After connecting at the Advanced Materials Show 2022, AZoM spoke with Selina Ambrose and James Stephenson from Promethean Particles about the mission of the company and the way MOFs are changing the game of carbon capture.
Please could you introduce yourself and your professional background?
Selina Ambrose (SA): I'm Selina Ambrose, the technical manager at Promethean Particles. In my role, I oversee all of our R&D activity and new product development. I manage and supervise the technical team here. I've been with the company for coming up to 10 years now and, prior to that, I did my Ph.D. in chemical engineering at the University of Nottingham - which was sponsored by Promethean. During my Ph.D., I was essentially using the company's proprietary technology to develop nanomaterials, mainly looking at the synthesis of nanomaterials that could be used for biomedical applications. My project had a ‘bio’ slant as my first degree was in Biochemistry and Genetics. It was a bit of a segue away from that into chemical engineering, but I very much enjoyed it.
James Stephenson (JS): Hi, I'm James, the chief executive at Promethean. I have been here for about two years now - I started in September 2020. I have 25 years of experience in the chemicals industry. I did my master's in chemical engineering at Swansea University back in the mid-'90s, but I only spent about four years doing "real engineering” before getting bit by the commercial bug.
I quickly moved on to the sales, marketing and business management side as I was very interested in what other functions and activities chemical companies did outside of the core manufacturing and engineering operations. This led me to pursue my MBA at Manchester Business School. Prior to Promethean, I've always worked for large American corporations. I have some prior experience looking at silicon nanoparticle inks for printed electronics. When the opportunity with Promethean came along, it felt like a great fit and an exciting opportunity to do something different.
Promethean particles operate the largest continuous nanomaterial manufacturing plant in the world. What is it about your processes that allows the manufacture of multiple materials on such a large scale in a cost-effective way?
SA: We have reactor systems that are designed to operate in a continuous manner using hydrothermal or solvothermal synthesis. That essentially means we are using hot pressurized water or hot pressurized organic solvents as our reaction media to create the particles.
We use continuous flow as opposed to batch. I like to think of it as the analogy of a shower compared to a bath, the latter being batch. We have our liquid precursors that flow into our reactor system, and we use a combination of elevated pressures and temperatures to then nucleate and create the particles from a ‘bottom up’ approach. Then, we collect our product as a liquid dispersion out of the system.
Because we can control the flow rates, pressures, and temperatures, we create a highly turbulent mixing phase in the reactor. There's a lot of energy in there that leads to very rapid nucleation of the particles. In a lot of other synthesis methods, you need to heat up your vessel quite slowly and so you get your particles forming in quite a slow manner, whereas in our system it's very quick. It's a much shorter reaction time to create the particles, and this has a lot of cost benefits when it comes to producing large volumes.
Because of these short reaction times, where we're talking seconds or a few minutes to create the particles as opposed to hours or days for competing technologies, we get very high throughput rates. Therefore, the production costs are a lot more favorable. The secret, I guess, is the design of our reactors.
We've got liquid solutions that we're using to create these solid particles in a flow system. As you can imagine, there is a risk that these particles will just build up and cause a blockage, and then it's not a continuous process for very long! Our reactor designs have been optimized to allow the particles to nucleate and flow out quite nicely with minimized risk of blockages. It is a truly continuous process, and therefore, it can be scaled to reap commercial benefits.
In terms of versatility, our reactors are essentially mixers, so they are quite flexible in terms of the reagents we can use. Lots of different precursors yield a wide range of chemistries and materials coming out, and so we can use the same reactors, the same infrastructure, and the same designs to create a whole host of different products.
What are metal-organic frameworks (MOFs), and what makes their properties unique?
SA: Metal-organic frameworks, or MOFs, are a class of compounds comprised of metal centers and joined by organic ligands or linkers to create a highly porous, cage-like structure. They are interesting for chemical separation or catalytic applications because they have very high internal surface areas.
The surface areas that these cage-like structures create are anywhere from about 1,000 m2/g right up to 10,000 m2/g, from literature reports. We're talking about the equivalent surface area of multiple football pitches in a teaspoon of powder - very, very high surface areas.
This is interesting because MOFs have got the potential for very high adsorption capacities. For gas capture applications, you can potentially adsorb a lot of gas with not a lot of sorbent material. Then also, with the MOFs, the metal centers and the organic ligands or linkers can be tailored to yield selectivity for certain molecules.
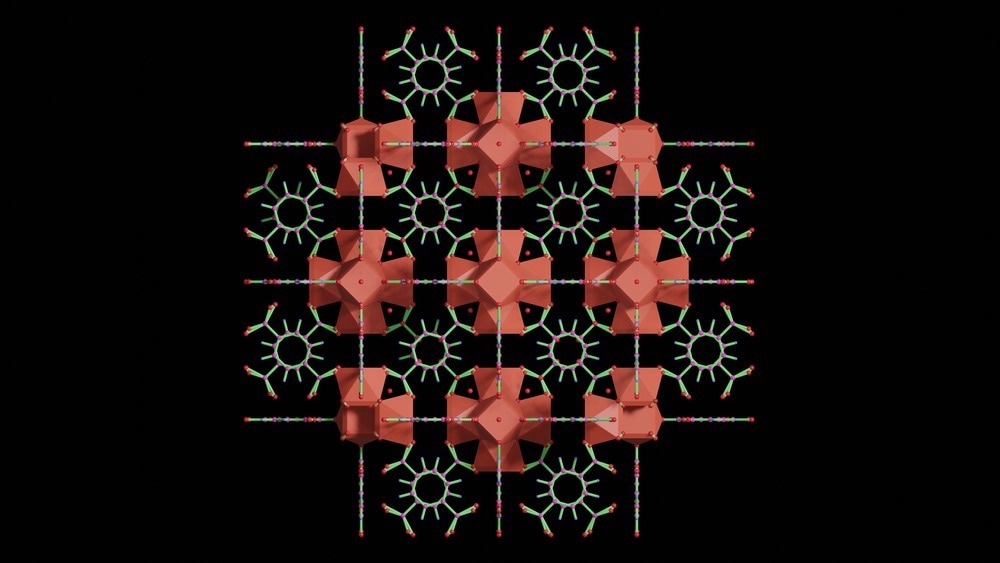
Image Credit: sanjaya viraj bandara/Shutterstock.com
If you are targeting the adsorption of carbon dioxide in a mixed flue gas stream, then you can design and tailor the MOF adsorbent to selectively adsorb the CO2 and leave all the other gases. MOFs are also very interesting for industrial applications because they tend to adsorb molecules through physical adsorption, or physisorption, rather than chemical adsorption, or chemisorption.
The difference here is that chemisorption tends to form very strong chemical bonds between your solvent and your adsorbed material, whereas physisorption forms a weaker bond. To then desorb or detach your molecule and regenerate your sorbent material, you need a lot less energy where there is a physical process rather than chemical adsorption.
JS: MOFs started being discovered really around the '90s, and there are more than 90,000 different combinations of metal centers and ligands that have been reported in the literature.
I think from a company perspective, one of the things we see is that historically MOFs have been the purview of academia. I joke about this a little, but a lot of MOFs have been named after an individual or an academic institution. That seems to have excited the community a little bit; however, we sometimes feel that some MOFs have been pursued more for novelty than viable industrial utility.
For CO2 capture MOFs to be successful in CCS applications, they have got to balance a number of different aspects. They don't just need to have high uptake capacities, as Selina mentioned. They also need to be selective for CO2, meaning they have got to ignore the other components in the gas stream. When we think about what we're trying to solve for the planet, they also have to enable much lower application energies, have a low environmental fate profile, and they have got to be non-toxic.
While some MOF developers might be chasing CO2 uptake records with an exotic MOF, its uniqueness doesn’t always correlate with utility and the probability that it can be scaled into millions of tons.
There are a lot of other key factors around MOFs that are not really being taken into account today. I think that's where Promethean, with our focus, are not only bringing a lot of benefit to the downstream users, but we're actually helping inform some of the MOF discovery and optimization work as well.
As promising as MOFs are, and as important as the capabilities and the performance that they show, one of the key reasons they're not more prevalent today is because their cost has been perceived as prohibitively expensive.
Without technology like Promethean's, MOFs have only really available at the gram, at best kilogram, scale, whereas the multi-ton scale is needed now so that companies can start doing meaningful carbon capture application development.
What limitations do traditional solvent-based carbon capture systems face?
SA: The traditional carbon capture technologies are liquid solvent amines. I talked about chemical adsorption versus physical adsorption before, and that is very much the case here, where liquid amines typically use chemisorption. Very strong chemical bonds form between the captured carbon dioxide and the amine itself.
To break these bonds to release the carbon dioxide and regenerate the liquid amine, you need to use a lot of energy. I think the numbers out there are pretty staggering—something like up to 30% of a power station's output is used to regenerate the liquid amine, where there is a carbon capture element in the process.
It is a good technology in that it's ready to be deployed now, because the scale of the emissions and climate problem is so huge that there needs to be a technology that is tackling the issue right here, right now. Amines do that; however, it's clear that something better is needed, and that is where we see MOFs coming in.
The mechanism for capturing and bonding the CO2 is a physical adsorption process, forming a weaker bond. When it comes to regenerating the MOFs and releasing carbon dioxide for storage or utilization, you need a lot less energy. Typically, from the calculations we've done, this is about half that of the liquid amines. Potentially, there are huge energy savings when it comes to using something like MOFs versus the current incumbent technology.
JS: I think, to put that into practical terms, let’s look at an example using some round numbers. Let’s say you are a power generator and you're going to build a new power generation plant that is going to cost in the order of a billion pounds of CapEx. You are designing that power plant to produce 1,000 megawatts. Now, by the time you have installed and operated a traditional carbon capture system, it has consumed 30-35% of the power output of your power generation plant.
So for that billion pounds, where you're supposed to be getting 1000 megawatts, you're now only getting 650-700 megawatts. Your effective cost per megawatt has just increased dramatically.
And so, when you bring it down to numbers, the financial aspect is obviously critical and becomes a significant driving force in addition to the climate and environmental angle. This combination is what is driving people to seek out more energy-efficient solutions like CO2 capture MOFs.
We know that current generation amine scrubbers are on an ‘S-curve.’ They're going to reach their energy efficiency limit at some point in the near future. We want to be working on alternatives now because we don't want to be starting that work only at the point when that limit has been reached. We get a window of opportunity between discontinuities to work on the next technology. That's where Promethean fits in. We're looking at that next S-curve and getting ourselves into that spot now.
SA: Also, with amine scrubbers, because it's a chemical process for adsorption and desorption, the amines react and can lead to the formation of undesirable by-products. From some of the stakeholders that we've spoken to, and current users of amine technologies, these by-products are a further problem because they’re hazardous. They need to be disposed of in a safe way, which means further costs. We think MOFs won't have that problem.
How can MOFs be used to more effectively capture carbon in an energy-efficient way instead?
SA: As I described earlier, the reduced energy penalty when regenerating MOFs – especially compared to incumbent amine scrubbers - is the main benefit here. Also, MOFs are a lot more robust compared to say, amines, in that they can be recycled and regenerated multiple times, and not degrade or create these by-products that I talked about.
When thinking about carbon capture and use of sorbents, we need to look at the whole life cycle. We know that with amine scrubbers at the moment, once they're used or spent they need to be disposed of in a landfill. With the MOFs that we produce, we are looking at ways to recycle them. Once they're spent, we want to break them down to their component metal and linker parts, then re-crystallize them to create fresh MOFs for use again. That way, they’re likely to have a much better environmental profile.
On the topic of life cycle, we recognize that carbon capture should go hand-in-hand with storage and/or utilization of the captured CO2. We are working with companies that specialize in CO2 utilization to see how the various parts of the value chain fit together to make sure that what we are doing at the end of our capture process then feeds nicely into utilization, and overall is as energy-efficient as possible. With the carbon dioxide that we’re capturing, it would be ideal if it can be used for something else rather than just pumped underground, so it is important to try and take a circular economy approach, while also using resources and energy as effectively we can.
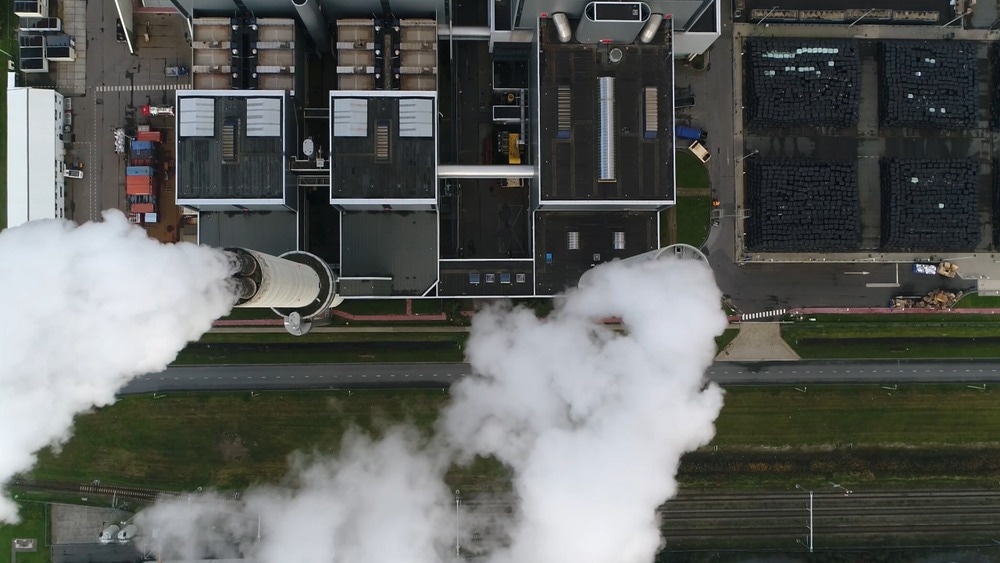
Image Credit: GLF Media/Shutterstock.com
JS: I think when we look at carbon capture as a whole, there is still a lot of uninformed strategy at the moment around what companies are trying to do and why and how that's going to be done. Clearly, many companies are under a variety of pressures to improve their environmental footprint and show a more committed approach to sustainability. This will only accelerate as governments start lowering the financial penalty thresholds that will subsequently impact increasingly smaller companies. It is critical we understand that landscape because it's an important one.
However, as important as carbon capture is, we believe for the sake of the planet that there are many other aspects that have to come first. It's almost like a hierarchy of needs. Industries have got to start being more efficient in the first palce, and then there's fuel switching and moving away from carbon-based energy sources altoghether. However, at the end of the day, the reality is that the world is currently emitting 36 gigatons of carbon dioxide every year into the atmosphere. Only so much will ever be offset by energy efficiency, fuel switching, and the drive towards electrification.
There will still, therefore, for the very foreseeable future, be a significant part of our industrial landscape that is going to produce carbon dioxide emissions. That’s why we need carbon capture MOFs. We never want to give the impression that all this other technology is bad and MOFs for carbon capture are the only way to go. We have to compete and cooperate differently with other technological solutions if we are going to have any meaningful impact on climate change.
Just building on what Selina mentioned with respect to downstream utilization, there are a lot of practical considerations. It would be quite easy for us to just concentrate on the capture process, but our customers are already asking the right questions about the end use. We often hear: “what will be done with the CO2 once you have captured and regenerated it.” Our recently published white paper discusses some of these aspects of carbon storage and sequestration in more detail. I can be downloaded from our website.
Just like I believe carbon capture should be a later option after we have increased energy efficiency and perhaps switched to less carbon-heavy energy sources, we would prefer to see more utilization of CO2 in current and future applications. At our position in the emerging CCUS value chain, we cannot just fall into the trap of saying, "Yeah, somebody else will figure it out." We could, since we know there are and will be myriad companies working on this, but it's probably a little bit of an irresponsible position to take.
How significant do you believe nanomaterials will be to industrial innovation in the future?
SA: Promethean are a member of the Nanotechnology Industries Association, the NIA. We've engaged with other nanomaterial producers and got a feel for the nano sector as a whole. From my perspective, nano has been misunderstood for quite a long time.
There have either been safety concerns or issues around the formulation and incorporation of nanomaterials into products, meaning the adoption of nanotechnologies and nanomaterials has been held back for the last 10 to 20 years, but I do think that's changing as more work has been done to understand these unknowns. The Nano Safety Cluster within Europe has done a lot of work and the European Commission has put a lot of funding into nano safety research.
I think for consumer goods and consumer applications, there may still be some reservations, largely because there's been a poor media portrayal of nano, and there are still some consumer regulations that are holding back nano-enabled products, acting as a barrier to the market. Particularly, for SMEs, getting products into those sorts of markets is a challenge.
JS: I think the problem with the broader adoption of nanomaterials at the moment is that a lot of the companies are somewhat early-phase, and the overall incorporation of nanomaterials into end applications is still relatively nascent. Customers are not really that interested in how "good" the nanomaterials are. They are interested in what benefits they bring to their applications and how this will enable them to create more value. This require application development and it can be very expensive for just one new material. To take multiple different nanomaterial classes and prove how they're going to work in the customers' applications can be financially prohibitive.
I think there's still going to be a lot of potential growth. It's on the incumbent nanomaterials manufacturers to put what they are doing into the language of their customers so that the benefits they're going to receive are clearly understood. That's got to be application specific. This is why we pivoted our strategic approach at Promethean from a broad materials technology platform to something much more application-focused, i.e. MOFs for carbon capture.
How do you anticipate Promethean Particles will grow and develop over the next decade?
JS: In all my career, I've never seen such a groundswell of unsolicited requests for information and help. So, even though we believe our current reactor technology provides us orders of magnitude greater capacity than other nanomaterial and MOF manufacturers, it's still only a tiny fraction of what is ultimately going to be required.
I believe that now Promethean is predominantly focused on MOFs for carbon capture, our key job is to continue to show that there is a path for MOFs to become a viable technology. Then beyond that, it's all about advancing the scale.
Now, fortunately, the technology that we've got scales very efficiently and not linearly. We don't need 100 times the footprint of Promethean in order to develop 100 times the capacity. That's where Promethean's time and effort has been and will continue to be. We have already taken significant further steps here with new reactor designs that will greatly increase Promethean’s capacity and economies of production. However, job number one is to continue to demonstrate the performance of MOFs in the carbon capture applications we want them to be successful in.
Looking forward, I see a lot more industrial collaborations with engineering contractor firms and certainly with end users and emitters. We've got some of that underway right now. You've probably heard about the initial project that we had with Drax and the University of Nottingham, called PICASSO. This is a great opportunity to show that we are advancing our technology readiness level by putting MOFs in a relevant environment and seeing how they perform.
We want to continue that to advance the technology through bigger and more automated systems and drive them towards commercial scale. Once we start getting up to those higher TRLs, 7-9, it's then really about continuing to drive the growth of the company through further investment and through our own organic growth, such that we can scale appropriately and start making a real impactful dent in the climate change problem.
About James Stephenson and Selina Ambrose
James Stephenson
Chief Executive Officer
With an extensive background in chemical manufacturing and processing, James’ career spans both sides of the Atlantic. He worked for Dow Corning (now Dow) for more than 16 years in the UK and United States including roles as Global Product Manager for the Electronics and Advanced Materials Business and the Global Market Director for Medical Materials. He also led an internal start-up for the development of silicon nanoparticle-based inks for printed electronics. Since then, he joined PolyOne (now Avient) as Global Marketing Director for their PVC business and was the General Manager/Managing Director for their composites business. Prior to joining Promethean, James served as Vice President, Global Business Development, at Carlisle Fluid Technologies.
James joined Promethean Particles as CEO in 2020. He holds an M. Eng in Chemical Engineering from Swansea University and an MBA from Manchester Business School.
Selina Ambrose
Technical Manager
A current board member of the Nanotechnology Industries Association (NIA), Selina holds a Ph.D. in Chemical Engineering, specializing in the continuous-flow hydrothermal synthesis of functional nanomaterials.
With more than 10 years of experience in the nanotechnology field, she leads the technical team at Promethean, managing the company’s research and development activities, which includes new product development.
Disclaimer: The views expressed here are those of the interviewee and do not necessarily represent the views of AZoM.com Limited (T/A) AZoNetwork, the owner and operator of this website. This disclaimer forms part of the Terms and Conditions of use of this website.