Functionally gradient materials (FGMs) are an innovative class of materials composed of two or more constituent phases with a continuously variable directional composition.
This unique structure allows FGMs to offer varying properties across their volume, making them ideal for applications that require resistance to high temperatures, transverse rupture strength, and high thermal conductivity while remaining lightweight.1
Rocket combustion chambers and nozzles operate under extreme thermal as well as mechanical stresses which make them prime candidates for FGMs. Cold spray additive manufacturing (CSAM) has emerged as a promising technology for producing these lightweight, high-performance components at relatively low cost with fast iterative development times.
Beneath this umbrella technology, high-pressure cold spray (HPCS) has demonstrated potential for creating advanced metal structures, particularly with materials such as GRCop-42 Copper alloy. It could also facilitate the transition into nickel-based superalloys—a material that indicates even greater functionality.1
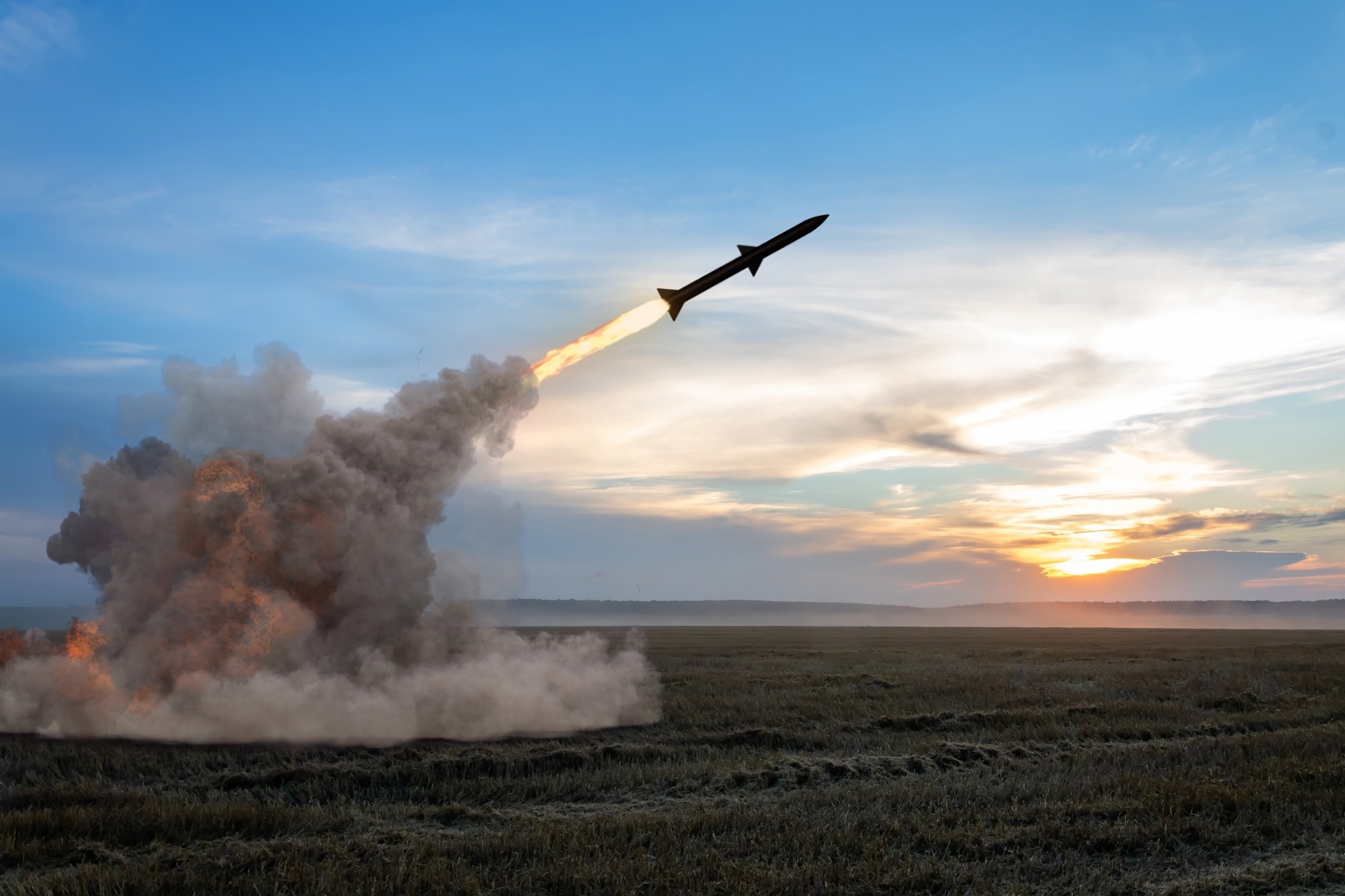
Image Credit: Anelo/Shutterstock.com
Problem: Overcoming the Challenges of Traditional Manufacturing
Traditional manufacturing techniques for aerospace components are complicated, partly due to alloys' strengthening elements. Even with advanced techniques like high-energy beam additive manufacturing, difficulties such as cracking persist.
Engineers must contend with these challenges while achieving proper bonding between materials, desired mechanical properties of components, and optimal thermal performance of FGMs.1,2
CSAM provides an opportunity to overcome many of these concerns. As a solid-state process, CSAM deposits materials with low porosity, high strength, and compressive residual stresses whereby avoiding the limitations associated with melting and resolidifying feedstock. Accurately characterizing the bonding and porosity within these multi-material structures is essential to optimizing the manufacturing process.
Traditional scanning electron microscopy (SEM) is often limited to small selective regions, making it difficult to fully assess the micron and sub-micron scale bonding characteristics of FGMs across an area large enought to be interpolated.1
Challenge: Achieving Accurate Multiscale Characterization of FGMs
During cold spraying, metallic powders are directed toward a substrate at supersonic speeds to create an alloy coating. The adhesion of these powders depends on multiple factors, including the velocity and plasticity of the powder particles.
Using HPCS processes with varying gas compositions, such as nitrogen (N2) and helium (He), introduces challenges in manufacturing large CSAM parts. While pure He gas processing can enhance particle velocity and result in higher coating densities, especially for high shear strength alloys like Ni and Ti, it is also more expensive.1
As previously mentioned, evaluating FGMs, like Ni-Cu CSAM alloy, for accurate and comprehensive characterization across multiple scales—from macro to nano—presents a significant hurdle. Effective analysis must account for large-scale open porosity voids and critical, fine-micron splat boundary voids affecting grain-to-grain adhesion.
Traditional SEM imaging is often constrained by its ability to evaluate only small, selective regions at the magnifications necessary for detailed analysis, limiting its effectiveness in assessing the entire material's structure.
This creates a pressing need to optimize processing parameters, assess large-scale metallographic samples accurately, and evaluate the cost-effectiveness of manufacturing processes.1
Solution: Large-Area Automated Multiscale (LAM) SEM Imaging and Correlated Analysis
A statistically validated approach to overcoming the challenges associated with FGM characterization can be found in large-area automated multiscale (LAM) SEM imaging combined with SEM-energy dispersive X-ray spectroscopy, advanced image analysis, and correlative techniques. This methology offers a solution for evaluating the HPCS processing results across larger sample areas with high resolution.1
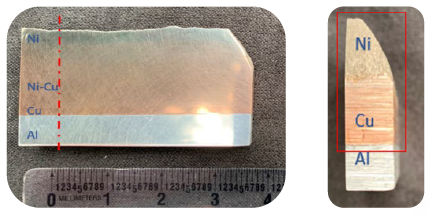
Image Credit: Thermo Fisher Scientific
In a study conducted by Thermo Fisher Scientific, the Axia ChemiSEM combined with Maps 3 Software allowed multi-centimeter scale LAM SEM imaging to be completed automatically, supplying comprehensive data on the distribution and adhesion of particles across the FGM sample.3
Avizo2D Software was then utilized to perform image analysis on the high pixel density images extracted from the stitched tile set, allowing for an accurate assessment of porosity classes (deemed Type 1 and Type 2).4
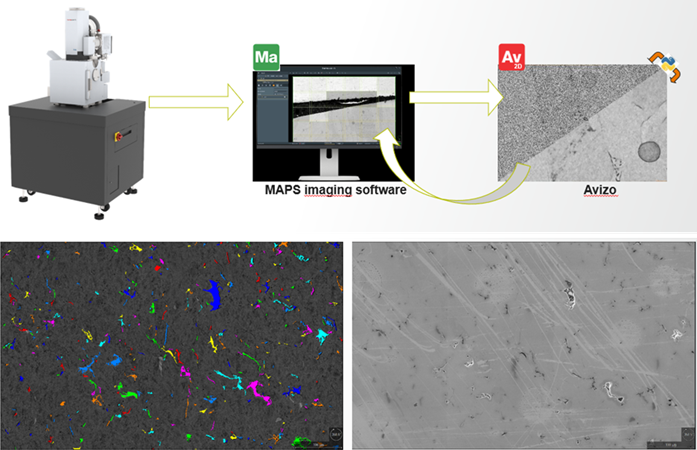
Image Credit: Thermo Fisher Scientific
Porosity Analysis
LAM 2D SEM imaging revealed that Type 1 porosity was closely comparable to results obtained from micro-CT scanning. Type 2 porosity, representing fine grain boundary voids, exhibited a higher area fraction than Type 1 and was more prevalent in nickel-rich regions due to the lower plasticity of nickel compared to copper.
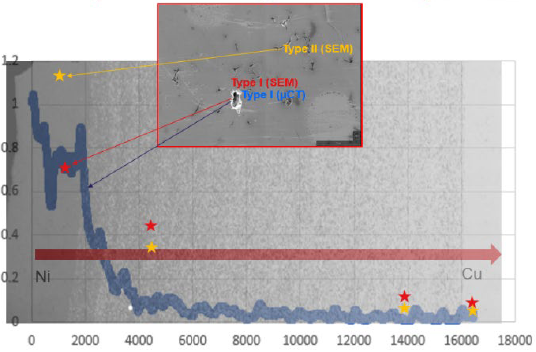
Image Credit: Thermo Fisher Scientific
Correlation with 3D Analysis
While micro-CT scanning provided a larger volume assessment, it struggled to resolve the fine-structured Type 2 porosity. Combining LAM SEM imaging with 3D tomography using a Helios 5 PFIB DualBeam allowed for a more comprehensive understanding of the volumetric data, validating the presence of critical fine structure voids not detected by micro-CT alone.
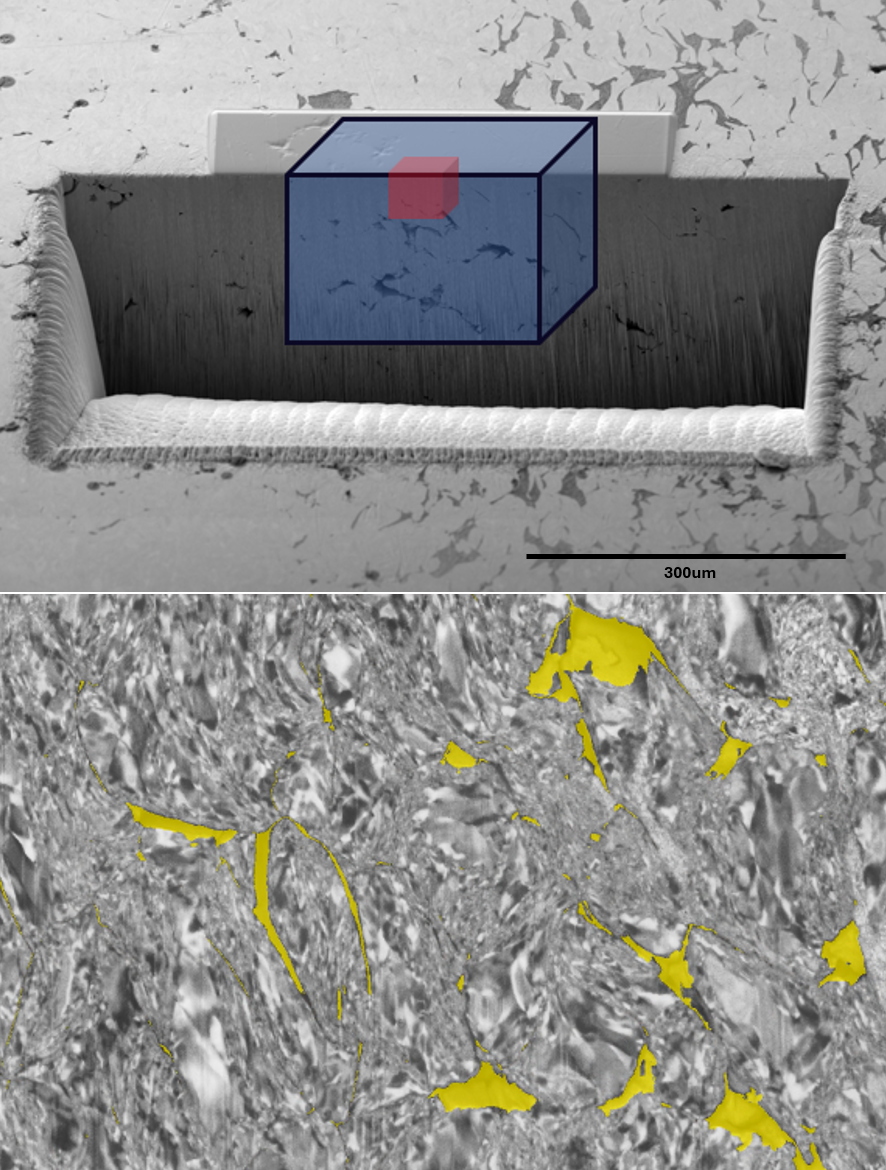
Image Credit: Thermo Fisher Scientific
AI-Assisted Segmentation
AI-assisted segmentation significantly reduced the time-to-results, permitting quicker and more efficient analysis. Deep learning algorithms facilitated the identification and segmentation of porosity features within the alloy, enhancing the overall assessment process.
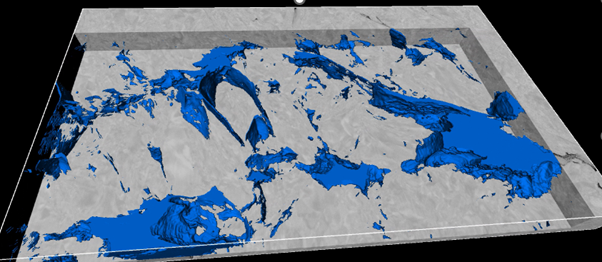
Image Credit: Thermo Fisher Scientific
Conclusion: Strengthening Characterization of FGMs with LAM SEM Imaging
The synergism of multi-scale SEM imaging, 3D plasma FIB tomography, and AI-assisted image analysis offers a powerful solution for accurately characterizing functionally gradient CSAM alloys.
This method aids in a comprehensive assessment, from macro to nanoscale, providing key insights into grain-to-grain bonding, porosity distribution, and the fine-tuning of processing parameters.
By employing Thermo Scientific's advanced imaging and analysis tools, researchers can better understand the structure and properties of FGMs and help bring about next-generation lightweight, regeneratively cooled rocket engines and other high-performance applications.
As additive manufacturing technologies continue to evolve, LAM SEM imaging and correlated analysis will play a critical role in driving innovation and safeguarding the success of FGMs across various industries.
References and Further Reading
- Thermo Scientific. (2024) Available at https://www.thermofisher.com/.
- Wei, Q., et al. (2022). Crack Types, Mechanisms, and Suppression Methods during High-energy Beam Additive Manufacturing of Nickel-based Superalloys: A Review. Chinese Journal of Mechanical Engineering: Additive Manufacturing Frontiers, 1(4), p.100055. https://doi.org/10.1016/j.cjmeam.2022.100055.
- Maps 3 Software Visual context for high-resolution microscopy Correlate data across optical, SEM, FIB-SEM and TEM instruments for high-throughput data collection. (n.d.). Available at: https://assets.thermofisher.com/TFS-Assets/MSD/Datasheets/MAPS-3-Datasheet.pdf [Accessed 9 Nov. 2024].
- Thermofisher.com. (2024). Avizo Software | Avizo2D Software | Thermo Fisher Scientific - US. [online] Available at: https://www.thermofisher.com/ca/en/home/industrial/electron-microscopy/electron-microscopy-instruments-workflow-solutions/3d-visualization-analysis-software/avizo-materials-science/avizo-2d-software-materials-characterization.html [Accessed 9 Nov. 2024].
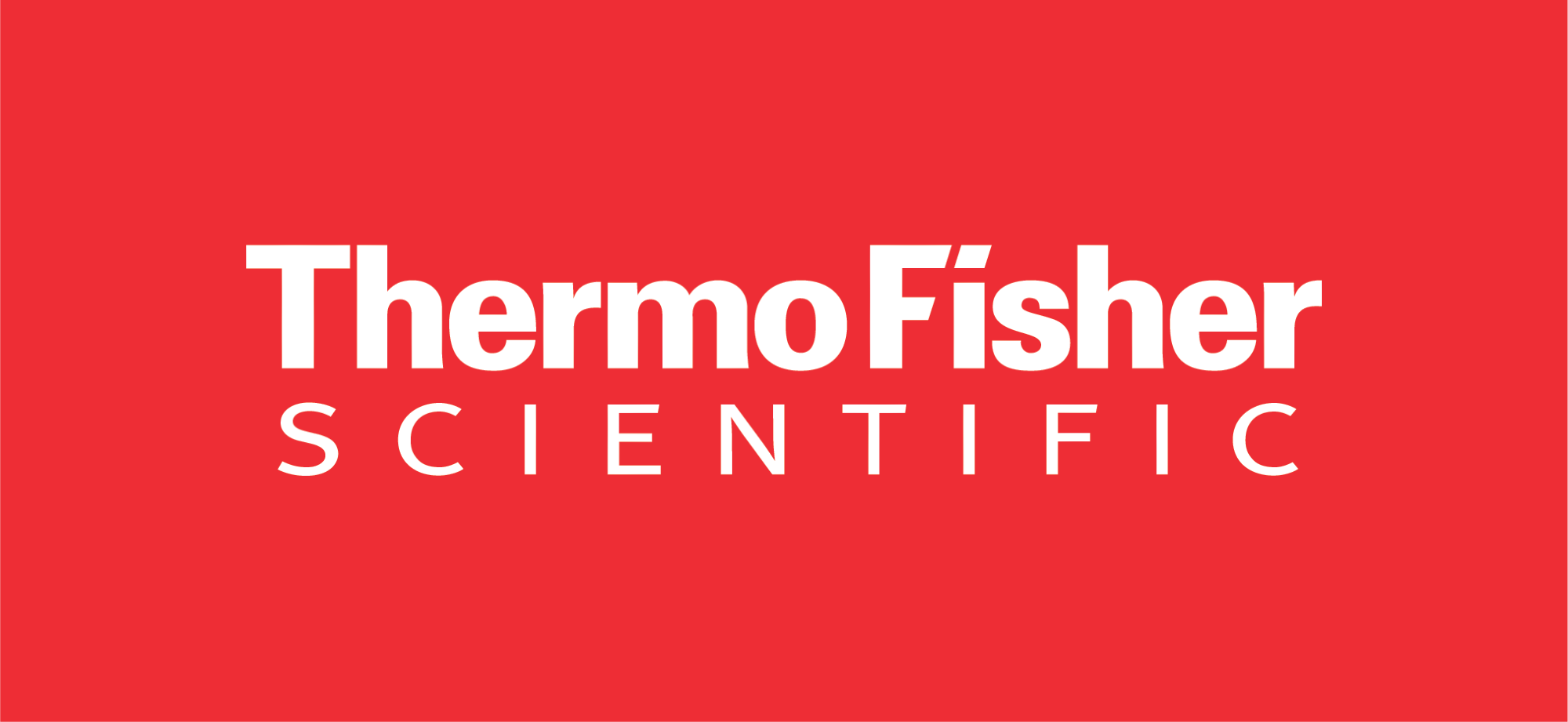
This information has been sourced, reviewed, and adapted from materials provided by Thermo Fisher Scientific – Electron Microscopy Solutions North America.
For more information on this source, please visit Thermo Fisher Scientific – Electron Microscopy Solutions North America.