By Surbhi JainJun 7 2022Reviewed by Susha Cheriyedath, M.Sc.
In an article recently published in the journal Additive Manufacturing, researchers discussed the bonding processes between the deposit and the substrate of friction rolling additively-made hybrid aluminum alloys.
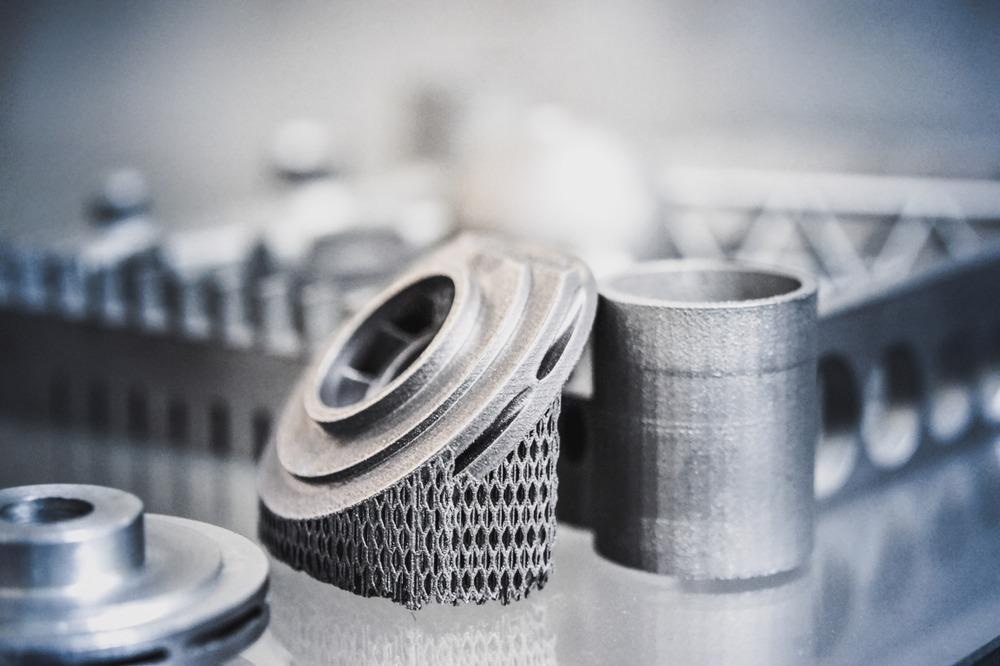
Study: Revealing the bonding mechanisms between deposit and substrate of the friction rolling additive manufactured hybrid aluminum alloys. Image Credit: MarinaGrigorivna/Shutterstock.com
Background
For usage in the aerospace and defense industries, high-strength aluminum alloys combine low density, high modulus and specific strength, high fatigue strength, exceptional fracture toughness, and superior corrosion resistance. However, traditional fusion-based additive manufacturing (AM) processes severely degrade the mechanical qualities of these alloys.
Solid-state friction-based additive manufacturing methods such as additive friction stir deposition (AFSD), friction stir additive manufacturing (FSAM), and friction surfacing (FS), have significant development capability and prospects for the development of high-strength aluminum alloys.
However, neither FSAM nor FS techniques can achieve continuous material addition, and AFSD requires expensive and specialized equipment. Friction rolling additive manufacturing (FRAM) is an innovative and low-cost solid-state technology that was recently created. This approach uses a rapidly rotating tool head to generate heat while also allowing for continuous material input. In order to better understand the solid-state manufacturing process, it is critical to study material flow behavior and the mechanism of bonding at the bonding contact.
About the Study
In this study, the authors used electron backscatter diffraction, 3D X-ray computed tomography, and transmission electron microscopy to demonstrate the mechanisms for FRAM-produced hybrid AA2319 and AA6061 aluminum alloys. Using a FRAM-produced hybrid material system and a multiscale characterization technique, the material flow behavior and mechanisms of interlayer bonding during FRAM were exposed.
The team used 2319 aluminum alloy welding wire as the tracer material and AA6061 as the substrate because the hybrid aluminum alloys could easily be recognized from one another. The essential principle of interlayer material mixing and material flow behavior was revealed at the macro-level by investigating the 3D shape of the interlayer using 3D X-ray computer tomography (CT).
The researchers examined the microstructure of the interface to elucidate the interlayer bonding behavior at the micro-level by using electron backscatter diffraction and transmission electron microscopy. Further, mechanical testing was used to confirm the hybrid material's bonding quality.
Observations
The hybrid sample's ultimate tensile strength (UTS) in the Z-direction was 225.9 MPa, which was comparable to that of AFSD-produced AA2219 samples. The UTS of the hybrid alloy, which was about 77.4%, was lower than that of 2319 feeder wire, which could be attributed to material softening produced by reciprocating deposition. Following FRAM, the grain size of AA 2319 was dramatically reduced compared to the original feeding wire, with an average grain size reduction of 300 to 5.2 µm.
Three conclusions were drawn on the quality of bonding between adjacent layers in FRAM. First, at the interlayer, material plastic flow and macroscopic migration behavior happened at the same time in both longitudinal and transverse directions, which generated a macroscopic mechanically interlocking nonplanar interface. The tool head's convex thread boosted material flow in the transverse direction, which made material mixing in the next layer easier.
Second, on both sides of the contact, substantial plastic deformation resulted in significant grain refinement. The sides of AA2319 and AA6061 had average grain size reduction rates of 98.3% and 95.9%, respectively. Third, complete metallurgical interface bonding was achieved by direct contact with no visible oxides.
A high-speed rotating tool head squeezed and sheared the materials at the interface during the FRAM process. Between the AA 2319 and AA 6061 alloys, material plastic flow and macroscopic migration behavior occurred simultaneously in the longitudinal and transverse directions, which generated a mechanically interlocked nonplanar contact. The thread shape of the tool head had a strong influence on material flow and mixing behavior at the interface.
Thread protrusion encouraged the lateral flow of plastic materials, which was advantageous for the mixing of interlayer layers and the formation of uneven surfaces. Grain refinement was substantial on both sides of the contact due to severe plastic deformation. AA 2319 and AA 6061 sides had grain size reduction rates of 98.3% and 95.9%, respectively. It was demonstrated experimentally that a direct contact interface without oxides could be formed between the alloys AA 6061 and AA 2319, which resulted in a strong metallurgical connection.
Conclusions
In conclusion, this study revealed the primary interface bonding processes by performing a multiscale evaluation of hybrid AA 2319 and AA 6061 aluminum alloys made by FRAM technology. The plasticized material first created thin and elongated grains under the shearing action of the tooltip, and subsequently, its interior shattered to form equiaxed and fine grains.
The authors believe that the findings of this study will aid in understanding the fundamental physical process of FRAM and will provide future recommendations for process parameter optimization and tool head design.
More from AZoM: How are PAT Techniques Used for Real-Time Particle Analysis?
Source
Xie, R., Liang, T., Shi, Y., et al. Revealing the bonding mechanisms between deposit and substrate of the friction rolling additive manufactured hybrid aluminum alloys. Additive Manufacturing 102942 (2022). https://www.sciencedirect.com/science/article/abs/pii/S2214860422003384
Disclaimer: The views expressed here are those of the author expressed in their private capacity and do not necessarily represent the views of AZoM.com Limited T/A AZoNetwork the owner and operator of this website. This disclaimer forms part of the Terms and conditions of use of this website.