With the application of the infrared camera of the optris PI Series, the Gubesch Group optimizes the production of automotive exterior parts. Consistent temperature profiles throughout the thermoforming process offer high-quality assurance and boost customer loyalty.
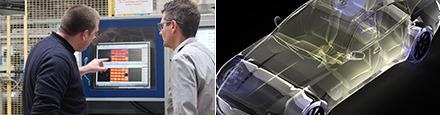
Image Credit: Optris GmbH
The composite fiber sheets necessary for the deep-drawing process have a thickness of 2.3 to 3.5 mm and are reinforced with glass fibers. Before forming the plastic sheets into perfect panel parts, they must be heated. This is conducted using low- and high-level heaters in a radiant field within the thermoforming machine.
Once heating is complete, the composite fiber sheets are cooled after being pressed into the mold of a panel part in the machine. This significantly reduces the handling time between heating and forming.
In addition to the forming process, simultaneous forming of functional groups (e.g. air inlet nozzles) is carried out. In another step, a laser cuts the panel part which is then shaped to its final form before being transferred to the end-customer for assembly.
Process Optimization is the Primary Objective
The Gubesch Group’s main objective is to optimize processes that guarantee stable production, optimum cycle time and limited production defects.
The sporadic burning of the panel parts appeared throughout the development phase due to the temperature settings being too high or the formation of folds due to an exceedingly low-temperature profile.
The greatest challenge during this process was constantly monitoring the temperature for setting and regulating the radiant heaters.

Our partner ist is active in the field of innovative thermoforming and injection molding technologies as a Full-Service-Provider. Image Credit: Optris GmbH
The initial application of a pyrometer on each side proved to be insufficient since the temperatures vary too much across the complete cut material section. Fitting multiple pyrometers in a line was also considered. But the achievable resolution here would also be too low.
Dr. Ing. Thomas Müller-Lenhardt, Head of R&D, Gubesch Group
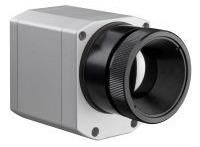
The IR camera optris PI 640 is flexible in use. Image Credit: Optris GmbH
The optris PI infrared camera offers the ideal solution. Its wide-area temperature measurement covers most of the composite fiber sheet, enabling both individual values, such as cold- and hot-spots, as well as average values and temperature profiles across the surface to be displayed.
One optris PI thermal imaging camera with a 64° wide-angle lens is placed in each of the top- and bottom heating sections of the starter field. Due to the camera’s proximity to the heating system, the front side encounters ambient temperatures of up to 315 °C – too hot for the optris PI without added protection.
Installing the thermal imaging cameras in an additional water-cooled cooling housing, in addition to fitting a decoupled plate in front of each housing (reflection of thermal radiation), proved to be an adequate solution.
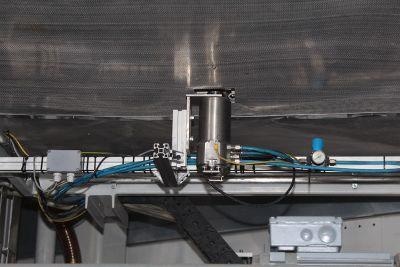
The CoolingJacket ensures a reliable use of the infrared camera. Image Credit: Optris GmbH
This sustained a constant ambient temperature of 35 to 40 °C for the thermal imaging cameras. To guarantee that the maximum ambient temperature of the optris PI of 50 °C is not exceeded, the internal camera temperature is checked using optris PIX Connect software.
Data Evaluation and Recommended Actions from Software Programmed In-House
Temperature evaluation is performed using the optris PIX Connect software. For the user, it offers detailed IR camera software, which automatically analyses and documents the temperatures and controls processes.
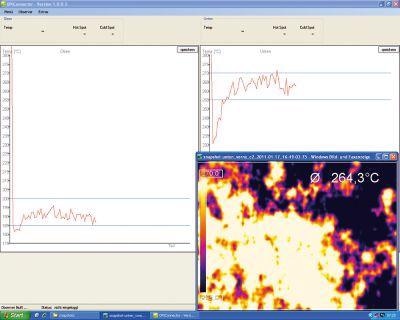
Thes software documents ans analyses the temperature data. Image Credit: Optris GmbH
The software facilitates video and snapshot recordings at up to 80 Hz and features a significant degree of customization for customer-specific modifications.
At the Gubesch Group, the data is sent to a proprietary user interface via a COM port interface. The software, developed by novo.design (Neustadt/Aisch), seeks out new snapshots from the two cameras at pre-determined time intervals.
Concurrently, the temperature values from both cameras are read-out and buffered. The most crucial information is displayed in a temperature diagram. A pre-defined upper and lower temperature limit allows for prompt alarms if the temperature gets too high or too low.
To make working on the machine easier, the alarm appears in a pop-up window together with an associated recommended action for the responsible plant operator. This means we can ensure the correct reaction at the plant.
Dr. Ing. Thomas Müller-Lenhardt, Head of R&D, Gubesch Group
The cameras are interconnected via a USB interface to the computer. An additional interface included on the camera is the Process Interface (PIF), enabling external trigger signals to be sent to the camera.
The trigger interface permits automatic snapshots to be triggered using a voltage signal. The signal for this is received via the machine control system. The most recent snapshots of the individual plastic sheets are clearly displayed in a display history and are saved as part of the documentation process.
Optimum Cycle Times, Reduced Scrap Volume
One significant advantage when applying the optris PI thermal imaging camera at the Gubesch Group is production optimization through dependable temperature monitoring for setting and regulating the radiant heaters.
The application of the PI thermal imaging cameras enables the realization of optimum cycle times of 90 seconds at the maximum heating power. This has maximized both yield and productivity.
“With a constant temperature profile, the scrap in production was substantially reduced,” explains Thomas Müller-Lenhardt, delighted with the improvement.
However, for the Gubesch Group, the primary advantage is high-quality assurance. The optimum heating temperature regulation allows the group to meet customer’s demand for the highest quality, leading to better customer loyalty and increases order volume.
The Reliability of Optris Products is Convincing
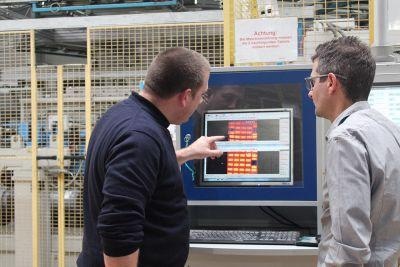
Technical support ensures the success. Image Credit: Optris GmbH
Choosing the optris PI was an obvious step for the Gubesch Group. Since pyrometers for folding units in bending processes were already well-proven in the business, reliable Optris devices were also selected for the new series production.
Andreas Theilacker, Regional Sales Manager, Optris
“The wide range of IR measurement devices, accessories and software options proved to be an advantage,” he continues.
Not only does Optris deliver thermal imaging camera solutions for industrial applications (IP 67, for example, also with industrial plugs), but also crucial components such as cooling housings, as well simple plant integration via the USB interface.
When selecting the optris PI thermal imaging camera for the application, additional factors were the comprehensive, license-free camera software for thermal image analysis and the free-to-use software interfaces (COM port, DLL) to transmit appropriate data to the user software.
Advantages at a Glance
- Attainment of the highest possible utilization of the plant and production volume
- Cycle time reductions
- Display of the temperature profile across the plastic sheet
- Ensuring high quality for customer loyalty and satisfaction
- Production defects minimized
- Regulation of the radiant heater temperatures is simple
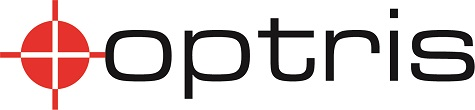
This information has been sourced, reviewed and adapted from materials provided by Optris GmbH.
For more information on this source, please visit Optris GmbH.