Toray Advanced Composites specializes in designing and developing advanced composite materials for the industrial, aerospace, satellite and consumer products industries. Toray’s division, CCS Composites designs and fabricates compression molded parts, which are developed using sophisticated fiber reinforced composites. Compression molded parts from Toray are utilized in various commercial aircraft, jet engines, helicopters, satellite and nacelle structures.
.jpg)
Compression Molding Overview
Compression molded composite parts from CCS Composites offer an alternative solution to metal parts as they are lightweight and exhibit more strength and stiffness. Designers at Toray are capable of optimizing a metal component into an efficient composite design. In addition, CCS Composites can even mold parts from syntactic thermoset pastes where extremely high service temperatures or low dielectric strengths are needed.
.jpg)
Materials Used in Compression Molding
Compression molding is an extremely controlled procedure that employs accurate resin infused fiber reinforced tape developed with high, intermediate or standard modulus fibers. Resins can be either thermoplastic such as Nylon, PEEK, PEI, and PPS, or thermosets such as epoxy, BMI, and cyanate ester. Bulk molding compounds are typically developed by cutting these unitapes into fiber lengths that range between 1/8” and 1”. Fibers with longer lengths tend to have higher strengths, while fibers with smaller lengths enable more intricate structural details to be molded within the part.
.jpg)
.jpg)
However, sufficient skill is needed to develop the tool, optimize the part shape to fulfill the loading requisites of the part, and reduce post-molding machining processes. With innumerable material and processing alternatives, CCS Composites makes sure that right selections are made to satisfy the performance, cost and weight requirements of particular applications.
Typical Property Comparison
|
3AL-2.5V Titanium Alloy |
6061-T6 Aluminum Alloy |
MS-1A |
MS-1H |
MS-4A |
MS-4H |
Density (g/cc) |
4.5 |
2.7 |
1.55 |
1.52 |
1.49 |
1.52 |
Tensile Strength |
psi |
100,000 |
44,000 |
42,000 |
37,100 |
45,000 |
43,800 |
MPa |
689 |
303 |
290 |
256 |
310 |
302 |
Compressive Strength |
psi |
100,000 |
44,000 |
41,000 |
32,800 |
52,000 |
47,900 |
MPa |
689 |
303 |
283 |
226 |
358 |
330 |
Flexural Strength |
psi |
100,000 |
44,000 |
67,000 |
63,700 |
93,000 |
108,800 |
MPa |
689 |
303 |
462 |
439 |
641 |
750 |
Tensile Modulus |
msi |
15.5 |
10 |
19 |
10 |
9 |
6.2 |
GPa |
107 |
69 |
131 |
69 |
62 |
43 |
Compressive Modulus |
msi |
15.8 |
10.2 |
16 |
9.2 |
8 |
7.3 |
GPa |
109 |
70 |
110 |
63 |
55 |
50 |
Flexural Modulus |
msi |
15.5 |
10 |
13 |
10 |
7 |
9.3 |
GPa |
107 |
69 |
90 |
69 |
48 |
64 |
|
The Case for Compression Molded Parts
The comparison chart given above illustrates how numerous properties of Toray’s compression molding compounds contend directly with ordinary metals, and this is only part of the benefit.
.jpg)
.jpg)
The first figure represents a simple metal bracket, while the second figure shows that the latest composite bracket can be net molded thickly at the similar weight, including more thicker support areas close to the holes with rounded edges. The flexibility of the design ensures that a simple shape can be altered to make a lighter weight part which is molded directly. On the other hand, metals typically need intricate machining and in such cases continuous fiber composites would prove quite difficult to fill into intricate shapes. Moreover, injection molding compounds cannot deliver the same performance as they do not exhibit the mechanical properties.
Metal vs Composites
Titanium and steel are known to have a higher tensile strength. However, bulk molding compounds tend to surpass these metals in terms of specific strength, which accounts for stiffness and density and helps in developing robust components at a fraction of the metal weight.
.jpg)
Compression molded aircraft access doors with lightning strike outer surface.
Typical Advantages of Compression Molded Composites
- Dimensionally stable
- Substitute multiple simple parts into one intricate part
- Non-corrosive benefits (chemical resistance, galvanic protection)
- Higher performance, lighter weight, and lower cost than other metal parts
- Lower part labor content
.jpg)
Applications Where Compression Molded Parts Excel
- Intricate shapes that limit the use of continuous laminate composites; this results in lengthy process or high expenditure
- Metal/composite parts that have varying cross-sectional thicknesses or material customizing requirements
Toray Commercially Available Molding Compounds
Matrix |
Tg °F (°C) |
Product |
Typical Tensile Modulus (Msi) |
Name |
Fiber Modulus |
Epoxy |
375°F (190°C) |
MS-4H |
SM |
6 |
MS-1H |
IM |
10 |
327°F(164°C) |
MS-4A |
SM |
9 |
MS-1A |
HM |
19 |
MC1100 PPS |
194°F (90°C) |
MC1100 |
SM or IM |
TBD |
MC1200 PEEK |
290°F(143°C) |
MC1200 |
SM or IM |
TBD |
SM - Standard Modulus, IM - Intermediate Modulus, HI - High Modulus
Conclusion
In addition, compression molded parts significantly reduces tooling costs and make them a better alternative to metal parts.
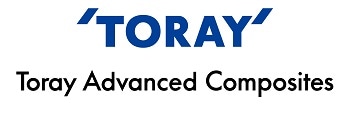
This information has been sourced, reviewed and adapted from materials provided by Toray Advanced Composites.
For more information on this source, please visit Toray Advanced Composites.