Designing and engineering any automobile is an extensive process: From the engine to the power train and axles and wheels to fuel systems, restraints, steering and safety systems. Moreover, interior design and infotainment are key factors scrutinized for both functionality and aesthetics, most notably by the driver and passengers.
Unfortunately, one frequent grievance that crops up is related to water ingress into interior headliners, usually via sealing gaps surrounding center high-mounted stop lights (CHMSLs).
Anyone who purchases a new car will be extremely disappointed to find out that their new expensive purchase leaks and that their vehicle’s headliner is stained, wrinkled and a hotbed for mildew and other mold species.
Perhaps the greatest reason for the occurrence of this phenomenon is the gulf between OEM material specifications and the performance requirements in the application.
Design engineers may call for the use of sealing foams that seem to offer appropriate functionality on paper, based on lab sample validation testing. However, such materials can later present issues during part validation, or post-production, as a result of real-life environmental conditions and specific part geometry.
Typically, the overriding consideration and determining factor is cost. The materials generally specified for lamp sealing, such as EPDM foam, can deliver advanced cost savings. While superficially, this seems to be advantageous, a closer look, however, reveals a complex picture.
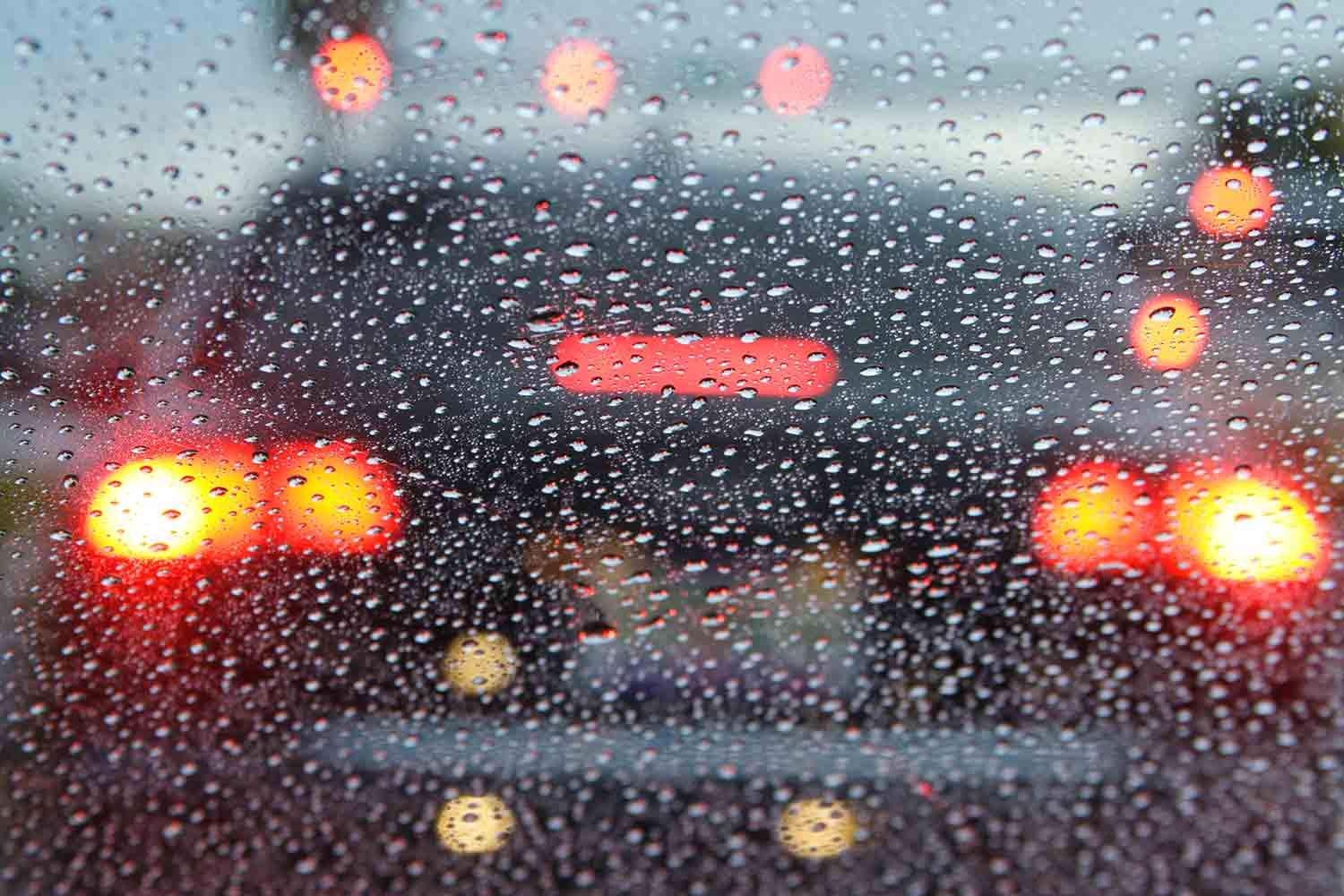
Figure 1. Moisture seeping into vehicle headliners via the center, high-mounted brake light is a common – but entirely preventable – complaint. Image Credit: Felix Mizioznikov/Shutterstock.com
End users tend to report leakage within just a few months of purchasing a new vehicle; for them, the issue is not just an annoyance. They are burdened with repair costs adding to the total expense of ownership, which has an impact on brand perception.
In turn, this has a negative impact on customer loyalty and reverberates backward in the supply chain, negatively impacting dealerships and manufacturers.
While one such response can include publishing repair instructions, this also opens the door to warranty claims and potential product recalls. OEMs can also choose to make in-situ adjustments to assembly lines to help improve part production, but this is likely to be laborious and costly.
By approaching such a challenge as a design engineering opportunity and specifying premium gasket and sealing materials, including silicone foam tapes, engineers can guarantee the long-term viability of rear lamp assemblies. This forward-thinking approach helps ensure product reliability and longevity, protect brand perception, and limit the chances for warranty claims. As a result, any initial costs are recouped in the long run.
Automotive Lighting and Considerations for Gasket Materials
The housing of rear-mounted lamps typically incorporates plastics such as ABS or polycarbonate-ABS (PC-ABS), making substrate compatibility a challenge. As a result, determining an appropriate type of sealing material for rear-mounted lamps requires a number of unique considerations.
For example, it is not possible to use PVC sealing foams due to the heightened risk of environmental stress cracking of the housing.
CHMSLs, which were once located inside rear windows are now placed on the outside roofs or inside spoilers. Since they are directly sealed to the vehicle, this is especially challenging and requires the performance of the sealing material to be 100% effective over the complete lifespan of the vehicle.
The conventional solution, EPDM foam, is beneficial due to its low cost. However, this solution also has numerous drawbacks.
One downside is its largely open-cell structure, which means seals typically require high levels of compression - in the range of 50% or more - to block water ingress effectively, specifically for larger lamps and more complex gasket arrangements requiring sealing along ribs.
In addition, the EPDM is usually characterized by a high compression set and prolonged compression, tending to result in permanent deformation, causing further challenges.
Consequently, the seal can be compromised with any movement in the part. Moreover, serviceability is restricted due to this phenomenon. If repair requires parts to be taken out, the seal will be less effective when reinserted.
Another potential issue of concern is of corrosion occurring when in contact with LEDs or electronics. This is relevant to sulfur-cured EPDM, which makes it unsuitable for lamp sealing. While peroxide cured EPDM is an acceptable alternative, it is typically costlier, stiffer and harder to assemble to get the compression level required.
Polyurethane (PUR) foam offers a good improvement over EPDM, providing a lower compression set granting greater resiliency. Because PUR foams are primarily microcellular, a high compression level is still necessary to create an effective seal. If the seal becomes exposed to the elements, poor UV stability can compromise it.
Placing a premium on both conformability and durability, silicone foams are the opposite end of the spectrum- a superior solution. With a low force-to-compress (FTC) to compression-force-deflection (CFD) ratio, they have evident flexibility, which facilitates improved sealing along a rib.
Simultaneously, closed-cell configurations offer effective water seal at just 30% compression UV and ozone resistant, sulfer-free and non-corrosive, with the ability to withstand a wide temperature range, silicone foam is well-suited for a variety of automotive applications for which product longevity is a necessity.
The key is for design engineers to avoid being bogged down by budgetary constraints predicated by short-reaching analysis. When looking at the bigger picture, the value of using top-shelf materials such as silicone is better for long-term cost savings and, ultimately, reputation amongst consumers.
Norseal Silicone Foam
The line of Norseal® Silicone foams offered by Saint-Gobain is an evident solution for tackling the challenge of rear-mounted lamp sealing. The medium density, closed-cell F-20 silicone foam rubber acts as the substrate for its 520HGF tape.
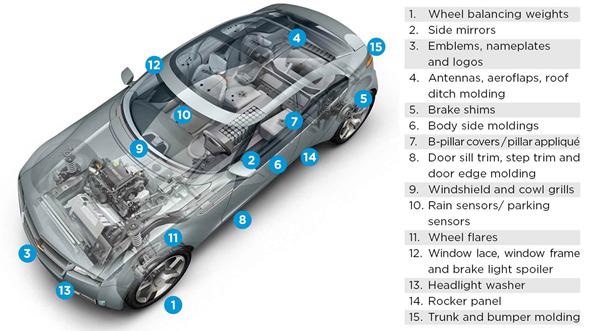
Figure 2. Over 60 years serving the sealing and bonding needs of the automotive world. Image Credit: Saint-Gobain Tape Solutions
Due to its resistance to environmental conditions, including air, dust, light, moisture, etc., Norseal F-20 is well-known throughout a number of different industries, including multiple transportation sectors.
Norseal 520HGF, displayed in Figure 3, uses a film-supported acrylic pressure-sensitive adhesive (PSA) to provide the benefits of F-20 silicone foam in an easy-to-apply form.
The formation of 520HGF is a sulfur-free formulation and eradicates corrosivity around electronics. While its low absorption quality provides long-lasting water sealing, it is also resistant to chemicals and cleaners and is flame-retardant.
Another major benefit of Norseal silicone foam is that it outperforms other elastometer tapes in areas such as longevity, weatherability and electrical resistivity. It is also well-suited for use in extreme temperature applications.
520HGF tapes come in a wide range of thicknesses and form factors, including strips, die-cuts, O-rings and other custom shapes and sizes.
Perhaps most crucially for rear-mounted lamps, the low compression set of both F-20 and 520HGF products is expressed in the delivery of more reliable seals with greater serviceability:
Norseal F-20 Data
- Compression deflection: 10 psi / 70 kPa (ASTM D1056)
- Compression set: <5% (ASTM D1056 “D”; compressed 50% for 22 hours at 212 °F/100 °C)
- Description: Medium-density, closed-cell silicone foam rubber product
- Density: 20 lb/ft3 / 320 kg/m3 (ASTM D3574)
- Ozone effect rating: No cracking (ATSM D1171-99 [2007], Method A)
- Temperature range: -60 to 100 °F/-51 to 204 °C
- UV resistance: No degradation (SAE J1960)
- Water absorption: <1% (ASTM D471/D1056)
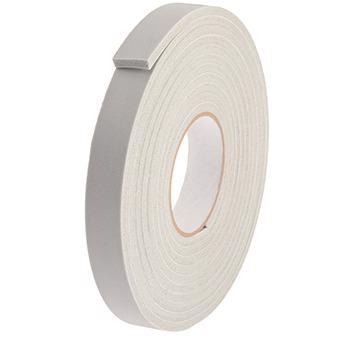
Figure 3. Norseal 520HGF SNS Tape offers flame-retardant, closed cell F-20 Silicone Foam as the base material, along with a film-supported acrylic pressure-sensitive adhesive. Image Credit: Saint-Gobain Tape Solutions
Norseal 520HGF Data
- Description: Pressure-sensitive adhesive silicone SNS foam tape
- Adhesion to steel: 30 oz/in / 335 gm/cm (test method: ASTM D1000)
Note: These are the standard values and should not be used for specification purposes.
One other fact design engineers may like to consider is that the Norseal Foam product range is utlized in many other automotive applications. These include door lock and quarterlight window vent sealing, HVAC and cow grill gasketing for climate control and vibration dampening solutions for dashboards and interior trims.
Additionally, Norseal Silicone Products facilitate the ongoing development of electric vehicles (EVs), with sealants to counteract external atmosphere intrusion, compression pads to allow for expansion and contraction in battery cell stacks and thermal interface materials to isolate cells when thermal runaway events occur.
Silicone Foams: Forward-Thinking Solutions to Alleviate Customer Issues
Silicone foams are generally reserved for applications requiring very low compression sets or resistance to extreme temperatures due to their cost. Designating their use to address rear-lamp moisture leakage may seem excessive.
As detailed above, however, there is a bigger picture to consider. By utilizing higher quality materials like Silicone foams, manufacturers can remain a few steps ahead and alleviate a common customer complaint, often more insidious than anticipated.
Saint-Gobain Tape Solutions is well-positioned as a partner to support design engineers and help them realize the potential for success. With over 60 years of experience serving the sealing and bonding needs of the automotive world, Saint-Gobain offers an extensive and well-calibrated approach to problems the industry faces.
In addition, customers of Saint-Gobain are not restricted to only working with the existing inventory, as is generally the case when dealing with tape suppliers; instead, customers have access to a team of engineers who design and develop the adhesives and can help offer custom solutions for any application.
Contact Saint-Gobain today to discuss how its silicone options can serve your application needs.
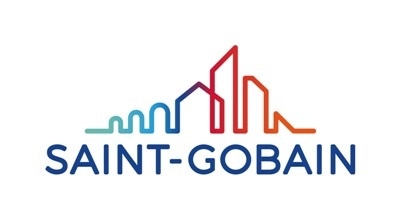
This information has been sourced, reviewed and adapted from materials provided by Saint-Gobain Tape Solutions.
For more information on this source, please visit Saint-Gobain Tape Solutions.