Hydrogen is one of the highest volume industrial chemicals used globally, serving a wide range of applications that exploit its unique physical and chemical properties. Some of the applications are:
- As a protective carrier gas in crystal growth, CVD coatings, semiconductor fabrication, and welding
- As a chemical feedstock to modify the properties of specialty chemicals and petrochemicals, and as a reducing agent to stabilize oils
- As a high heat, clean fuel gas in applications that involve thermal spray coatings, and glass melting and fabrication.
- As a reducing atmosphere in thermal treatment that involves metals such as sintering, heat treating, brazing, float glass manufacturing, etc.
- In nitrogen/hydrogen blends as a lower cost, high performance, environmentally advantageous substitute to helium for leak checking.
- As a fill gas for hydrogen-cooled electric generators; pure, low density hydrogen safely enhances the efficiency of electricity production.
The usage range of applications for industrial hydrogen spans from just 10 seconds of scf/d (standard cubic feet per day) of hydrogen for specialty crystal growth and leak checking to well beyond 100 MM scf per day (million standard cubic feet per day) of hydrogen for a refinery.
Given the broad range of usage rates, different hydrogen supply approaches have evolved to suit the requirements of customers. The Proton Exchange Membrane (PEM) water electrolysis on-site hydrogen generators developed by Nel Hydrogen serve a section of the market of small-to-medium-sized users that might otherwise be served by a form of delivered hydrogen.
Hydrogen has several characteristics that make delivery and storage difficult:
- Extremely low ignition energy
- The widest flammability range of all gases (4% to 75% in air)
- The ability to leak from the tiniest openings
Hydrogen is classified as a highly hazardous material, and its storage is highly regulated. The relevant code documents include National Fire Protection Association standards NFPA 55 or NFPA 2.
Generally, if more hydrogen is stored, greater distance should be maintained between the hydrogen storage and other site operations - storage of large quantities of hydrogen occupies a lot of site space. In the United States, the maximum limit for indoor hydrogen storage is generally 2,999 Scf - about 10 cylinders.
In some cases, permissible indoor storage is even more limited by factors such as seismic concerns, the presence of other flammables or hazardous materials, siting above or below ground level, or other relevant factors.
Of all the industrial applications, the use of hydrogen as a chemical feedstock has the highest use rate. This application has always employed an onsite hydrogen generation approach, which involves producing hydrogen as it is needed, to prevent the need for huge volumes of hydrogen storage.
These large chemical factories liberate hydrogen from hydrocarbons and steam using heat and catalysts in reformers to generate large volumes of hydrogen to meet the high volume, 24/7, steady rate process needs, at a relatively low-cost. Such reformers are large and expensive to build, own, and operate, and have a limited turndown range.
Although several organizations have attempted to adapt hydrocarbon reforming for smaller uses, reforming is not yet recognized as commercial for hydrogen requirements under approximately 25,000 scf/h (600,000 scf/day).
.jpg)
Proton Exchange Membrane (PEM) based water electrolysis hydrogen generators provide operational, production and safety cost benefits to hydrogen users that use very little hydrogen to be served by hydrocarbon reforming. Previously, these users would have had to utilize delivered and stored hydrogen.
Amenable users may also have other operation needs such as limited installation spaces, high purity, variable use rate, operation less than 24/7, and the need for fast permitting, easy installation, operation, and maintenance.
With PEM on-site hydrogen generators, small-to-medium flow rates of pressurized, highly pure hydrogen can be made at predictable costs, with near-zero hydrogen inventory. These generators can vary production rates to suit the requirements of customers.
Currently, PEM on-site hydrogen generation is best suited for industrial customers using less than about 3,000 scf/h (~75,000 scf/day), although bigger systems that can benefit larger customers in certain situations, are being introduced.
PEM on-site gas generation offers many attractive characteristics:
- Near zero gas inventory
- Compact equipment that require little safety review and no emission permits
- Extremely low water content and high gas purity
- Load following by varying the rate of hydrogen delivery exactly as required
- Fast permitting, easy installation, simple operation, high reliability, and minimal maintenance
- Medium gas pressure: high enough pressure to allow for surge storage load leveling
Although PEM on-site hydrogen generation is the ideal hydrogen supply solution for several customers, it is not a universal solution. PEM on-site hydrogen offers the best economics for any customer who considers any or all of the above-mentioned characteristics important. Customers who may opt for delivered, stored hydrogen are:
- Portable or temporary hydrogen needs
- Hydrogen flow rate requirements that cannot be predicted and are widely variable
- Intermittent hydrogen use (perhaps for a few minutes at a time, a few times per day)
- Customers for whom hydrogen purity is not important
.jpg)
Truck delivery of hydrogen is the competition for PEM on-site hydrogen in the target hydrogen market. Traditionally, truck delivery of packaged pressurized gas cylinders have been used for the supply of delivered hydrogen, or bulk hydrogen delivered and stored as a cryogenic liquid or compressed gas. Customers who use delivered hydrogen would use up to 100,000+ scf/d of hydrogen.
There are opportunities for hundreds of PEM on-site hydrogen generation systems to replace delivered hydrogen for industrial applications every year. This makes it possible to standardize and reduce the cost of systems, ensuring the best performance at the lowest overall cost.
Nel Hydrogen has focused on the development of highly adaptable standardized systems that provide optimal performance in areas that are important to potential customers, while saving money where possible. With large field population of near-identical units and a robust service capability, Nel Hydrogen has been able to use field performance as feedback to the design and manufacturing processes, continuously enhancing generator performance, price competitiveness, and reliability.
The PEM on-site hydrogen generators of Nel Hydrogen are factory-built and standardized to meet the challenging quality and safety standards of compliance organizations worldwide. Equipment that meets these standards can be used across the world with minimal risk of compliance issues in any particular locale. The on-site hydrogen generators of Proton are compliant with applicable UL, CSA, and CE ATEX requirements.
Hydrogen Purity
PEM on-site electrolysis involves splitting water to make hydrogen product gas, which is extremely pure - 99.9995+% or better - and the byproduct oxygen. The importance of hydrogen purity may differ from customer to customer depending on what the customer uses hydrogen for.
Customers who use delivered hydrogen pay a considerable premium price for highly pure hydrogen, and the gas price purity premium is generally much higher for smaller users, as the analysis price is semi-fixed but is allocated over a delivery batch size. The price for analyzing a liquid hydrogen trailer is allocated over the entire 1.2 MM scf of hydrogen in the trailer, while the cost of analyzing a cylinder would be charged to the 200-300 scf of hydrogen in that cylinder.
Users in need of a quality certification pay for three things – preparing the delivery batch (cylinder, multi-pack, or trailer) ready to be filled and filling it, performing the quality verification on the batch of hydrogen, and the time take for quality verification.
Gas chromatography (GC) is generally used to perform the primary analysis for quality verification. The lower the limits of detection and the more detailed the quality specification, the longer the GC run will take.
As every fill batch has to be tested if an analysis certificate is needed, more tests for a given amount of hydrogen will have to be performed for those forms of delivery that involve smaller batches. The batch size is the smallest for users of cylinder, with each batch as small as each cylinder. Users of tube trailer hydrogen, which is made and delivered in large “batches”, pay less, while users of liquid hydrogen pay an even smaller premium.
A useful rule of thumb is that for delivered cylinders, every “9” of purity beyond 99.95% industrial grade purity, for example 99.99% or 99.999% or 99.9999%, leads to doubling of the price per cylinder. Hence a $25/cylinder 99.95% industrial grade hydrogen can easily become a $200 or higher cost hydrogen cylinder, driven by the need to achieve, prove, and document the required purity in the small cylinder batch size. This can be particularly evident for electronic quality hydrogen.
The cost of using higher purity delivered hydrogen is drastically increased by its premium pricing. Thus PEM on-site hydrogen generation that inherently provides premium quality hydrogen can be especially attractive to users of high purity grades of hydrogen.
Zero-Inventory Hydrogen
Nel Hydrogen essentially uses a zero-inventory production approach to design its PEM on-site hydrogen systems. For instance, a model C30 hydrogen generator, which is capable of delivering up to 30 N⋅m³/h (1140 scf/hr or 2.7 kg/h) of hydrogen, has only 14 g (6 scf) of internal hydrogen when operating at 100% of capacity.
Safety, compliance, and lessened investment in facility exhaust systems are the benefits of zero inventory hydrogen supply. Minimizing the size of pressurized internal vessels has enabled Nel Hydrogen to fall below the lowest threshold for most national and regional pressurized gas limitations.
Load-Following
PEM on-site hydrogen systems can load-follow users’ hydrogen needs from 0% delivery up to 100% of capacity by adjusting production to match the rate of hydrogen use exactly, without using additional power or wasting hydrogen. The specifics of electrochemical hydrogen production helps to achieve variable hydrogen delivery, without compromising on the operating efficiency on turndown, wasting hydrogen, or shifting product quality.
Pressurized Hydrogen for Surge Storage Adaptability
PEM on-site hydrogen generators are not only capable of load-following, but can also make pressurized hydrogen. This can be used with surge hydrogen storage to serve the variable hydrogen flow rate requirements of the customer that sometimes go beyond the ability of ordinary load-following.
In this manner, a smaller hydrogen generator can ne used as a variable rate hydrogen requirement, which could sometimes exceed the capacity of the hydrogen generator. Examples of how this is helpful include:
- A hydrogen generator that is sized to the average use rate can be used to feed batch furnaces, but the surge storage allows the furnace to be filled quickly
- Torches that run intermittently but at high rates can be powered from surge storage to meet virtually unlimited flow rates for limited periods of time
- For semiconductor applications, providing a small amount of surge storage capacity can prevent a pressure drop if a mass flow controller opens suddenly
Operating Efficiency and Expandability
For several processes, the operating efficiency of smaller scale systems is lower than that of larger systems of the same type. However, modern PEM on-site hydrogen systems do not lose efficiency at smaller scale, due to the specifics of electrochemical hydrogen generation. In addition, the systems can be operated across a wide range of ambient conditions.
The PEM hydrogen generators from Nel Hydrogen are built with a modular, expandable design that enables the hydrogen generators to be quickly expanded in capacity if required to accommodate growth. For instance, Nel Hydrogen’s model C10 hydrogen generator can make up to 10 N⋅m³/h of hydrogen (about 380 scf/h). The unit can be expanded, within a cabinet and at a customer’s site, to a C20 or a C30 unit that has the capacity of up to 30 N⋅m³/h of hydrogen (about 1140 scf/h).
Electrical Rates
Electricity rates that are denominated in dollars per kW⋅h widely vary across the US, around the world, and even based on the specific characteristics or arrangements of a particular site. Not taking the other factors into consideration, sites with lower cost electricity find PEM on-site hydrogen more price competitive than sites that have higher electrical rates.
For instance, at an industrial electrical rate of $.06/kW⋅h, a PEM hydrogen generator will make hydrogen for approximately $1.00 per 100 scf variable cost; while the same hydrogen in higher electrical cost areas where industrial power might cost $0.12 or more per KWh will cost more than $2.00 per 100 scf variable cost. The cost of PEM electrolysis generated hydrogen can be less in areas where electrical rates are lower.
Power plants - especially baseload plants in areas where electricity is regulated - may have particularly low electrical costs. The low electrical costs for these plants is due to the fact that electricity within the fence may be priced as parasitic power at its variable cost only, leading to electrical costs in the $0.03 to 0.04 per kW⋅h range, even in areas where the rates for other customers may be much higher.
With more markets providing the time-of-day option for less expensive nighttime power, a completely new option for saving money using PEM electrolysis hydrogen generation may become commercially attractive.
Portability & Ability to be Relocated
Most hydrogen applications are fixed in location for practical purposes. For instance, a heat treat facility uses hydrogen in furnaces that are fixed in location, and a power plant uses hydrogen at a fixed site for the life of the plant. Some customers use hydrogen for applications that need portability, such as a hydrogen torch that is used for work that may need portability.
The design of typical PEM hydrogen generators (e.g. bulk, weight, fixed connections) makes them highly suitable for fixed use rather than for applications that need portability. Hydrogen cylinders may be a better option for portable applications.
In contrast, a PEM hydrogen generator may be a better solution for a customer located in a temporary or rented facility, particularly for a hydrogen user that needs more than a few cylinders of hydrogen weekly. With PEM on-site hydrogen, the cost of required permanent hydrogen delivery and distribution infrastructure can be reduced or completely avoided, making it advantageous.
Foundations and other infrastructure for external hydrogen storage, the cost of extensive building internal piping from the delivery area to the usage area within the building, and underground piping from hydrogen delivery/storage area to the building are some of the avoided costs.
For customers in rented facilities with hydrogen uses of larger than a few cylinders weekly, it may be beneficial to use hydrogen generation that can be placed immediately adjacent to the use area, and can be relocated when the customer expands and moves to new facilities. The amount of invested capital spent on piping and foundations that have be abandoned (and perhaps even removed at additional cost) when the customer relocates or expands, can be minimized with the hydrogen generator approach.
Equipment Cost Allocation and Variable vs Fixed Costs
PEM on-site hydrogen generators are capital equipment. Three key factors affect the cost of hydrogen produced:
- The cost of purchasing and installing the hydrogen generation system, and its useful life
- The variable cost of the energy used to produce hydrogen
- The cost of service and maintenance
.jpg)
.jpg)
Generally, for PEM on-site hydrogen generation, the total cost of hydrogen is approximately half variable cost (of which 90% is electricity, with maintenance and DI water making up the remainder), and half capital (fixed) cost. This is a larger proportion of fixed cost than is generally the case for the hydrogen delivered.
As a result, PEM on-site hydrogen is especially attractive when hydrogen is used several hours each day, and consequently the fixed cost can be allocated over more hours. However, in situations where hydrogen is used relatively for a few hours on a daily basis, the supplied hydrogen may be more economical
For those using PEM on-site equipment, if there is an increase in hydrogen usage hours, the entire cost of hydrogen from PEM on-site hydrogen generation reduces quickly because the fixed cost is allocated over more hours.
For those using delivered cylinders for hydrogen supply, hydrogen is primarily a variable cost. The rental costs and delivery charges of cylinders are generally modest. For those using the smallest volumes, the facility piping for cylinders can be minimal as long as usage continues to remain low so that the cylinders can be located close to the point of use (usually permissible as long as inventory remains below 2999 scf).
While the price of hydrogen in the cylinders is relatively high, for certain customers it is preferable to have the flexibility to use hydrogen or not, and have the costs follow the molecules. This is especially true for customers initiating a new process, or serving requirements whose growth pattern is not possible to estimate, or setting up an experimental rig – all situations where customers cannot estimate whether they will use hydrogen in the future, or how much.
As hydrogen usage grows, the disadvantages of delivered hydrogen cylinders outweigh the advantages, making alternatives more attractive.
Disadvantages of hydrogen cylinder supply include:
- Cylinder handling and impurities entering the system on changeouts
- Costs of cylinder gas, particularly for better grades
- Potential runouts as each cylinder contains only a relatively small amount of hydrogen
- Cylinder accounting for rental charges and deliveries
- Potentially variable quality, as suppliers refill industrial grade hydrogen cylinders on top of the heel from the previous users
Conclusion
Customers who use up to 75,000 scf/d of hydrogen should consider using the hydrogen supply option of PEM on-site hydrogen. Customers should plan ahead and account for the timing requirements of their hydrogen supply contract, so that they can make a change when they are contractually free to do so.
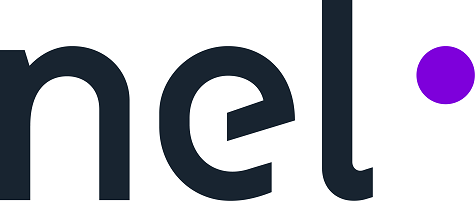
This information has been sourced, reviewed and adapted from materials provided by Nel Hydrogen.
For more information on this source, please visit Nel Hydrogen.