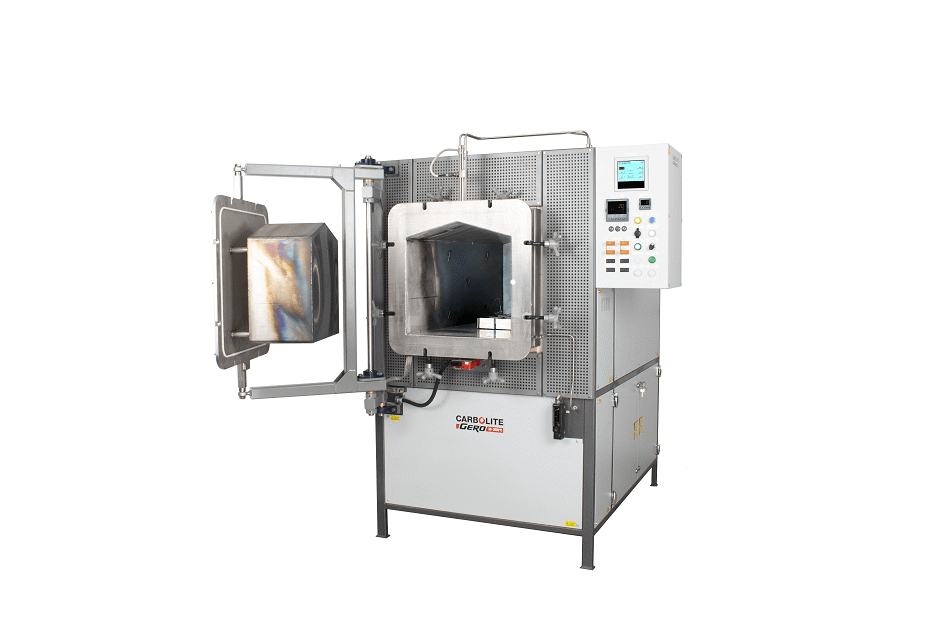
GPCMA/174 Furnace
Currently, additive manufacturing of 3D metal parts is carried out using two primary techniques. Although these techniques are time-intensive, they are excellent when it comes to manufacturing “impossible” or complex parts that cannot be produced through conventional machining or casting methodologies.
This has already led to the development of a number of prototype pieces and even innumerable “impossible parts” for the automotive, aerospace, medical, and tooling industries.
Conventional Techniques Used for Additive Manufacturing of 3D Metal Parts
Electron beam manufacturing (EBM) performed in a vacuum chamber eliminates the need for heat treatment of the manufactured parts. Wire (for example, Titanium, CoCr, Ti-6AI-4V, Inconel 625, and Inconel 718) or metal powders are welded together in consecutive layers with an electron beam as the heat source. This process leads to the formation of fully dense metal components. Since the process is carried out in a vacuum, oxidization of the material is prevented.
Direct metal laser sintering (DMLS) involves using a laser in an atmosphere of pure inert argon. The process is digitally driven, direct from 3D CAD data. For each CAD data slice, a thin, even, fine-sieved metal powder layer (cobalt chromium, titanium alloy Ti6Al4V, nickel alloys Inconel 625 and Inconel 718, stainless steel, and aluminum alloy AlSi10Mg) is deposited over the build plate before the laser precisely melts the chosen areas of the powder. This process is repeated to develop layer by layer until the part is completed.
DMLS can be applied to manufacture very small features and parts and has the potential to reproduce geometries such as enclosed spaces that could be challenging to machine. The thickness of the layers can be as low as 20 μm, and the tolerances on tiny features can be as small as ±50 μm.
The existing build rates for manufacturing components using a DMLS process are very low. In addition, costs are high since it is necessary to produce raw metallic powders using a ball-mill/grinder and then sieve and test them before they can be used. It is obvious that existing DMLS machinery needs a considerable amount of investment. However, if the dimensions of the needed part are less than 250 mm x 250 mm x 350 mm, the process could be best suited for those who demand rapid prototyping or small quantities of “impossible” or complex parts that can be subsequently milled, machine drilled, reamed, or slotted. They can also be painted, powder coated, anodized, or polished.
There has been a rapid increase in the demand for 3D Additive Manufacturing. Journals, tradeshows, and websites have flourished with the increase in maximum part sizes, reduction in 3D manufacturing times, increased availability of powder alloys, and with components manufactured for the medical, aerospace, automotive, and tooling sectors using this technique achieving standards approval in increasing quantities.
Using a Carbolite Furnace for the Heat Treatment of 3D Additive Manufactured Parts
The DMLS process necessitates the use of a heat-treatment solution with precise temperature uniformity. This guarantees that the manufactured parts comply with the suitable metallurgical properties of the chosen metal alloy.
The heat-treatment is carried out in an inert (usually argon) atmosphere to prevent the contamination of the sintered part by oxygen molecules that can modify the physical and chemical properties (porosity) of the finished component. It is necessary for the inert process to be repeatable with an optimally measured gas flow monitored to be compliant with an AMS 2750E Classification specified by the customer. As a matter of fact, in one particular example, the atmosphere is maintained at <1000 ppm (0.1%) oxygen throughout the entire manufacturing process, which can be decreased to as low as 100 ppm (0.01%) oxygen by using a reactive metal like titanium.
CARBOLITE’s General Purpose Chamber furnaces come with Type B instrumentation and fulfill the demands of AMS 2750E Class 1 when used in combination with a Haynes 230 or Inconel retort. The furnaces are available in different sizes (Industrial Furnace GPC 13/131, 13/200, 13/300, 13/350, and 13/405; or Laboratory Furnace CWF 13/65) with the capacity to handle one to four 4 build plates, which are perfect for those performing DMLS Additive Manufacturing.
The latest GPC 13/300 retort furnace has a working volume of 400 mm x 400 mm x 350 mm, a 6180 XIO data logger, and an automatic on/off gas control powered by a Eurotherm 3508 controller. Trace levels of oxygen and argon/nitrogen gas flow in the modified atmosphere of the retort are constantly monitored. The CARBOLITE GPC range offers under-hearth heating together with heating from the top as well as sides, thus enhancing the temperature uniformity within the retort where temperature thermocouples are positioned. The location of the Cascade Controls within the retort allows more rapid heating times, thereby considerably reducing customer cycle times when used in combination with optional forced cooling.
A temperature interlocked swing-out door provided in the 13/300 furnace further shortens cycle times, thus facilitating rapid and easy access for loading/unloading with a water-cooled silicon rubber door seal that preserves a modified atmosphere within the chamber all through the entire heat treatment process.
Conclusion
CARBOLITE’s has designed its GPC range with retorts on purpose to facilitate 3D Additive Manufacturing to be performed with the highest specifications. This range eliminates the difficulties that are often encountered while using furnaces from other manufacturers.
The inability to preserve an inert atmosphere, the need to use extra equipment to remove the retort while loading/unloading parts, or the need for using large volumes of high-cost inert gases are the most common problems experienced by users while using other furnaces. CARBOLITE GPC range solves all of these denigrating issues to guarantee reduced operating costs every day for its customers; it also ensures “best in class” temperature uniformity and prevents undesirable oxidization. Most significantly, heating on four sides, easy loading/unloading enabled by CARBOLITE’s specialized water-cooled silicon sealed swing-out door, and forced cooling option considerably reduce the production cycle times.
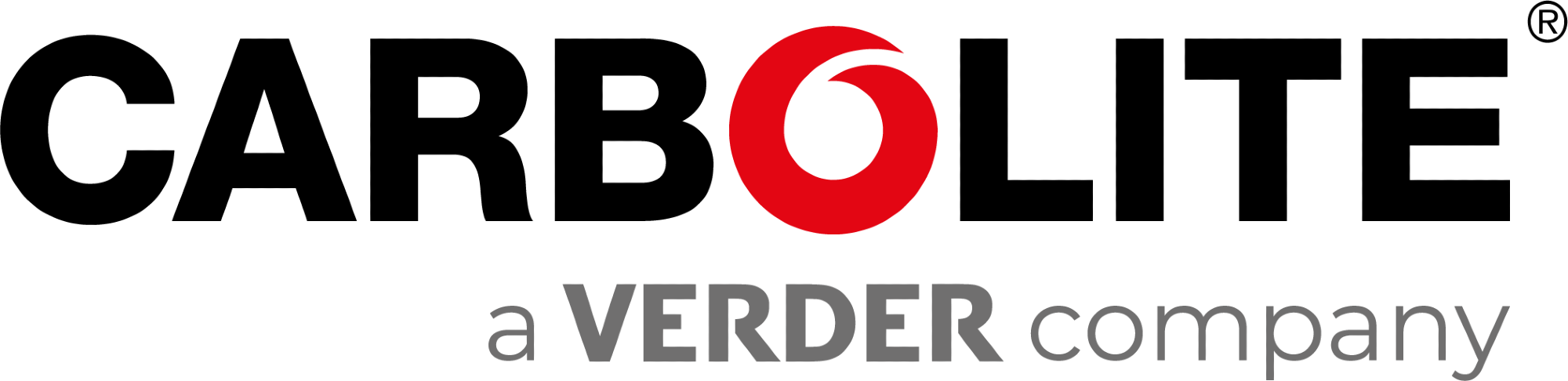
This information has been sourced, reviewed and adapted from materials provided by CARBOLITE.
For more information on this source, please visit CARBOLITE.