There is increasing pressure on manufacturing facilities to produce efficient, high-quality results, particularly in industries that require precision components.
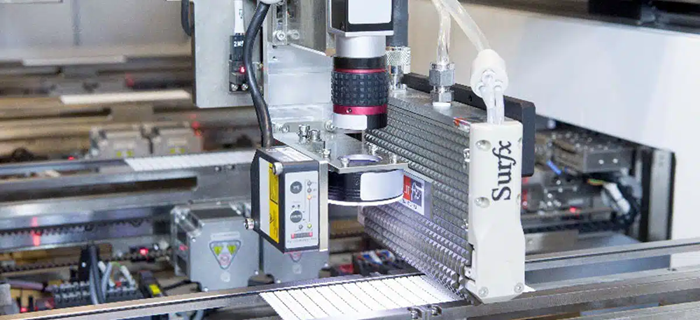
Image Credit: Surfx Technologies, LLC
Engineers are scrutinizing every stage of the manufacturing process, from design to final product, in search of innovative solutions to meet demanding consumer expectations. Plasma technology has emerged as a leading answer to challenges related to quality, efficiency, and sustainability.
With the growing need for advanced semiconductor manufacturing, the global plasma source market is projected to reach $2.6 billion by 2030. Additionally, the increasing emphasis on plasma-based surface cleaning and modification is significantly fueling this market's expansion.
Plasma and its Uses in the Manufacturing Industry
Plasma is a neutral, ionized gas comprised of free electrons and positive and negative ions. It is often referred to as the fourth state of matter after solids, liquids, and gases.
Plasma is generated by applying energy to a gas until a critical number of electrons leave the atomic shell, prompting the gas to ionize.
Plasma has been part of the natural world for millennia, but it has become commonplace in manufacturing and production sectors due to recent technological innovations.
Plasma is routinely used in several applications throughout the manufacturing industry, including the production of high-quality electronics, automotive, aerospace, and medical components.
Common uses of plasma in the manufacturing industry include:
- Plasma cleaning: Plasma cleaning removes contaminants from the surfaces of sensitive components to increase bond and adhesive strength.
- Plasma etching: Plasma is used to remove certain materials from component surfaces, enabling the precise shaping of materials and intricately designed parts.
- Plasma-enhanced chemical vapor deposition (PECVD): PECVD makes use of plasma to deposit thin, protective material films onto sensitive surfaces. This approach is frequently used to create insulating layers on electronic components.
Plasma is found in the manufacture of components for a range of industries, including:
- Electronics: Electronics are often made up of sensitive components that necessitate the implementation of dry in-line manufacturing methods. Plasma treatments are used to clean these components prior to the manufacture of electronic components like circuit boards.
- Medical: A large number of medical machines rely on high-level adhesion to ensure quality results. Plasma treatments can be used to efficiently clean medical components, ensuring the sterility required for use in health care settings.
- Automotive and aerospace: Products in the automotive and aerospace sectors are subject to especially challenging field conditions, with little to no tolerance for failure in the field. Plasma cleaning is key to increasing yield, improving bond strength, and enhancing process control, key factors in ensuring a more robust and longer-lasting product.
Uses of Plasma Cleaning
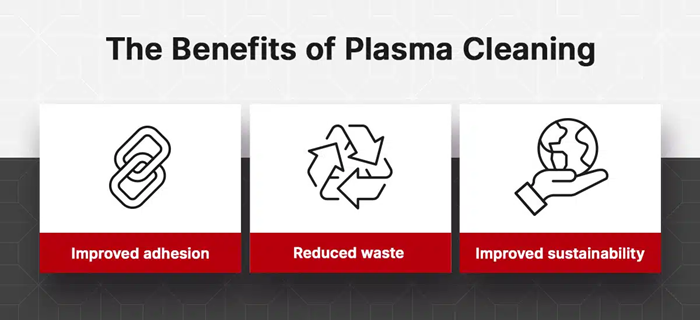
Image Credit: Surfx Technologies, LLC
Plasma cleaning has become a popular choice in manufacturing for tackling the challenge of microscopic contaminants on surfaces. These tiny impurities need to be removed to ensure that critical components adhere properly.
Plasma cleaning excels at getting rid of both organic and inorganic residues, including surface oxidation and stubborn organic materials, from a variety of surfaces like metals, alloys, and plastics.
Plasma cleaning is also able to remove surface contaminants with no impact on material integrity or performance. The gentleness of this technique affords it significant versatility, meaning that plasma treatments can be applied to a wide range of materials and sensitive components, for example:
- Semiconductor wafers
- Wire bonding and die attach
- Wetting and adhesion in electrics assembly
- Bonding composite structures, fasteners, and assemblies
Advantages of Plasma Cleaning
Plasma cleaning provides an array of benefits to manufacturing applications.
Improved Adhesion
Plasma cleaning in a manufacturing line can enhance bonds created at later points in the process. Plasma cleaning removes foreign contaminants present on the base material, meaning that these contaminants can no longer inhibit the bonding process. Where necessary, the cleaning process can also be adjusted to target specific contaminants and materials.
Reduced Waste
Contaminants inhibit bonding or plating during manufacturing, potentially leading to adhesion issues such as bubbling. These issues could render components unusable, impacting profitability due to the generation of excess waste. Plasma cleaning before the bonding and plating process can mitigate these risks.
Improved Sustainability
Plasma cleaning removes the need for harsh cleaning chemicals and volatile organic compounds (VOCs), both of which pose risks to nearby workers and bystanders and damage the environment.
Almost 90 % of consumers believe that organizations should do more to reduce their carbon impact. Thankfully, the plasma cleaning process is inherently environmentally friendly, making it a popular choice in the current market.
Different Types of Plasma
Depending on the application, several gases can be used to create plasma for manufacturing applications. Each plasma type offers distinct advantages and disadvantages, but each plays a key role in overall manufacturing workflows.
Some of the main plasma types employed in manufacturing include:
Argon-Only Plasma
In traditional vacuum-based techniques, using argon plasma alone can lead to ion bombardment that roughens surfaces, creating significant challenges in semiconductor fabrication.
However, when plasma is produced at atmospheric pressure, argon serves as a carrier for process gases, which can delicately remove surface contaminants—making it well-suited for delicate components.
Argon-Oxygen Based Plasma
When oxygen is added to an argon plasma process, oxygen molecules can break apart to form highly reactive single oxygen atoms. These atoms interact with organic contaminants on the substrate's surface, converting them into gaseous byproducts that are then removed without the need for liquids.
The reactivity of oxygen plasma is such that it can integrate into polymer chains under certain thermodynamic conditions, creating polar functional groups on polymer surfaces. This capability makes oxygen plasma an effective tool for a variety of surface-cleaning applications.
Argon-Hydrogen Based Plasma
Hydrogen (H2) plasma is a powerful reducing agent that can be used to clean or reduce oxides from a range of components. Much like oxygen, the hydrogen molecule can dissociate when hydrogen is introduced as a process gas in argon plasma, forming single neutral hydrogen radicals.
This process is valuable in many microelectronics and semiconductor applications, because the radicals formed are extremely reactive and able to react with metal oxides, essentially reducing materials back to pure metal.
Helium-Based Plasma
Helium-based plasma works in the same way as argon-based plasma. While helium’s valence electron characteristics make it easier to initiate plasma, it is less favored for high-volume manufacturing due to its higher cost.
Integrating Plasma into Manufacturing Processes
There are significant benefits to integrating plasma into a manufacturing process. Reliance on potentially harmful chemicals can be reduced and adhesion enhanced, all without damaging sensitive components.
Surfx Technologies offers a comprehensive range of atmospheric plasmas, ideally suited for the high-volume manufacturing of automotive electronics, electrical components, and medical devices.
The company’s innovative automatic plasma machines are high-quality and trustworthy, thanks to their incorporation of treatment speeds, process tuning, and process logging.
Acknowledgments
Produced from materials originally authored by Surfx Technologies.
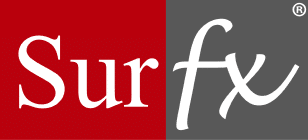
This information has been sourced, reviewed and adapted from materials provided by Surfx Technologies, LLC.
For more information on this source, please visit Surfx Technologies, LLC.