In this interview, AZoMaterials speaks with Dr. Nikhil Gupta, Professor of Mechanical and Aerospace Engineering at New York University and Dr. Kaushik Yanamandra, Applications Development Engineer at Zeiss Microscopy, about how X-ray microscopy and machine learning techniques are transforming materials research and failure analysis.
Can you please introduce yourselves and your roles at your respective organizations?
Nikhil Gupta: I’m a Professor of Mechanical and Aerospace Engineering at NYU Tandon School of Engineering where I lead the Composite Materials and Mechanics Lab. My research focuses on syntactic foams, metal matrix composites, and non-destructive evaluation techniques to better understand material properties and behavior.
Kaushik Yanamandra: I’m an Applications Development Engineer at Zeiss Microscopy. I focus on developing applications for engineering materials research. My work involves advancing imaging techniques like X-ray microscopy (XRM) and integrating machine learning tools to extract meaningful insights from imaging data.
Why does microscopy matter in engineering material characterization?
Nikhil Gupta: Materials behave differently at different scales, and microscopy helps us bridge the gap from macro to micro or nano, for example.
An important aspect is tailoring the microstructure to enhance material performance. Microscopy plays a vital role here—it supports the micro-engineering of alloys and enables near-line quality analysis, quality control, and informed decision-making in manufacturing.
In other words, microscopy isn’t just about capturing images; it’s about making better materials faster. But to truly understand how materials function, we need to study them across multiple length scales, from centimeters down to nanometers, to uncover what matters most at each level.
Why is XRM such a valuable tool in engineering materials characterization?
Kaushik Yanamandra: XRM helps us bridge the gap between macroscopic structural features and nanoscale phenomena. With its dual-stage magnification—geometric and optical—XRM achieves sub-micron resolution in bulk specimens without the need for sectioning. That means we can detect fine details like intragranular cracks, porosity, precipitates, and inclusions, even in dense materials.
These microstructural features often play a key role in how materials perform under stress, which makes XRM a powerful tool for failure analysis, process optimization, and quality control in advanced engineering materials.
What are some unique advantages of XRM compared to conventional microCT systems?
Kaushik Yanamandra: The main advantage is resolution independence from sample size.
In traditional microCT, resolution is limited by how close the detector and source can be placed relative to the sample, which is governed by geometric magnification. ZEISS XRM introduce a scintillator that converts X-rays to visible light and applies optical magnification after that, allowing large samples to be imaged at high resolution. Additionally, XRM offers superior phase contrast and is better suited for imaging multiphase materials or materials with subtle density differences.
How does the DeepRecon Pro module enhance XRM data quality?
Kaushik Yanamandra: DeepRecon Pro is part of our Advanced Reconstruction Toolbox and utilizes a noise-to-noise convolutional neural network. It is trained on raw 2D projections to distinguish between image features and noise, effectively enhancing the signal-to-noise ratio. This allows us to significantly reduce exposure times and projection counts without compromising image quality. For example, scans that previously took 9 hours can now deliver similar detail in under an hour. It also corrects for beam hardening and ring artifacts that traditionally degrade reconstructions.
Can you give examples where DeepRecon Pro made a significant difference?
Kaushik Yanamandra: Certainly. In ceramic matrix composites, DeepRecon Pro enabled us to reduce scan duration from 9 hours to 1 hour while preserving contrast and resolution necessary for feature segmentation.
In dense nickel-based metal matrix composites, we applied DeepRecon Pro to visualize titanium carbide and graphite phases that standard FDK reconstruction missed or rendered indistinct due to high background noise. We also used it on aluminum syntactic foams to visualize wall porosity in embedded hollow spheres. These internal features are critical failure initiators, and identifying them non-destructively is a game-changer.

DeepRecon Pro with ImageClarity.
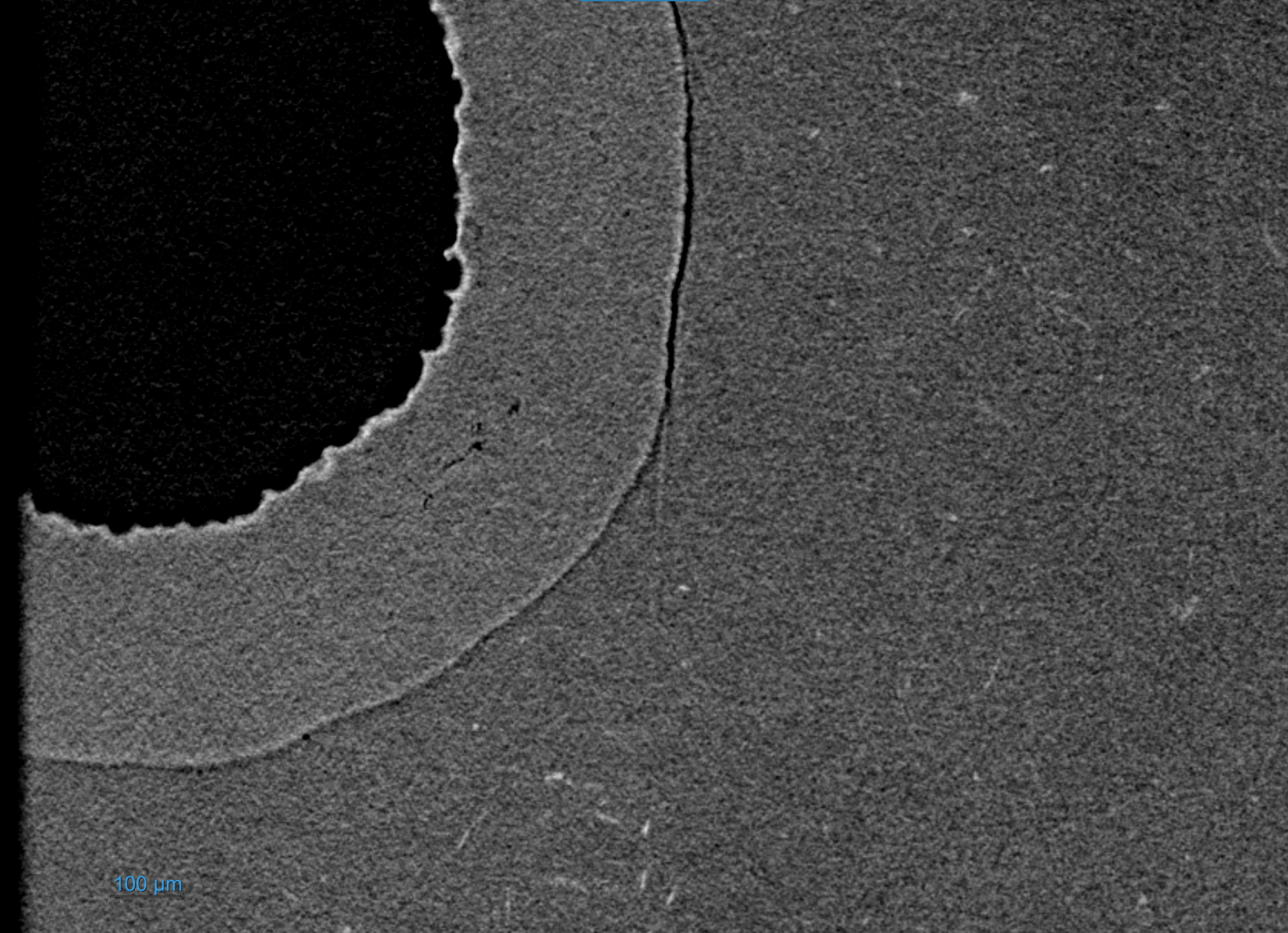
Standard FDK.
In Metal Matrix Syntactic Foam, porosity in the metal matrix is filled with hollow spheres of Aluminum oxide reducing the weight over a conventional metal of the same size and shape. It is crucial to observe fine features such as porosity to predict or assess the sample's quality and mechanical strength. DeepRecon Pro ImageClarity (top) enables researchers to see more of these features than traditional FDK reconstruction (bottom). Image credit: Dr. Nikhil Gupta, Professor at New York University Tandon School of Engineering
Dr. Gupta, how are you applying XRM in your research at NYU?
Nikhil Gupta: We focus on metal matrix syntactic foams containing microscale hollow ceramic particles. These structures are susceptible to microcracks and porosity, especially within particle walls. Conventional scanning electron microscopy (SEM) is inherently destructive and only reveals surface or section-plane features.
XRM, especially enhanced with DeepRecon, gives us volumetric datasets at resolutions around 2 microns or better. We can identify particle fractures, evaluate wall thickness variability, and detect precipitates and microvoids. These insights allow us to model damage initiation and propagation mechanisms in three dimensions, which was not previously feasible.
What are the benefits of using XRM data for finite element modeling in your lab?
Nikhil Gupta: With conventional techniques, we idealized particles as perfect spheres or ellipsoids. Now, XRM allows us to import actual geometries, including particle wall thickness, orientation, and embedded defects. When these real-world geometries are meshed and simulated, we get much closer agreement between our models and experimental mechanical properties like Young’s modulus and yield strength.
We’ve seen up to 30% improvement in predictive accuracy. This capability is essential for developing reliable lightweight structures for aerospace, automotive, and energy applications.
Have you explored using XRM for in situ experiments?
Nikhil Gupta: Yes, we’ve conducted stepwise in situ compression tests, using XRM scans between mechanical load cycles to monitor damage evolution over time. This approach allows us to correlate crack initiation sites and particle fracture patterns with the material’s mechanical load history.
While real-time imaging isn’t yet practical due to current scan durations, even intermittent imaging has delivered high-value insights. We've been able to generate property maps that link particle wall thickness and porosity to specific mechanical failure modes—an invaluable resource for designing the next generation of syntactic foam composites.
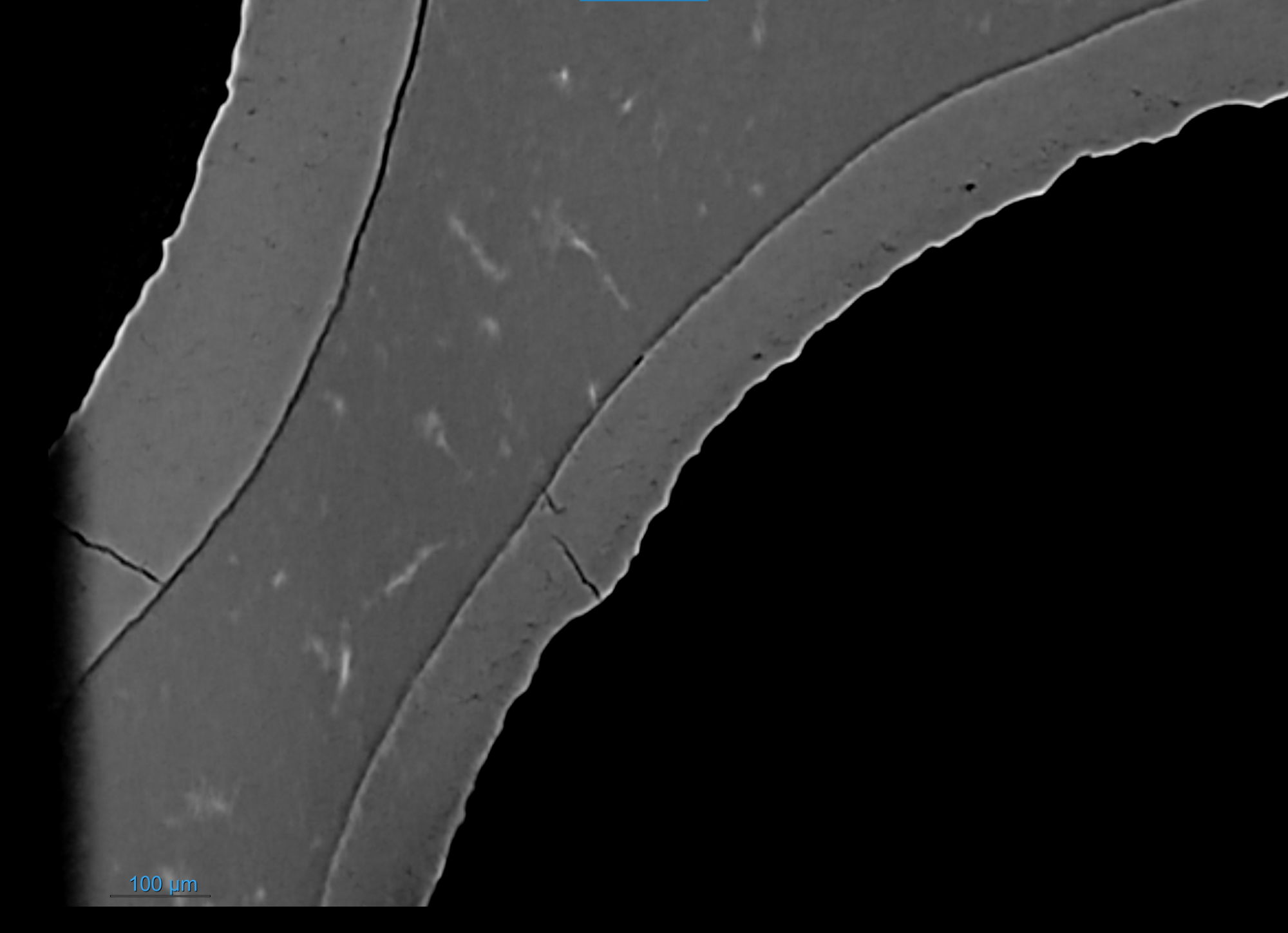
DeepRecon Pro with ImageClarity.
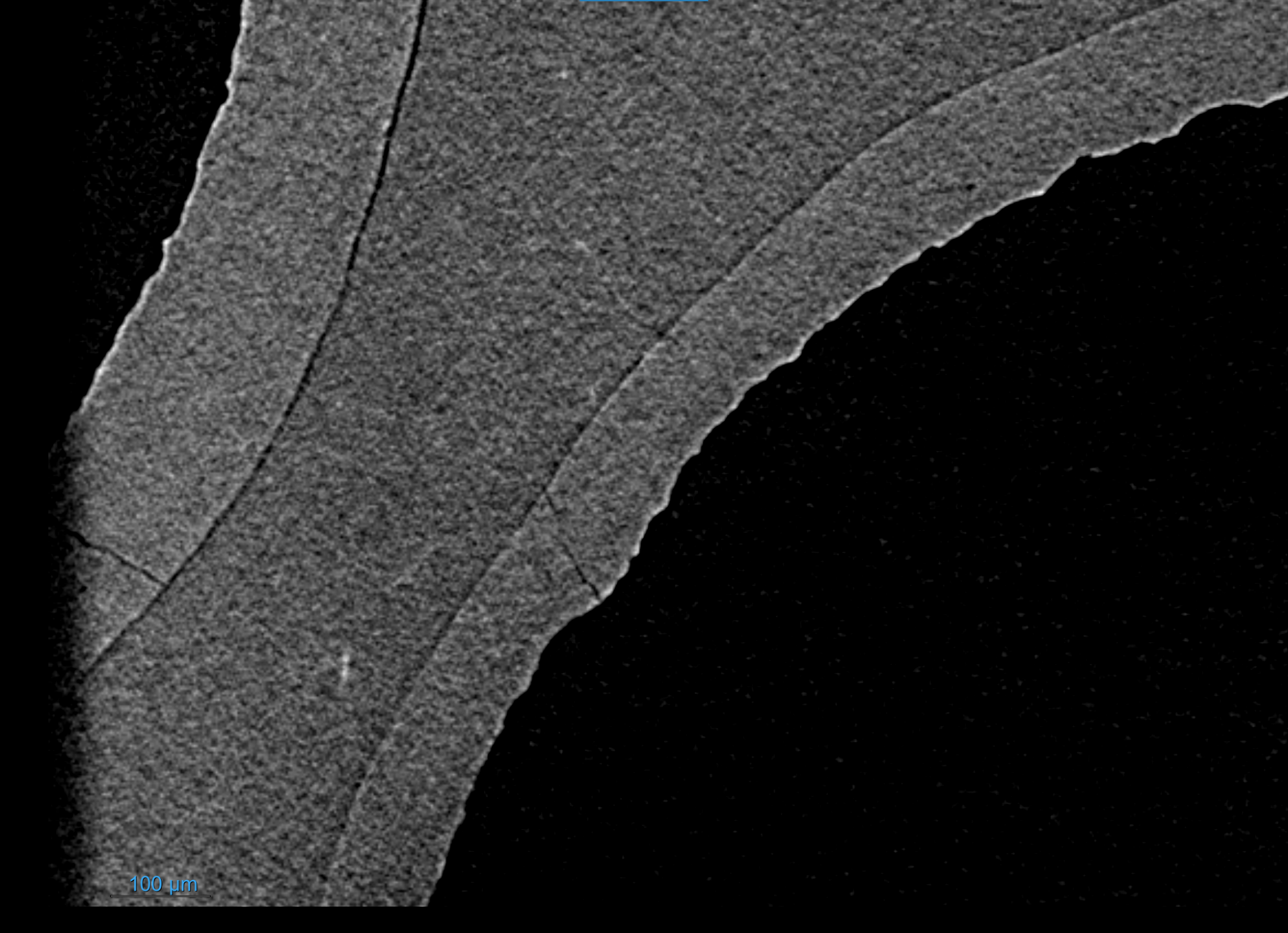
Standard FDK.
In the images above, we see the expanded number of features typically available with DeepRecon Pro Image Clarity (top) over standard FDK imaging (bottom). The cracking is especially clear with DeepRecon Pro. Image credit: Dr. Nikhil Gupta, Professor at New York University Tandon School of Engineering
What do you see as the future potential for XRM and AI-based DeepRecon in materials science?
Kaushik Yanamandra: The combination of XRM and AI is leading to more intelligent, high-throughput workflows. We’re currently working on developing user-guided and fully automated imaging protocols that integrate reconstruction, segmentation, and analysis. As processing power and detector sensitivity increase, real-time defect detection and live feedback during manufacturing could become feasible. DeepRecon and similar AI tools will continue to enhance resolution and reduce acquisition time, enabling broader use in production quality control.
Nikhil Gupta: These tools bridge the experimental–computational gap. We’re moving toward a future where we can build a digital twin of every physical specimen, simulate performance under various conditions, and validate against in situ test data. This will revolutionize materials R&D and significantly reduce development cycles for structural components.
As scan time reduces and image quality increases, we expect to see widespread adoption in industrial inspection settings, not just academic labs.
About Dr. Nikhil Gupta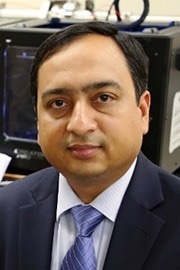
Dr. Nikhil Gupta is a Professor in the Department of Mechanical and Aerospace Engineering at NYU Tandon School of Engineering. He is a leading expert in syntactic foams and lightweight composite materials. Dr. Gupta received his Ph.D. in Engineering Science from Louisiana State University. He directs the Composite Materials and Mechanics Laboratory at NYU, where his research focuses on advanced manufacturing, materials characterization, and non-destructive evaluation. With over 250 peer-reviewed publications and seven issued patents, Dr. Gupta is a Fellow of ASM International and the American Society for Composites, and an influential voice in the field of advanced materials.
About Dr. Kaushik Yanamandra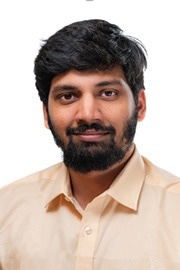
Dr. Kaushik Yanamandra is an Applications Development Engineer at Zeiss Microscopy, specializing in imaging techniques for engineering materials. He earned his Ph.D. in Mechanical Engineering from New York University and completed postdoctoral research in the School of Materials Engineering at Purdue University. His expertise lies in advanced X-ray microscopy and developing machine learning tools to improve materials characterization. He has over a decade of experience studying the mechanical behavior of materials and plays a key role in integrating AI with imaging to push the boundaries of non-destructive testing.
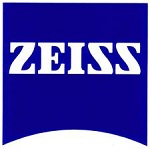
This information has been sourced, reviewed and adapted from materials provided by Carl Zeiss Microscopy GmbH.
For more information on this source, please visit Carl Zeiss Microscopy GmbH.
Disclaimer: The views expressed here are those of the interviewee and do not necessarily represent the views of AZoM.com Limited (T/A) AZoNetwork, the owner and operator of this website. This disclaimer forms part of the Terms and Conditions of use of this website.