Each time a gelcoat delivery arrives, it is crucial to review the order details and shipping advice for:
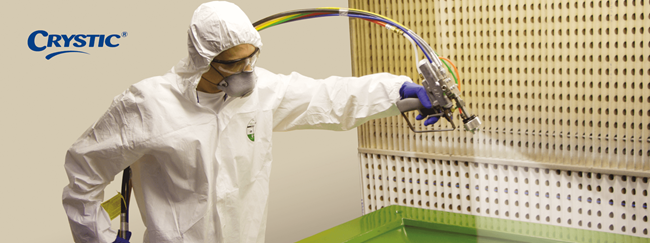
Image Credit: Scott Bader Company Ltd.
- Packing condition
- Correct amount
- Product code: brush, color, spray, or type
- Batch number
Always store the catalyst away from the resin and gelcoat.
Storage
- Store in a different storage room away from direct sunlight
- Store stock in its original kegs and drums, with caps and lids closed tightly
- Ensure kegs and drums sit on well-maintained pallets
- Observe product shelf life and rotate stock regularly
- Store under 20 °C. If storage is cold, the product must be adjusted to an ambient temperature (18–25 °C) before use
Mold Preparation
Each mold requires equal care and attention as the gelcoat to attain the optimal finish. This can be achieved by:
- Checking the mold for damage and cleaning thoroughly to eliminate debris, dust, or loose contaminants
- Applying a suitable release agent to the clean mold’s surface, following the instructions attentively
- Ensuring the area utilized for gelcoating is dust-free
- For new molds, ensure the surface is sealed with a suitable mold sealer before applying the chosen release agent
Material Preparation
- Ensure the drums or kegs collected from storage are in good condition and free from damage before opening
- Check the product code for the correct color and type
- Ensure enough of the product has been mixed relative to spray or brush the mold in one session to ensure even and consistent thickness
- With a low-shear mechanical mixer, mix the gelcoat each day before use in its original keg or drum, and leave it to stand for 10 minutes to allow time for the thixotropy to recover
- Before using, ensure the gelcoat is at its optimum working temperature of 18–25 °C (the absolute minimum temperature is 15 °C)
- Use a clean pail if the gelcoat is decanted from its original packaging
Always wear protective goggles, clothing, and gloves.
Checking Spray Equipment
Just as with molds, all equipment should be well-maintained to attain optimal results, including spray equipment if it is being used:
- Ensure filters are clear and clean
- Select a suitably sized spray gun, nozzle and angle to optimally suit the mold size and degree of complexity
- Check and adjust the spray pattern
- Use the lowest possible gun pressure that achieves a uniform spray fan pattern
- Verify the catalyst-to-gelcoat ratio
Spray Operator Protective Clothing
Whoever applies the gel coat should wear a protective disposable suit, face mask, and gloves while spraying. Anti-static protective clothing should also be worn wherever a risk of ignition from static electricity exists.
If a risk assessment suggests it is necessary, use a properly fitted, air-purifying, or air-fed respirator that complies with an approved standard. Respirator selection should be based on known or expected levels of exposure, the product’s hazards, and the respirator’s safe working constraints.
Working Area
Gelcoating must be undertaken in a purpose-built spray booth in a segregated part of the workshop that is equipped with:

Image Credit: Scott Bader Company Ltd.
Cleaning and Maintaining Equipment
If reusing brushes, clean them thoroughly with solvent in a dedicated space or cleaning room with proper ventilation to remove fumes. All residual gelcoat must be taken away from brushes to avoid corrupting a new batch when the brush is used again. Washed brushes should be stored and submerged in solvent inside a covered container.
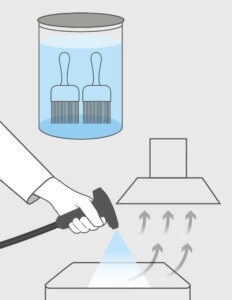
Image Credit: Scott Bader Company Ltd.
When applied to gel coats, brushes should be clean, dry, and free from solvent. Ensure bristles are dry before use to prevent moisture from transferring from brush to gelcoat.
Remove the spray gun nozzle and flush it with a cleaning agent. Clean nozzles and filters alongside all other components according to manufacturers’ guidelines to extend the equipment’s working efficiency.
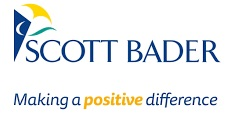
This information has been sourced, reviewed and adapted from materials provided by Scott Bader Company Ltd.
For more information on this source, please visit Scott Bader Company Ltd.