Modal testing of structures with closely coupled modes is a task performed very frequently. On many occasions, structures have modes that possess very similar resonant frequencies. In one such case, a plate’s specific bending mode may happen at a nearly identical frequency to its torsion mode. Among more complicated geometries and structures, this “accidental” frequency degeneracy is commonplace. However, when a structure is planned to be highly symmetric, the coupled modes are anticipated to be “by design.”
In finite element (FE) simulations, all these modes are found separately. Nevertheless, in testing in the real world, it can be a challenge to extract the modes from measurement data. This application note introduces a new method to separate closely spaced modes with MIMO testing (multiple input, multiple output) that uses two automated modal hammers.
.jpg)
Figure 1. A PSV-3D Xtra Scanning Vibrometer measuring a brake disk, excited by the SAM Scalable Automated Modal Hammer.
The Need for Modal Extraction Using MIMO
In the case of a brake disk, the frequency splitting of the peaks is usually small because the disk is typically highly symmetric. When animating the measured deflection shape at the maximum frequency of a slightly widened resonance, the effect of both underlying mode shapes put together can be seen and can’t be split from each other. For FE correlation, the engineer would like to take out all mode shapes from the test data and correlate them with corresponding modes from the FE simulation.
This extraction is accomplished by curve fitting of the measured data using special modal analysis software such as PolyWave or FEMtools. If the asymmetry of the object is big enough and the excitation of the underlying modes can be compared, the modal extraction can separate the symmetric modes and allow for proper correlation of the total data set when using one excitation source at one fixed point. Often these conditions are not realized and, for some or even all modes, only one out of the two symmetric modes can be extracted.
Let us regard the scenario of a rotationally symmetric brake disk. Because of its symmetry, the FE model calculates two first bending modes, both at an identical frequency but with a 45° shift in the node line in-between the two mode shapes. The situation is a lot less ideal in an actual modal test:
- The disk is not completely symmetric, which leads to a frequency splitting of the two resonances and separated peaks in the spectra. Dependent upon the amount of separation and damping (peak width), the peaks may be resolvable or appear as a marginally widened single peak.
- The amplitudes of each resonance rely on the selected excitation location. For instance, if excitation is located close to one mode’s deflection shape node, one resonance will overshadow the spectra, the other will hardly be able to be detected.
The use of test data acquired by exciting at two or more locations will frequently overcome this issue. This approach using multiple excitation locations is named MIMO - (multiple-input, multiple-output). MIMO tests are usually performed by fixing two or more shakers to a structure and performing a principal component analysis of the obtained data to separate the influences from each excitation source.
Since these shakers contact the structure, they influence the vibration behavior of the structure. This is especially true for lightweight objects or structures with little damping, where the perturbing influence of the shaker can notably alter the outcome of the results.
A Better Approach: Scanning Laser Doppler Vibrometry (SLDV) with Automated Modal Hammers
Scanning Laser Doppler Vibrometers (SLDV) are top-of-the-line instruments for measuring the vibration response without mass-loading or changing the damping of the test object. Beyond this, in comparison to mass-adding contacting transducers, a high spatial resolution scan is easy to perform with a focused laser beam, which clearly reveals the higher-order deflection shapes. Similarly, an automated modal hammer with its transient impact avoids changing the vibration behavior of the object under test and is an ideal match for a modal test when using scanning vibrometers.
Currently, there have been reports of MIMO tests using several shakers or a single hammer exciter; however, no MIMO tests using scanning vibrometers and two hammer exciters are present in the literature. In the following experiment, this extremely beneficial setup is tested.
Experimental Setup
A brake disk is suspended on soft foam and excited by a Polytec SAM Scalable Automated Modal Hammer. The 3D surface velocity is measured at 256 individual scan points with a Polytec PSV-3D Xtra Scanning Vibrometer. Two measurement runs were undertaken, each one relating to a different hammer excitation position. The results for the first bending mode are shown in the following images. The marked points correspond to the respective excitation locations. The beginning excitation point predominantly excites the resonance that is seen on the left-hand side; the second point’s response is seen on the right-hand side.
Data Handling for Modal Extraction
While using two excitation sources at the same time (i.e. two shakers), the integrated PCA (Principle Component Analysis) option of the PSV software can be of use in separating the influence of each excitation source in the following post-processing. In this scenario, the measurements are performed separately, which creates two independent data files. The two data files can be merged manually into one common universal file and are imported into the PolyWave or FEMtools software for modal extraction. The results are then viewed in comparison to those gained with only one excitation point.
For modal extraction that uses stability diagrams as a base, a maximum modal order must be specified. The correct choice of this parameter is vital for the quality of the results: if selected too low, not all modes will be extracted which can obscure the separation of close-by symmetric modes. If selected too high, many extraneous computational modes can be seen that do not relate to “real” physical ones. This latter effect leads to big, off-diagonal values in the MAC (modal assurance criteria) matrix, which quantifies the similarity of the obtained mode shape.
Since the symmetrical resonances are only marginally separated, the curve fitting was performed in small spectral segments; each segment contained one or two visible peaks and corresponded to one to three underlying mode shapes. From the results of the simulation, eleven modes were expected in the selected frequency range, five pairs and one rotationally symmetric mode.
.jpg)
Figure 2. Points of excitation; ODS for first excitation point (left), ODS for second excitation point (right).
Single Excitation Point Results
To start, a modal extraction was performed with the results from a single excitation point measurement. In this case, two evaluation methods were attempted: one with a low maximum modal order of 12, and one with a significantly higher maximum order of 60. For the low maximum order of 12, not every mode can be found identifying just 6 out of 11 modes, plus one computational mode (Figure 3). For a top order of 60, non-physical computational modes appear: 13 modes are indicated instead of 11 physical modes. Notable off-diagonal values in the AutoMAC indicate computational modes. Even further, two mode pairs 6 and 7 around 2.065 kHz and 12 and 13 around 3.250 kHz - are not separated well (Figure 4).
Mode
# |
Frequency
[Hz] |
Damping
[%] |
MPC
[%] |
MPD
[*] |
MAC alias
[%] |
☑ 1 |
1141.057 |
0.04 |
99.9 |
1.6 |
0.4 |
☑ 2 |
1613.210 |
0.23 |
100.0 |
1.1 |
99.3 |
☑ 3 |
1619.208 |
0.16 |
99.8 |
2.1 |
99.3 |
☑ 4 |
2065.746 |
0.03 |
99.5 |
3.9 |
0.0 |
☑ 5 |
2299.589 |
0.18 |
99.8 |
2.4 |
0.0 |
☑ 6 |
3186.371 |
0.09 |
97.7 |
10.4 |
0.4 |
☑ 7 |
3249.870 |
0.06 |
99.5 |
4.4 |
0.2 |
.jpg)
Figure 3. Mode table and AutoMAC for a single excitation point test with a low maximum order of 12.
Mode
# |
Frequency
[Hz] |
Damping
[%] |
MPC
[%] |
MPD
[*] |
MAC alias
[%] |
☑ 1 |
1141.088 |
0.03 |
100.0 |
1.0 |
0.4 |
☑ 2 |
1145.476 |
0.04 |
100.0 |
0.4 |
0.2 |
☑ 3 |
1612.595 |
0.21 |
100.0 |
0.7 |
0.1 |
☑ 4 |
2065.520 |
0.04 |
99.5 |
3.5 |
15.1 |
☑ 5 |
2065.668 |
0.04 |
93.8 |
15.2 |
15.1 |
☑ 6 |
2286.801 |
0.17 |
99.8 |
2.4 |
0.4 |
☑ 7 |
2299.565 |
0.19 |
99.9 |
1.8 |
0.4 |
☑ 8 |
3186.303 |
0.08 |
99.8 |
1.9 |
0.4 |
☑ 9 |
3195.274 |
0.11 |
99.8 |
2.3 |
0.2 |
☑ 10 |
3249.974 |
0.06 |
99.8 |
2.5 |
1.7 |
☑ 11 |
3251.203 |
0.05 |
96.8 |
10.5 |
1.7 |
.jpg)
Figure 4. Mode table and AutoMAC for a single excitation point test with a high maximum order of 60.
Mode
# |
Frequency
[Hz] |
Damping
[%] |
MPC
[%] |
MPD
[*] |
MAC alias
[%] |
☑ 1 |
1141.073 |
0.03 |
100.0 |
1.0 |
0.5 |
☑ 2 |
1145.486 |
0.05 |
99.8 |
2.1 |
0.4 |
☑ 3 |
1613.324 |
0.25 |
100.0 |
1.1 |
99.5 |
☑ 4 |
1618.715 |
0.22 |
99.8 |
1.9 |
99.5 |
☑ 5 |
1631.379 |
0.07 |
96.8 |
9.5 |
91.1 |
☑ 6 |
2065.015 |
0.07 |
98.4 |
7.0 |
78.6 |
☑ 7 |
2065.995 |
0.03 |
97.0 |
10.3 |
78.6 |
☑ 8 |
2287.820 |
0.16 |
99.8 |
2.8 |
0.7 |
☑ 9 |
2299.319 |
0.20 |
99.6 |
3.7 |
1.3 |
☑ 10 |
3186.388 |
0.09 |
99.8 |
2.1 |
0.4 |
☑ 11 |
3195.319 |
0.10 |
99.1 |
4.0 |
0.3 |
☑ 12 |
3249.786 |
0.07 |
99.9 |
1.8 |
23.0 |
☑ 13 |
3251.546 |
0.05 |
88.6 |
20.1 |
23.0 |
.jpg)
Figure 5. Mode table and AutoMAC for a dual excitation point test with maximum order of 12. All modes were identified and well separated with no computational modes introduced.
MIMO Results, Using Two Excitation Points
Next, MIMO results using two excitation locations were processed. As the results are obtained from two separate measurement runs, which are merged into one file after the test, no principal component analysis (PCA) is required. This is because there is no influence from the second excitation source onto the transfer function from the beginning source to the output measurement points.
From the curve fitting, it was quickly confirmed that there are notable benefits when using the combined file with two excitation locations. Beginning from a low modal order, the fitting process works reliably, reducing evaluation time and leading to a complete set of modes without the addition of non-physical modes.
This result was achieved with only a top modal order of 12. In Figure 5, the resulting mode tables and the corresponding Auto-MAC matrices are demonstrated. From the mode table and AutoMAC diagram in Figure 6, it's obvious that the extracted modes are nicely decoupled. When observing the mode shapes, it is apparent that all relevant modes were located. All the symmetric modes were found. Mode three is rotationally symmetric and can only be seen in one instance.
In Figure 7, the modal participation factor records that for many modes, one of the excitation sources (reference 1 or 2) is dominant. This confirms that separating modes becomes a lot easier with the use of two excitation points. For modes five and ten, the participation of the two excitation points is more even. This means that the excitation points were not the best selected for the total separation of these two specific pairs of symmetric modes, but are still tolerably suited, as is viewed in the mode shape table and the Auto-MAC. The two excitation locations that are superposed on the first pair of symmetric mode shapes in Figure 8 illustrate this prior point.
It's apparent that the starting excitation point is on a maximum of the first mode shape which is a minimum of the second mode shape and the other way around. This provides confirmation that splitting this mode pair becomes a lot easier with the use of two excitation points.
.jpg)
Figure 6. Full set of Extracted mode shapes.
.jpg)
Figure 7. Modal participation Factor for the dual reference test.
.jpg)
Figure 8. Points of excitation are shown with respect to the maxima of the first mode pair.
Conclusion
To conclude, by combining a PSV-3D Scanning Vibrometer with two SAM Scalable Automated Modal Hammers, a top-of-the-range MIMO modal test was conducted and was extremely useful for mode separation, symmetric structures and FE model correlation.
In particular, for lightweight and low-damped, symmetric structures where the mass loading effect of two or more shakers obstructs quality results, this type of approach is a truly realistic option.
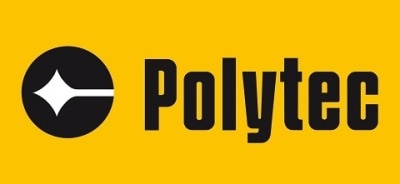
This information has been sourced, reviewed and adapted from materials provided by Polytec.
For more information on this source, please visit Polytec.