Applied Aerospace Structures Corp. (AASC) are specialists in the design, fabrication, and evaluation of lightweight structural assemblies, paying special focus on high-performance engineered structures used for aircraft, space, and ground systems.
.jpg)
Figure 1. GPS IIF SATELLITE. Image Credit: General Plastics
AASC has been an innovative and responsive supplier to the aircraft and space industry for over five decades, producing a broad range of composite aircraft hardware and components. The company also supplies other structures for manned space missions, satellites, launch vehicles, and ground-based defense applications. Its aircraft and air space divisions are involved with various directed-energy weapons programs.
The Challenge
Large composite aerodynamic coverings are fabricated by AASC to meet the structural, dynamic, and thermal stability requirements of precision weapons. The Lawrence Livermore National Laboratory, a federal research facility, approached AASC to build an aeroshell for its cutting-edge Kinetic Energy Projectile missile. This weapon is capable of flying through low-orbit space and reaching targets anywhere in the world within 30 minutes.
At the Holloman High-Speed Test Track in New Mexico, the Lawrence Livermore National Laboratory had planned a rocket sled test to evaluate the performance of this new precision-effects warhead. The track is nearly 10 miles long and is used to conduct dynamic tests of missile components under rigorous conditions and at hypersonic speeds, rather than expensive live-missile launches.
Earlier, the federal research facility used advanced composites to build an aeroshell prototype to assess how the missile would go through the atmosphere. In this test, the laboratory required a cost-effective aeroshell to evaluate the shape of the charge. The AASC needed a cost-effective material that can be easily machined in-house to rapidly prototype the large aeroshell. The material had to exhibit high stability and compatibility to its low-temperature, multistep curing processes. AASC had to meet the schedule as the test track is in high demand throughout the year.
The following are the key requirements:
- Cost-effective prototype for one-time use
- In-house machinability
- Fast tool turnaround
- Fulfill the low-temp curing process
The Solution
General Plastics' LAST-A-FOAM® FR-7100 Multi-Use Core Series material had been used for various other AASC projects:
- For machining holding fixtures
- For machine tools
- As an assembly tool for holding reflectors for SpaceX
As the physical properties and advantages of the FR-7100 Series were familiar, AASC chose the 30-pound density of this rigid polyurethane foam to mold tools to cure graphite laminates to the molds machined by the company in-house. The low cost was the major reason behind the selection of this polyurethane foam for the test aeroshell, as it was a 10-foot long and 4-foot tall structure and a one-time build.
Tools made of materials such as aluminum, carbon, steel or invar were too heavy and costly for this application. Moreover, this foam enabled AASC to modify the mold tool easily to be used as the machining fixture as well as the assembly fixture, leading to a significant reduction in cost and time. The customer was in need of a material that is easily machinable to tight tolerances internally to speed up production.
With General Plastics' foam, a rapid turnaround was achieved. AASC obtained and machined a large bonded block of FR-7130 foam to a finished prototype tool within four weeks of raising a purchase order. Earlier, it took 12-16 weeks for a metal tool and involved the following steps:
- Fabricating an egg-crate backing structure
- Forming skins and welding it
- Creating a shape post and machining accurately to the required shape
The sled or nose cone looks like a flattened diamond shape constructed with two lower and upper aeroshells roughly 5/8" thick. For the two leading-edge tools, the foam was employed to produce tools for the two inner supports and to create four internal structural components. Layup and curing of the skins were done using the lower and upper aeroshells. Also, the assembly was built using the upper and lower aeroshells.
A very smooth surface was achieved on the foam tools by applying a low-temp epoxy primer. Curing the graphite laminates was performed on the foam tool at 170ºF, followed by removing the parts from the tool and fully curing them at 350ºF in the autoclave. Laminate spring back, creep, bowing, or changes in its properties were not observed when processing.
AASC was able to make the prototype within four months. During the test, the prompt strike warhead enclosed in AASC's prototype aeroshell was launched from the Holloman test track at Mach 2 speed. In addition to acquiring critical predictive data during its 5-second run, the prototype aeroshell confirmed the value of employing General Plastics' FR-7100 Multi-Use Core Series for cost-effective, fast-turn prototyping.
Key Benefits of FR-7100
The following are the key advantages of using the FR-7100:
- Cost-effective and versatile for components, prototypes, and models
- Shows high dimensional stability as it will not bow, twist, or warp
- Ideally suited for a composite layup, drape-forming, and vacuum-form tools
- Fine cell structure makes it suitable to achieve very smooth finishes
- Uniform in density with nonabrasive, grain-free surface
- Sheets and large blocks can be easily machined, painted and bonded
- Easy to shape or carve with a range of cutting processes
- Closed-cell foam avoids water or moisture absorption
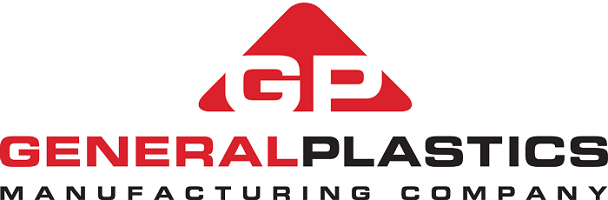
This information has been sourced, reviewed and adapted from materials provided by General Plastics Manufacturing.
For more information on this source, please visit General Plastics Manufacturing.