A persistent challenge in research and development (R&D) is the "Valley of Death", which illustrates the critical gap between basic research and the commercialization of a product or technology. This term highlights the difficulties and risks of translating laboratory innovations into market-ready solutions. Typically, private industry invests significantly in new technologies only after they are well-established and supported by viable business models.
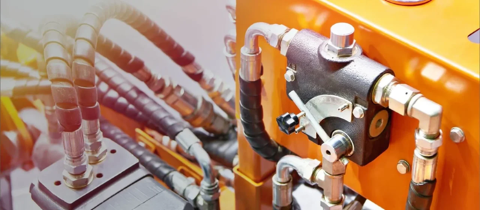
Image Credit: AIMPLAS
The plastics market is experiencing continuous growth, with a global value of $624 billion in 2023 and a compound annual growth rate (CAGR) of 3.4%. This market encompasses:
- Sustainable plastics and bioplastics (e.g., biopolyesters, biodegradable polymers), with a CAGR of 21.3%, projected to reach a market value of $20.9 billion by 2028.
- High-performance plastics (e.g., polyamides, polyimides, fluoropolymers), which have a CAGR of 9.5% and an expected market size of $59 billion by 2032.
Significant advances in R&D have been made in bioplastics and high-performance plastics, focusing on creating more sustainable materials with enhanced properties suitable for various applications in the plastics industry.
For developing innovative polymers—those with improved characteristics and sourced from unconventional materials—pilot plant development is essential. This stage transitions achievements from laboratory scale, often measured in grams or a few kilograms, to multi-kilogram production in a pilot plant, allowing for demonstrations of industrial-scale production in tons per year.
Plastics Research and Chemical Recycling
The chemical recycling market is rapidly advancing as a key segment within sustainable waste management and circular economy practices. Unlike mechanical recycling, which compromises polymer quality with each cycle, chemical recycling breaks down plastic waste into its basic units (monomers) and other valuable chemicals, facilitating the production of high-quality materials comparable to virgin polymers.
In 2023, the global market for chemical recycling of plastics reached $14.82 billion, with a projected CAGR of 9.4% from 2024 to 2030. Key materials targeted for this process include polyethylene terephthalate (PET), polyurethanes (PUR), and polyamides like nylon.
Chemical recycling involves two main steps:
- Depolymerization: Breaking down the polymer into its monomers.
- Repolymerization: Reassembling monomers into polymers.
Solid-state polymerization (SSP) is a particularly noteworthy polymerization technology. This thermal process, applied after initial polymerization, enhances the molecular weight of polymers through solid-state reactions without melting them.
For materials such as PET and polyamides, SSP is crucial for improving intrinsic viscosity and mechanical properties, making recycled polymers suitable for high-performance applications like food-grade packaging and engineering plastics.
SSP is essential for producing high-quality recycled polymers that comply with stringent regulatory and industrial standards. As demand for sustainable materials increases, SSP provides a viable solution to enhance the properties of recycled polyesters such as PET and polyamides, thus broadening their applications and supporting the growth of chemical recycling markets.
AIMPLAS: Bridging the Valley of Death
AIMPLAS’s pilot plant capabilities serve as a bridge across the Valley of Death. The pilot plant for chemical processes facilitates the scaling of laboratory results to near-commercial production while assessing feasibility, paving the way for industrialization.
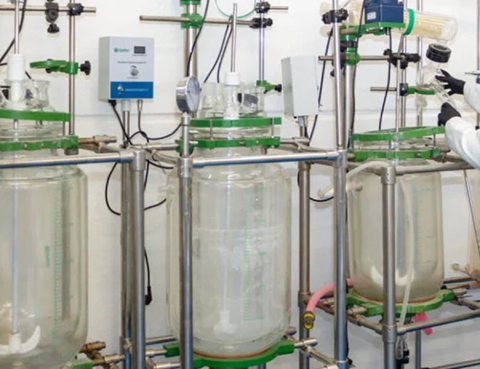
Image Credit: AIMPLAS
The Pilot Plants Feature Two Main Types of Reactors:
- Glass reactors: Designed for reactions under moderate pressure and temperature, these reactors have capacities ranging from 4 to 200 L and can reach temperatures of up to 300 °C using thermal oil jacketed cookers. They are suitable for processes requiring inert atmospheres.
- Steel reactors: For higher pressure and temperature conditions, AIMPLAS employs AISI-316L stainless steel autoclaves with 10 to 100 L capacities. These reactors are equipped with mechanical agitators and electric heating, allowing for temperatures up to 300 °C and pressures of up to 50 bars. They are ideal for producing high molecular weight and high-viscosity polymers like polyesters and polyamides.
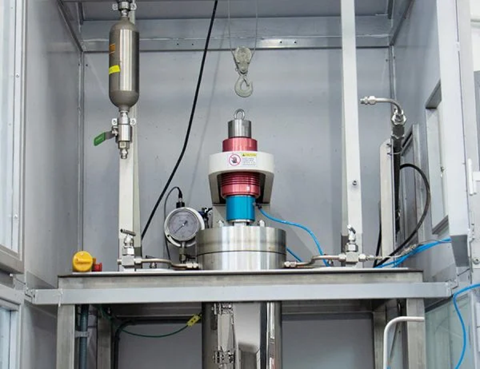
Figure 2. Steel reactors with capacities of 10, 20 and 100 L. Image Credit: AIMPLAS
Following polymerization, AIMPLAS can process the resulting polymers in-line into filaments or pellets, preparing the materials for direct use in extrusion and other applications.
Regarding solid-state polymerization (SSP), AIMPLAS’s pilot plant includes rotary equipment capable of processing batches of polyester such as PET up to approximately 10 kg, efficiently enhancing properties for subsequent applications.
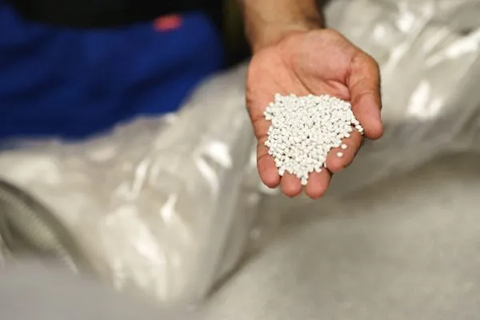
Image Credit: AIMPLAS
AIMPLAS is dedicated to adding value to the plastics industry and society. By utilizing pilot plant scaling capabilities aimed at industrial implementation, AIMPLAS assists companies in optimizing processes for developing innovative and sustainable polymers.
The organization supports R&D as well as regional and national enterprises in addressing challenges related to decarbonization, hydrogen utilization, and catalysis, fostering innovation and sustainability in the plastics sector.
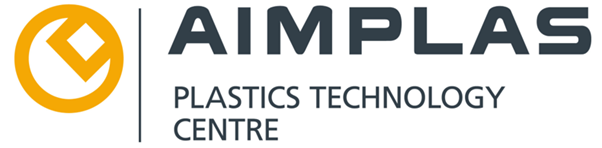
This information has been sourced, reviewed and adapted from materials provided by AIMPLAS.
For more information on this source, please visit AIMPLAS.