Using polymer binders to process metal and ceramic composite materials allows for the simultaneous injection of multiple small components, such as dental brackets, potentially replacing over 33 machining steps in production.1 This is just one of the many applications made possible by polymer-based printing and injection technologies utilizing powder and sintering methods.
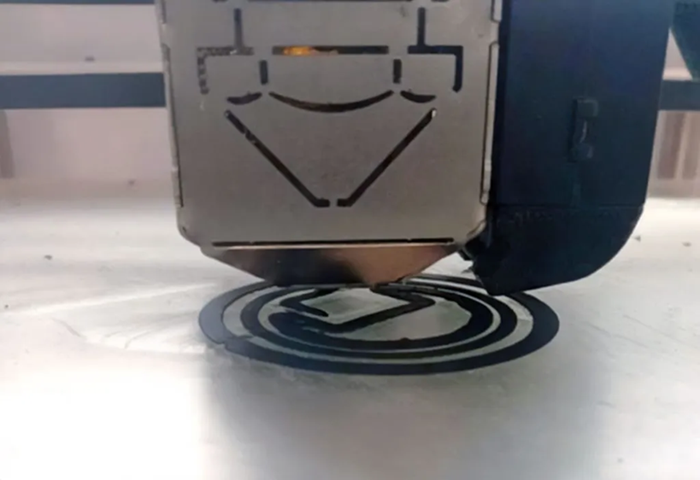
Image Credit: AIMPLAS
Advantages of Material and Processing
Metal and ceramic components are essential due to their specific properties, including hardness, thermal and electrical conductivity, high temperature, and corrosion resistance. Among the available processing methods, powder injection molding (PIM) and fused filament fabrication (FFF) are particularly notable for their versatility.
These techniques enable the production of complex metal and ceramic parts to produce high performance at reduced costs, especially for large-scale manufacturing. Thermoplastic polymers play a vital role in facilitating these processes.
Advantages of These Production Processes
These methods use a temporary thermoplastic binder to carry a heavy load of metal and ceramic powders during injection molding and printing. After thermal processing in a furnace, the polymer degrades and fuses with the solid particles through sintering, resulting in the final metal and ceramic components.
The process begins with the development of a feedstock, a composite of powder and polymer binder. This feedstock is molded like plastic, either through injection molding or by extruding filaments for printing. The resulting parts, known as green parts, undergo a debinding process to create brown parts, which contain enough polymer to maintain cohesion during sintering.
During the sintering stage, the brown parts fuse to reduce porosity and achieve the desired density and properties of the metal and ceramic materials.
The Essential Role of the Polymer Binder
Though the binder system typically comprises less than 15% by weight of the feedstock, it is critical for a defect-free manufacturing process. Its functions include:
- High powder content: Minimizes deformation during debinding and sintering, balancing the solid load with the flow characteristics of the polymer system.
- Sufficient rigidity: Prevents deformation during handling and thermal treatments.
- Flexibility and rigidity in filament production: Ensures smooth feeding into 3D printers without issues like buckling or tearing.
- Controlled degradation: The binder must degrade progressively without deforming parts, necessitating a carefully balanced mix of polymers and additives.
The binder system typically consists of four components: flexible polymers, backbones, plasticizers, and additives. Each contributes specific properties such as flow, rigidity, and compatibility with powders.
Table 1. Properties provided by the binder system to printable and injectable materials. Source: AIMPLAS
Property |
Composition for Printing |
Composition for injection |
Flexibility |
Flexible component
40-70 %vol.
Mainly thermoplastic elastomers |
– |
Flexibility |
Fluidising component
0-10 %vol.
Waxes, low molecular weight polymers |
Fluidising component
15-50 %vol.
Waxes, low molecular weight polymers |
Rigidity |
Backbone component
0-50 %vol.
Mainly polyolefins |
Backbone component
15-50 %vol.
Mainly polyolefins |
Compatibility |
Additives
0-5 %vol.
Compatibilisers, dispersants |
Additives
0-5 %vol.
Compatibilisers, dispersants |
Applications
Various successful applications highlight the versatility of these methods, including:
- Aerospace: Injection molding of small compressor blades for Rolls-Royce engines, such as those used in the Pearl 15.
- Automotive: Optimization of oil spray coolers, reducing machining steps for angled cavities.
- Consumer Electronics: Over 500 million smartphone camera protectors have been produced since 2016 using this technology.
- Biomedical: In the production of dental brackets, a single injection step replaces more than 33 traditional machining steps.
![Examples of parts processed through indirect methods using thermoplastic binders [1, 6]: a) Compressor blades for the Rolls-Royce Pearl 15 aircraft engine. b) Oil spray cooler. c) Camera protector. d) Alumina nozzle. e) Dental brackets](https://www.azom.com/images/Article_Images/ImageForArticle_24422_17456505972166777.png)
Figure 2. Examples of parts processed through indirect methods using thermoplastic binders 1, 6: a) Compressor blades for the Rolls-Royce Pearl 15 aircraft engine. b) Oil spray cooler. c) Camera protector. d) Alumina nozzle. e) Dental brackets. Image Credit: AIMPLAS
Contribution to Current Challenges
AIMPLAS offers the necessary facilities for compounding, characterization, injection molding, and 3D printing to develop materials suitable for these applications. Given the critical nature of the binder system, designing new metal and ceramic materials requires careful adjustments to meet flow characteristics, molding requirements, and the debinding process.
With their expertise, AIMPLAS supports the development of polymers compatible with various powder materials, ensuring that the feedstock fulfills all processing requirements while addressing the challenges of 3D printing, metals, and ceramics.
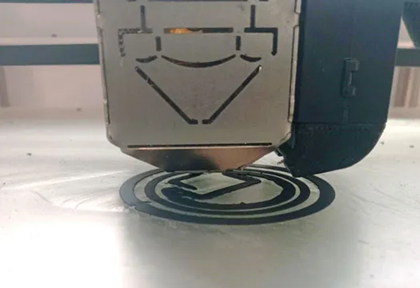
Figure 3. Printing process of polymer matrix material with ceramic filler. Image Credit: AIMPLAS
References and Further Reading
- Huff, S. de OrthoOrganizers (Ed.), Conferencia PIM 2000 “PIM Producers”, State College, Penn State, 2000.
- Loh, N.H., Tor, S.B. and Khor, K.A. (2001). Production of metal matrix composite part by powder injection molding. Journal of Materials Processing Technology, 108(3), pp.398–407. https://doi.org/10.1016/s0924-0136(00)00855-4.
- Naranjo, J.A., et al. (2021). A novel printable high-speed steel filament: Towards the solution for wear-resistant customized tools by AM alternative. Journal of Materials Research and Technology, 11, pp.1534–1547. https://doi.org/10.1016/j.jmrt.2021.02.001.
- Gonzalez-Gutierrez, J., et al. (2018). Additive Manufacturing of Metallic and Ceramic Components by the Material Extrusion of Highly-Filled Polymers: A Review and Future Perspectives. Materials, 11(5), p.840. https://doi.org/10.3390/ma11050840.
- Joamn Gonzlez-Gutirrez, Beulke, G. and Igor Emri (2012). Powder Injection Molding of Metal and Ceramic Parts. InTech eBooks. https://doi.org/10.5772/38070.
- Powder Injection Moulding International. (2016). PIM International magazine archive for MIM & CIM Industries. (online) Available at: https://www.pim-international.com/powder-injection-moulding-international-magazine-archive/ (Accessed 26 Apr. 2025).
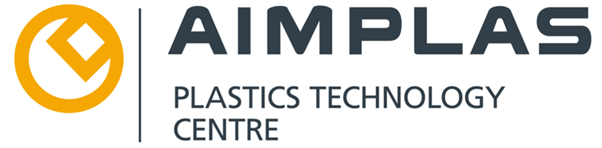
This information has been sourced, reviewed and adapted from materials provided by AIMPLAS.
For more information on this source, please visit AIMPLAS.