In wastewater applications, if a pump stops working, it is usually assumed that the pump is the source of the problem. However, this is not always true. In fact, a large number of failures happen due to the system’s effect on the pump or due to additional external environmental/ operational factors.
Pumps are just one area of a system comprising of multiple parts that affect their operation, and constantly restoring broken down pumps without clarifying the root source of the failure happens frequently. Doing this can cost a lot over time and may result in stressful circumstances. In the normal duplex pump station scenario, for instance, a downed pump can produce a lot of alarm as with one pump down, the one lasting pump is all that is in the middle of an operational station and a possible sewage overflow.
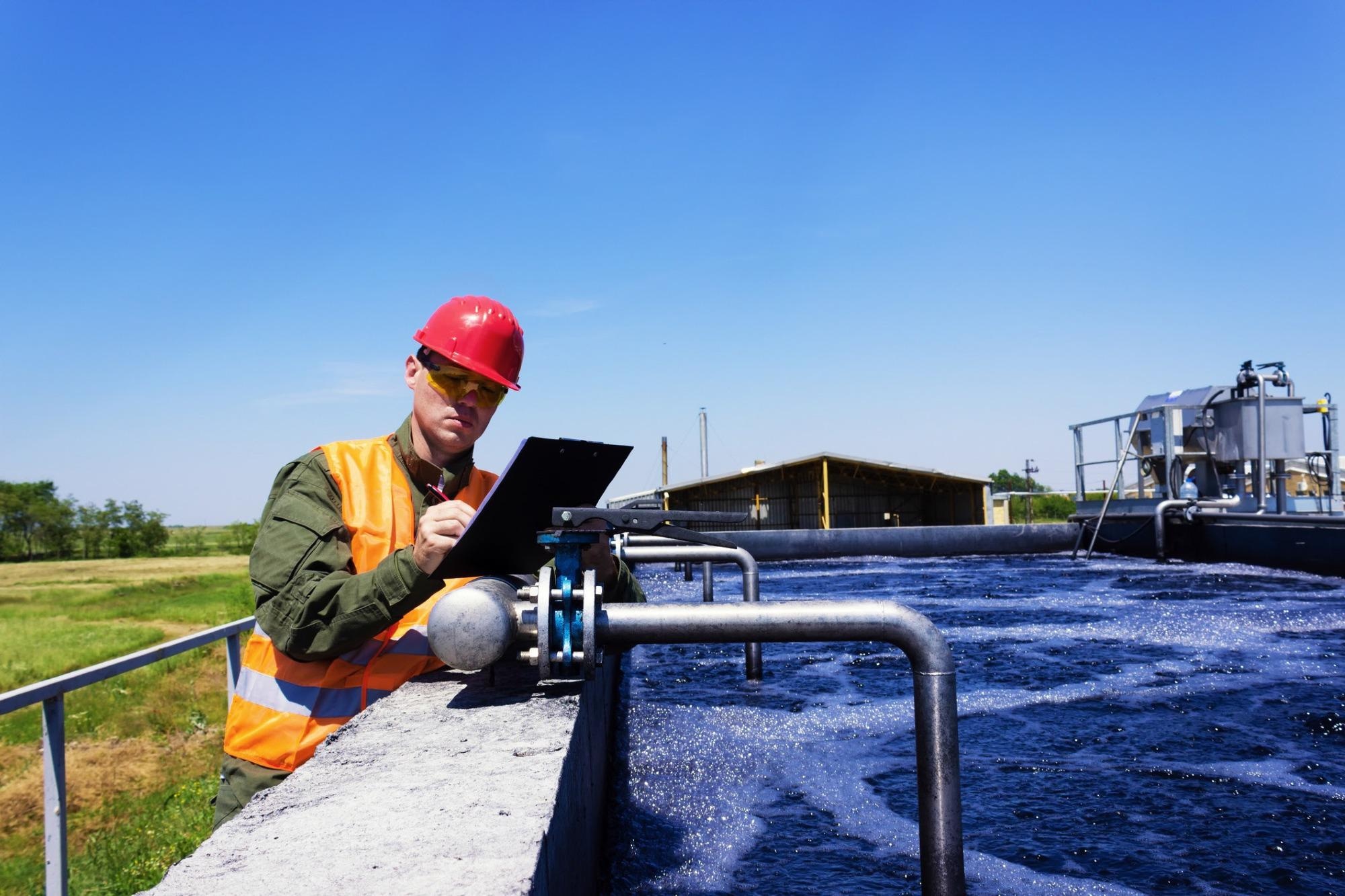
Image Credit: Homa Pump Technology
Because pumps are so vital to wastewater systems, it is prudent to perform more system troubleshooting on strange or repetitive break downs to locate and explain the root cause issue(s) that adversely affect the system. Apart from the notion that the pump is the issue, operators or maintenance staff may reason that there isn’t adequate time or resources to dig deeper into difficulties.
Pinpointing the true cause of issues is probably cheaper and less time-consuming than often assumed. Good suppliers who distributed the original equipment and the manufacturers’ applications engineering/ service staff that assist them are superb resources accessible to help with this or to offer advice. This begins by examining symptoms such as unusual sounds and strange occurrences of electrical trips, etc., that may be associated with persistent pump failures.
Troubleshooting problems is possible, or at least narrowing down an issue to allow for a more targeted service call by assessing important indicators and raising the right questions.
Getting Started
The core triggers of pump failures usually come under one of two categories - electrical or mechanical. Poor-quality power can cause pump/ motor malfunctions, so start by getting power readings. Are the voltage and amperage values within the usual range, and are they stable between phases, etc.? Voltage unbalance amid phases on the supply side will create an excessively elevated current unbalance and motor temperature increase, shortening motor life; a 1% voltage unbalance can generate a current unbalance in the range of 6-10%, and with a 3% voltage unbalance, the resulting motor temperature rise is boosted by up to 18%.
Voltage supply unbalance can be due to uneven single-phase loads on the three-phase grid, frequently located in regions where residential single-phase air conditioning loads are common. Voltage drop and the related current growth from being fitted long distances from the transformer can have an adverse effect, as can numerous issues occurring from the employment of adjustable frequency drives. This can be seen in the section on VFDs below.
For mechanical or performance problems, and additionally, to possibly ascertain the reason that the motor current or input power is high, it is vital to understand where the pump is functioning on its curve. The operational “duty point” of the pump is the intersection of the system curve and the pump curve. In the design period, the system curve of the pump discharge piping and force main is usually determined with some conservatism built-in. With time, the actual system curve can alter because of things such as sedimentation accumulation in the piping, air entrainment at piping high points, scale accumulation on pipe walls, etc.
Older stations might have been sized because of an expected heightened future capacity that might or might not have taken place. It is common for new equipment retrofits of older stations to be chosen based on the existing system curve and design pump duty point, which could be far from the actual conditions, causing an improperly sized pump.
Flow meter readings, if accessible, are perfect for ascertaining the actual flow rate of the pump in the system and permits the pump and actual system curves to be plotted, displaying where the pump is running contrasted to the design circumstances. If a flow meter is not accessible, a drawdown test can be employed to ascertain the flow rate of the pump. A drawdown test is carried out by first calculating the volume of the sump as a function of sump level, then noting the amount of time it takes to fill the sump between two specific sump levels (inflow).
Then, following the sump filling, noting the time to pump down to a particular elevation. Measuring over a smaller range - 1 to 2’ range is usually preferred because a smaller duration usually means that the inflow stays mostly constant. Using the formula [Pump Flow = Gallons/Minute Inflow + Gallons/Minute Pump Down] offers a satisfactory pump flow rate measurement. In a lot of failure cases, the pump is not functioning within specifications, so defining definite pump flow provides an understanding of pump health and can offer hints about problems, like the pump running off its curve or beyond the specified Acceptable Operating Range (AOR), where recirculation cavitation and/ or extreme vibration may take place.
Pressure recordings from a pressure gauge on the discharge line rectified back to the pump discharge elevation are also useful for establishing where the pump is being employed. Once a low-flow indication has been established, the following checklist can be consulted:
- Is the check valve fully opening?
- Is the head on the pump in excess of the original design?
- Is there sufficient NPSHA at the site contrasted with pump needs?
- Is there cavitation (low-pressure condition where the liquid transforms into a vapor at the eye of the pump impeller) because of insufficient Net-Positive Suction Head Available (NPSHA)?
- Does the measured flow and pressure relate to the pump curve? If not, identify unanticipated inlet losses.
- Is the impeller displaying premature wear?
- Is there a clog in the piping?
- Is air entrainment happening from cascading flows in the sump?
If the basics above have been assessed, and a definitive issue still has not been identified, diagnostic testing should be considered. A full-service testing organization can bring to site equipment that records power quality and can further assess mechanical difficulties by completing vibration testing and additional tests.
VFDs Can also Present Problems
Variable frequency drives (VFDs) are frequently used as they permit a variety of flows by adjusting the pump curve through speed regulation, work as soft starts for a gentler ramp-up preventing the high preliminary motor inrush currents, and allow. VFDs offer additional problems that can cause problems with the pump. Some frequently occurring VFD-related problems include low operational speed. If the pump is too big, or if the duty point is centered on maximum station inflow conditions, then most of its operation can be at a lower speed. In such cases, it is vital that the lowest speed setting is set so that the flow velocity through the piping system is large enough to stop sedimentation from settling out and that adequate pressure is produced so as to conquer the static head.
If the wastewater is strongly concentrated with rags or stringy materials, low speed operation can create rag balls or fouling accumulation to take shape in the eye of the impeller, which may cause many issues. Increasing the pump speed up to full speed operation should be considered for a small amount of time during start-up and shutdown, in this case to “flush” the pump at the start and finish of its pumping cycle.
There are multiple considerations with VFD use like length of cable, cable size, and type of VFD that can create voltage distortion in the shape of spikes or harmonics, which may damage the motor stator, or trigger frequent mode voltages and shaft voltages which create bearing currents. Bearing currents generate heat and degrade bearing grease and races, possibly resulting in complete failure. In these instances, sine wave filter or dV/dT filter could be necessary.
There are multiple system and operational/ environmental facets of a pump application that can cause pump breakdowns in wastewater applications, so repairing repeat failures without further investigation is an inadequate method. For long-term operational security and savings, deciphering and fixing the original cause is best.
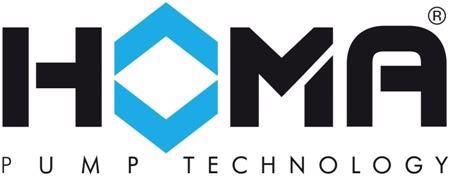
This information has been sourced, reviewed and adapted from materials provided by Homa Pump Technology.
For more information on this source, please visit Homa Pump Technology.