Phosphatizing, which contributes to an estimated global revenue of more than 500 million dollars, is the most vital metal pretreatment procedure. ProcessLab is a customizable modular atline analysis system that controls, records, and documents all significant analytical bath parameters of the complete phosphatizing procedure (Figure 1).

Figure 1. The ProcessLab atline analysis system with operating unit and autosampler
During the phosphatizing procedure, a hard, electrically non-conducting surface coating is produced. This coating layer is tightly adhered to the underlying metal, preventing the corrosion of metal and enhancing the adhesion of organic finishes and paints that are subsequently applied.
The basic phosphatizing procedure involves the etching reaction and the surface coating formation. Subsequent to thorough de-greasing and rinsing of the metal work-pieces, the phosphoric acid eliminates the interfering surface-bound metal oxides and enhances the surface roughness. Then at the surface of the work-piece, the alkali phosphates react with the formerly generated metal ions, forming a layer of insoluble tertiary metal phosphates.
Even at a smaller coating thickness of 1 μm, iron phosphate coatings provide basic protection against corrosion and are appropriate for interior use at controlled environments. Conversely, adding metal cations such as Ca2+, Mn2+ and Zn2+ to the phosphatizing bath causes the formation of highly resistant mixed-metal phosphates with a coating thickness of 7 - 15 μm.
Due to their modified crystal structure, these layers are appropriate ideally for rough interior environments or outdoor use. Zinc as well as iron phosphatizing occur through the same mechanism, but zinc phosphatizing is marked by the preferential incorporation of zinc cations. The iron cations located at the surface of the metal barely play a part in the formation of the metal phosphate. A first-class protection from corrosion can be achieved by the supplementary addition of more cations such as Ni2+ to the phosphatizing bath, thus ensuring better surface properties.
Phosphatizing of Metal Surfaces
The car bodies and work-pieces to be phosphatized go through varied baths where they are sequentially degreased, rinsed, activated, phosphatized and cleaned again (Figure 2). A single analysis system like ProcessLab, which is particularly adapted to the specific requirements of the phophatizing process, controls all of the bath-relevant parameters.
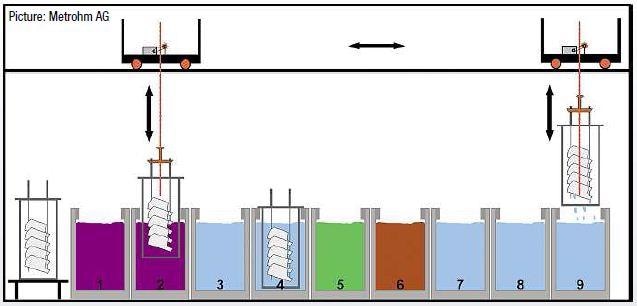
Figure 2. Operating sequence of the phosphatizing process.
Degreasing baths (1, 2): |
removal of oil, grease and wax residues from the metal surface |
Rinsing baths (3, 4): |
elimination of degreasing chemicals with water |
Activation bath (5): |
activation of the metal surface |
Phosphatizing bath (6): |
formation of a surface layer of insoluble heavy metal tertiary phosphates |
Rinsing baths (7, 8, 9): |
removal of acid residues, soluble salts and all nonadherent particles present on the metal |
Atline Analysis System
In an atline system the analytical unit is positioned directly into the process line, enabling the on-site determination of the required parameters. Manual sampling is carried out along different sampling points in the production line. This proximity, in combination with the modular concept (accommodation of all analytical modules in a single housing unaffected by dust and splashes), enables efficacious process control by determining all of the bath-relevant parameters (Table 1).
Table 1. The analytical parameters of the phosphatizing process at a glance
Process |
Degreasing |
Rinsing |
Activation |
Phosphatizing |
Rinsing |
Final rinsing |
Bath number |
1 |
2 |
3 |
4 |
5 |
6 |
7 |
8 |
9 |
a) Conductivity |
• |
• |
• |
• |
• |
|
• |
• |
• |
b) pH value |
• |
• |
• |
• |
• |
|
• |
• |
• |
c) Free alkalinity |
• |
• |
|
|
|
|
|
|
|
d) Total alkalinity |
• |
• |
• |
• |
• |
|
|
|
|
e) Free acid |
|
|
|
|
|
• |
|
|
|
f) Total acid |
|
|
|
|
|
• |
• |
• |
|
g)Accelerators |
|
|
|
|
|
• |
|
|
|
h) Zinc |
|
|
|
|
|
• |
|
|
|
i) Fluoride |
|
|
|
|
|
• |
|
|
|
The TFT screen and the user-friendly software ensure easy and straightforward operation. The barcode reader ensures unambiguous sample identification and avoids the need for laborious manual entry of data. High sample throughputs can be easily managed with the automation of analytical tasks, improving repeatability.
The ProcessLab atline analysis system controls, records, and documents the significant process parameters. The analytical data set is stored in a database for being internally processed or transferred to a process control system.
Conclusion
Rigorously defined process steps are followed to treat the metal surfaces in different degreasing, cleaning, rinsing, activation and phosphatizing baths. All of the different bath parameters should be closely observed as the quality of the produced coating is largely determined by these parameters.
Conductivity, pH value and free/total alkalinity are the parameters determined in the degreasing, cleaning and rinsing baths, respectively. Parameters such as accelerators, free and total acids, zinc and fluoride can be analyzed from the phosphatizing bath. The ProcessLab atline analysis system records, monitors and documents the significant analytical parameters of the complete phosphatizing process.
Complete process control can be achieved by combining the analytical methods with the intuitive operation ensured by the user-friendly interface. The integrated software supplements the analytical functions by offering a number of possibilities for data processing and documentation of the measured values. The ProcessLab atline analysis system satisfies all of the requirements related to process monitoring and documentation.
References
[1] Sankara Narayanan T.S.N., Surface pretreatment by phosphate conversion coatings — a review, Rev. Adv. Mater. Sci 9 (2005) 130-177.
[2] Rausch W., The phosphating of metals, Finishing Publications Ltd., London (1990) 418.
[3] Paul S., Surface coatings: science and technology, John Wiley & Sons (1996) 950.
[4] Uhlig H.H. and Revie R.W., Corrosion and corrosion control, Wiley-Interscience (1985) 464.
[5] Zhang X.G., Corrosion and electrochemistry of zinc, Plenum Press (1996) 475.
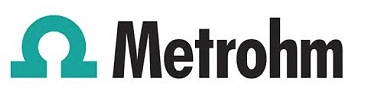
This information has been sourced, reviewed and adapted from materials provided by Metrohm AG.
For more information on this source, please visit Metrohm AG.