Interview conducted by Olivia FrostAug 12 2022
AZoM speaks with Mike Georgalis, North American Sales Manager for TMC. TMC is a world leader in vibration control for equipment used in semiconductor, photonics, life science, metrology, and materials analysis.
TMC's origins go back to 1969 as Backer-Loring Corporation. TMC was officially founded In 1979 as a spin off from Backer-Loring. TMC was purchased by AMETEK in 2011. Having the backing of a $6B corporation really helps us to provide excellent support and services worldwide. There are about 140 employees at TMC, supporting a variety of industries such as, electron microscopy, semiconductor, photonics, metrology, and life sciences.
In this interview, vibration control for original equipment manufacturers (OEMs) of Industrial equipment and scientific instruments is discussed, with a focus on issues affecting instruments like Payload Vibration caused by moving stages, the pros and cons of various types of Isolators, and when you should stack vibration isolation systems and what issues to look out for.
What are three different types of general scales to which vibration control applies?
NIST coined three phases: normal precision, precision, and ultra-precision. An example of normal precision would be an automobile component.
A car built in the 1970s required a lot more maintenance than a car built nowadays. The reason is the tolerances in the engine and in the car have gotten tighter and better over time – the pistons fit more tightly and run more smoothly inside their cylinders, and crankshafts have less friction, space, and rattling. This is due to the tolerance getting tighter and more precise.
At the precision level, integrated circuits (ICs) are a good example. Gordon Moore coined this theory in the semiconductor industry that the number of transistors per unit area will roughly double every two to three years. There is this exponential expansion of how many transistors can fit on a unit surface area on a Silicon chip.
That is a reason that drives technology such as our consumer electronics. In the 90s, you had a cell phone the size of a brick and a CD player, your own personal planner, a beeper, and other items. Advancements in semiconductor technology now enable all of those functions to fit into your cell phone.
Ultra-precision is a general term coined by a study done by Dennis Swyt at NIST. This encompasses applications like cryo-electron microscopy, various transmission electron microscopy, single-molecule biophysics and other applications looking down to the atomic and even angstrom scale in biological molecules. This is interesting in life science because this is how we were able to image the COVID virus so quickly.
What are some of the instruments that perform these operations and are sensitive to vibration?
Scanning Electron Microscopes (SEMs), Transmission Electron Microscopes (TEMs), and Focused Ion Beam Systems (FIBs) are used in a variety of applications such as semiconductor failure analysis, inspection, defect review, wafer inspection and manufacturing. They are also used in life science and for materials analysis. We have gene sequencers and NMR in the life science field. The photonics field uses very large petawatt lasers, interferometry, holography, quantum computing and virtual reality-type applications.
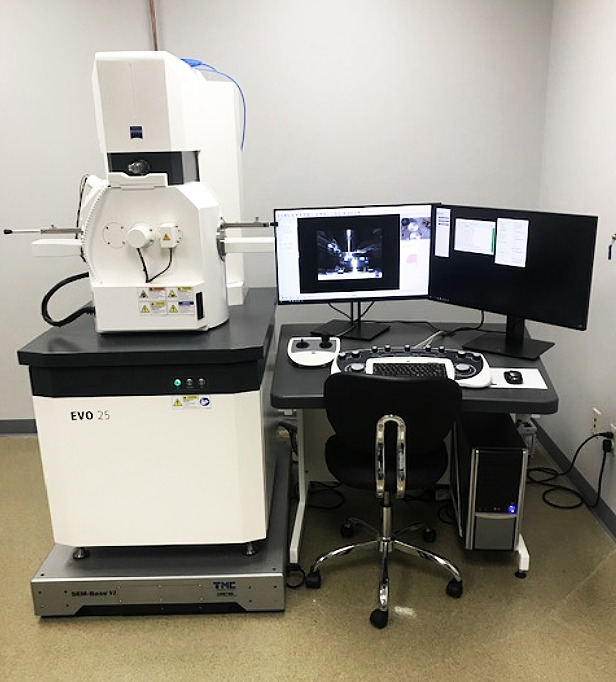
Image Credit: TMC Vibration Control
Some advanced instruments, such as those with moving stages, require their own vibration control because the vibration is internally generated by noise generated by the instrument itself.
What factors contribute to instrument vibration?
Payload refers to the instrument itself and anything that might sit on top of a platform or on top of an isolation system.
From the ground, there is floor vibration that comes from things like trains, buses, automobiles, people walking, buildings swaying in the wind, and seismic activity.
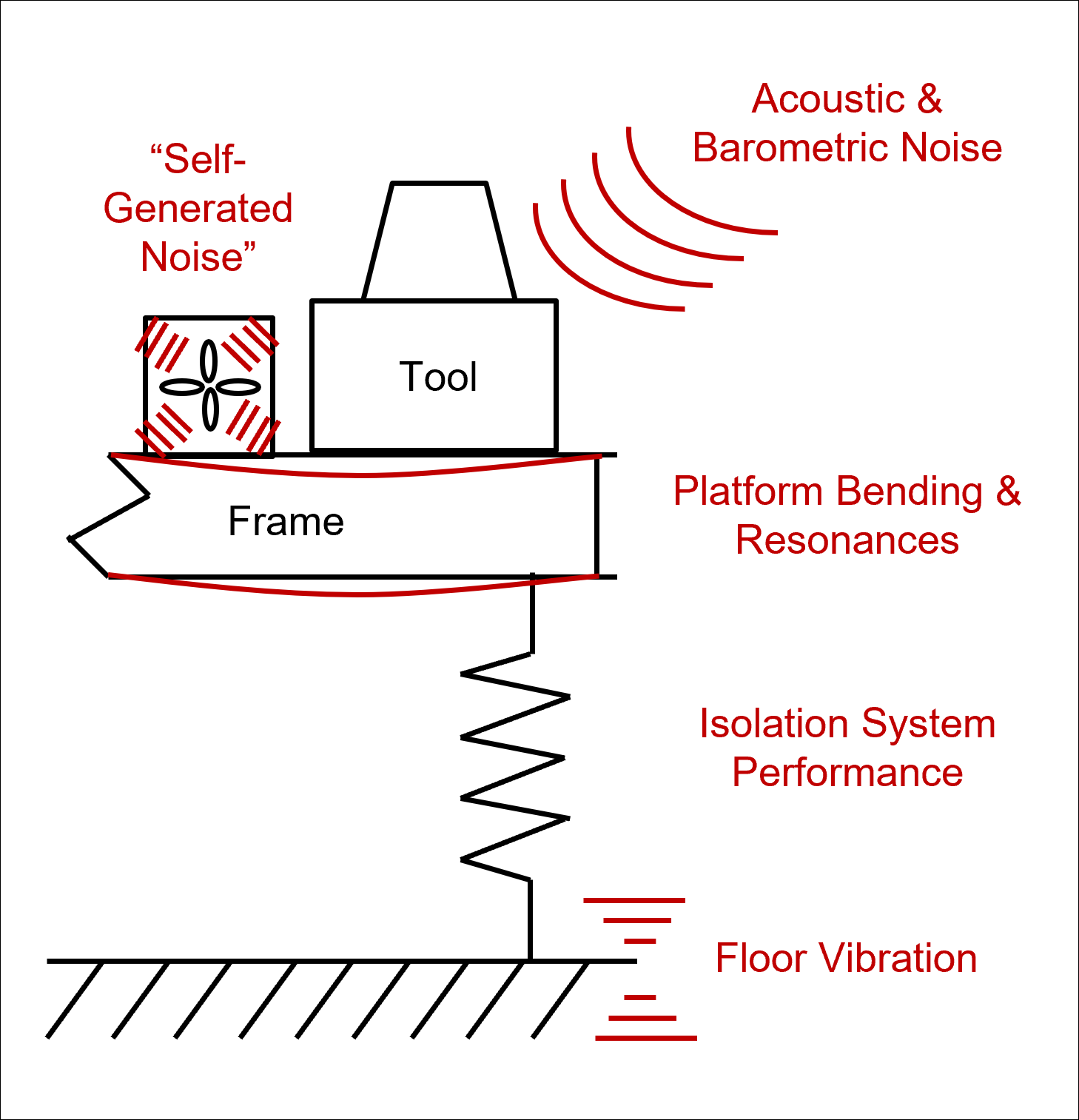
Image Credit: TMC Vibration Control
Then, there is acoustic and barometric noise and pressure waves from people talking, various instruments, opening and closing doors, an HVAC system kicking on and off, or an elevator going up and down a shaft displacing the air in the elevator shaft.
Another contributor to payload vibration is the isolation system itself. An isolation system inside a machine can help reduce some frequencies, but it can also hurt the problem by amplifying some frequencies at its natural resonance. Then, there is the noise generated from the tool itself from moving parts such as stages, motors, robots and other moving parts.
What are different types of isolators that help cancel vibrations?
The simplest isolator that exists is a spring. It is basically a filter that performs a transfer function. A transfer function is basically a ratio of the payload motion to the floor motion. Most passive isolators are mass spring damping systems.
Many of the ones used in industry and that are commercially available are pneumatic isolators which are sealed air chambers in which high-pressure air is put into and floats a piston upon which the instrument is placed. These are good isolators, and for high frequencies, they do a great job. In terms of weaknesses, they are generally soft and shake and move easily.
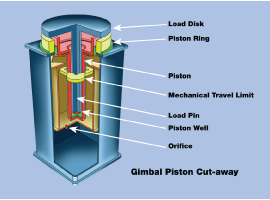
Image Credit: TMC Vibration Control
Air isolators are the industry standard because and provide good high frequency isolation but they have weaknesses. Air isolators are susceptible to the ideal gas law because they are sealed air chambers. If there are major pressure or temperature changes at expansion and contraction of the air outside of the isolator, that sealed chamber is going to react.
Pneumatic air isolators are passive vibration isolation systems. Another type of vibration isolation is active systems. Active vibration isolation systems always have three components:
- A motion sensor
- A force actuator like a piezoelectric stack or linear motor or pneumatic cylinder
- A control loop which is software that controls the system
Can you explain the two different types of active vibration isolation?
The parallel type system is supported by some passive spring, and your force actuator is in parallel. You can use a parallel type system to get a very effective cancellation of known payload noises while using a lot of its bandwidth. A lot of information coming into the sensor limits your ability to achieve stability where you want to cancel out noise at certain frequencies. Thus, this is a system that actually controls its own vibration very well, but it does not work well for floor vibration because it is using all of its effort to cancel out its onboard vibration.

Image Credit: TMC Vibration Control
The other way to arrange these systems is in a serial-type system. This system has a force actuator supporting the inner mass with a passive isolation system on top and a sensor isolated from the payload so your feedback loop can focus on floor noise.
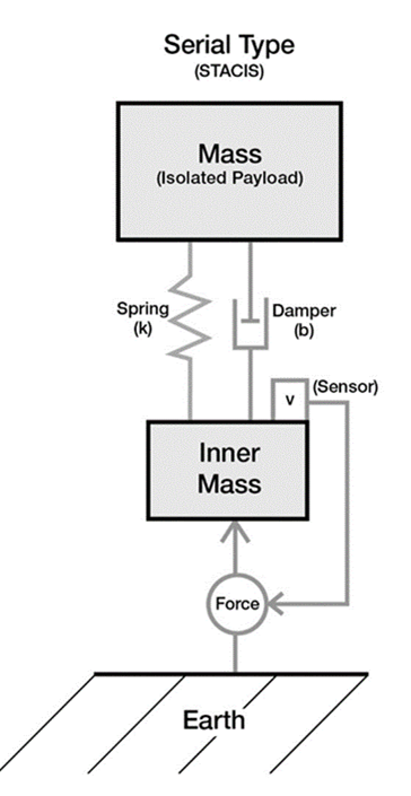
Image Credit: TMC Vibration Control
This system has a quiet inner mass and a very stiff system with no internal resonances with a lot of bandwidth which provides excellent, low-frequency vibration cancellation. The disadvantage of a serial system is that it does not cancel onboard noise well. This is why we often see stacked systems with onboard noise canceled by some parallel type system and the floor vibration handled by an active vibration cancellation platform.
Can you combine different types of vibration isolation systems? Why would you do this?
You can combine an active system with an active system, a passive system with an active system, or a passive system with a passive system. To properly stack two systems, you need one of two criteria: a separation of mass or a separation of stiffness.
Separation of mass means a large mass in between two springs of a similar resonant frequency. Separation of stiffness means that if you have two isolation systems with different enough spring constants, you do not need any mass between them.
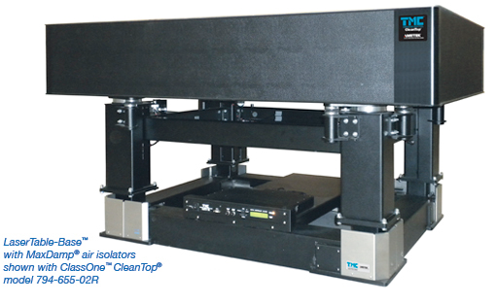
An example of a "stacked system"
Image Credit: TMC Vibration Control
What are some instruments that need vibration control, and how does vibration control affect these instruments?
Most scanning electron microscopes are on an air isolation system, and if there is a vibration problem, this relative motion can misguide the beam. With a serial active isolation system, you can cancel that low-frequency vibration that is being resonated by internal isolators and get a good image.
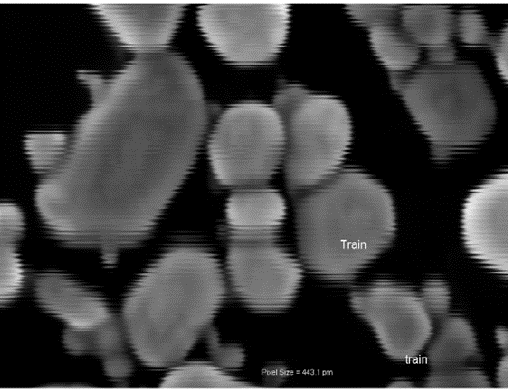
SEM with vibration problems
Image Credit: TMC Vibration Control
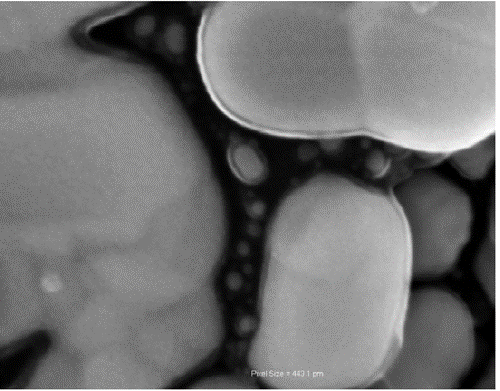
SEM with STACIS serial vibration isolation solution
Image Credit: TMC Vibration Control
Another good example is wafer inspection. These instruments have a stage that moves, stops quickly, and the vibration created by that motion needs to dissipate quickly so an accurate measurment can be made. The goal for a step and settle application is to cancel out the induced motion of the stage as fast as you possibly can. This is a good application for a parallel type cancellation system because as they are best suited to cancel out motion from stages and other moving parts.
How does TMC build systems, and what are some examples of how systems have been built into OEM-type instruments?
The vibration that affects ultra-precision equipment comes from a variety of sources. Each source requires its own mitigation techniques. The key is to think about vibration control early in the design process. You want to engage your solutions early on to better integrate a solution into your frame.
You can integrate systems or stack systems. To build systems, the key contributors to vibration control are mass, stiffness, damping and the isolators used. The more mass you put into a frame, the more stiffness you put into the frame, and the less it is going to vibrate.
However, they have a limit, are expensive, and take up space. At some point, your vibration isolation system needs to become sophisticated enough to start taking over for what mass and stiffness cannot do.
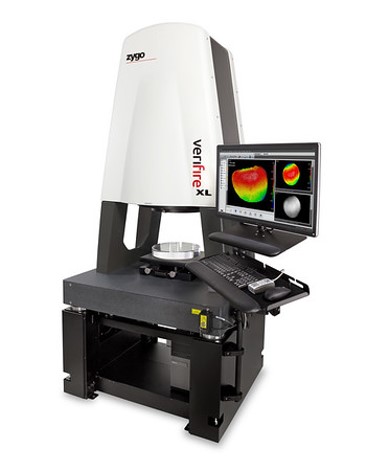
An example of a metrology system with passive vibration isolation designed in
Image Credit: TMC Vibration Control
One example of building systems into OEM-type instruments is a simple integrative passive isolation system on interferometers that are commonly built into scanning electron microscope frames, transmission electron microscope frames, and NMR frames.
In a different case, we use serial-type piezoelectric actuators built into the frame of an optical profilometer to create a two-stage isolation system. We have also made a damped die spring for motion control which provide settling from the stage motion and floor vibration cancellation.
How do you keep up with OEM customer demand? Do they give you a forecast of how many platforms they are going to need in a year?
As everybody knows, the semiconductor market has been experiencing crazy growth in the last couple of years. We work with many of the major OEMs to design and manufacture their internal vibration cancellation systems for tool induced vibration and for floor vibration. We also have to ramp the factory to meet those needs. Forecasting is very important and helps us line up our labor and our supply chain to meet the demands.
What do you see as some of the advantages of outsourcing the design of client machines and vibration control platforms to TMC?
At TMC, we are a team of vibration experts and engineers. The reason why people come to us and why people should come to us when they are designing an instrument is because vibration control systems can be complex. When you are designing an instrument, you want to focus your efforts on getting that instrument to do what it needs to do in the best way. You want to think about your technology – the photolithography or electron microscopy technology. You do not want to waste time developing a vibration cancellation system as part of your total tool from the ground up.
TMC has more than 50 years of experience in vibration control. We think it makes sense for OEM customers to focus on their strengths and allow us to focus on our strengths.
Can you give guidelines on handling the damping of payload-induced internal flexible modes?
It depends on what the motion inducing that flexible mode is. If there is a mass and it is moving from one place to another, it could be causing frame flexure and frame torsional modes when it moves. If the mass is causing the flexure and it is a static flexure once it stops moving, then the recommendation would be to make the frame stiffer or more massive. If this is something that is moving and causing an impact, and you want to try to minimize impact from that motion, then you might be thinking about active cancellation.
About Michael Georgalis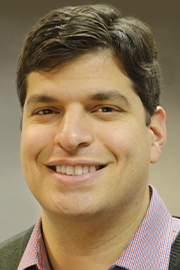
Michael Georgalis is the North American Sales Manager for Technical Manufacturing Corporation (TMC), a unit of Ametek, Inc. TMC provides vibration isolation systems and magnetic field cancellation systems for electron microscopy, semiconductor, photonics, metrology, and life science applications. Michael has a B.S. in Physics from Cleveland State University and an M.B.A from Endicott College in Beverly, MA. He is based at TMC’s factory and world headquarters in Peabody, MA. Michael held roles in Engineering, Applications, Marketing, and Sales for various lighting, optics, and LED manufacturers before joining TMC in 2013.
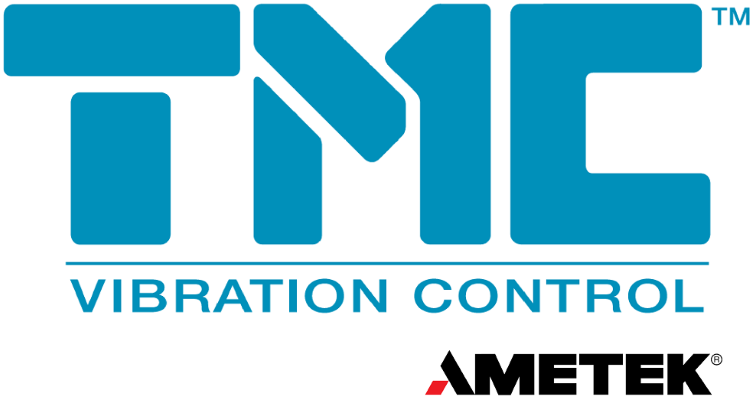
This information has been sourced, reviewed, and adapted from materials provided by TMC Vibration Control.
For more information on this source, please visit TMC Vibration Control.
Disclaimer: The views expressed here are those of the interviewee and do not necessarily represent the views of AZoM.com Limited (T/A) AZoNetwork, the owner and operator of this website. This disclaimer forms part of the Terms and Conditions of use of this website.