Testing is vital in the aerospace industry to achieve success in product development and implementation. Mechanical testing of products and materials of use in aerospace applications is regulated by stringent standards and accreditation is frequently a necessity. The type of testing performed includes, but is not limited to, tensile, compressive, flexural and fatigue testing.
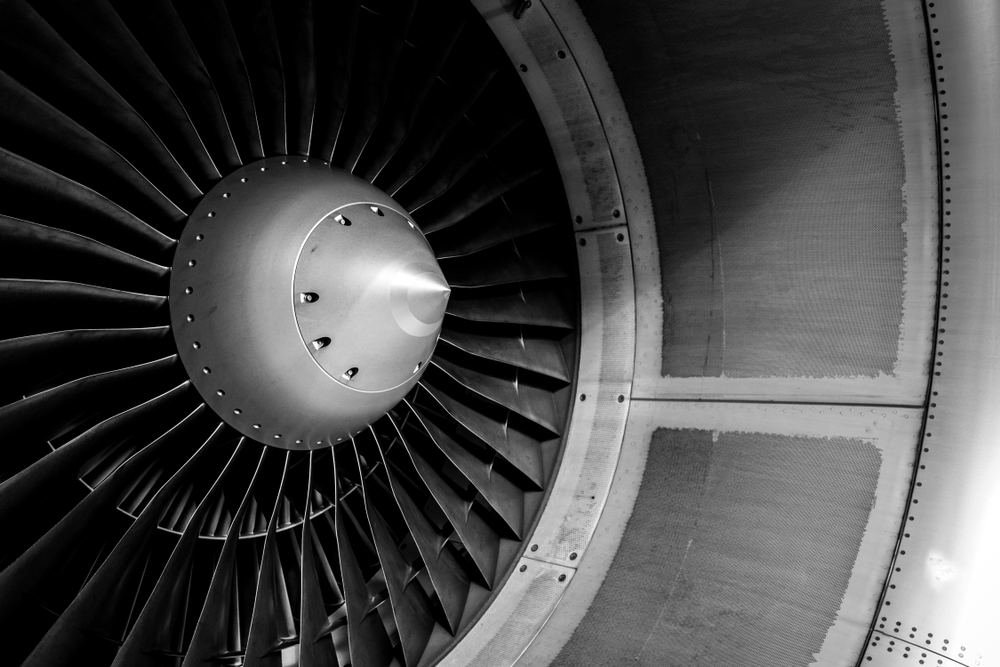
Image Credit: Bychykhin Olexandr/Shutterstock.com
Highly developed universal testing machines and custom testing systems are of use in running tests and the determination of properties, for example breaking strength, ductility, elongation, fracture toughness, and fatigue life cycle. ADMET provides adaptable standard designs and custom machines kitted out with advanced software and accessories such as environmental chambers to conduct aerospace testing while repeatability and reproducibility of test results is ensured. Additionally, ADMET provides calibration and verification to reach ISO/ASTM and A2LA standards.
Mechanical Testing for Aerospace
Dependent upon the kind of material tested and the application it is meant to be of use in, quality control and material science professionals decide the kind of testing and the environmental conditions needed in determining the material’s mechanical features.
Tension testing is one of the most frequently used mechanical tests and is typically applied to test materials of use in aerospace applications. The stress-strain curves gained when the tests are finished grant knowledge on properties such as the tensile strain, strength, and modulus. Stress-strain curves are often created by universal testing machines equipped with an extensometer. The extensometer allows input on strain data while the stress is gained by dividing the force measured with the load cell or the pressure transducer by the original cross-sectional area.
Compression testing applies force in a compressive direction to take measurements of compressive strength which is the utmost load a material can withstand before it breaks or yields. Additional properties measured include compressive strain, compressive yield stress, modulus of elasticity, and deformation. Testing machines can be kitted out with deflectometers and displacement transducers to take measurements of the specimen deformation data.
Flexural testing, also known as flex or bend testing, is undertaken to take measurements of the flexural strength and modulus of materials using 3-point and 4-point bend fixtures. The flexural modulus is a feature of import for materials of use in aerospace applications as it is an indicator of a material’s stiffness. The yield point, the stress level where there is an detectable growth in strain with zero increase in stress, may also be analyzed running flex tests.
.jpg)
Test report showing flexural strength. Image Credit: Admet Inc.
Fatigue testing develops a fatigue strength curve that is of use in testing the fatigue properties and life cycle of products through repeatedly applying and releasing force. Fatigue life, the number of stress or strain cycles that must occur to cause failure, can be impacted by the stress level, stress rate, the environment, cyclic wave form, and the material’s conditioning. Materials used in the aerospace industry frequently have specific fatigue criteria that they are required to achieve to be used in a certain design.
.png)
Live display during fatigue testing. Image Credit: Admet Inc.
Shear testing reports include shear strain, shear stress, and shear modulus in tension or compression loading. In the aerospace industry, products like composites, fasteners, and adhesive material are tested in shear to measure the shear stress/strain data. ASTM D5379 is a test standard developed to take measurements of the shear properties of composite materials with the use of a special compressive shear testing fixture. ASTM F1362 describes testing for shear strength and shear modulus of aerospace glazing interlayer materials. Dependent upon the type of material and application that will be tested, lap shear testing methods include ASTM D1002, ASTM D3163, ASTM D5656, and ASTM D5868.
Product Configurations for the Aerospace Industry
ADMET testing systems are developed and constructed in Norwood, Massachusetts. ADMET’s in-house product development and engineering teams enables added versatility and customization on the basis of the specific needs of their customers.
Included in the following is a list of test machine configurations that have played important parts for some consumers in the aerospace industry.
Inverted Servo-Hydraulic Machine for Landing Gear Testing
A custom product configuration, the inverted servo-hydraulic system was designed with a top-mounted actuator. The design enables testing load vs. position and cyclic properties of landing gear components like shock absorbers in compression. The load capacity was chosen by the consumer and the configuration has been used to test a much greater number of components than first planned.
.jpg)
Inverted frame test system. Image Credit: Admet Inc.
Wear Testing Machine for Airline Seat Cushions
The “Squirmin’ Herman” test system was developed on the basis of Boeing standard BSS-7302 and is of use in investigating the impact of aircraft passenger wear on seat upholstery fabrics and fire blocking layers.
ADMET wear testing machines come with a dynamic actuator and the fixturing needed to run tests that can be catered to choice. This featured configuration demonstrates the dynamic foam testing system with the Squirmin’ Herman fixture, designed per the description in the standard. Both position and load can control the dynamic movement.
ADMET Custom Material Wear Testing Machine
Foam Tester for Seat Cushions
Indentation Force Deflection (IFD) testing is a must for aircraft seat cushion manufacturers. ADMET’s eXpert 5603F Foam Testing Machine supplies the user with a compact device to perform ASTM D3574-B1 and ISO 2439 IFD testing on foams. The typically used frame accommodates 15” by 15” samples, and other designs available entail wider base platens to test bigger specimens.
.jpg)
IFD Foam Tester. Image Credit: Admet Inc.
ADMET foam testing systems enable users to run automatic IFD tests. To begin with, the height of the sample at the pre-load force is automatically measured. Then the sample is compressed to precisely the previously defined compression percentages (commonly 25% IFD, 65% IFD, and return 25% IFD). The preflex cycle and dwell time can be enabled or disabled during the test procedure. Following the test, an individual test report and grouped test report is available, and every test is saved automatically and may be exported to a .csv file.
eXpert 5603F machines can also be kitted out with different accessories to perform tensile, elongation, peel, and tear tests.
ADMET eXpert 5600F Foam Testing System - ASTM D3574 - Tensile & Compression
Universal Testing Machines for Composites, Plastics, Fabrics, Seatbelts, and More
20,000 Pound Capacity Webbing Tensile Break Test
ADMET universal testing machine (UTM) options include designs that enable the user to conduct mechanical strength testing on all materials from an aircraft’s tip to tail. Testing systems are accessible in electromechanical and servo-hydraulic configurations as well as in single column and dual column frame alternatives.
ADMET’s electromechanical offerings include the single column eXpert 7600 series and dual column eXpert 2600 series.
eXpert 7600 series can go up to 5kN and can conduct tension, flexure, compression, and more. Single column frames are often an inexpensive and compact solution for low-force capacity testing. Additionally, the extended column option provided with these systems enables high-elongation materials to be tested.
eXpert 2600 series universal testing machines can be found in tabletop or floor standing configurations from 2kN to 300kN. The adaptable design of eXpert 2600 machines enables testing in tension, compression, flexure, adhesion, shear, peel, and more with various grips, ASTM fixtures, and additional accessories ready for use.
For tests, both static and dynamic, that are high capacity, the servo-hydraulic eXpert 1000 series machines are extremely cost-competitive. Contrary to some designs currently available for purchase, ADMET servo-hydraulic system frames are supplied with integral power supply and electronics thereby making efficient use of highly valued lab space.
All ADMET testing systems mentioned previously can come with accessories such as environmental chambers that enable testing to be run under a variety of environmental conditions. ADMET’s MTESTQuattro controller can log and graph temperature together with the test data enabling aerospace engineers to analyze how materials can react to temperature changes.
System Retrofits
.jpg)
eXpert 2654 with environmental chamber. Image Credit: Admet Inc.
ADMET provides an upgrade/retrofit option to extant testing machines in the form of software, digital controllers, grips/fixtures, or extensometers. Retrofit upgrades improve testing systems’ functionality, add flexibility in the diversity of test results and analyses the user can conduct. Additionally, ADMET retrofit packages enabling users to run tests following standardized test methods such as ASTM standards as well as develop customized test procedures from scratch. Dependent upon the system and new imperatives, retrofits enable expense savings when compared with the purchase of a new universal testing system.
An in-depth diagnostic methodology is a requisite to retrofit extant universal testing systems. ADMET’s Electrical and Engineering team can retrofit static, dynamic, electromechanical, and hydraulic systems.
Controller and Software Systems
The MTESTQuattro controller and software are recommended for aerospace applications to provide versatility as well as precise and duplicable tests. MTESTQuattro operates on an 8 kHz closed-loop PID controller to make sure of accurate and repeatable testing.
Additionally, to MTESTQuattro, ADMET’s DC1x Digital Fatigue Controller can be relied upon for fatigue tests. The DC1x is equipped with a touch panel display and may also be used with ADMET’s GaugeSafe software to view and edit test setups and view waveforms and peak/valley/cycle data in real-time on a computer using Windows. For additional analysis, data and results from the tests can also be loaded into spreadsheet programs.
A significant characteristic of the DC1x Fatigue Controller is that it is capable of maintaining consistent load or displacement amplitudes for dynamic testing even up to 40 Hz.
Conclusion
The aerospace industry necessitates premium quality testing for precise and duplicable results that will ensure successful prototypes and designs develop into safe and efficient end products. ADMET testing systems, all constructed at the facility in Norwood, Massachusetts, feature adaptable designs and custom solutions that aid consumers in this high-stakes industry reliably reach their testing targets every day.
This information has been sourced, reviewed and adapted from materials provided by Admet, Inc. - Materials Testing Equipment.
For more information on this source, please visit Admet, Inc. - Materials Testing Equipment.