The Loccioni Group has achieved a widely recognized leadership in the implementation of automated quality control and testing systems in production lines and laboratories, thanks to close collaboration with the world’s largest manufacturing companies for over 40 years.
MUSA (Measurement Unit in Sound-proof Area) is a turn-key, fully automated testing method for washers, integrating vibration and noise evaluations which are typically carried out in R&D laboratories. A total (100%) evaluation on the finished products is an appropriate technique to guarantee a high standard of quality. This is because statistical tests on a random choice of samples cannot confirm the quality of a full production run.
It is widely known that vibration tests allow discrimination between faulty and good products. Hence, the analysis of the vibration signals may be utilized for quality control of household appliances. LDV (Laser Doppler Vibrometry) is commonly used for in-line quality control where non-contact measurements are crucial.
.jpg)
Figure 1: MUSA measurement unit layout.
.jpg)
Figure 2: LDV pointing at the washing machine tub.
.jpg)
Figure 3: Velocity time signals for a good (above) and faulty (below) washing machine.
MUSA – the System
This article shows an industrial solution for in-line monitoring of washing machines, where the employment of microphones and LDV permits an objective vibroacoustic characterization of the product in order to establish specific mechanical faults. The system mainly comprises:
- Three microphones, one per station, located on the rear part of the washing machine, facing the motor
- A sound-proof cabinet that can decrease the external noise by about 35 dB, containing three stations running simultaneously (Fig. 1)
- Three IVS-400 industrial LDVs, one per station, pointing at the tub of the washing machine in a radial direction with respect to the axis of the motor (Fig. 2)
Three washing machines are brought to the sound-proof cabinet and stopped in front of each station before the cabinet doors are closed. Each washing machine is taken to the spinning phase and the signals coming from the microphones and LDV are gathered at the same time, both during the run-up and the steady state.
.jpg)
Figure 4: Washing machine RPM computed from the LDV.
.jpg)
Figure 5: Velocity signal STFT of a good washing machine during run-up.
.jpg)
Figure 6: Velocity signal FFT for a good washing machine during steady state phase.
.jpg)
Figure 7: Power spectrum of the velocity time signals for a good (left) and faulty (right) washing machine.
.jpg)
Figure 8: Front panel of the vibration test system.
The core of the system is the signal processing software which:
- Quantifies the machine’s RPM directly from the LDV signal (Fig. 4)
- De-noises the velocity signal
- Analyzes the LDV and microphone signals throughout the transient state in the time-frequency-domain (STFT, Fig. 5)
- Analyzes the LDV and microphone signals throughout the steady state in the frequency domain (Fig. 6)
Features are calculated both in the run-up and steady state phases. The chosen features are compared with fixed thresholds to determine the status of the machine. These values are then related to the specific model of the machine being assessed. The sum of the energy in specific frequency bands is gathered and correlated to the specific defect, for example the defect associated with the electric motor.
The main frequency peak in the spectrum corresponds with the RPM of the washing machine, as seen in Fig. 7. It is approximately 20 Hz, which is relative to the speed of the tub (1,200 RPM). The faulty machine exhibits extra frequencies around 280 Hz and 560 Hz, as seen in Fig. 7.
It can be easily recognized that these frequencies are associated with the motor (the fundamental and the second order harmonic). It is established that the ratio between the RPM of the motor and washing machine RPM is 13.5. Hence, it follows: RPM motor = 13.5 x 1,200 = 16,200, or 270 Hz.
Results
The software has been developed using the LabVIEW® programming language. By utilizing the LDV, the system can identify the following defects:
- Defective bearings
- Defective motor
- Unscrewed counterweight
- Unscrewed or damaged pulleys
- Drum unbalance
- Defective belt (dirty, damaged or incorrectly positioned on the pulley)
- Defective/missing spring connecting the drum to the cabinet
The microphone mostly permits the operator to identify the defects that create noise but are not large enough to produce vibratory effects on the machine, like missing material (e.g. a screw) inside the tub, a ground wire touching the pulley, etc.
Conclusion
The solution described above exhibits how the developed data analysis system, comprised of a data acquisition system and pattern recognition algorithms, and appropriate sensors, can be applied successfully to mechanical defect diagnostics for washing machines in the production line.
Certain features have been extracted to replace the subjectivity of human inspection testing with an objective assessment of product quality. Notably, laser Doppler vibrometers can be utilized to identify most of the mechanical defects in washing machines.
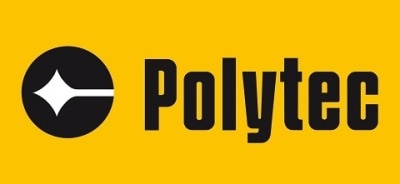
This information has been sourced, reviewed and adapted from materials provided by Polytec.
For more information on this source, please visit Polytec.