Flowmeter Technologies and Their Applications
Why do we measure flow? What do we need to know in respect of basic knowledge on flow measurement? What do we need to know about the most used terminology in flow measurement?
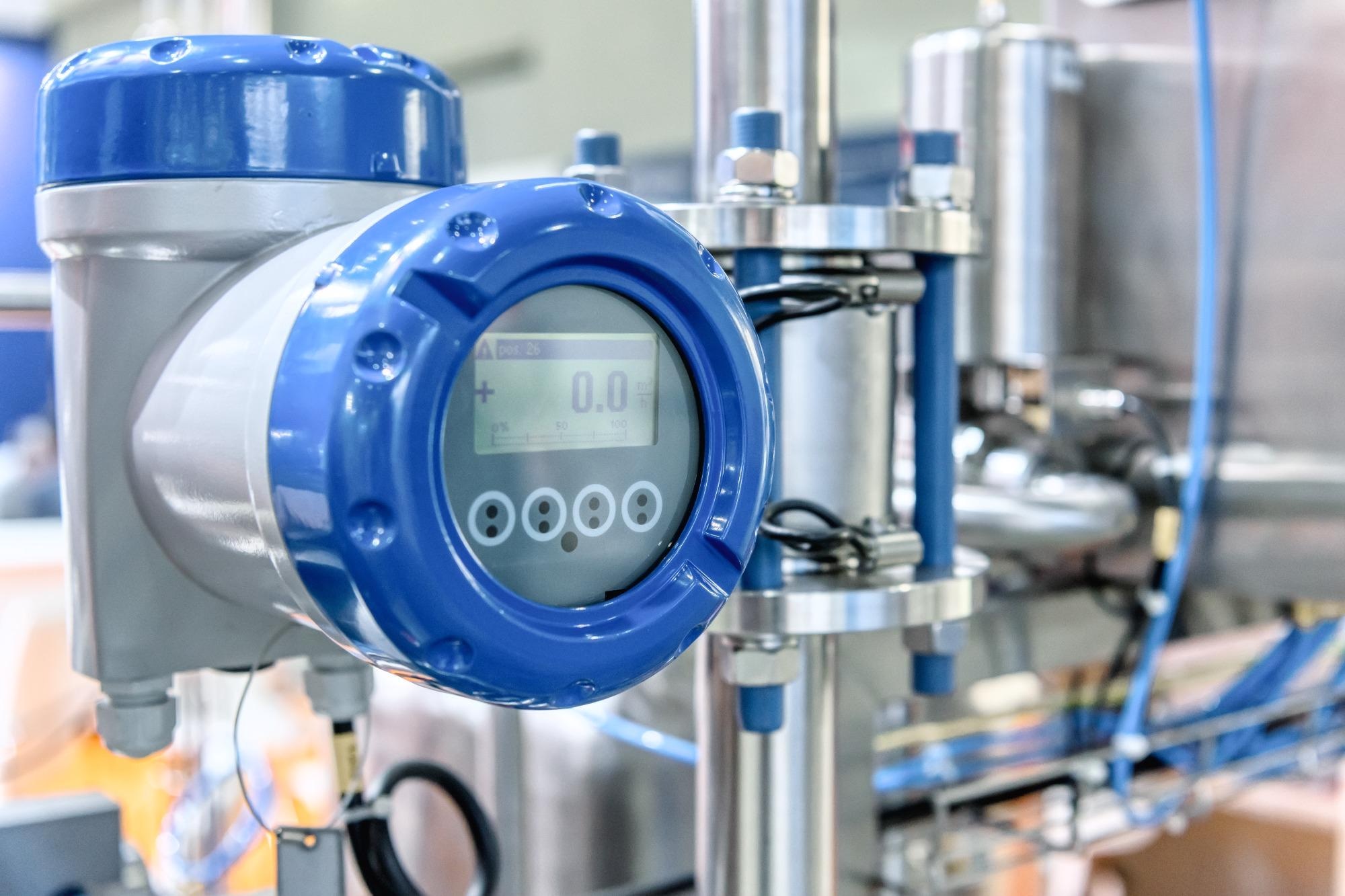
Image Credit: shutterstock.com/nordroden
Flow measurement is one of the most important aspects of process control after pressure and temperature. This is one of the variables most used and important for most of the processes in a variety of industries.
Acid is one of the most frequently measured process variables. It is also one of the most challenging ones. There are many different technologies that can be used for acid measurement, and the measurement technologies interact quite closely with the different applications and installations.
This article will give an overview of different flow measurement technologies available, their pros and cons, where to use them and where not to use them.
Considerations when Performing Flow Measurement
There are several topics to be aware of and to recognize when selecting the right technology as there is no one single flow meter technology that fits all applications.
How can someone determine which flow technology meets their specific application situation and needs? To answer this question, it is important to realize what the different purposes are for flow measurements.
The first consideration is custody transfer, or a billing part of flow measurement is the measurement of a quantity of fluid produced or generated to sell or pass to another customer or business partner.
The next point is product integrity, meaning that, in processes consisting of different flow streams and different flow quantities needing to be blended or mixed, it is very important to be in control of all the different flow streams and mix them together to make sure that the product quality and the output of the process is exactly what is needed.
Once close control is established of all the different flow as streams, it is important to know them precisely to gain efficiency. A user can only optimize processes that they measure. Thus, it is very important to measure specifically all the different flow rates to optimize the efficiency of different processes.
Once a user has a process, they need to be measuring the different variables to be in control of them. In the monitoring process, variable control is quite important.
Last but not least is the consideration of safety. Uncontrolled flows, like a cooling loop with too little flow or some other processes with too much flow, can generate major safety hazards. The ability to measure and then react to uncontrolled flows can help prevent any kind of damage.
Flowmeter Technology in Industry
With these different purposes, flowmeter technologies are differently distributed in different industries such as oil and gas, marine, petrochemical power, pulp and paper, food and beverage, waterways, water and mining, and metal.
For instance, in the food and beverage industries, a very hygienic version of a flowmeter is required; in mining and metal, technologies might include abrasive slurries; and with oil and gas applications, hydrocarbons are central.
While the individual requirements and specific details must be considered, the main purposes of flow measurement remain the same.
For flow measurement, there are six flow technologies representing most of the market, three of which have almost an evenly distributed market share in respect of the number of flow measurements and smaller technologies.
The big three are differential pressure flow measurement (DP flow), electromagnetic flow measurement and Coriolis flowmeter measurement. Depending on the different market studies, all three technologies are of almost equal size with respect to measurement points.
The other three technologies are ultrasonic flow measurement, vortex and swirl flowmeters and variable area meters. Other flowmeters usually comprise mechanical meters and thermal mass meters, among others. These different technologies are commonly used and widely spread.
Accuracy with Flowmeter Technology
The first and main purpose of measurement is to get a certain accuracy. For flow measurement, it is very important to understand that the accuracy statement, or accuracy definition, can be given in one of two ways: accuracy as percent of weight or accuracy as percent of full scale.
With a statement such as 1% of full scale, users will receive the same 1% relative error at the beginning at maximum flow. Of course, the relative error gets bigger and will grow bigger the further away it is from the maximum flow.
To illustrate this concept, we have a definition as a percentage of rate with 100 gallons per minute. With 100% gallons per minute and 1% accuracy, the uncertainty range is from 99 to 101 gallons per minute, representing 1% uncertainty.
With 50 gallons per minute, a few stay with 1% accuracy of the rate, and the result is 49.5 gallons per minute with 250.5 gallons per minute as an uncertainty range.
The relative error stays the same 1%, but the absolute number of errors (the error in respect of gallons per minute allowed) has shrunk from one gallon per minute to half a gallon per minute.
That example is clearer with 10 gallons per minute, with a range of 9.9 to 10.1, making 1%. The relative error always stays the same while the absolute changes which is the opposite of the definition of percent of full scale.
For example, at 100 gallons per minute with 1% of full scale, the uncertainty range is from 99 to 101 gallons per minute, representing 1% uncertainty. But with low flow rates, for instance, 10 gallons per minute, one gallon per minute is still a permissible error.
This flow rate is already representing 10% of relative error. That is the major difference of rate with constant relative error and off-scale with the constant absolute error. This is something very important to be aware of because quite often, at first sight, users just look at the number statement for accuracy.
If users have poor repeatability, they automatically have poor accuracy. Poor repeatability means the arrows are all over the place, so none of them have hit the target. This situation is off-target and not repeatable.
On the other hand, if conditions are very repeatable, always hitting the same spot, that is important, although that spot could be a little bit off target, meaning you have good repeatability but still have a poor accuracy simply because of an offset.
The target is great repeatability, always hitting the same spot, and great accuracy, meaning being on target.
There are different means, and depending on the purpose of your measurement, repeatability is more important. For instance, the user may just want to monitor a process or be in control of a process. However, if the user wants to cast a transfer or billing, then accuracy is key.
These different aspects are always linked together, and usually, the repeatability statement of the different measurement devices are better than the accuracy statements.
It is important to bear in mind that these accuracy statements are made under reference conditions, and these conditions are met at a calibration laboratory at the manufacturer.
A lot of effort is undertaken to ensure that technologies in labs are traceable to national standards and that they meet the reference conditions; this is what the performance is stated on.
Differences Between Technological Theory and Reality
Real-life can be very different from the theory behind the technologies. The installed accuracy can vary and differ from the referenced accuracy as a result of different installation conditions, different fluids and all kinds of other differences in respect to reference conditions. This is something that users always must keep in mind.
In addition to these differences to reference, differences in conditions could include a difference in fluid, fluid characteristics and viscosity. In this case, all these different substances have a different viscosity when compared to water, for example, and viscosity can differ at different temperatures.
This has the potential to affect the performance of flowmeters, as well as the characteristics of the fluid itself.
The next difference is the flow pattern, which involves how the flow is flowing through the pipe. Here is another practical example from everyday life: There are some differences seen if the tap is opened just halfway.
Just a flow coming out of the tap represents or comes in as a laminar flow. If the tap is opened further, it becomes a turbulent flow.
What is the difference between both flows? It can be clearly seen that with the laminar flow, the maximum flow velocity in the pipe is in the center. As you observe closer to the edge of the pipe, the flow velocity gets smaller. With the turbulent flow, a straight line is observed, and the flow velocity is the same at all different parts of the pipe.
For those readers who are familiar with Reynolds numbers, laminar flow is usually used for Reynolds numbers below 2100, and turbulent flow for Reynolds numbers above 3000.
Why are the flow pattern and the flow profile so important? For example, imagine an elbow in a pipe and that someone wants to install a flow meter somewhere downstream of that elbow. The user needs to be aware of the flow pattern because that can reveal how is the flow velocity distributed throughout the pipe.
In this example, before the elbow, flow is evenly distributed throughout the whole pipe. But when the flow comes to the elbow, there is a section with a very low flow velocity, possibly to the point where there is no flow. On the outside of the bend, there is very high velocity and a lot of flow.
Then, just after the elbow, the flow pattern is different from the area before the elbow. It takes quite a while until, finally, the flow pattern is evenly distributed again. This means that the pipe installation of different flow meters can influence flow measurement. This differs from technology to technology.
Defining Flowmeter Measurement Needs
The most important question that users need to ask themselves before selecting the right flowmeter technology is what their measurement needs are.
Their choice will depend on whether the purpose of their measurement is more control measurement, monitoring measurement, the measurement for custody transfer, or safety measurement.
Several detailed considerations also need to be included in flowmeter deliberation. Such questions include: What kind of fluid do I have? Do I have liquid, gas, steam or liquids with solids or any other aspects I should be aware of? What are the operating conditions? What are the temperatures? What are the flow rates? Do I need any display? Do I need any special communication needs?
There are a lot of details to be considered when selecting the right flow meter and the right flow technology. There must be a balance of all those considerations with the required accuracy or the performance a user wants to get out of the flow meter.
For instance, when a user wants to fill a truck or container, it is not only the flowmeter that defines the accuracy of the system but also the speed of the valve and how much fluid remains in the piping.
There are many different aspects, but they all come together in this system accuracy, and users need to think about repeatability, response time, installation conditions, and the pressure loss that they can accept.
Finally, the last consideration is how much budget is available for the flowmeter technologies as it is not just the price of the flow meter but also the installation cost.
Bernoulli’s Principle
Once users know their needs, the second step is to pick a principle. There are six main flowmeter principles, and the article will now describe in more detail what the pros and cons are of each principle.
With differential pressure, there is a pipe with flow going through it. The idea is that users put a constriction or a restriction into the pipe to accelerate the flow and to create a pressure drop.
Once there is a restriction in the pipe, the flow will flow with high velocity at that area than before it. Thus, users have just created a pressure drop that describes the difference in pressure before and after that restriction.
Users can measure that difference in pressure with a pressure transmitter, and that pressure loss, also known as the difference in pressure, is thus proportional to the square of the flow rate. This concept is called Bernoulli's equation and formulates the basic idea of this process.
There are many ways to restrict a flow diameter or a flow pipe. Users can either use venturi tubes, V-cones, flow nozzles, or wedge meters. The most used restrictor for diameter or pipe is an orifice plate. Users can simply put a plate into the stream and restrict or limit the diameter.
In principle, the restriction, or the pipe element of it, is called a primary device and then the pressure transmitter is called a secondary device. It is important to note that the diameter of that orifice needs to be untouched, especially with orifice plates.
The diameter needs to remain the same, and if users have a difference anywhere from the flow, they would have a misreading. They would also have a misreading or even a stop of measurement if they observe any clogging in the connection between the primary and the secondary device.
The mechanics of this principle already gives users a few pros and cons to consider, with benefits including the versatile use of the technology for all kinds of different applications such as being with liquids, gases, vapor or steam.
The technology can be used with high temperatures or low temperatures and in quite extreme conditions such as very high pressure and very high temperatures. With respect to the orifice plates, users would prefer to have the fluid clean to be able to prevent wear out.
Other devices like V-cone or wedge meters can measure dirty fluids as well. All these purposes can be met, and the advantages include use in extreme postconditions.
Because of a lot of experience using this technology, there is a lot of data available with this flow measurement principle that makes it approved for custody transfer. It is a very well-understood way of measuring flow.
Limitations surrounding this principle also exist. Because of the physics, users have a very small range of flow rate that they can use the meter for. It is, therefore, not a very wide area, and that means users must be very carefully sizing the meter to match their needs.
Additionally, the accuracy of this is not the best in the industry, and the meter is affected by density pressure and viscosity changes. The meter can be maintenance intensive, for instance, in the cases of the orifice plate, and it is possible that it wears out.
Electromagnetic Flowmeters
The next flow meter technology this article will introduce is electromagnetic flowmeters. The electromagnetic flowmeter system consists of a pipe again that has flow going through it. The idea is that established electromagnetic coils in the pipe create an electromagnetic field.
Due to the concept of Faraday's law, this magnetic field with a moving conductive liquid will induce a voltage at two different electrodes along the pipe, and that voltage can be measured to give users the resulting flow.
A very important precondition for that would be that there is a liner and that the magnetic field is established very well. Then the priority is the need to protect the meter from external disturbance. An alternative is that this whole system needs to be resistant enough against any kind of EMC disturbances from the outside world.
There are advantages and disadvantages to this technology. One advantage, for instance, is that users have no restriction whatsoever in the pipe, so there is no pressure drop and no obstruction to the flow, which benefits the measurement principles.
Therefore, it is vital that users have a conductive fluid for this. The limit is usually at five micro siemens. ABB has meters available that can measure with 0.5 micro siemens already, but some conductivity is always needed.
This is still a measurement principle that does not obstruct the flow, and it does not require much straight up or downstream distance. Thus, it is quite easy to install.
A liner acts to electrically insulate the fluid from the tube, and because of the different lining materials available, users can employ that principle with highly corrosive liquids and use them for very aggressive substances.
With no pressure drop, many purposes can be met. An advantage to this principle is that under conditions independent of any pressure, temperature or viscosity changes, users can even measure fluids with a lot of entrained solids. Another advantage is that the technology even comes with a huge variety of line sizes.
For example, sizes range from a 10th of an inch up to 96 inches, or even two millimeters up to 2500 millimeters. It is easy to install with no moving parts and experiences no pressure loss. The only requirement is that the system always needs a conductive liquid.
A major limitation is that there are other more accurate measurements out there. If a user has any deposits or coating affecting the electrodes, they might have electrical insulation stopping your measurement.
In that specific case, users need to think of specially designed electrodes or default to using another flow principle. Again, there are always both pros and cons with each principle.
The Coriolis Force
Next, this article will describe the Coriolis meter. What is the first principle of a Coriolis meter? With all Coriolis meters, there is the housing of a meter and flow tubes within the meter.
These flow tubes are made to oscillate, and they are vibrated by the meter. There is also an electronics aspect to the meter, and the electronics vibrate the tubes and the flow, or the fluid that is flowing through the tube.
All parts of the different tubes are completely in phase, and all of them are in parallel going outside or inside. This meter has a nice and clean oscillation.
As soon as users have flow going through the tube, the law of Coriolis, also known as the Coriolis force, comes into play. In other words, as soon as the meter has a moving mass in an oscillating system, the meter experiences a Coriolis force.
The Coriolis force has a different direction at the inlet of the meter compared to the outlet of the meter. Because of this, instead of the clean and nicely parallel swinging oscillating tubes, the technology undergoes a tumbling effect and then has tubes with a clear face shift from one end of the tube to the other.
This means the inlet and the outlet section of the tube are all nicely oscillating. However, they are slightly out of phase, meaning they are phase-shifted, and there is a little time gap between the inlet and the outlet. This is proportional to mass flow, and this is how users can measure mass flow using this technology.
An advantage of that principle is that users get mass flow directly but do not get volume flow or flow velocity. Additionally, with the frequency of the oscillation, users get density measurement in addition.
The technology works with all different fluid properties. Users do get some pressure drop because they must restrict the flow diameter. It works with liquids, gases, vapor, or steam.
There are different materials of construction available, and users get density measurements on top of all that.
A variety of different purposes and applications are possible, thus providing users the highest accuracy in the market, direct mass flow measurement, approved the forecasted transfer and very reliable, non-moving parts. This is also very low maintenance and not affected by low flow profile or installation difficulties.
The Coriolis meter does have its limitations as well: It is a pricey technology, users can observe a significant pressure drop simply because they restrict the diameter of the fluid, and there are limited line sizes available.
The Vortex Flowmeter
The next technology this article will describe is the vortex flowmeter. Vortex flow measurement involves a pipe with flow going through the pipe. A bluff buddy is introduced into the pipe, and the meter experiences all kinds of turbulences in the liquid or in the gas, which are occurring with a certain frequency.
If users measure the movement of these turbulences with a piezo sensor, they can measure the frequency of them. The frequency is proportional to the flow rate. This means that the higher the flow rate, the higher the frequency of turbulences which will, in turn, give users the flow rate.
One benefit of the vortex flowmeter is that it is a very robust technology because the bluff buddy protects the sensor. Thus, it can provide a very robust and very insensitive measurement. This meter, however, does depend on the flow pattern. If the flow velocity is unevenly distributed, and users have more flow rate in some areas and not in others, the meter will result in a big misreading.
In addition to the very robust measurement, the meter provides good accuracy, especially when compared to the differential pressure meter. It also has a low-pressure drop and a wide flow range of mobility.
People can use it with all kinds of liquids, gases, steam and vapor as it is available with a reasonable selection of sizes and no moving parts.
Limitations of the vortex flow include a lot of inlet and outlet sections required to have an evenly distributed flow pattern. With higher viscous fluids, users cannot use that principle. The flow range is better than with differential pressure, but still, there are some limitations.
The Swirl Meter
The swirl meter was developed to overcome challenges posed by the vortex flowmeter. The idea is to install a swirl at the entrance of the meter so that the swirl creates its own flow pattern.
Users create a swirl of their own and create their own flow pattern, and by doing so, they become independent from the flow pattern of the process pipe. With that swirl, users can measure again the frequency of these roles with the same piezo element that they had from the vortex meter.
The frequency is proportional to the flow rate, giving users the flow measurement.
With swirl meters, there are similar pros like previously stated with vortex when working with liquids, gases, steam. Swirl, however, boasts an even higher accuracy of 0.5% and yet still a low pressure drop, and there is no big disadvantage of very long straight inlet or outlet sections.
Pipe reductions are not needed, and installation costs are low. Limitations, again, come in the form of viscous fluids. These are all features of swirl metering.
Ultrasonic Flow
The next flow principle is ultrasonic flow. The idea behind ultrasonic flow measurement is that users have a couple of sensors, a few pairs of sensors that each across a pipe for each other. Once this is done, every sensor is transmitting a sound and receiving one.
The idea is to measure the speed of that sound, and the time it needs to go from one sensor to the other. If the sound is going with the flow, then the time is less, and the speed is higher. If the sound is going against the flow, the speed is lower, and the time is higher.
That means that transit time between those sensors is changing depending on the flow, and it is changing more so with higher flow rates and lesser with lower flow rates. This is providing the flow measurement, also known as the flow rate.
As several different pairs applied increases, users can compensate for possible flow pattern differences.
The principle behind this is quite nice and can easily be applied. Users can even have a clamp-on version of this meter, so there is no need to have the sensors in line with the pipe being in touch with the fluid.
It is important to note that users cannot simply clamp it on in an existing pipe but can retrofit the measurement to an existing piping system. This is quite a nice method currently applied for all different types of liquids.
Note that the transit time is usually made for clean liquids because any kind of solids can affect that measurement. For solid liquids or liquids with solids, there is a different method available.
The big advantage of this principle is that it can be used for small and large meter sizes and with very corrosive fluids. There is no pressure loss, and these flowmeters can be retrofitted in case of clamp on to provide robust measurement as well.
The technology chosen for flowmeter measurements influences the flow profile and the medium to low accuracy rates.
Variable Area Flowmeter
The last technology that this article will touch on is called variable area flowmeter. The system has a pipe with a very important flow going from bottom to top. Variable area is a vertical installation.
The system has a float or ball inside the pipe, and if the flow is going upwards, the ball or the float will also be pushed upwards. The more flow there will be, the more the float or ball will be pushed upwards. If users put a scale on the tube, they can see how much flow there is.
The float will always stay or remain at the point where the force from the flow pushing it upwards is in balance with the gravity force pulling it downwards. The different options to use this include a glass tube and a reference scale or an electromagnetic system following that float where users can get electrical output.
The great advantage of variable area flowmeters is that it is a very simple method that has been in use for over 100 years. It is also a very cost-effective and simple method, and if the user chooses the form with glass tubes, they can observe the liquid, which is another benefit.
There is also no need for any power supply at all if users do not want to have any electrical output. Another benefit is that it can be used with liquids and gases. It should be used with clean liquids.
However, users must be very careful in selecting the right size meter so that they do not run into a problem. This meter has a limited turn-on or limited flow span, and the whole functionality is limited, but if users have a lot of measurement points, this is a great choice.
Summary
The selection of a flowmeter technology always comes back to the needs of measurement for the intended applications.
To summarize, if users want to choose measurement technology, they should think of the purpose of their measurement in terms of transfer processes, monitoring processes, control of processes, and safety procedures.
They should also consider the performance required for installation: Is very high accuracy needed, or is accuracy not so important? Do they need robustness? Is a low maintenance solution required?
All these considerations come into play, and needs must be balanced with cost and economics. As well as initial cost, the cost of ownership, maintenance and installation should be taken into consideration.
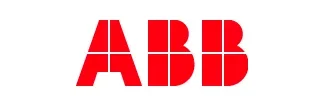
This information has been sourced, reviewed and adapted from materials provided by ABB Measurement & Analytics - Analytical Measurement Products.
For more information on this source, please visit ABB Measurement & Analytics - Analytical Measurement Products.