Conventionally sintered ceramics such as porcelain or stoneware are subjected to a viscous flow sintering process.
Surface tension is the key driving force of the process resulting in decreased overall surface area by aggregating discrete, separate glassy phases into one cohesive body. The glassy phase viscosity moderates the speed of this process.
Most sintering models in literature suggest ideal particle geometries, are restricted to solid-state sintering of a single component and analyze systems in which diffusion is dominant for material transport. In this sector, experimental methods are the most effective route to study sintering and optimize industrial processes.
Experimental Methods
Traditional thermal analysis techniques such as differential scanning calorimetry (DSC), differential thermal analysis (DTA), differential scanning calorimetry (DSC) and thermogravi-metric analysis (TGA) cannot offer full information about the sintering rate or the sintering onset temperature. The sintering process is described best by measuring the dimensional change, which is a direct representation of the densification process.
In the early part of the 1990s, heating microscopy was intensively applied for studying sintering in a number of material systems. Optical measurement methods are ideal for fast-firing sintering. Optical dilatometry enables experiments that mimic fast-firing processes and capture the large dimensional changes and very low forces that are present.
The development of the double-beam optical dilatometer significantly improved the heating microscope technique. The optical dilatometer was designed and patented by Expert System Solutions in 2001. There are two independent optical systems focusing on either end of the specimen optimizing sensitivity and precision compared to the single microscope methodology. The instrument is based on the double-beam concept.
The first optical path is used for measuring the top of the specimen. Alignment is continuously maintained using a stepper motor. The second optical path is focused on the sample holder and acts as a reference beam to correct the mechanical drift of the sample holder.
.jpg)
Figure 1. Measuring scheme of the non-contact double beam optical
Optimizing the Sintering Process
The proposed experimental procedure aims at optimizing fast-firing processes by determining the optimal top firing temperature offering complete densification without swelling with the minimum processing time. Specimen preparation is done with a laboratory press equipped with a steel die, which yields a 15x5x5mm sample. Any standard laboratory procedure can be used for preparing the powder or it can be taken directly from the production line.
Specimen preparation must be done very carefully as the measurement is impacted by humidity, powder preparation and specific pressure. The pressing of samples are done with a specific pressure of 400 or 500kg/cm2, based on the normal industrial practice, but they can be cut from an industrially prepared ware. The sintering tests are performed on materials wet milled and dry pressed with 5% humidity at 400kg/cm2. Since the specimen is subjected to a very rapid heating cycle, they need to be completely dry, or they could explode inside the dilatometer kiln, similar to the industrial firing kiln. Results were obtained for a sample of technical porcelain using an optical dilatometer. Three different testing phases were used for studying sintering behavior.
Determining the Temperature of Maximum Sintering Speed
This test is done with a heating rate of 80°C/ min up to 1400°C. Figure 2 shows the dimensional change in black. Densification is seen, followed by total bloating due to over-firing. The maximum sintering speed temperature is determined by plotting the first derivative of the sintering curve dimension change with regards to temperature. This temperature is 123°C, accompanied by sintering speed of 0.08%/s.
.jpg)
Figure 2. Determining the temperature of maximum sintering speed. The peak in the first derivative of expansion with time shows that the maximum sintering speed occurs at 1230°C.
Determining the Temperature of Optimal Densification
This test is for verifying the temperature allowing complete and rapid densification while averting bloating. A constant heating rate of 80°C/min is applied, followed by isothermal segments of 2 min at successive temperature steps. The steps begin at 1190°C and end at 1260°C, roughly centered around the previously determined temperature of maximum sintering speed. The temperature profile is shown as the red curve in Figure 3.
This test shows that the temperature at which the material reaches the highest level of densification without bloating.
.jpg)
Figure 3. Determining the temperature of optimal densification
Confirmation of the Optimal Firing Cycle
The temperature for optimal densification has been identified in previous experiments. To confirm that these conditions are suitable, the complete firing profile is created within the optical dilatometer.
The rate of sample heating is 80°C/min to 1220°C, followed by an isothermal hold for 10min. In this case, the maximum shrinkage of the sample is 7.3% and is completely sintered after 5min of the isothermal segment. It was observed that there was no bloating tendency even after complete sintering, confirming the suitability of the firing conditions. This experiment confirms that an ideal firing cycle for this technical porcelain consists of a heating rate of 80°C/min to 1220°C, followed by an isothermal dwell of up to 10min, or as little as 5min. Determining the optimum firing cycle, however, is not the sole demand of a correct industrial practice.
Pyroplasticity
Pyroplasticity can be defined as the gravity-driven viscous deformation of a ceramic material during firing, which affects a manufacturing plant’s productivity. The relation between thickness and the material’s deformation rate as a function of firing temperature is determined. Quantifying the pyroplastic deformation is done by measuring the amount of bending of a body sample during heating. This measurement is significant for bodies that require complete sintering.
.jpg)
Figure 4. Confirmation of the optical firing cycle. A direct simulation of the proposed firing cycle shows that full densification is achieved without bloating.
It is possible to measure pyroplasticity with an optical fleximeter. The sample is suspended between two support rods 70mm apart, while a camera frames the center of the sample, which moves during heat treatment as shown in Figure 5.
.jpg)
Figure 5. Measuring scheme of the non-contact optical fleximeter
In Figure 6, pyroplasticity, or two possible behaviors are demonstrated. Two samples of technical porcelain were subjected to a heating cycle comprising a heating rate of 30°C/min, an isothermal dwell of 5min at 1220°C and a second isothermal dwell of 5min at 1230°C (red curve).
.jpg)
Figure 6. Flexion and deformation speed curves of two samples of technical porcelain
Understanding Ceramic Material Behavior
Technical Porcelain 1 which is a solid curve shows a final bending of more than 6mm, and at 1230°C, the maximum deformation rate occurs. Technical Porcelain 2, which is shown by a dashed curve shows a final bending of less than 3mm and the maximum deformation rate occurs at the beginning of the first isothermal segment at 1220°C.
The deformation curve for Porcelain 1 reaches a maximum deformation of 6,401µm at 1230°C, reaching a speed of deformation equal to 19.17 x 10-3µm/s, while Porcelain 2, at 1230°C, reaches a maximum deformation of 2,815µm and a speed of deformation equal to 7.4 x 10-3µm/s.
It is surprising that Porcelain 2 reduces the deformation speed with an increase in temperature. It is thus clear that glassy phases are changing their compositions, becoming more viscous. Adding vitroceramic materials to bodies, for example, can reduce bending, showing an increase in modulus of elasticity caused by the transition from the vitreous phase to the crystalline phase. It can be seen from this example how pyroplasticity and deformation speed may affect the productivity of a manufacturing plant.
Conclusion
Optimization of industrial processes can be done effectively with the optical, non-contact measuring approach, making it possible to achieve consistent measurements of the thermal behavior in terms of sintering speed (measured as shrinkage), bloating, pyroplastic deformation speed and bending.
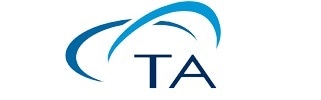
This information has been sourced, reviewed and adapted from materials provided by TA Instruments.
For more information on this source, please visit TA Instruments.