Electronic devices are usually thought of as securely and safely mounted in a protective enclosure or sitting on a table top, yet portable devices require completely different standards to which electronics must be built.
Vibrations and shock loads, which electronics must endure can be especially significant when mounted in a boat or a car. Smooth water or roads are easy to handle, but they are also required to survive the roughest seas and bumpiest dirt roads, and these electronic devices must be built to endure these higher forces without failing.
Electronics are mounted securely to the chassis of the vehicle with differing amounts of isolation, yet these components must endure more extreme vibration forces than the occupants. This can make the design of such devices challenging, particularly for small, delicate automotive electronic structures.
As electronics are required do more and more in our vehicles, their durability becomes even more vital. Heavy, tall or items such as relays, inductors, capacitors and chokes must be securely mounted so they cannot damage their mountings, or flex so they break their electrical connections.
They can flex an entire PC board even when properly mounted, leading to failures in other places when they experience vehicle-induced vibration. Calculating the motion in these modules is best performed by utilizing a non-contact technique such as a laser vibrometer. In order to assess the movements on automotive electronics, Dr. Arvind Krishna at Delphi identified the benefits of the laser vibrometer.
Doppler laser vibrometers only need a line of sight to the object being measured. They are highly accurate, do not require a location to bond the accelerometer, have a flat response curve, do not measure the shape or texture of the part, and do not change the structure in any way because they only touch the part with a beam of light.
Capacitors
Dr. Krishna measures tall components on PCBs, which pose possible vibration durability challenges for Delphi’s applications. Capacitors are unique because they can also experience durability failures when exposed to vehicle-induced vibrations.
The housing must secure the capacitor, but the leads cannot break, and the mounting also cannot flex the board causing neighboring components to fail. Even when this is achieved, capacitors can still fail internally. This makes capacitor choice and testing even more crucial.
.jpg)
Measuring a capacitor‘s cradle while mounted in a product housing.
.jpg)
Laser “Dot” indicating signal capture spot on the body of the Capacitor mounted on a PCB.
.jpg)
Pressure Sensor – Thermistor Lead Response.
Pressure Sensors
A pressure sensor is another especially challenging device. A high spatial resolution non-contact method is required to measure the motion without touching the device due to the slender lead wire and the small size of the thermistor (2 – 3 mm ball).
The laser vibrometer achieves this objective and also has the capability to measure large and small amplitudes over a wide range of frequencies providing information about the tip’s motion at 775 Hz, 9290 Hz, and 1879 Hz. This permits the researchers to develop new designs and new capabilities of the whole structure.
Dr. Krishna has made improvements to Delphi’s devices as a result of the information gathered by the laser vibrometer. Measuring on parts regardless of their construction, material, or size allows researchers to identify the way a part is moving accurately and quantify the enhancements from each modification.
Dr. Arvind Krishna said about the Laser Vibrometer: “Ease of use, transportability and accuracy have allowed the Polytec laser vibrometer to become a popular test alternative to traditional accelerometers in the lab. We look forward to finding novel applications for the laser equipment in the future!”
.jpg)
Acceleration response PSD captured using Polytec Vibrometer at capacitor body resulting from random vibration input.
.jpg)
Excellent signal provides tip motion information, strongest at 930 Hz.
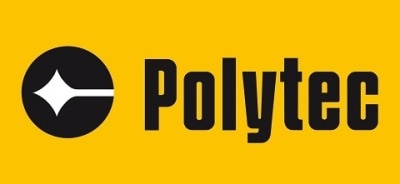
This information has been sourced, reviewed and adapted from materials provided by Polytec.
For more information on this source, please visit Polytec.