Coloring
In comparison to semi-crystalline, amorphous thermoplastic materials are available in a wider color range as they are transparent. However, all plastics can be made/are available in a wide range of colors.
Compounded Material
There is an increasing use of combining color concentrates or masterbatches with natural, or uncolored, material due to the ease with which color may be added at the machine. This is much different to earlier times when plastics were molded from colored granules. However, even now, the most accurate coloring strategy is compounding, and provides the most precise and reproducible colors.
It is also the most suitable for small runs and provides the best density of color. While most engineering plastics are sold in already colored (fully compounded) commodity plastics are usually colored on the injection molding machine.
Masterbatches
Both solid and liquid masterbatches are available, and a wide color range is possible from such blends. Solid masterbatches are the most popular; about 60% of all in-house, color addition is done by solid masterbatch. These types of solid masterbatches may be based on the base polymer (polymer specific concentrate), or on a wax-like carrier (a universal carrier).The polymer concentrates are the cheaper option.
It is important to check beforehand whether a universal masterbatch is suitable for use with the plastic; claims of some masterbatches being universal have to be treated with caution. Other additives, for example, UV absorbers, can also be a part of some masterbatches.
Masterbatch Advantages
Masterbatches may be employed either by dry-blending the masterbatch with the resin and feeding the mixture in the molding machine or, by actually adding (dosing) the masterbatch on the injection molding machine. The use of masterbatches results in:
- Cheaper color, compared to compounded material
- Simplified storage because only natural material is ordered and stored
- Reduced cost of raw material, as only natural material is ordered, and bulk purchases may be arranged
- Reduction in dusting problems in comparison to dry pigmint use
However, employing masterbatch mixtures can cause problems.
The common issue is differences in color shade between different machines due to the inaccuracies in the dosing equipment. Separation of the masterbatch from the plastic in the hopper when using dry blends is another problem.
Liquid Color
Here, the colorant is dispersed in a liquid carrier to obtain a liquid masterbatch, which can be metered or, dispensed with ease during processing. However, despite initial optimism, liquid colors are not used widely.
The most successful applications seem to be those on long runs with a single color where precise metering to obtain uniform color can be ensured and maintained. However, if they are split, cleaning could be a major problem. Maintaining dosing accuracy is another issue.
Dry Color
Although the use of dry colorants is the cheapest way of coloring plastics, the process tends to dusty and messy. Sachets or cartons with the exact amount of colorant for a specific size lot of plastics material are available to ensure color consistency across a production run (improvements in accuracy and consistency).
It is vital that the surfaces of the granules are evenly covered with the colorant when dry colorants are used, as this will ensure satisfactory dispersion of colorant in the polymer melt. The blending time and the type of blending technique (such as single- or multi-axis rotation) should be standardized to obtain uniform coverage of granules by the colorant.
In order to obtain color uniformity, a successful procedure needs to be maintained after it is established. Care needs to be taken to ensure that the colorant does not absorb moisture during storage, as agglomerates wll readily occur, which can cause color shading or streaking in the molding. Many powdered pigments (e.g. cadmium-based) require careful handling due to toxicity issues; such problems are the reason why there is a decline in the use of dry colors.
Note:
The type of dye or pigment used considerably affects the properties and dimensions of the molded part, irrespective of the method employed to color the natural polymer.
Reprocessing
The ability to reclaim faulty moldings and the feed system produced during the molding of thermoplastic materials is often a mixed blessing, as it can lead to the attitude that the production of faulty moldings does not matter.
'After all, the moldings can be ground up to give reclaimed material and so used again' is an often-repeated comment.
Wasted Effort
The wasted time and effort need to be taken into account even though moldings can be reclaimed. It costs a lot of money to operate an injection molding machine, so it makes sense to run the injection molding machine properly and consistently so that the production of reject moldings is avoided.
Post-production, plastic moldings need to be looked after. Handling moldings should be avoided whenever possible, and they must be covered, as plastics attract dust when exposed to the atmosphere.
Material Changes
There should be very little or no change in the plastics material during the molding process, as changes are not desirable. Some of the changes that can happen are:
- Water contamination - caused due to condensation or by absorption of water by the material
- Oxidation – when heated in contact with oxygen, plastics 'oxidize' or combine with the oxygen, which is first indicated by a color change and then by a change in properties
- Overheating – if overheated, even in the absence of air, plastics undergo thermal degradation or decomposition, which can be dangerous
- Dust contamination – static electricity can be generated on plastics, and this phenomenon quickly attracts dirt or, dust
Effect of Additives
Some materials can speed up (they catalyze) chemical changes, for example, copper causes a quick change in hot PP. Consequently, care should be taken when adding any material to a resin/material, and it must only be done when it is certain that it won't casue an undesirable change.
This means that every additives should have been tested, and only tested-additives are used in production. A substitute for a specified-color masterbatch or pigment should not be used, unless the substitute is tested and approved.
Ruthless Rejection
When faulty feed systems and moldings are scheduled for reclamation they should be very carefully looked after, and only those parts that are contamination-free and devoid of color changes should be used.
This is because it is common practice to combine reclaimed material (regrind) with virgin (new) material, and if the reclaimed material is not contamination-free, then the quantity of reject material produced can be significant. This problem, if left unchecked, can quickly get out of control, so any feed system or any moldings suspected of being degraded or contaminated must be ruthlessly rejected. Only good quality material should be reclaimed.
Regular Inspection
All material that is to be reclaimed must be covered. The grinder and the storage containers need to be kept spotlessly clean. Regular inspection of grinder blades must be done for breakage, wear, and bluntness, and necessary replacements should be made.
The reclaimed material must be put through equipment to remove fines or dust, water, and metal fragments. This material must be considered as new stock, and must be stored in tightly sealed containers in a dry, clean storeroom. The reclaimed material needs to be mixed with virgin material in a precisely approved ratio.
By the Press Granulation
An auger regranulator assembly can be used to carry out regranulation of feed systems at the molding press. The entrance section of the regranulator is kept next to the chute of the molding machine, into which the feed system falls when ejected from the mold.
After regranulation, the material is automatically mixed with the virgin material at the approved ratio, and then fed into the molding machine hopper. This process has two benefits: the risk of contamination is minimized, and the need to re-dry hygroscopic materials is reduced. However, such an assembly takes up precious floor space around the molding machine.
Runnerless Molding
Many moldings are made by employing injection molds where the feed system does not get ejected at the end of the cycle. The feed system is kept hot so that at the time of the next injection shot, the incoming material moves through the feed system which is still hot.
The sprue and runner system is usually the thickest part of the shot, and hence, it generally takes the longest time to cool down, which shows down production if it has to be cooled for ejection purposes. By removing a cold feed system, reclaiming costs can be saved, and the cycle can be accelerated.
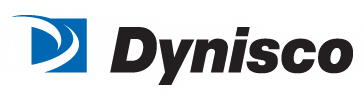
This information has been sourced, reviewed and adapted from materials provided by Dynisco.
For more information on this source, please visit Dynisco.