Technology advances have steadily been implemented to improve the performance of commercial atomic force microscopes (AFMs) since the release of the first commercial model about 30 years ago.
Now, the most recent advance in ambient-temperature AFMs is making them more portable, compact and user-friendly, which is enabled by Negative-Stiffness vibration isolation.
AFMs, or atomic force microscopes, are now one of the foremost tools for measuring and imaging cells and materials on the nanoscale.
The AFM is instrumental for imaging an array of applications by revealing sample details at the atomic level, with resolution on the order of fractions of a nanometer; some examples of its applications are manipulation of atoms and nano-sized structures on a variety of surfaces, data storage, lithography, and defining surface characterizations.
The AFM scans across a sample surface to image its topography and material properties by utilizing a sharp tip (probe) and a radius of curvature on the order of a few nanometers attached to the end of a tiny cantilever.
Forces between the surface and the tip lead to a deflection of the cantilever when the tip is brought into proximity of a sample surface. A laser beam is reflected from the top surface of the cantilever to a photo-sensitive detector to record this deflection.
Characteristics such as chemical, magnetic, electrostatic, mechanical and other forces can be precisely measured by AFM because of the resultant change of position of the cantilever/probe/tip.
An advantage that the AFM has when compared to other microscopy techniques is that these characteristics can be displayed in a three-dimensional surface profile of the sample (in the X, Y and Z axes).
Although AFM technology has advanced considerably, its benefits have not always been easily accessible for researchers requiring AFM adaptability, portability.
AFMs have also not been adequately accessible in nanotechnology student laboratories due to budget limitations on the number of AFMs at their disposal and lack of student skill in their operation.
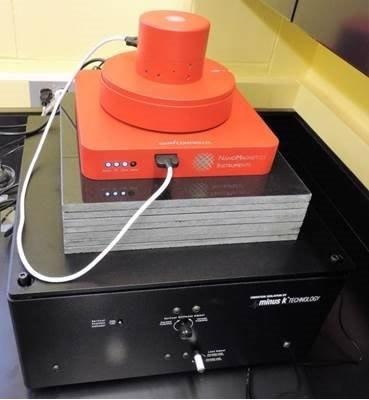
ezAFM+ supported by Negative-Stiffness vibration isolation. Image Credit: Minus K Technology
A More Portable, More User-Friendly AFM
A relatively new user-friendly, portable and compact ambient-temperature AFM has now mitigated these inhibitions. NanoMagnetics Instruments, a leading manufacturer of scanning probe microscopes for low-temperature applications, has developed the instrument.
The ezAFM+ atomic force microscope is a benchtop instrument designed for ease of transport, quick setup and short learning times.
Kent Schuyler, North American Manager for NanoMagnetics Instruments/NMI stated, “This AFM has excellent system performance, comparable with traditional AFM.”
The core of what NMI designs and builds are scanning probe microscopes/SPMs for low-temperature applications. We have engineered this legacy technology into an easier to use ambient-temperature, more portable AFM than what was currently available on the market. This new instrument is the ezAFM+.
Kent Schuyler, North American Manager, NanoMagnetics Instruments/NMI
The ezAFM+ instrument operates in full electrical and mechanical SPM modes such as DMT, Kelvin probe, and tapping. STM requires highly effective mechanical isolation and is also a plug-and-play option.
This new AFM has 100 um Z that is somewhat adaptable to the application, as well as exceptional scan range on the order of 150 um in X&Y. Instead of more traditional piezo-based motors the scanner utilizes voice coil motors (VCM).
Tip-limited resolution is sustained while voice coils still enable exceptional range. Well integrated optics provides extremely functional electronic focus and better than 2 µm resolution.
Negative-Stiffness Vibration Isolation
Any vibrations from the environment can impact AFM systems. As resolutions continue to bridge from micro to nano, the need for more precise vibration isolation with atomic force microscopy becomes more critical.
An absolutely stable surface must be established for the instrument when measuring a very few nanometers or angstroms of displacement. Horizontal and/or vertical noise will be caused by any vibration coupled into the mechanical structure of the instrument, bringing about a reduction in the ability to measure with the highest resolution.
AFMs are most sensitive on the vertical axis, but can also be quite sensitive to vibrations in the X and Y axes.
Schuyler noted, “During development of the ezAFM+ we considered a number of options for vibration isolation.”
Weighted masses hung from bungee cords, air tables, and active vibration. We have primarily decided on Negative-Stiffness vibration isolation. Consequently, this portable new AFM comes equipped with a state-of-the-art vibration isolation platform which is also portable and easy to operate.
Kent Schuyler, North American Manager, NanoMagnetics Instruments/NMI
Negative-Stiffness isolators developed and patented by Minus K Technology provide a unique capability for AFM research. The isolators use a completely mechanical, passive concept in vibration isolation that does not require electricity or air.
There are no pumps, motors, or electronics. They achieve a high level of isolation in multiple directions while operating completely in a passive mechanical mode.
Dr. David Platus, inventor of Negative-Stiffness isolators, and President and Founder of Minus K Technology explained, “In Negative-Stiffness vibration isolation, vertical-motion isolation is provided by a stiff spring that supports a weight load, combined with a Negative-Stiffness mechanism. The net vertical stiffness is made very low without affecting the static load-supporting capability of the spring. Beam-columns connected in series with the vertical-motion isolator provide horizontal-motion isolation. A beam-column behaves as a spring combined with a Negative-Stiffness mechanism. The result is a compact passive isolator capable of very low vertical and horizontal natural frequencies and very high internal structural frequencies.”
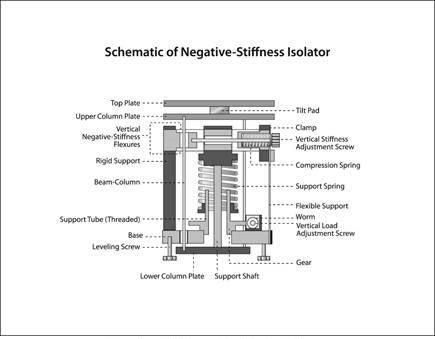
Negative-Stiffness vibration isolator. Image Credit: Minus K Technology
Vibration Transmissibility
Dr. Platus added, “Negative-Stiffness isolators deliver very high performance, as measured by a transmissibility curve.”
“Vibration transmissibility is a measure of the vibrations that are transmitted through the isolator relative to the input vibrations. Every isolator will amplify at its resonant frequency, and then start isolating. Negative-Stiffness isolators resonate at 0.5 Hz – and in some cases at lower frequencies both vertically and horizontally. At this frequency there is almost no energy present. It would be very unusual to find a significant vibration at 0.5 Hz. Vibrations with frequencies above 0.7 Hz⃰ are rapidly attenuated with increases in frequency. When adjusted to 0.5 Hz, Negative-Stiffness isolators achieve approximately 93 percent isolation efficiency at 2 Hz; 99 percent at 5 Hz; and 99.7 percent at 10 Hz.” Dr. Platus continued.
Natural frequencies of 1.5 Hz horizontal and 0.5 Hz vertically are provided by some low-height Negative-Stiffness isolators. Negative-Stiffness isolators are flexible in that they can custom tailor higher resonant frequencies when lower frequencies are not required.
(*Note that isolation begins at 0.7 Hz and improves with an increase in the vibration frequency for an isolation system with a 0.5 Hz natural frequency. System performance is more commonly described using the natural frequency.)
Location Flexibility
The ezAFM+ and its vibration isolation platform have both been designed for adaptability. Any typical lab table can be used for Negative-Stiffness to achieve excellent vibration isolation.
Negative-Stiffness vibration isolation enables sensitive instruments, like ezAFM+, to be located wherever a laboratory or production facility needs to be set up because of its very high isolation efficiencies with low-hertz vibrations in both vertical and horizontal vectors; this is the same no matter if the set up is on a building’s vibration-compromised sixth floor or in a basement.
Compressed air or electricity are not required for Negative-Stiffness isolators. There is nothing to wear out, so there is no maintenance and no chambers, pumps, or motors. The machines operate solely in a passive mechanical mode.
The system is easier to set-up and maintain and simpler to transport because equipment can be isolated from vibrations without having to deal with electricity or compressed air. Negative-Stiffness vibration isolation makes a complimentary match with ezAFM+ when considering portability.
Since its release, ezAFM+ has become the practical low-dimensional materials characterization system in the United States. And the Negative-Stiffness isolator is a standard, critical component of the system.
Kent Schuyler, North American Manager, NanoMagnetics Instruments/NMI
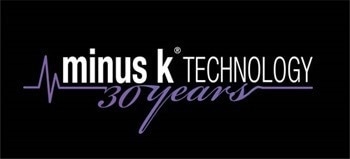
This information has been sourced, reviewed, and adapted from materials provided by Minus K Technology.
For more information on this source, please visit Minus K Technology.