Advanced rotary tube furnaces are generally used in the thermal processing of powders but are also used for processing granular materials, irregularly shaped materials and large agglomerates. Under suitable conditions, the rotary tube furnace will be more energy efficient when compared to that of the pusher tunnel furnace.
Since a significant amount of energy is required to heat the pusher tunnel furnace, the rotary’s rotating tube is used to offset the total energy consumption. This article describes how the use of tube internals allows the rotary furnace to be more energy efficient.
When tube internals are used in a rotary furnace, it results in improved radial mixing, increased heat transfer surface area, controlled gas flow direction, improved gas solid interactions and also controlled material dwell time. These factors not only increase the capacity of the unit for a given furnace volume or reduce the required residence time, but also enhance the quality of the product and control help in controlling uniformity and quality.
Surface Area
In the rotary furnace, the function of the tube internal is to enlarge the surface area for heat transfer. The tube internals located in the heating section of the rotary furnace are sustained at a lower temperature when compared to the tube wall and a higher temperature than the process material thus offering another surface other than the process wall’s inner tube for transferring heat to the product.
This improved heat transfer area can be considered as the plates or fins of a heat exchanger. In other words, the total heat transfer of the exchanger will increase when there is an increase in the plates of the heat exchanger.
The increased surface area not only helps to heat the process material but also helps to cool the product after processing. However, internals are not used in the overall design of most rotary tube cooling chambers. These chambers simply serve as water cooled jackets around the exterior of the rotary tube, which is not always efficient.
.jpg)
Figure 1. Cooling tubes.
Image Credit: Harper
By increasing the surface area within the tube, there will be more cold surfaces and the material will cool more efficiently. In addition to using the enlarged surface area of a tube internal to conduct heat via the tube wall, some designs also enable the cooling water to penetrate into the internals. This helps in increasing the total cooling efficiency (Figure 1).
In this design, it can be seen that the pipes running via the process area are open to the exterior of the tube in such a way that the cooling water flows easily without wetting the process material. This increases the cooling surface without depending only on the heat transfer via conduction in the rotary tube wall.
Radial Mixing
In advanced materials, product homogeneity and consistency is very important. When materials are processed in a rotary furnace equipped with specific tube internals like flat bar lifters (Figure 2), consistency can be significantly enhanced by augmenting the radial mixing of the material. When the flat bar lifter is sized below the height of the material bed, it will promote agitation in the material bed as it is transferred by the rotary tube, thus increasing envelopment.
.jpg)
Figure 2. Radial mixing flight.
Image Credit: Harper
Similarly, a greater bed turn-over can be achieved if the flat bar lifter is larger than the material bed, although this may add to the processing costs. There is always a possibility of getting reduced yields of material in case the velocity of the processing gas is too high or the particle size of the material is too small.
Enhanced Gas-Solid Interaction
In many processes, such as boron nitriding and aluminum nitriding, the reaction gas is very important. One way to determine whether the reaction has occurred or not is to ensure that there is consistent contact between the material bed and the reaction gas. When this phenomenon is known, the tube fill percentage need not always be reduced to ensure gas infiltration via the entire bed to acquire the required gas-solid reaction.
Moreover, when the rotary furnace is equipped with unique lifters, material is brought up along the walls of the tube to a specific point of discharge where it is dropped via the process gas. This not only increases the time exposure but also increases the amount of material exposed to the process gas.
Gas Flow
Depending upon the reaction, any contact between the end product and process off-gases can impede product quality. In some situations, processing is also hindered when there is contact between the off-gas and the raw feed material. If this presents an issue, an Archimedes screw or a solid core helical flight can be strategically placed (Figure 3). These tools create a sufficient barrier to prevent migration of gases.
.jpg)
Figure 3. Continuous helical flight.
Image Credit: Harper
Material Flow
A rotary furnace serves as a suitable thermal instrument for powder processing and can also be used for irregularly shaped materials or large agglomerates. In the absence of internal flights in the rotary tube, the agglomerates and irregularly shaped materials can separate on their own owing to the tumbling flow in the tube.
In order to control this phenomenon, an Archimedes screw can be used which is continuous across the entire tube length. In such a scenario, the angle of the rotary tube does not play a major role in ascertaining the material’s residence time; instead the pitch of the flight and the tube rotation determine the precise residence time.
Current Processing Methods
Harper International, a company specializing in custom thermal processing equipment, has collaborated with U.S. Demil to design a unique rotary tube furnace. This furnace was used in the demilitarization of obsolete, excess and unserviceable weapons for safety and environmental purposes. The success of this project has been attributed to the unique design of the tube internals, where considerations were taken with respect to the controlled migration of material via the tube, while controlling the flow of gas through the reaction area and imposing a key reaction location inside the rotary tube.
Conclusion
Thus, functional tube internals can improve not only the processing efficiency but also enhance the product quality. Rotary tubes which lack internal flights are less efficient and also consume a significant amount of energy.
About Harper International
Harper International is a global leader in complete thermal processing solutions and technical services essential for the production of advanced materials. From concept to commercialization, from research scale to full production line operations, Harper is perpetually on the cutting edge of the most innovative furnace and oven designs in the world. For decades, they have pioneered some of the most unique, customized systems available, with a focus on processing materials at high temperatures up to 3000°C and in non-ambient atmospheres.
Harper serves advanced, cutting-edge material markets including Fibers & Filaments, Powders, Metal Oxides, Technical Ceramics, Rare Earths, Graphene, Energy Device Materials and Nuclear Materials. Their support to these emerging industries begins in early stages of research and development, whether at corporate R&D centers, universities, government institutions, or start-ups. Harper is a partner through the entire development process assisting in the scale up and commercialization of advanced materials that will change our everyday lives.
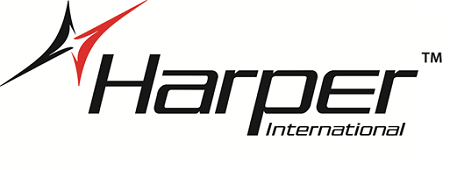
This information has been sourced, reviewed and adapted from materials provided by Harper International.
For more information on this source, please visit Harper International.