Toray Advanced Composites provide advanced, market leading fire-retardant composites for the aircraft interiors industry. Experts across the industry use Toray lightweight composite materials in a wide range of aerospace interior applications to eliminate secondary operations, increase mechanical durability and deliver optimal FST safety.
Toray's Cetex® brand of differentiated Reinforced Thermoplastic Laminates (RTL) as well as unidirectional (UD) tapes are used in a wide variety of aircraft interior applications, ranging from flooring and cabin seating, to stowage bins and galleys. Reinforced with carbon fibers or glass, thermoplastic composites provide:
- High quality surface finishes that considerably reduce the need for filling and sanding prior to application of decorative trims or sublimation printing
- Very low FST & OSU properties (OSU <25/25)
- Very tough surfaces for better impact and wear performance, allowing long term durability
- Excellent moisture resistance leading to better durability
- Part count reduction, overmolding thermoplastics allows consolidation of parts and integration of mechanical fixation
- Quick manufacturing cycles, press forming in minutes
- Component coloring, option to provide ‘base color’ for applications
.jpg)
Toray Cetex® laminates are customized to users’ application needs and are consolidated as multiple or single-ply construction to improve functionality. The RTL semi-finished product offering includes customized color, fiber layups, and a surface finish ready for service.
Toray Cetex® TC925 FST – Polycarbonate (PC) resins offer a cost-effective solution that combines good FST & OSU results with excellent impact performance.
Toray Cetex® TC1000 – Polyetherimide (PEI) resins offer optimum FST & OSU performance, coupled with good chemical resistance and ideal secondary operation compatibility (welding, jointing, and painting).
Toray Cetex® TC1100 – PolyphenyleneSulfide (PPS) offers good FST performance as well as excellent solvent resistance for structural applications.
Toray Cetex® TC1225 – Part of the PEEK family, Polyaryletherketone (PAEK) resin provides excellent thermal and structural performance as well as compatibility to PEEK for injection welding and overmolding.
Materials are available either as prepreg rolls or consolidated laminates (RTL) with a format of 3.66 m x 1.22 m (12’ x 4’).
Product Applications
Storage Bins
Toray Cetex® is the ultimate solution in an industry where weight and impact performance is critical. Exceptionally lightweight and durable for hardwearing bin surfaces and linings, Toray’s embedded color eliminates secondary painting and finishing needs.
Cabin Linings
Featuring excellent durability and high impact resistance, Toray Cetex® delivers near-perfect demold performance. It eliminates rework and maximizes efficiency for trim by minimizing post-processing (sweep/sand) operations.
Cargo Linings
With excellent durability and exceptional FST performance, Toray Cetex® provides near perfect demold performance. It eliminates rework and maximizes efficiency for large surfaces by minimizing post-processing (sweep/sand) operations.
Service Carts
In an industry where weight and impact performance is critical, Toray Cetex® serves as the ultimate solution. Exceptionally lightweight and durable for hardwearing cart surfaces, graphics can also be sublimated into the surface thus removing secondary painting and finishing needs.
Ducting
For ultimate flow rate performance, Toray Cetex® thermoplastics provide the lowest porosity levels in the lightest materials available. Toray's laminate systems are used in low pressures systems across the world and are rolled and seam welded for maximum efficiency.
Ceiling Linings
Toray Cetex® is stiff and lightweight and provides near perfect demold performance. It eliminates rework and maximizes efficiency for large surfaces by minimizing post-processing (sweep/sand) operations.
Galleys
Galleys and dividers are high volumes, wear applications that require resilient low-maintenance performance. Toray’s Cetex® thermoplastics with in-color and high moisture barrier technology now provide new possibilities for the workspace.
Seat Structures
Toray Cetex® thermoplastics are capable of fast manufacturing cycles and are perfect for high volume parts such as thermoformed seat structures, including armrests, back panels, and seat pans. Materials can also be overmolded with features for design integrity and process improvement.
Flooring
Aircraft flooring is manufactured in high volumes and prone to abuse, and hence it requires exceptional resilience. Toray’s hybrid system integrates the best of lightweight thermoplastic and thermoset technology to provide remarkable durability and longer service life, withstanding carpet changes without any surface degradation.
.jpg)
Image Credit: Toray Advanced Composites
Product Overview
Thermoset
|
RESIN MATRIX |
DRY Tg ONSET |
CURE TIME AND TEMPERATURE |
KEY PRODUCT CHARACTERISTICS |
OOA/VBO |
DURABILITY/ TOUGHNESS |
CHEMICAL RESISTANT |
OEM QUALIFICATION |
E721-FR |
Epoxy |
120 °C (248 °F) |
60 minutes at 120 °C (248 °F) |
• Fire retardant under FAR 25.853 Appendix F - vertical burn material test criteria (ii)
• Core bondable |
Ο |
|
Ο |
|
TC264-1 |
Epoxy |
124 °C (255 °F) |
90 minutes at 118-127 °C (245-260 °F) |
• Flame retardancy applications e.g. ducting, decorative enclosures and composite panel assemblies |
Ο |
Ο |
Ο |
|
BT250E-1FR |
Epoxy |
125 °C (257 °F) |
60 minutes at 121 °C (250 °F) |
• Self adhesive to honeycomb and foam core
• Outstanding surface finish with OOA |
Ο |
Ο |
|
MIL-R-9300 (BT250E-1) |
Toray Cetex® Thermoplastic
|
RESIN MATRIX |
PEAK Tg |
PROCESSING TEMPERATURE |
KEY PRODUCT CHARACTERISTICS |
SECONDARY OPERATIONS |
DURABILITY/ TOUGHNESS |
CHEMICAL RESISTANT |
OEM QUALIFICATION |
TC925 FST |
PC |
153 °C (207 °F) |
260 °C (500 °F) |
• Good FST performance, OSU (<25/25)
• White color option for visual aspect
• Value orientated solution |
Ο |
+
+ |
+ |
|
TC1000 Premium |
PEI |
215 °C (419 °F) |
315 °C (600 °F) |
• Excellent FST performance, OSU (<15/15)
• Qualified to OEM specifications |
Ο |
+
+ |
+
+ |
BMS 8-353 (Type I)
ABS 5036
ABS 5814 |
TC1000 Design |
PEI |
215 °C (419 °F) |
315 °C (600 °F) |
• Excellent FST performance, OSU (<15/15)
• Ideal for customer qualified design programs
• Broader color palette and range of textures |
Ο |
+
+ |
+
+ |
|
TC1100 |
PPS |
90 °C (194 °F)
Tm 280 °C (536 °F) |
320 °C (608 °F) |
• Achieves 35/35 for OSU performance
• Outstanding solvent resistance for structural applications
• High impact resistance
• Ideal for beams and floor panels |
|
+
+ |
+
+
+ |
BMS 8-353 (Type II Class 3)
ABS 5045
ABS 5222
MEP 15-052 |
TC1225 NEW |
PAEK |
147 °C (296 °F)
Tm 305 °C (581 °F) |
325-350 °C (615-662 °F) |
• Outstanding structural and thermal performance
• Compatability to PEEK for injection overmolding and welding |
Ο |
+
+
+ |
+
+
+
|
|
Film Adhesives
|
RESIN MATRIX |
DRY Tg ONSET |
CURE TIME AND TEMPERATURE |
KEY PRODUCT CHARACTERISTICS |
OOA/VBO |
DURABILITY/ TOUGHNESS |
CHEMICAL RESISTANT |
OEM QUALIFICATION |
TC263 |
Epoxy |
110 °C (230 °F) |
2 hours at 121 °C (250 °F) |
• High peel strength
• Ideal for metal or composite bonding |
Ο |
Ο |
Ο |
|
Nomex® Honeycomb* Aerospace Grade
|
CONFIGURATIONS CELL SIZE & DENSITY |
SHEET SIZE |
KEY PRODUCT CHARACTERISTICS |
ANA-3.2-29 |
3.2 mm 29 kg/m³ |
1250 x 2500 mm |
• Fire resistant and self extinguishing to FAR 25.853
• High temperature strength up to 180 °C (356 °F)
• High strength to weight ratio and easily formable to shape
• Nomex® paper sheets are coated and bonded together with a high modulus phenolic resin |
ANA-3.2-48 |
3.2 mm 48 kg/m³ |
1250 x 2500 mm |
ANA-3.2-64 |
3.2 mm 64 kg/m³ |
1220 x 2440 mm |
ANA-4.8-48(OX) |
4.8 mm 48 kg/m³ |
1250 x 2500 mm |
Nomex® is a registered trademark of E.I du Pont de Nemours and Company.
* Cut to customer thickness specifications +/- 0.125 mm.
Offered from Langley Mill, UK. Additional grades can be sourced upon request, subject to minimum order quantities.
Hybrid Panel Solution
Toray Cetex® TC1000 are also available as part of a hybrid panel solution, benefiting from the surface properties of the thermoplastic RTL capping a conventional thermoset (Toray E721-FR or BT250E-1FR)/Nomex® honeycomb core structure.
.jpg)
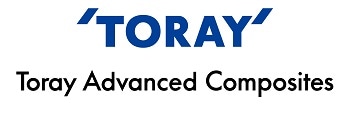
This information has been sourced, reviewed and adapted from materials provided by Toray Advanced Composites.
For more information on this source, please visit Toray Advanced Composites.