most recommended evaluation techniques?
For abrasion resistance tests, an evaluation technique that provides a quantitative result, such as mass loss, is ideal. Typically, this is reported after a set number of abrasion cycles, but it could also be to a specified point, for example, when the substrate is exposed.
When test results require a judgment of the appearance or condition of the specimen, it is critical to establish a grading scale or define the pass/fail criteria. A visual grading scale may be used to rank the specimen when testing to a fixed number of abrasion cycles.
Pass/fail criteria can be used when testing a fixed number of abrasion cycles or the number of abrasion cycles required to reach a predetermined endpoint. In all cases, there should be a written description of the damage or a photographic or visual representation (or both) of the abraded specimen.
What should an operator consider when comparing the results of different materials?
When comparing abrasion resistance between two or more materials, the test parameters must be the same, for example, the abrasive wheel, vacuum suction level and load. It is also essential to recognize that differences between material compositions may require additional consideration in order to make an accurate comparison.
A recent change to the "Significance and Use" section of ASTM D4060 includes characteristics of coatings that could cause problems, for example, the presence of air entrainment bubbles that may be found in some flexible coatings. As the material is worn away, if air bubbles are exposed, this will change the contact surface area of the abrasive wheels (and the associated pressure applied by the wheels), resulting in higher mass loss.
D4060 also points out that coatings, that include dense fillers, typically result in greater mass loss but often have less change in coating thickness. If an operator looks at just the mass loss readings, they may reach the wrong conclusion that the coating with the lowest mass loss is the most abrasion-resistant.
Data presented in the ASTM D4060 precision statement clearly indicates that epoxies had more than double the mass loss compared to a urethane coating. The conclusion one might draw is that urethanes are more robust than epoxies, but that is not supported by field data.
The 2019 release of ASTM D4060 includes a note that states, "when comparing the wear resistance of coatings that have different specific gravities, a correction for the specific gravity of each coating shall be applied to the mass loss to give a true measure of the comparative wear resistance."
Coatings that include silica, metal oxides or other extremely dense particulates may wear the abrasive wheel. Wear debris from these coatings will include particulates that may cause three-body abrasion, which could contribute to the breakdown of the coating if not removed by the vacuum suction system.
Coatings that have different surface roughness or coefficient of friction ratings should also be accounted for during comparison tests.
What is the best approach for calibrating a Taber Abraser, and what issues should operators be aware of?
Despite seeming simple, testing using the Taber Abraser involves a complex series of interactions between each critical component.
Proper instrument calibration is vital as an out-of-tolerance Taber Abraser can lead to significant differences in test results.
Improper alignment of the abrasive wheels can lead to each wheel abrading a different path from its complementary wheel, as well as the wheels on other machines. Wear path surface area can differ by as much as 20%, and the area abraded by both wheels on a sample could be less than 50% of the total abraded area for that specimen.
An abraser arm that is misaligned creates a wheel alignment issue. A 4 mm misalignment would trigger a change in wear area of approximately 1000 mm2 and result in a less aggressive test. Wheel overlap would also be reduced from 100% to approximately 65%.
Wheel bearing rotation plays a critical role in the proper operation of the Taber Abraser. Worn wheel bearings may have an excessive play or inhibit easy wheel rotation.
When looking for signs of bearing wear, it is advisable to check the shaft on which the wheel revolves and the pivot point of the abrader arms, including any sideways, twisting, or other motion outside the specific rotation of the arm or the shaft. A "stuck" bearing will cause the wheels to slide and result in a more aggressive test.
A properly working Taber vacuum system is necessary to remove debris from the specimen surface that is generated during the wear test. Be certain to clean or replace vacuum filters and bags as needed. It is also advisable to clean the vacuum pick-up nozzle occasionally. With reduced vacuum suction, debris can build up on the specimen, potentially changing the type of wear from two-body to three-body.
For some materials, this debris may form a protective barrier that reduces the amount of abrasion caused by the wheels. For other specimens, debris buildup results in a more aggressive test leading to higher than normal results.
Testing with wheels that are rounded or crowned may result in significant deviations from expected results. Crowned wheels increase the pressure at the sample interface due to the reduced contact area of the wheel. As a result, specimens may show an early failure along with an undersized wear path.
Table runout issues (typically observed as a table wobble) can result in improper wear as the wheel contact area changes during the table rotation. A heavy wear pattern that is seen on the outer edge of the specimen could be a result of table runout; runout off by as little as 0.035 " could potentially influence results.
The abraser arm provides a standard load of 250 g on the wheel. By using the auxiliary weights, standard wheel loads of 500 or 1000 g can be obtained. The auxiliary weights are marked with the total load that will be exerted on the wheel and equals the combined mass of the abraser arm and auxiliary weights.
Since the arms work independently, the loads are listed per arm and should not be combined. An operator that mistakenly believes 500 g per each of the two abraser arms results in a total load of 1000 g will be testing with half the required load. This will lead them to report higher abrasion resistance than operators conducting the test correctly.
While most companies have a calibration schedule for their instrument, operators do not always know the age of their instruments. The Taber Abraser has been in use since the 1930s. To find out how old a Taber Abraser is, operators can check the first two digits of the serial number - prior to the year 2000, the first two digits represent the year of manufacture, and after 2000, it is the first four digits. For example, an instrument with the serial number 841234 was manufactured in 1984 making it over 35 years old.
How can operators ensure their test method is current and that it adheres to best practice guidance?
To ensure that test data is reliable, it is advisable to follow an established test protocol that has been proven to be robust and reliable. When I asked the previously mentioned customer about the year the test method that they were following was released, the customer admitted having an older version in their files.
While this does not necessarily create a problem, it is important to ensure you are following current test methods. Most standards organizations have procedures in place to ensure their test methods are peer reviewed on a regular basis and kept up-to-date.
Operators should not assume that because a particular test method has been in use for a long time, it cannot be updated. New technologies or advancements may require additional information to be added or require the procedure to change.
Test methods should be reviewed and audited to ensure that operators are using the latest documentation available, and technicians should be routinely evaluated to verify that tests are being carried out correctly.
Accreditation to ISO/IEC 17025 demonstrates that a laboratory is capable of providing valid results and that the individuals performing the work are competent. However, this may not be a viable option for a small test laboratory in a manufacturing facility. In this case, the quality department could conduct its own audit.
Alternatively, Taber Industries can provide expertise, guidance and experience. This could involve a visit to our lab, on-site training seminars at a customer's facility, or consultations on abrasion or scratch resistance testing.
Getting involved with the industry organizations that are responsible for the test methods utilized is also a good option for many organizations – as well as a range of networking opportunities. One benefit is that operators would have the ability to participate in method reviews and inter-laboratory studies themselves.
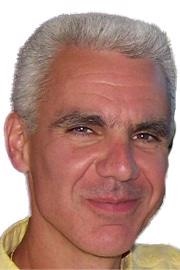
About Alan Jaenecke
Mr. Jaenecke has been employed by Taber Industries since the year 2000, and plays a critical role in the company’s Materials Test and Measurement division. Although his main responsibilities include sales and marketing, Mr. Jaenecke is Taber Industries’ technical contact for standards organizations including ASTM, ISO, NEMA, Tappi, SPE, and SAE. Through industry affiliations, he has written and developed new test methods and coordinated numerous reviews for existing methods. Having previously operated Taber’s in-house test facility, he has a wealth of experience performing wear and durability tests. Alan received his Masters of Business Administration from the State University of New York at Buffalo, where he earned a dual concentration in Marketing Management and Corporate Financial Management.
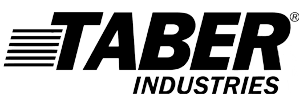
This information has been sourced, reviewed and adapted from materials provided by Taber Industries.
For more information on this source, please visit Taber Industries.
Disclaimer: The views expressed here are those of the interviewee and do not necessarily represent the views of AZoM.com Limited (T/A) AZoNetwork, the owner and operator of this website. This disclaimer forms part of the Terms and Conditions of use of this website.