Commercial exploitation of lamb wave inspection has been restricted by weaknesses in detection methods. Structural damage can be identified clearly from locally increased in-plane and out-of-plane vibrations, by employing the non-contact technique of 3D Scanning Laser Vibrometry. This technique is quick, simple, and reliable, avoiding complex Lamb wave propagation studies, baseline measurements and signal post-processing.
Introduction
Aircraft manufacturers, designers, and operators face many measurement and test challenges. New, large-capacity civil airframes which make better use of composite materials are being developed and will become more widespread. Also, new military structures show better performance by employing more structural complexity. End-users of these new aerospace structures call for high operational availability and lower life-cycle costs.
These goals can be attained with a wider utilization of damage-tolerant design concepts and the application of new materials, which results in lighter structures and better performance. While these new aircraft are being developed, the existing fleet is aging and must be maintained.
Many life extension programs have been considered and carried out. Military aircraft are redesigned to add new weapon capabilities and civil structures are being converted from passenger aircraft to freighters. These developments are a huge challenge for the current aircraft structural inspection and maintenance techniques.
A significant maintenance effort is needed for aging aircraft structures. The application of damage-tolerant concepts and new materials in next-generation aircraft also require better and more reliable structural health monitoring, with regular periodic inspections, to ensure a safe and extended operational life.
Damage Detection with Lamb Waves
There are numerous technologies for automatic damage detection in aerospace structures. Lamb wave inspection is a widely employed method, which is based on guided ultrasonic waves, i.e. ultrasonic wave packets propagating in bounded media.
There are three major disadvantages related to conventional Lamb wave damage detection methods:
- Current signal processing and interpretation methods employed for damage detection use signal parameters which reference baseline data representing the “no damage” condition. These parameters can be influenced by parameters other than structural damage such as bad coupling between the transducer and the structure or changes in temperature.
- Often associated with complex data interpretation, Lamb wave monitoring strategies need highly qualified NDT technicians for point-by-point field measurements. So, broad deployment is restricted by a lack of properly trained technicians and higher costs.
- A large amount of actuator/sensor transducers are needed for monitoring large structures. This is slow, labor-intensive and costly. It is impractical to cover an aircraft with many thousands of bonded or embedded transducers from a logistic point of view.
3D Scanning Laser Vibrometry
Laser vibrometers can overcome many challenges associated with Lamb wave damage-detection methods. The application of a non-contact, PSV Scanning Laser Vibrometer to structural damage detection is shown in Figure 1. Lamb waves from a piezoceramic transducer are sensed by utilizing the PSV-3D Scanning Vibrometer from Polytec, shown in Figure 2.
The 3D Scanning Vibrometer covers the full optically accessible surface with a high density of sample points. The vibration vector is measured, including both out-of-plane and in-plane components at every sample point. These measurements are assembled into an intuitive 3D animated deflection shape.
Examples of damage detected in aerospace specimens employing Lamb wave monitoring can be seen in Figures 3 and 4. These results demonstrate that structural damage can be identified by locally increased in-plane vibration amplitude (e.g. fatigue crack in Figure 3, and delamination in Figure 4) and by attenuation of out-of-plane vibration amplitude (e.g. fatigue crack in Figure 3).
Conclusions
Laser vibrometer scans can reveal structural damage and its severity, for example, delamination area and crack length. Simple contour maps and profiles of Lamb wave amplitude across the structure are enough to observe the damaged areas and do not involve baseline reference measurements in undamaged structures, examinations of complex Lamb wave propagation in the structures, or signal post-processing to extract damage-related features.
This technique is quick, straightforward, reliable and immune to environmental influences. We thank Professor Wieslaw Staszewski of Sheffield University for his work in this area.
.jpg)
.jpg)
Figure 1. Experimental setup for Lamb wave damage detection using 3D Laser Scanning Vibrometry as receiver.
.jpg)
Figure 2. In-plane and out-of-plane Lamb wave responses plotted using Polytec’s PSV Software.
.jpg)
Figure 3. Fatigue crack detection in metallic structures with Lamb waves – RMS amplitude contour maps with amplitude profiles across fatigue cracks for: 75 kHz in-plane vibration (above) and 325 kHz outof-plane vibration (below).
.jpg)
Figure 4. Impact damage detection in composite structures with Lamb waves – amplitude contour map with amplitude profiles across delamination for 100 kHz in-plane vibration.
.jpg)
Figure 5. Measurement Setup: Piezoactors for local excitation of Lamb waves on a carbon fiber wing section.
.jpg)
Figure 6. Full-field measurement with high spatial resolution on large components or complete aerospace structures.
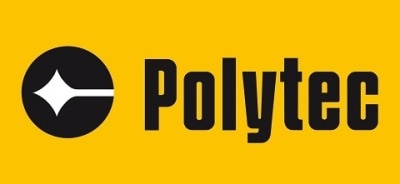
This information has been sourced, reviewed and adapted from materials provided by Polytec.
For more information on this source, please visit Polytec.