Sponsored by Mo-SciNov 22 2021
Spray drying is the name given to the rapid drying process of creating dry powders from liquid slurry. The liquid is typically sprayed with hot gas to accelerate the drying stage, which renders it highly time-efficient.
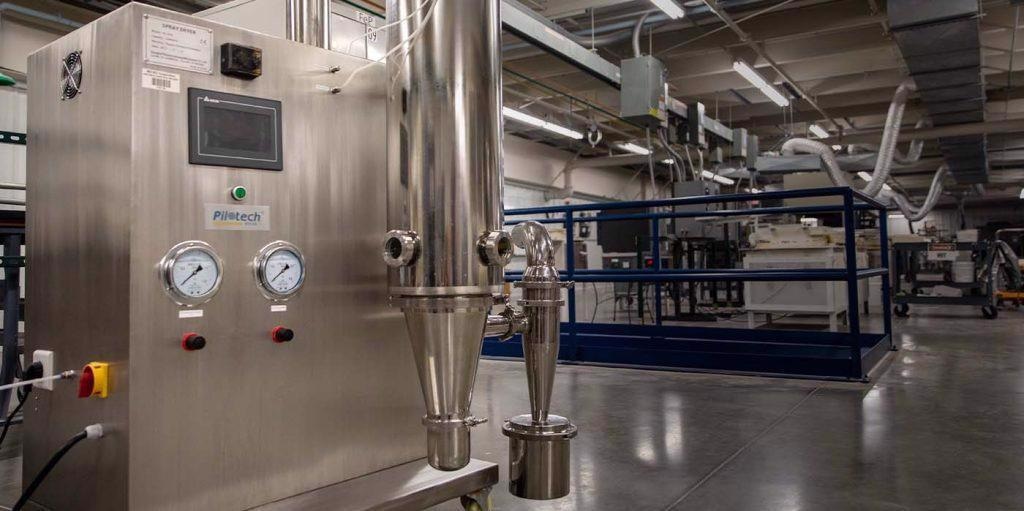
Image Credit: Mo-Sci Corp.
This process of spray drying is used for the production of powders across many industries, from a diverse range of starting materials, which can include foods, biological matter, and glass powders.1,2
In addition to simply producing dust-free powders, spray drying technologies can be used as part of the particle manufacturing process.
Producing granular powders via spray-drying methods may have beneficial effects for high-performance materials such as ceramics in terms of the physical properties of the final material.2
In part, this is because spray drying allows for excellent selectivity for particle sizes, which can then be controlled by varying conditions. These conditions include pressure, temperature, and nozzle dimensions.
There are several steps involved in the spray drying process. The first of these is that the sample is atomized to form a liquid droplet which contains within it the chemical species of interest.
Secondly, the solvent is rapidly evaporated, typically with heated air, which is done to remove the excess solvent and to form a particle. This can be a composite particle if multiple chemical species are present.
From air-shear nozzles to spinning disks, there are numerous atomizer designs, in addition to ultrasonic nebulizers, which are customizable to the process of interest.
Spray Drying Applications
Spray drying has various applications, which include the production of dried milk powders, the manufacture of pharmaceuticals, and the creation of ceramics for dentistry.
Glass powder production is also ideally suited to spray drying. This is because it has rapid drying capabilities as well as the ability to produce very spherical particles of narrow size distributions.
Though there are alternative methods for the production of glass powder - which include, for instance, an entire family of glass milling techniques such as ball milling or hammer milling – such techniques do not necessarily offer the same precise control, especially when it comes to the production of particulates with dimensions on the order of microns.
The level of control offered by spray drying over the physical properties of the particles is highly desirable for biomedical applications.
There are necessary stringent checks in this area to do with quality and reproducibility, and at both microscopic and macroscopic levels, the products must be reliable.
A variety of chemical solvents are compatible with spray drying, including aqueous solutions, which renders it a flexible and diverse technique to be used on a range of different systems.
It is largely thanks to its ability to create small particles that spray drying has become a popular choice for glass powder production. Given that the particle size is proportional to the concentration of the chemical feedstock, it can therefore be controlled to limit the number of large particles that are formed.
Separation based on size is also made easier thanks to the different behavior of particles of different sizes.
Spray drying can also be used to create aggregates, in addition to being excellent at selecting given particles sizes and providing homogenous size distributions. For instance, spray drying has been used to aggregate 5 µm particles into loosely agglomerated particles of ~ 25 µm diameter for the creation of dental materials.5
Changing the powder to liquid ratio in this application affected the rate of fluoride release. This, in turn, helped to create material for dental implants, which would assist in the prevention of further cavities.
There are a number of clear and obvious advantages of homogenous size distributions that can also be seen in the making of sealing glasses. Used for bonding and setting components, sealing glasses can be supplied in a range of different forms, such as tapes, pastes, and preforms.
Making preform involves the process of pressing the glass powder in a mold and subsequently firing it. There are very stringent requirements on the properties of the glass powder used in this type of manufacture, including good flow without clumping – an objective that spray drying can help achieve.
Organic binders are also often added to the liquid slurry before spraying as part of making preform glasses through spray drying. Organic binders such as this help the particles hold together stronger and form agglomerates, improving the final preform's adhesive effects. This ensures that they flow nicely into molds and can be set in the correct shape.
Glass Processing Services from Mo-Sci
Mo-Sci offers a range of specialty glass powders from unique formulations and is one of few suppliers to do so.6 The class VI spacer grade glass microspheres produced by Mo-Sci are designed to offer highly accurate spacing and are available in size ranges from 38 µm ± 7% to 850 µm ± 5%.
Mo-Sci additionally offers a widespread range of bioactive glasses along with other biomaterials, including a range of spray-dried powders.
Each of these materials is produced in an environmentally-controlled space with very high purity ceramic or precious metal equipment to maintain the rigorous safety standards required for biomedical devices and avoid any risk of contamination.
Contact Mo-Sci today to find out how their custom processing capabilities could boost the performance of your glass powder range using advanced manufacturing techniques.
References
- Shishir, M. R. I., & Chen, W. (2017). Trends of spray drying: A critical review on drying of fruit and vegetable juices. Trends in Food Science and Technology, 65, 49–67. https://doi.org/10.1016/j.tifs.2017.05.006
- Arpagaus, C., Collenberg, A., & Rütti, D. (2019). Laboratory spray drying of materials for batteries, lasers, and bioceramics. Drying Technology, 37(4), 426–434. https://doi.org/10.1080/07373937.2017.1410487
- Cattell, M. J., Patzig, C., Bissasu, S., Tsoutsos, A., & Karpukhina, N. (2020). Nucleation efficacy and flexural strength of novel leucite glass-ceramics. Dental Materials, 36(5), 592–602. https://doi.org/10.1016/j.dental.2020.03.017
- Nandiyanto, A. B. D., & Okuyama, K. (2011). Progress in developing spray-drying methods for the production of controlled morphology particles: From the nanometer to submicrometer size ranges. Advanced Powder Technology, 22(1), 1–19. https://doi.org/10.1016/j.apt.2010.09.011
- Panpisut, P., Monmaturapoj, N., Srion, A., Angkananuwat, C., Krajangta, N., & Panthumvanit, P. (2020). The effect of powder to liquid ratio on physical properties and fluoride release of glass ionomer cements containing pre-reacted spherical glass fillers. Dental Materials Journal, 39(4), 563–570. https://doi.org/10.4012/dmj.2019-097
- Mo-Sci (2021) Glass Milling, https://mo-sci.com/glass-milling-equipment-techniques/, accessed 10th September 2021
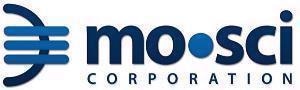
This information has been sourced, reviewed, and adapted from materials provided by Mo-Sci Corp.
For more information on this source, please visit Mo-Sci Corp.