In this interview, AZoM talks to Sarah Heald at Coca-Cola® about how the Thermo Scientific® MAX-Bev® System helps them with their CO2 purity monitoring.
Can you tell us a little bit about yourself and your role at Coca-Cola?
My name is Sarah Heald, and I am the quality supervisor at Coca-Cola Beverages Northeast, in the Londonderry Production Center near Manchester, NH. I work with a talented and diverse team of lab technicians and syrup batchers who carry out extensive testing on raw materials and finished products.
We test everything from raw materials to the finished products that you would see on the shelf. My role is to create "the perfect sip" to deliver the best experience for the consumer, and we rely on the Thermo Scientific MAX-Bev system to help us do that.
What did you do before implementing the MAX-Bev system, and how has the product changed the entire process?
Creating '"The Perfect Sip" using the MAX-Bev CO₂ Purity Monitoring System
Image credit: Thermo Fisher Scientific
Before implementing the MAX-Bev system, we lacked a continuous monitoring system. This meant that more testing of CO2 was required at the time of delivery. A lab tech could sometimes be occupied with receiving the truck for up to an hour, with any mistake causing repeat testing. With this type of system, we have simplified our processes, saving time and easing stress on the lab techs, drivers, and other plant personnel as well. The MAX-Bev system has been a huge improvement to our CO2 receiving process overall.
Can you walk us through the quality control process for monitoring CO2 purity at Coca-Cola, including the use of the MAX-Bev system?
When a CO2 delivery arrives, a lab tech will greet the driver at the CO2 tanks. After verifying all the seals on the truck match the paperwork, the driver connects the hoses. A sample from the truck is taken through the analyzer to ensure that the purity matches the supplier's certificate of analysis. What is great about the MAX-Bev system is that everything is timed and automated, so there are no further actions for the tech at this stage. The results are displayed on the screen as a simple pass or fail for all of the attributes that Coca-Cola requires for their beverage products.
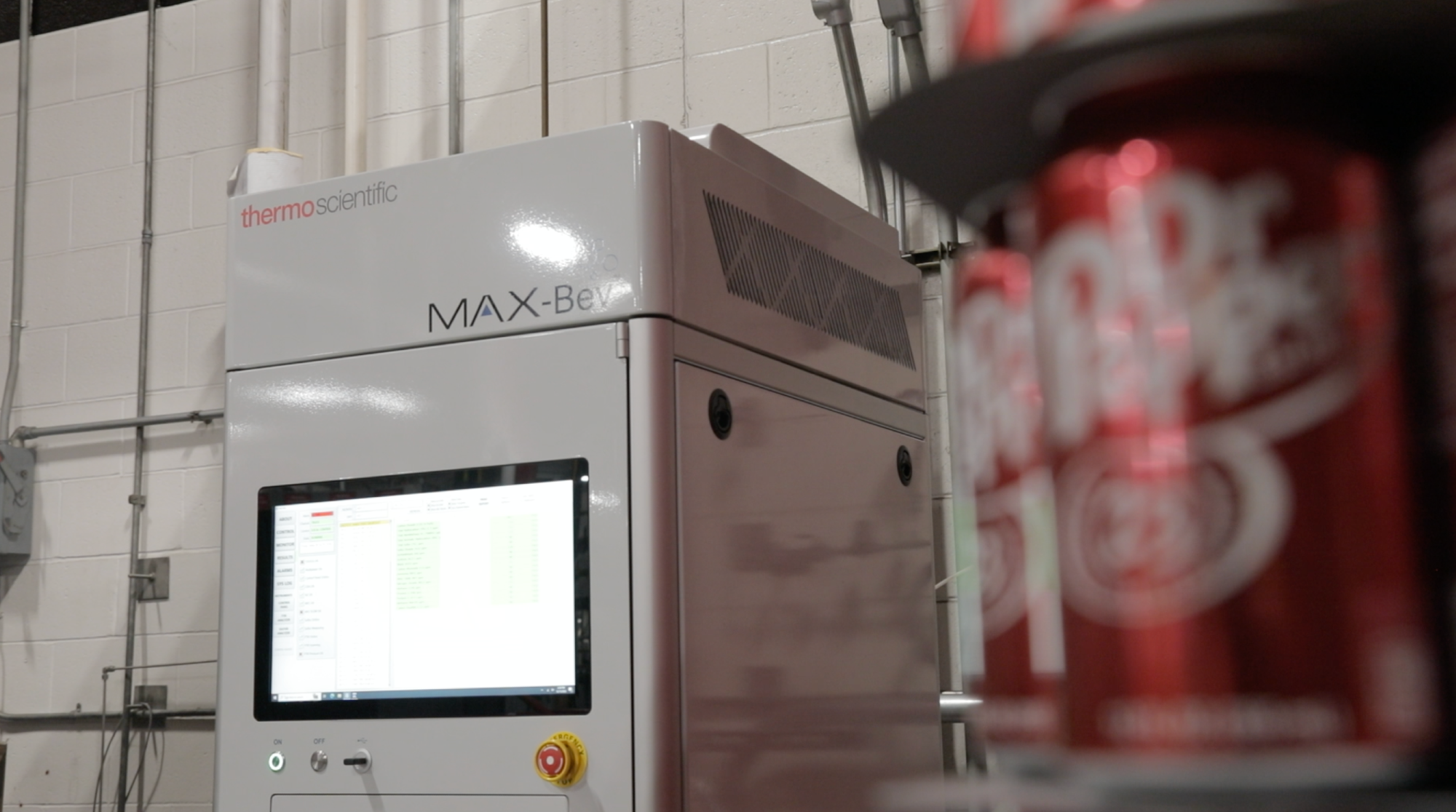
Image credit: Thermo Fisher Scientific
How important is it that the CO2 purity monitoring process is accurate and precise?
There are different grades of purity of CO2. Beverage-grade purity must be 99.9% pure which is why we require very precise and accurate testing of the CO2 to ensure we are receiving this level of purity.
We use a parts-per-million scale to measure the level for some impurities, whereas for other impurities, we have to go down to parts per billion. Hence, we are measuring on an extremely small scale.
This level of purity is extremely sensitive to measurement, which is why we rely on the MAX-Bev system to provide the required accuracy. If we are unable to detect the impurities from the truck at the point of origin, the finished product may have an off-odor or smell.
What are the benefits of the MAX-Bev system? How does it compare to the traditional methods?
The previous system also used an analyzer, but we had to return to the building to get the results and then go back out to the truck to inform the driver that the test had passed.
Before this system, all of the testing was done manually. The lab tech would get a sample of CO2 from the truck, bring it back to the lab, and conduct a series of tests involving dangerous chemicals and glassware that could take up to 30 minutes to complete.
If a mistake was made, they would have to start over from the beginning, which could take up to an hour.
The MAX-Bev analyzer has eliminated a significant amount of human error that can occur during testing. In addition, the time saved has also significantly improved the process.
Can you discuss the technical capabilities of the system in terms of measuring trace impurities and why these features are important for quality control?
As the purity of beverage-grade CO2 is so high, the analyzer must be able to detect impurities at an extremely low level. This is why the FTIR technology must be very accurate. For instance, aromatic hydrocarbons are very important to look at when testing the CO2 from the truck. The maximum acceptable level is 0.02 parts per million.
The MAX-Bev system can detect aromatic hydrocarbons at this level without issue. This is another reason why I am so confident in this analyzer.
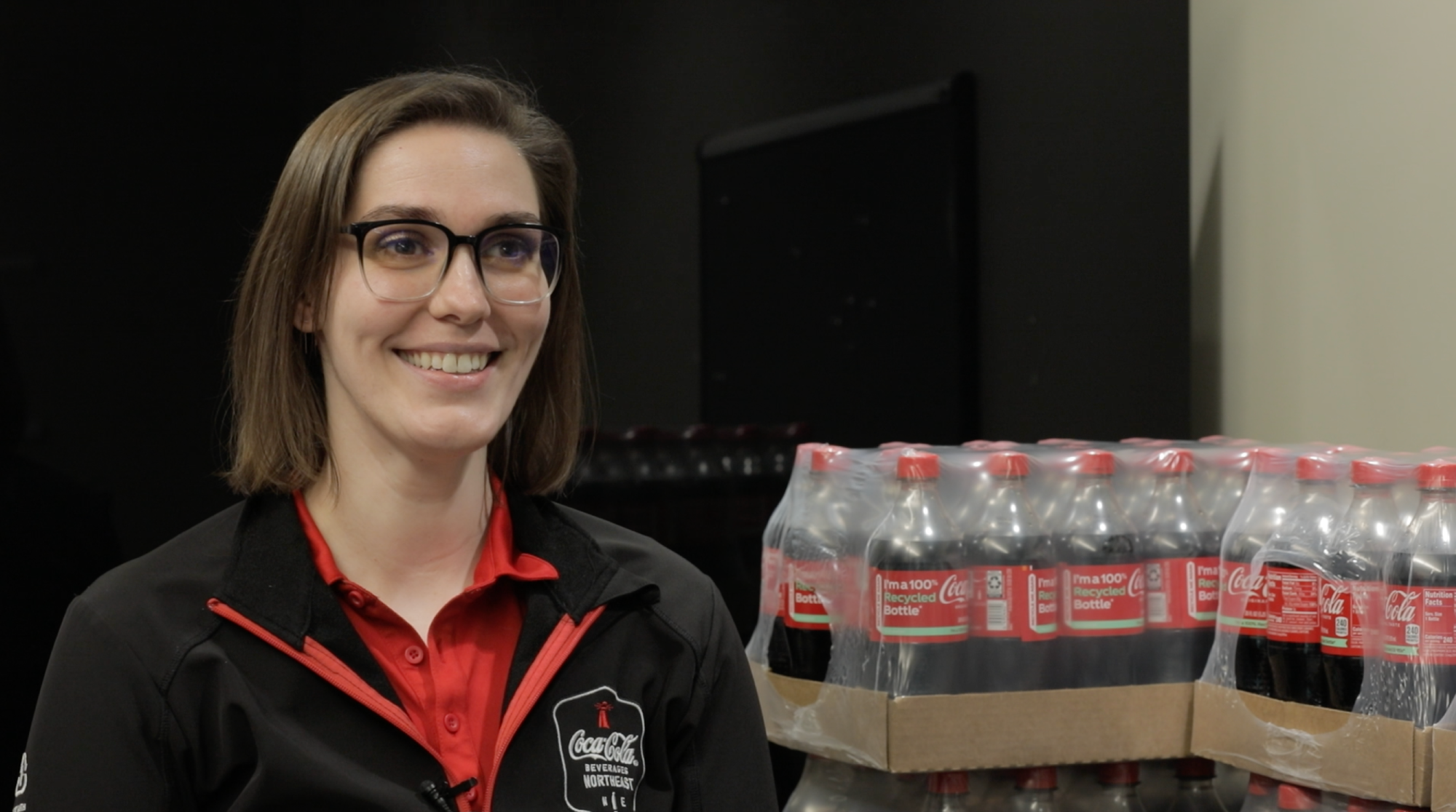
Image credit: Thermo Fisher Scientific
Can you discuss the reliability of the system, as well as the support you receive from Thermo Fisher Scientific?
The system is extremely reliable. We have also established a strong relationship with the technical representatives from Thermo Fisher Scientific. They conduct regular health checks on the system, either in person or remotely. They can log in to the system at any time to conduct checks. They then send us detailed reports via email. They can also come on-site with little notice. We have previously scheduled services, and they usually arrive within the week.
Having said that, we do not need to use these services much because the system is already very reliable. It is very self-explanatory; there are almost no errors that we cannot figure out on our own. From a technical standpoint, it is very easy to use. My lab techs prefer this system to our old system, even though it had a similar interface. Since implementing the MAX-Bev system, I have noticed a significant decrease in the stress level associated with receiving a CO2 truck.
What are some challenges you face when it comes to maintaining the purity of CO2 during transport, storage, and shipping?
Keeping our supply steady during COVID-19 was a huge challenge for us. With the requirement for beverage-grade CO2, we had to ensure that we had approved suppliers. When you do not have an established relationship with certain suppliers, it is very difficult to guarantee 99.9 % purity.
This is where we rely on the MAX-Bev technology and our relationship with Thermo Fisher to produce reliable results, ensuring that we are getting 99.9 % purity when we have to use outside suppliers.
In addition, we are required to accept first deliveries due to the risk of contamination if the first delivery is not received. This is where the storage issue comes in. The supply is similar to a car; if you do not have the right fuel grade, your car does not run the same. If you do not have the correct purity of CO2, drinking a classic Coke® will not provide the same experience. Certain people can tell the difference, so we need to make sure that the level of purity is beverage grade.
How does ensuring CO2 purity affect the quality and taste of Coca-Cola’s products?
If we accept a CO2 delivery that contains the wrong grade, the issue may not be apparent until the product is on the shelf, and we might not know about it until the consumer complains.
This is very frustrating for me as a quality supervisor because it could have been easily prevented by using an online analyzer and conducting a test as simple as pressing "start", as the MAX-Bev system does. These complaints are some of the easiest to prevent, especially when they pertain to something as manageable as unpleasant odors and tastes.
How does the MAX-Bev system help you meet industry CO2 purity standards, such as those set by the ISBT?
The ISBT’s industry standards for beverage-grade CO2 are identical to those set by Coca-Cola, meaning there is no difference between them. At our facility, the MAX-Bev system ensures that every CO2 delivery we accept is 99.9 % pure, fully meeting these industry standards.
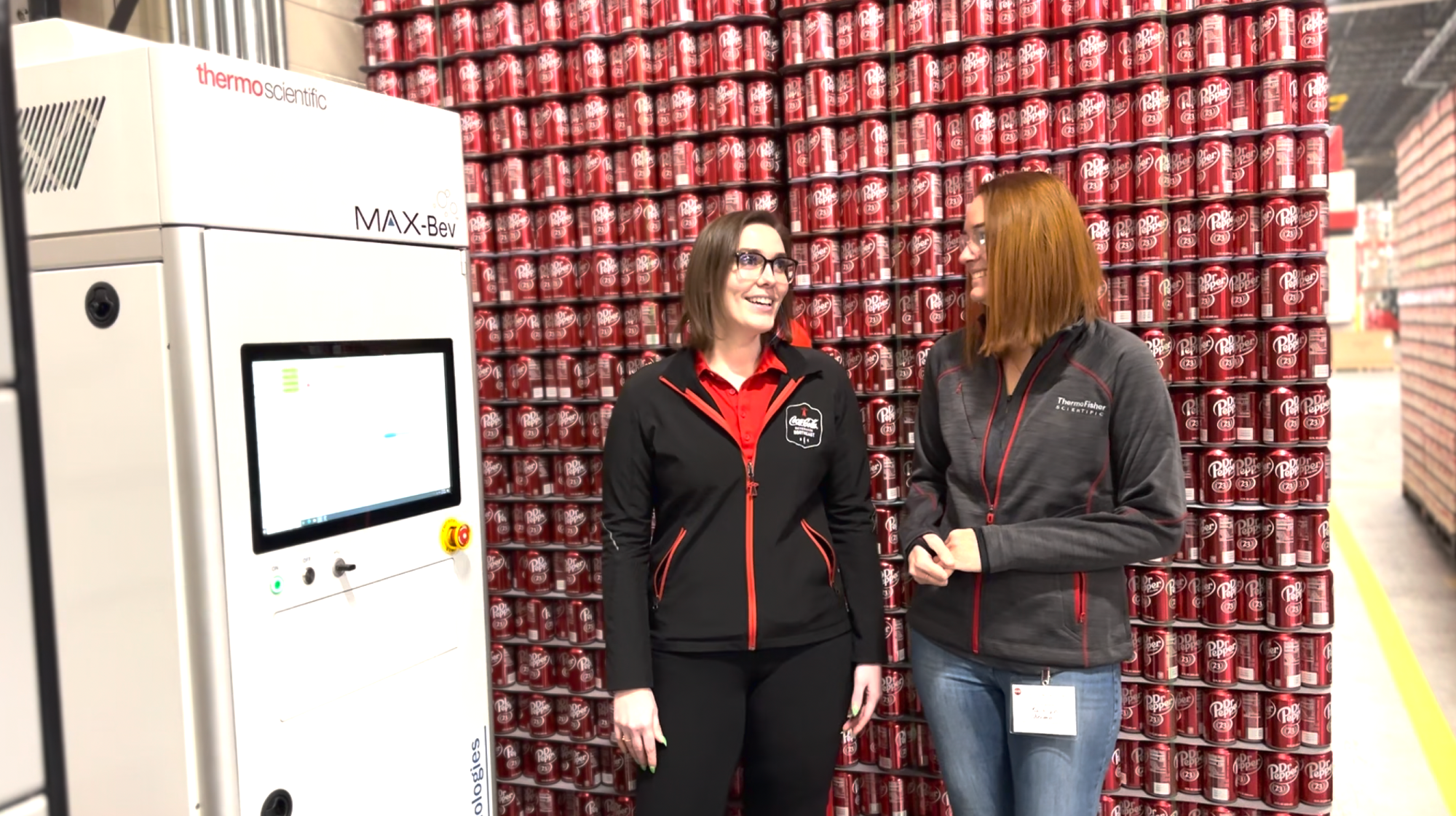
Image credit: Thermo Fisher Scientific
Could you talk a little bit about how you use the MAX-Bev system to retrieve results?
The MAX-Bev analyzer features an excellent user interface with screens on both the inside and outside, making it easy to immediately determine if the results are passing or failing.
Additionally, results can be retrieved directly from the database via USB, allowing for easy printing from a PDF file. The system also includes onboard storage for results on the computer integrated into the analyzer, and these reports can also be printed externally.
What happens when the tanker arrives and the gas is delivered, how frequently the test is run, and how many times a tank must be tested?
When a truck arrives, the driver will hook up and place the hose in bypass mode. As a result, a small portion of the truckload will be placed in the analyzer rather than the tank. So, we can be certain that what is in the truck is 99.9% pure beverage-grade CO2.
It will do three rounds of testing. Each test is about three minutes long. This will ensure that all of the attributes assigned to us by Coca-Cola, for making sure that all the impurities are below a certain level, are met before we accept the delivery.
How long does the process take now compared to the old system?
It now takes about 15 minutes between when the driver calls the lab and when the lab tech returns from a completed test. The lab tech meets the truck driver outside. Once the truck driver has connected his hoses from the truck to the MAX-Bev system and our external CO2 tanks, a small amount of the CO2 in his tanker will be diverted into the MAX-Bev to be analyzed for impurities. The test will take about a total of nine minutes.
Previously, the testing procedure took much longer. It could take anywhere from 30 minutes to an hour to collect a CO2 sample from the truck and transport it to the lab.
Looking forward, how do you see MAX-Bev helping to improve quality control for a company like Coca-Cola?
The only improvement I could see right now, and I know things can change, is the three-minute test. I understand that this is just splitting hairs, but if we could make it two minutes, that would be the only improvement I can see.
I have heard that unpleasant odors in CO2 tanks may be caused by microbial activity. Perhaps we could develop a technology or implement a screening process to mitigate this issue in the future.
About Sarah Heald
Sarah Heald is the quality supervisor at Coca-Cola Beverages Northeast, in the Londonderry Production Center near Manchester, NH. She works with a talented and diverse team of lab technicians and syrup batchers who carry out extensive testing on raw materials and finished products to create "the perfect sip" and deliver the best experience for the consumer.
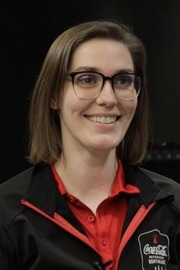
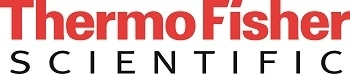
This information has been sourced, reviewed and adapted from materials provided by Thermo Fisher Scientific – Environmental and Process Monitoring Instruments.
For more information on this source, please visit Thermo Fisher Scientific – Environmental and Process Monitoring Instruments.
Disclaimer: The views expressed here are those of the interviewee and do not necessarily represent the views of AZoM.com Limited (T/A) AZoNetwork, the owner and operator of this website. This disclaimer forms part of the Terms and Conditions of use of this website.