A team of McGill University researchers, collaborating with colleagues in the United States and South Korea, has devised a novel method for producing high-performance lithium-ion battery materials, which might help phase out expensive and/or difficult-to-source metals such as nickel and cobalt. The results were reported in Nature Communications.
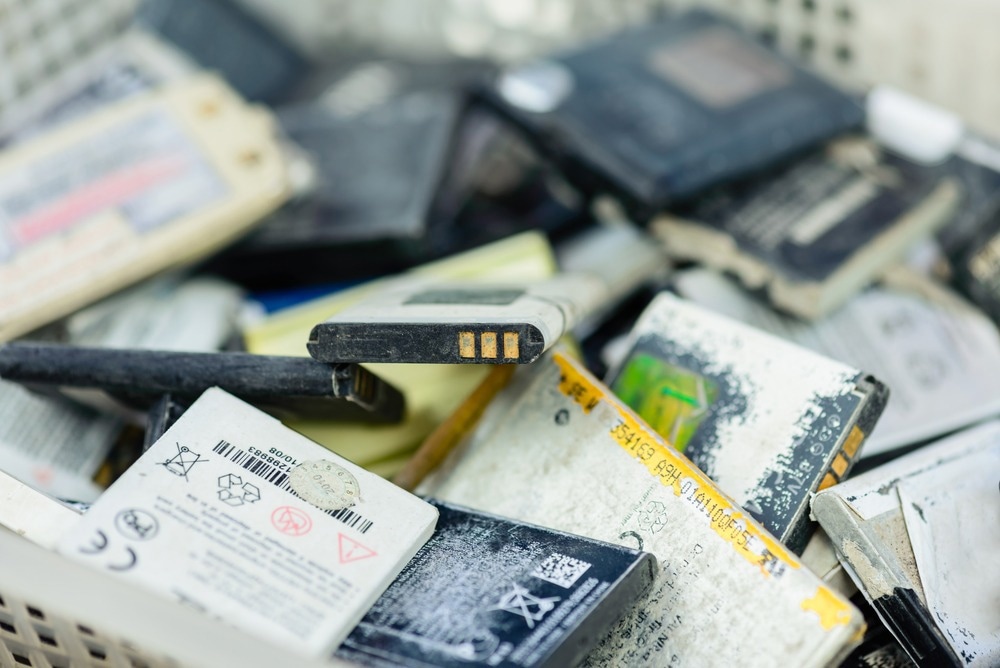
Image Credit: Smile Fight/Shutterstock.com
The team’s achievement is developing a more efficient technique of generating "disordered rock-salt" (DRX) cathode particles, an alternative battery material. Until recently, manufacturers struggled to manage the size and quality of DRX particles, making them unstable and difficult to employ in production environments.
The researchers solved this difficulty by devising a technique for producing uniformly sized, highly crystalline particles with no grinding or post-processing necessary.
Our method enables mass production of DRX cathodes with consistent quality, which is essential for their adoption in electric vehicles and renewable energy storage.
Jinhyuk Lee, Study Corresponding Author and an Assistant Professor, Department of Mining and Materials Engineering, McGill University
According to the researchers, the findings point to a feasible path for more sustainable and cost-effective lithium-ion batteries, which are essential components of the worldwide move to electrified transportation and renewable energy.
A Materials Breakthrough
The researchers devised a two-step molten salt method to create the DRX particles. Molten salt allows better control over particle creation, increasing efficiency and quality.
Prior to restricting the particles’ development, the researchers encouraged nucleation, or the creation of tiny, homogeneous crystals. As a result, they were able to create battery-ready particles smaller than 200 nanometers, which is thought to be crucial for maximizing the performance of these materials in lithium-ion batteries.
“We developed the first method to directly synthesize highly crystalline, uniformly dispersed DRX single particles without the need for post-synthesis grinding. This morphological control enhances both battery performance and the consistency of large-scale DRX cathode production,” added Lee.
After 100 cycles of charging and discharging, the novel materials retained 85% of their capacity in battery cells. That is more than twice as effective as DRX particles made with more antiquated techniques.
From Lab to Industry
A McGill team conducted the study in partnership with scientists from Stanford University's SLAC National Accelerator Laboratory and the Korea Advanced Institute of Science and Technology (KAIST). It was partially funded by Wildcat Discovery Technologies, a battery company located in the United States that wants to scale DRX technologies for commercial applications.
The team's technology might also make the process more scalable and energy efficient, removing a major barrier to the widespread use of DRX cathodes. Given the global demand for batteries, this might have a significant ripple effect.
Acceptance of our work highlights both the fundamental insight and industrial potential of the method. It shifts the field toward scalable manufacturing.
Hoda Ahmed, Study Lead Author and PhD Student, Department of Materials Engineering, McGill University
According to the researchers, this synthesis technique opens the way to next-generation lithium-ion batteries that are more sustainable, inexpensive, and easier to make on a large scale.
Wildcat Discovery Technologies and the Natural Sciences and Engineering Research Council of Canada provided funding for the study.
Journal Reference:
Ahmed, H., et al. (2025) Nucleation-promoting and growth-limiting synthesis of disordered rock-salt Li-ion cathode materials. Nature Communications. doi.org/10.1038/s41467-025-60946-4.